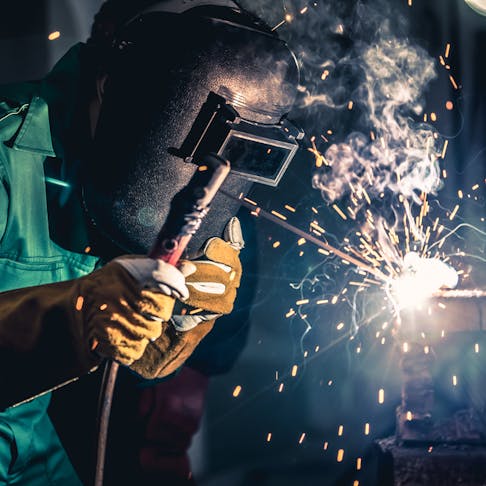
10 Disadvantages of Arc Welding
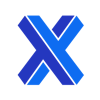
Arc welding is a versatile process that is valued for its ability to quickly produce strong, permanent joints in metal parts. Arc welding is aptly named due to the electric arc used in the process to generate the heat needed to melt and fuse the metal workpieces.
The arc is created by an AC or DC power supply and moves between an electrode and the workpiece. Because of the versatility of the many variations in the arc welding process, it can be used in a variety of environments and on a variety of materials. The different methods of arc welding are used in many industries, including: aerospace, automotive, medical, construction, and marine.
However, arc welding is not without its disadvantages and limitations. From requiring an extensively trained and skilled operator to being a slow process compared to other joining methods, arc welding has several disadvantages. This article will review 10 disadvantages of arc welding.
1. Requires Specialized Equipment and Skills
Specialized equipment and a skilled operator are required for arc welding to be successful. Arc welding requires special equipment such as: a power supply, electrodes (consumable or nonconsumable), wire feeding machinery, containment to protect the welding environment, flux or shielding gas canisters, and associated equipment for welding to be possible. Additionally, extensive PPE including an auto-darkening welding helmet, welding gloves, and welding jacket is required for safe welding practices.
In terms of skills, operators must be trained in how to use particular welding tools and must be familiar with how different weld parameters can impact the quality of a weld. This is because most arc welding processes are still completed manually. Becoming proficient in welding requires extensive study and practice. If welds are not produced correctly, joints can be weak and brittle and can consequently compromise the structural integrity of a part.
2. Produces a Lot of Heat, Fumes, and Sparks
Because arc welding is a thermal process that involves electricity and molten metal, intense heat, fumes, and sparks are sure to be generated. This creates a dangerous environment that requires extensive precautions such as: proper PPE, ventilation, and welding screens to ensure the health and safety of the operator and other people in the area. The absence of such precautions can not only affect the quality of a weld due to weld splatter, sparks, and fumes but can also severely injure people.
3. Can Only Be Used on Specific Materials and Thicknesses
Arc welding is a process that uses extreme temperatures (up to 6000 °F) to melt and fuse metals. While arc welding is great for producing strong, deep welds in thick parts, exceptionally high temperatures may distort thin workpieces. Additionally, depending on the type of arc welding, the process can only be used on certain materials. Some types of arc welding, like FCAW, are only capable of being used on ferrous materials. TIG (tungsten inert gas) arc welding, on the other hand, can be used on a wider variety of metals. However, it requires more initial investment and significantly more training for successful welding operations.
4. Welds May Be Brittle or Have Porosity If Not Done Properly
A weld joint consists of separate pieces of metal which are heated and melted together. To make a successful weld, the pool of molten metal must solidify at the proper rate and without any holes (porosity) in the metal matrix. Improperly produced welds may be brittle or porous or both. Welds may be brittle if the wrong filler metal is used or the weld cooldown profile is incorrect. Porosity is caused by gases either from the surrounding air or contaminants like oil that become trapped in the liquid weld pool and are unable to escape before the weld begins to solidify.
5. Welding Electrodes Need To Be Replaced Regularly
Another disadvantage of arc welding is that welding electrodes must be replaced regularly. Electrodes are materials that are manipulated by the welder to produce an electric arc. Electrodes may be classified as consumable or non consumable. No matter the classification, electrodes must be replaced. Consumable electrodes melt during the welding process and are continuously used. While nonconsumable electrodes do not melt, they still are depleted over time due to vaporization or oxidation of the electrode material.
6. Slow Process Compared to Other Welding Methods
One major disadvantage of arc welding is that it is a slower process than certain other welding methods, such as laser welding. While the electric arc generates an intense amount of heat in a short time, lasers in laser welding processes can melt and fuse materials nearly instantaneously. However, the weld pools developed by laser welding processes are much smaller than those developed by arc welding. Additionally, arc welding sometimes requires multiple passes for welds to be complete while laser welding can complete welds in a single pass.
7. Limited Mobility When Welding Large or Complex Structures
Welding large or complex structures is difficult if using arc welding processes. Because arc welding is a largely manual process, welding over a long distance increases the possibility for welding errors to occur. Additionally, welding large or complex structures may require operators to complete welds in a stepwise manner — that is, operators complete a portion of a large weld, then move their equipment to complete another portion of the weld and keep repeating this until the entire weld is complete. This may cause uneven cooling in the structure and may cause welds to be weak and brittle in some areas. While it may be difficult, other welding processes like laser welding and electron beam welding, are completely impossible to be used for welding large or complex structures.
8. Welding in Certain Positions May Be Difficult or Impossible
Some jobs require welds to be completed over the operator’s head or in hard-to-reach and confined spaces. Welding in these positions presents a larger safety risk to the operator. Not only that, but welding in difficult positions may also lead to discomfort which can consequently impact the quality of a weld. Though the process may be difficult, arc welding is the best joining process for these situations.
9. Requires a Power Source, Which May Not Be Available in All Locations
Arc welding requires a power source, since the electrical arc is fundamental to the welding process. Some welding may need to be completed on sites where an electrical source is not available. Electrical generators are a sound alternative and can provide electrical power wherever it may be needed, but are not always practical. Without a reliable power source, arc welding is impossible.
10. Arc Welding May Cause Deformation or Warping of the Workpiece
Arc welding uses extreme temperatures generated by an electric arc to melt and fuse workpieces. Though arc welding is great for producing resilient, deep welds in thick parts, thinner workpieces are subject to distortion and warping because of heat input and uneven cooling rates. Additionally, some materials are more susceptible to thermal expansion than others. Arc welding may not be suitable for joining thin workpieces or for materials that have high thermal expansion rates.
What Is Arc Welding?
Arc welding is a joining process that uses an electric discharge to melt and fuse materials. Electric arcs are generated by a direct current or alternating current between an electrode and the metal workpiece. The electrode is made from electrically conductive materials such as brass, aluminum, copper, or mild steel. All welding processes require the weld pool to be protected from elements in the air. This is accomplished either by an inert shielding gas or flux. Flux is typically made from materials like hydrochloric acid, zinc chloride, and borax, and protects the molten metal from reacting with the elements in the air during the welding process. For more information, see our guide on Arc Welding.
How Does Arc Welding Work?
Arc welding works by melting metals using heat generated by gasses that have been ionized by the high voltage between an electrode and a grounded workpiece. The electric arc that bridges the gap between the electrode and the work produces a significant amount of heat. When an arc is produced, temperatures can rapidly reach up to 6,500 °F which melts and fuses the base materials. As the molten metal cools, it solidifies, and a strong, permanent joint is created. A shielding gas such as argon, nitrogen, and doped with oxygen is directed during the welding process and protects the molten metal from reacting with the elements in the air.
What Is the Primary Use of Arc Welding?
The primary use of arc welding is to create permanent and strong joints between two materials. Arc welding covers a range of applications including: joining structural members in high-rise construction, fabrication of ship hulls, and DIY home projects.
What Are Some Applications of Arc Welding?
The arc welding process can produce strong, permanent joints in a variety of metals for different applications. Some applications of arc welding are listed below:
- Joining workpieces and complete assemblies in the automotive, aerospace, shipbuilding, and construction industries.
- Repairing damaged components, such as a cracked chassis in a car or a cracked steel beam in a bridge.
- Creating unique artistic sculptures and different types of decor.
How Does Arc Welding Equipment and Maintenance Cost Compare to Other Welding Methods?
Arc welding equipment and maintenance are much cheaper than the equipment and maintenance needed for other welding methods such as laser welding and gas welding. Equipment needed for arc welding includes a welding machine, power supply, electrode, flux, PPE, and various miscellaneous tools such as clamps, magnets, pliers, and grinders, among other things. These items are much cheaper than laser welding systems or electron beam welding systems that can easily exceed the price of all the materials needed for arc welding combined. For instance, arc welding equipment can cost anywhere from $50-5000 while laser welding and electron beam systems can range anywhere from $5000 -100,000 plus.
How Do the Disadvantages of Arc Welding Compare to Laser Welding?
The biggest disadvantage of arc welding compared to laser welding is that it is a much slower process and not automated. Therefore, it has higher associated labor costs and is at higher risk of welding defects compared to laser welding. The primary disadvantages of laser welding are the cost of entry and welding joint size. Laser welding equipment is significantly more expensive than arc welding equipment. Additionally, since highly precise lasers produce small welded joints, larger joints are not ideal for laser welding.
Are There Any Environmental Concerns Associated With the Use of Arc Welding?
Yes. Arc welding is a thermal process that melts metal, and creates fumes, and particulates that can contaminate the air. Harmful fumes from cadmium, iron oxide, zinc oxide, and hexavalent chromium, among others, are all produced during arc welding.
Are There Any Safety Concerns for Welders and Bystanders During Arc Welding?
Yes. There are numerous safety concerns for both welders and bystanders due to the extreme temperatures that are generated and the exceptionally bright light that is produced by an electric arc. Proper PPE should be worn to ensure the safety and health of welders. To protect bystanders, the welding work area should be surrounded by welding screens that dim the light produced by welding. While radiation intensity is strongly dependent on the distance from the welding arc, standing at least 10 meters from the welding area is ideal to prevent vision damage.
Can New Technology or Methods Reduce Arc Welding’s Disadvantages?
Yes, new technology, such as increased automation and the use of robots, not only dramatically improve the safety of arc welding processes, but also improve efficiency and weld quality. Additionally, advancements in virtual reality (VR) have led to new training programs for beginner welders without putting them in harm’s way.
Do All Types of Arc Welding Have the Same Disadvantages?
Yes, all types of arc welding (stick, MIG, TIG, and SAW) have the same disadvantages compared to other welding methods like laser welding. For instance, all types of arc welding have lower efficiency, require a skilled operator, and can be difficult to use on thin materials.
What Are Some Advantages of Arc Welding?
Despite its disadvantages, arc welding also has many advantages. The biggest arc welding advantages are listed below:
- When done properly, arc welding can produce strong, permanent joints with little distortion.
- Arc welding can be performed in a variety of settings, including outdoors in windy or rainy environments.
- Arc welding is a highly economical process since most arc welding equipment is much more affordable than the equipment needed for other welding processes like laser welding or electron beam welding.
- Arc welding is portable and easily transportable compared to laser welding and electron beam welding. While it may be tedious to haul arc welding equipment for welding large or complex structures, the process is more capable of welding in a variety of settings.
Summary
This article presented the disadvantages of arc welding, explained them, and discussed each in detail. To learn more about arc welding, contact a Xometry representative.
Xometry provides a wide range of manufacturing capabilities, including sheet cutting and other value-added services for all of your prototyping and production needs. Visit our website to learn more or to request a free, no-obligation quote.
Disclaimer
The content appearing on this webpage is for informational purposes only. Xometry makes no representation or warranty of any kind, be it expressed or implied, as to the accuracy, completeness, or validity of the information. Any performance parameters, geometric tolerances, specific design features, quality and types of materials, or processes should not be inferred to represent what will be delivered by third-party suppliers or manufacturers through Xometry’s network. Buyers seeking quotes for parts are responsible for defining the specific requirements for those parts. Please refer to our terms and conditions for more information.
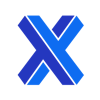