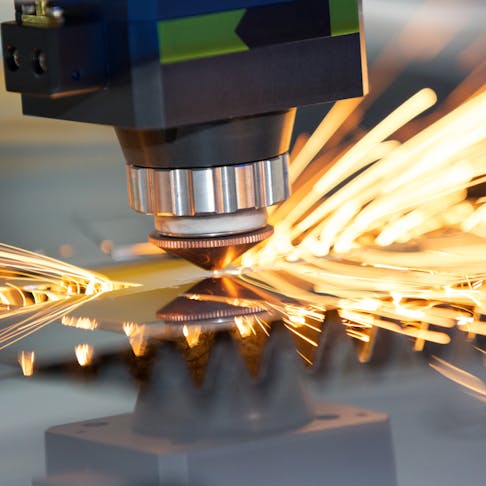
6 Disadvantages of Laser Welding
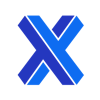
Laser welding is a widely used manufacturing technique due to its precision, speed, and versatility. It uses a highly concentrated light beam to melt and fuse materials together, producing solid and reliable joints.
Laser welding has some disadvantages to take into account, just like any other welding technique. Engineers and manufacturers must be aware of these drawbacks to be able to choose the best welding technique for their particular applications. This article will examine six disadvantages of laser welding and identify any potential obstacles to its application.
1. High Cost
Compared to other welding techniques, laser welding equipment usually requires a larger initial investment. Modern optics, control systems, and safety precautions are all features of complex laser welding machines. Additionally, laser welding equipment can have high maintenance and servicing costs. The requirement for specialized education and experience also raises the overall cost. Due to these high costs, laser welding may not be an option for some applications for small businesses or producers on a tight budget. In some fields and applications, however, the potential advantages and benefits of laser welding may outweigh the upfront costs.
2. Limited Penetration Depth
While laser welding is efficient for joining thin materials, it may have trouble joining thicker materials or parts with wide gaps in the joint. Reduced penetration depth occurs as a result of energy loss in the laser beam as it advances deeper into the material. The best option is electron beam welding when it comes to producing a complete and seamless weld in a single pass. This method uses the strength of electron beams to enable deep penetration welding, ensuring a solid and flawless bond in a single quick pass.
3. Sensitivity to Materials
While laser welding can be highly effective for certain materials, it may encounter challenges with others. Some materials, such as aluminum or copper alloys, are highly reflective and have high thermal conductivity. Because much of the energy is reflected off the surface before it can be absorbed, and what energy is absorbed quickly disperses from the weld zone, it can be difficult for the laser beam to adequately heat the surface and achieve a strong weld.
Additionally, certain materials such as high-carbon steel and aluminum alloys may be prone to cracking, distortion, or changes in their material properties due to the rapid heating and cooling cycles involved in laser welding. This material sensitivity requires careful consideration and optimization of welding parameters to ensure successful welds and avoid potential defects.
4. Safety Concerns
The high-intensity laser beams which are used in laser welding can pose risks to human operators and the environment. Severe eye injuries, burns, and skin damage can all result from direct laser beam exposure. In addition, the process produces gasses, vaporized particles, and fumes that could be harmful or toxic if inhaled. Appropriate safety measures must be put in place, such as the wearing of safety goggles, using the right ventilation systems, and following safety procedures. Accidents, injuries, and long-term health problems may result from failing to address these safety issues.
5. Limited Joint Access
Given that the laser beam can only access a certain portion of the joint, the size and shape of the components that need to be welded must be taken into account. Welding parts with intricate geometries or inaccessible locations may be difficult. Additionally, to achieve complete joint penetration, the welding process might need multiple passes or part repositioning, which can lengthen and complicate the welding process.
6. Reduced Weld Strength
Laser welding can result in reduced weld strength due to factors like high cooling rates, incomplete fusion or penetration, sensitivity to material properties, and limitations in joint design. These factors may cause the bonds in laser-welded joints to be weaker and reduce their overall strength. To maximize the weld strength and guarantee the dependability and durability of laser-welded joints, it is essential to carefully evaluate the welding parameters, material compatibility, and post-weld heat treatment.
How Do Environmental Factors Like Temperature and Humidity Affect Laser Welding?
Laser welding processes can be significantly impacted by environmental factors like temperature and humidity. High temperatures have the potential to degrade the quality of a weld by causing thermal distortion and affecting the material's properties. Humidity has the potential to cause the weld zone to become porous and weaken the joint. Although these problems are not unique to plastics, they are usually more obvious in plastic welding due to the material's sensitivity to heat and moisture. High humidity levels can also bring moisture into the welding area, absorbing laser energy and reducing welding efficiency. It is possible to implement cooling systems or temperature-controlled environments to maintain steady operating conditions to overcome these difficulties. Dehumidifiers or drying systems, for example, can be used to minimize the effects of moisture during laser welding, ensuring reliable and consistent weld quality.
How Might Laser Welding in Tight Places Be Safer?
Comparatively speaking to other types of welding, laser welding in confined spaces can present special safety challenges. The issue at hand is the possibility that the laser beam will cause mishaps or damage if it is not properly aimed or controlled. Implementing sophisticated monitoring systems that continuously examine the welding process and look for any anomalies or deviations is one strategy. Operators can quickly address any potential safety risks thanks to real-time feedback. Furthermore, it is essential to implement stringent safety procedures and give operators thorough training. To ensure the safety of operators and nearby staff, protective measures like laser shielding, safety goggles, and the appropriate personal protective equipment should be used. Additionally, routine inspection and maintenance of the laser welding equipment help find any potential problems and guarantee its best performance, lowering the risk of accidents.
What Are the Long-Term Health Consequences of Laser Welding Radiation Exposure?
The effects of laser welding radiation exposure on long-term health can differ depending on the extent and length of exposure as well as individual susceptibility. Long-term exposure to high-intensity laser radiation can cause eye damage, skin burns, and pulmonary infection. There should be a variety of safety measures in place to protect people from these risks. This entails employing stringent safety procedures such as: using suitable laser shielding and enclosures to reduce radiation leakage and making sure operators wear specialized laser safety goggles. Careful setup and monitoring of exposure times are essential in minimizing the long-term health effects of exposure to laser welding radiation, in addition to routine health monitoring, training, and adherence to safety regulations. These precautions assist in preventing excessive radiation exposure for workers while lowering the risks.
How Does Laser Output or Power Affect Laser Weld Quality?
The output (or power) of the laser has a big impact on the effectiveness of laser welding. The depth, width, heat input, and overall penetration of the weld are directly influenced by the power level. Incomplete welds may result from insufficient power, while material damage may occur when excessive power is used. Controlling the laser output precisely is essential for ensuring consistency and quality. The use of cutting-edge laser systems with reliable power sources and closed-loop feedback mechanisms can accomplish this.
Does the Quality of Laser Weld Vary Depending on the Type of Laser Used?
Yes, the type of laser source used affects the quality of the laser weld. Different lasers produce different wavelengths of light and have different pulse duration and power capabilities. For instance, CO2 lasers are better suited for deeper penetration welding of thick materials while fiber lasers are commonly used for high-speed welding of thin materials. Also, Nd:YAG lasers are popular in the aerospace sector due to their precision welding abilities. Therefore, the choice of laser type depends on the material's thickness, welding material, the required welding speed, the joint geometry, and the desired welding quality.
How Do Laser Welding's Constraints Affect Underwater or Space Welding?
When used in space or underwater, laser welding is subject to special limitations. Underwater welding faces difficulties like the water's ability to absorb the laser energy and the requirement for safeguards against rapid cooling. To get around these limitations and create efficient laser welding processes for underwater and space applications, researchers have investigated some techniques, including laser beam welding which doesn't require shielding gasses or a vacuum environment to work. Back in 1989, NASA scientists were already aware of its potential and specifically advised its inclusion in emergency repair kits for satellites and space stations. With these improvements, welds in demanding environments will be trustworthy and of high caliber.
What Are the Typical Applications of Laser Welding?
A wide range of industries use laser welding because it is a versatile joining method. The following are some typical applications of laser welding:
- Automotive Industry: Welding of car bodies, exhaust systems, and engine components.
- Aerospace Industry: Welding of aircraft structures, engines, and fuel systems.
- Medical Industry: Welding of implants, instruments, and medical devices.
- Electronics Industry: Welding of electronic components, batteries, and sensors.
- Jewelry Industry: Welding of precious metals and alloys for jewelry manufacturing.
What Are Some Advantages of Laser Welding?
There are some benefits to using laser welding over traditional welding methods. The following are some of the main benefits of laser welding:
- Precision: Laser welding produces highly precise and accurate welds due to its focused heat source, allowing for fine control over the welding process.
- Speed: Laser welding is a fast process, as the laser beam can be rapidly moved along the joint, resulting in efficient and high-speed welding.
- Minimal Heat-Affected Zone (HAZ): Laser welding generates a narrow and localized heat-affected zone, minimizing distortion and reducing the potential for thermal damage to the surrounding material.
- Versatility: Laser welding can be used to join a wide range of materials, including ceramics, composites, metals, and plastics, making it suitable for many applications.
Summary
This article presented the disadvantages of laser welding, explained them, and discussed each of them in detail. To learn more about laser welding, contact a Xometry representative.
Xometry provides a wide range of manufacturing capabilities, including sheet cutting and other value-added services for all of your prototyping and production needs. Visit our website to learn more or to request a free, no-obligation quote.
Disclaimer
The content appearing on this webpage is for informational purposes only. Xometry makes no representation or warranty of any kind, be it expressed or implied, as to the accuracy, completeness, or validity of the information. Any performance parameters, geometric tolerances, specific design features, quality and types of materials, or processes should not be inferred to represent what will be delivered by third-party suppliers or manufacturers through Xometry’s network. Buyers seeking quotes for parts are responsible for defining the specific requirements for those parts. Please refer to our terms and conditions for more information.
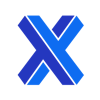