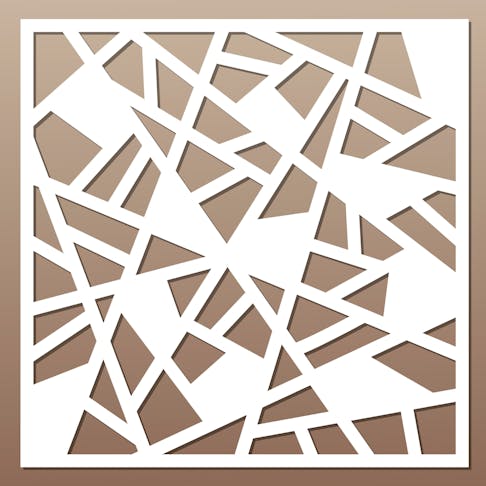
The 7 Disadvantages of Using Laser Cut Stencils
Learn more about the various disadvantages of using laser cut stencils.
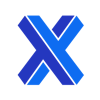
A stencil is a thin sheet of material (usually cardboard, plastic, or metal) with patterns cut out of it. The application of images, patterns, and blocks of color to products is a common method for lifting appearance and quality out of the ordinary. In particular, complex graphics/logos and multicolored embellishments speak of care in design and manufacture. Unfortunately, this process can be very hard to get right and very easy to mess up. Significant difficulty in the production and use of stencils makes this a valued skill set that is not hard to learn, but it is hard to perfect.
Here is a brief review of methods and difficulties involved in the addition of stencil-based mono-color and multicolor artwork to products:
1. Multilayered Art Requires the Use of Many Stencils
When a variety of colors are layered onto a workpiece, each is likely to need its own stencil. Stencils are intricate and delicate parts in their own right, and their use can lead to errors if the skill level is not high enough. Multiple stencils amplify the opportunity for errors, lending the work a much higher risk of failure. Cross-contamination is also a major potential problem, so each application must be thoroughly cured/dried before tackling the next. Stencils must also be thoroughly cleaned if they’re to be used a second time.
2. Restricted Color Palette in Stenciled Artwork While Employing Stencils for Artistic Purposes
In stenciled artwork, each color (or potentially each opening in the stencil) is likely to require a different color. This makes a multicolored process either very slow (to allow cure/dry between colors), very error-prone if the cure isn’t complete, or more costly if multiple stencils are used to isolate colors.
3. Secured Pigment and Dye Must Be at the Surface To Avoid Spills
A critical stage in stencil printing is the holding of the stencil firmly onto the substrate to be printed. Any movement and lifting can result in destructive quality issues. Paint/ink will spread under the masked areas, or fail to fully apply to the surface.
Additionally, in multicolor and multi-stage processes, the perfect correspondence of subsequent stencil stages is critical to avoid blurred and distorted images. For this reason, it is common to use “trust” points or fiducials in positioning stencils. In some processes, these consist of location pins on the work table that align with holes in the stencil.
4. Stencils Are Expensive
For long-term stability, rather than single-use, stencils must be cut from a robust material that can: withstand paint or dye solvent and/or water content, be produced with high-quality edges and limited kerf (to get crisp results), and be cleanable—to remove paint/dye buildup that may occlude or obstruct applications.
Single-use stencils can often be made of paper, but the most effective, long-term stencils are cut from thin stainless steel foils. An intermediate option is to use Mylar® film for the stencil, but these can be creased and damaged relatively easily.
The most effective stencils are those whose thickness is not much greater than the wet film of ink/paint being applied. A large step-down from the stencil surface to the surface being marked is more liable to leave the stencil markings with feathered and imperfect edges.
5. Making Stencils Is Difficult
The best stencils are made from thin, spring stainless steel foils. These require a relatively high laser power and very careful cutting/handling, to make high-quality results. The use of Mylar® films can achieve much of the same quality of result more easily. But these require more careful handling, especially in the post-use cleanup stage, to avoid bending/curling the material. Handling the vector artwork tools required to design a stencil as a cut file requires the development of some moderate skills, though it is well within reach of the most inexperienced user, with a little care, patience, and trialing.
6. Closed Designs Must Be Altered in Order To Prevent Inner Stencil Parts From Falling Out
Stencils seem like a really simple idea—and for non-complex shapes, they are. However, if the design calls for stencil islands (sections of stencil material required wholly inside the boundary of a stencil cutout) they must be supported. This can require design changes to the cutout, or necessitate bridging elements between poorly or unsupported areas of the remaining material. This process requires patience and experience to ensure that the inserted supports don’t disrupt the desired effect by preventing the continuous printing of features.
Support bars can be narrow enough that ink/paint flows under them, but this rarely leads to a visually perfect result. The supports can be integrated into the design, which makes for better results when well done. But this is not a simple task. The same can apply to long, unsupported sections of the stencil, where lack of support from surrounding material allows them to move as the stencil is used, ruining the result.
7. Hazardous Fumes May Be Discharged
It is common for dyes and paints to contain solvents that can represent a health hazard to the user, especially when close attention to detail brings the operator close to the point of application. Precautionary use of good, cross-flowing ventilation is strongly recommended. If you can smell the ink/paint then you are exposing yourself to potential solvent risks. It’s equally important to try to select inks and paints that have a low VOC (volatile organic compound) content, as this reduces the risk of harm to very low levels.
Is It Better Not To Use Laser Cut Stencils?
No, it is not better to avoid laser-cut stencils. Laser-cut stencils can offer great results, but they require skilled handling in repeated use. Laser cutting compares favorably with other methods of cutting stencils—methods such as abrasive waterjet, CNC punching, and chemical etching. For more information, see our guide on Laser Cutting.
What Are the Advantages of Using Laser Cut Stencils?
The advantage of laser cutting stencils is their durability. Once the stencils are made, and the operator has upskilled to achieve good results, a well-made and carefully handled stencil will last for many thousands of applications without wear and cost only the ink/paint and the operator's time.
Can You Cut Stencils With a Laser Cutter?
Yes, stencils can be cut with a laser cutter. Mylar® stencils can easily be cut on a low-power, home laser cutter. Mylar® cuts very cleanly and quickly and can give excellent quality results. Stainless steel stencils will require a higher-power laser to achieve good results, but such capability is still within range for relatively low-cost equipment.
What Is the Difference Between Laser Cut Stencils vs. Other Applications?
Laser-cut stencils are likely to have good fidelity with original design data and can be cut in very thin foils, for clear and sharp-edged results compared to other applications. Screen printing uses a mesh foil which is occluded to form the screen pattern. This technique is very old and well-understood, and these forms of stencil are very low-cost to make. Transfer printing is a commonly used technique in which a full-color image can be printed onto a paper-like transfer medium in a normal inkjet printer. Heat is then transferred to a surface by the application of a hot plate and pressure. This technique offers two-stage processing (however complex the image is) and requires no tooling to be manufactured. The transfer medium is relatively low cost, but single use, so this can raise the per-item processing costs.
Alternative stencil production methods such as waterjet cutting can produce equally good results, compared with laser-cut stencils. There is little cost difference between laser and waterjet cutting, in such thin and processable materials.
Other methods for stencil cutting, particularly optical/chemical processes such as photo etching can substitute but have fallen out of use as they are considerably slower and more costly than laser cutting.
Summary
This article presented the disadvantages of using laser cut stencils, explained what they are, and why each is a disadvantage. To learn more laser cut stencils, contact a Xometry representative.
Xometry provides a wide range of manufacturing capabilities, including sheet cutting and other value-added services for all of your prototyping and production needs. Visit our website to learn more or to request a free, no-obligation quote.
Copyright and Trademark Notices
- Mylar® is a trademark of DuPont Teijin Corporation.
Disclaimer
The content appearing on this webpage is for informational purposes only. Xometry makes no representation or warranty of any kind, be it expressed or implied, as to the accuracy, completeness, or validity of the information. Any performance parameters, geometric tolerances, specific design features, quality and types of materials, or processes should not be inferred to represent what will be delivered by third-party suppliers or manufacturers through Xometry’s network. Buyers seeking quotes for parts are responsible for defining the specific requirements for those parts. Please refer to our terms and conditions for more information.
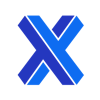