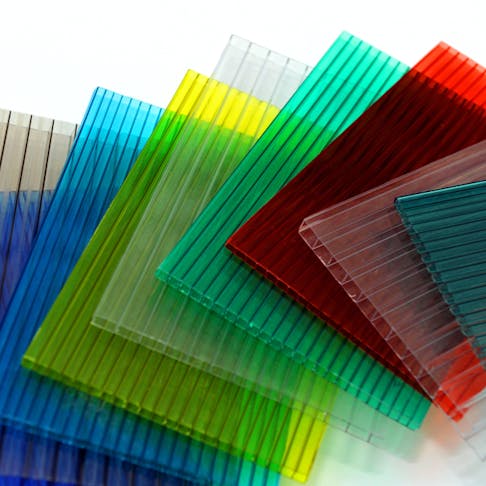
Polycarbonate Laser Engraving and Cutting
Learn more about laser engraving with this material and its different applications.
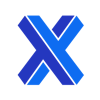
Polycarbonate is a transparent thermoplastic with excellent physical properties. It is used in many engineering and consumer applications under a variety of brand names such as LexanTM or MakrolonTM.
Polycarbonate can be successfully laser-cut and engraved. However, the infrared absorption properties of polycarbonate mean that laser cutting and engraving must be carried out carefully, within very specific conditions, in order to come out with clean and precise edges. A CO2 laser is the best option for cutting polycarbonate while a fiber laser is best for engraving the material.
How To Laser Cut and Engrave Extruded Polycarbonate
Most polycarbonate stock comes in the form of extruded sheets of specific widths. Here are the steps to laser-cut and engrave extruded polycarbonate:
- Use a high-powered CO2 laser.
- Select polycarbonate sheets (ideally no thicker than 3 mm for laser cutting) and/ or the polycarbonate workpieces to be engraved.
- Load your project into graphics software that will interface with the laser cutter/ engraver.
- Adjust the machine’s settings (power, speed, and frequency).
- Load the polycarbonate sheet onto the cutting bed.
- Test the laser’s focus and settings with a test cut. For engraving, test the laser’s focus and settings with a small test etch.
- Execute laser cutting or engraving.
How to Laser Cut and Engrave Cast Polycarbonate
Polycarbonate is only extruded, not cast.
What Are the Differences Between General Part and Presentation Part Cutting for Polycarbonate?
Laser-cut polycarbonate items tend to have discolored edges (yellow or black). These edges are still smooth and accurate, so they are suitable for general parts. However, for presentation parts, this discoloration is unacceptable. Thin parts discolor less, so there are some limitations on the thickness of polycarbonate that can be used in laser-cut presentation parts.
Generally, a stock with thicknesses of 3 mm or less can be cut with clear edges, but this requires specific settings (high power and fast speed). Thicker polycarbonate (up to 8 mm) is fine for general parts whose discoloration is not a problem. The range of acceptable power and speed settings can then be wider, and the machine may take multiple passes to cut.
What Is the Fastest Speed for Polycarbonate with Presentation Parts?
The fastest speed for polycarbonate parts intended for presentation is 70 mm/second. For polycarbonate presentation parts, the discoloration of cut edges must be avoided, so fast speeds like this keep discoloration to a minimum. Lasers cut by melting the polycarbonate, but if the laser moves too slowly, there will be a large heat-affected zone adjacent to the cut, with a noticeable buildup of charred decomposition products.
What Is the Best Power for Polycarbonate with General Parts?
The best power setting for general-part polycarbonate cuts is between 50-100 W using a CO2 laser. Due to the material’s absorption capability, higher power is generally better when cutting polycarbonate. It is more critical to use higher power for presentation parts, as speedy cuts leave less discoloration behind. However, for general parts, some yellowing of the edge is acceptable, and a lower power of around 50 W can be used.
How Does the Thickness of a Polycarbonate Sheet Affect the Wattage Required by a Laser Cutter?
A thicker polycarbonate sheet will demand more power (wattage) out of the laser cutter. The power is proportional to the energy transferred to the material to cut it. Thicker polycarbonate requires more energy to reach melting temperature.
Most laser-cutter users recommend sticking with polycarbonate sheets of 1 mm or thinner. A power of 50 W should be suitable for sheets this thin. Success can be achieved with sheets of up to 3 mm in thickness, but only with caution and incremental adjustments to the settings. Cutting thicker sheets of polycarbonate with a laser cutter will result in more charred, melted edges. A laser with a power of 150 W is recommended for cutting 3 mm polycarbonate.
Thicker sheets will also take longer to cut — it must either be done at slower speeds or over the course of multiple passes.
What Is the Best Setting for Laser Cutting Polycarbonate?
It is best to use a high-wattage laser cutter to cut polycarbonate. A 50.8mm (2”) lens is recommended, with a resolution of 160 PPcm (~400 PPI). The frequency of the laser should be set as high as possible (around 50 kHz). The pressure of the assist gas should also be high (in the order of 400 kPa) as the higher pressure will expel melted material more quickly. This will limit the amount of discolored melt that solidifies on the cut surface.
Two possible approaches can be used for the laser cutting settings:
- It is good to set high-power machines to lower outputs. A 150 W cutter, for instance, would be operated at 75-100 W. The speed is then fine-tuned such that the cut will be finished in a single pass. That usually means a speed of 50-70 mm/s.
- The second approach to laser-cutting polycarbonate is aimed at lower-powered machines. This approach can also be used on thicker sheets of polycarbonate. Use the full power of the laser cutter and increase the speed so that it takes 2 to 4 passes to complete the cuts. By using this fast speed, edge charring and discoloration are minimized.
For more information, see our guide on Laser Cutting Settings for Different Materials.
What Are the Common Mistakes Made When Laser Cutting Polycarbonate?
There are a number of common mistakes that are made when laser cutting polycarbonate. These include:
- Trying to cut sheets that are too thick.
- Cutting at an insufficient speed.
- Using a low-power laser cutter.
What Are the Best Beginner Tips for Laser Engraving Polycarbonate Sheets?
If you are a beginner in laser-cut polycarbonate, remember these tips:
- Use a high-powered CO2 laser.
- Use the fastest speed which allows the part to be popped out in a single pass.
- Leave the plastic protective film on the part until after cutting.
What Is the Advantage of Laser Cutting Polycarbonate?
The advantage of laser cutting polycarbonate is the high precision. For thin sheets, this gives clean edges and repeatable cuts. A secondary advantage of laser cutting polycarbonate is the absence of tool wear and the fact that you never need to change tools.
What Is the Disadvantage of Laser Cutting Polycarbonate?
An obvious disadvantage of laser-cutting polycarbonate is the laser’s tendency to leave yellow discoloration along the cut edges. This is a buildup of melted decomposition products created by the laser’s heat. Hardened melt can leave an imperfect, burred finish. Laser cutting of polycarbonate should be done only on sheets of the right thicknesses and with lasers that move at properly calibrated cutting speeds. Finding the right compromise may take some experimentation.
Which Laser Cutter is Best for Polycarbonate?
A 9.3-micron CO2 laser is best for cutting polycarbonate. Plastics very readily absorb CO2 lasers’ long wavelengths and the optical output power is sufficient for cutting. A 1.06-micron fiber laser, on the other hand, is best for engraving polycarbonate because it leaves a highly precise opaque black marking.
What Are Examples of Polycarbonate Projects for Laser Cutting?
Polycarbonate is an ideal material for the following projects due to its transparency and high impact strength:
- Greenhouse windows
- Clear roofing panels
- Models for high-heat applications (up to 240°F)
- Safety windows
- Vandal-proof (bullet-resistant) windows
- Windshields for boats or motor vehicles
- Clear guards for moving machinery
- Optical lenses
- Sport helmet visors
- Diffusers for LED lights
What Are the Alternatives to Polycarbonate for Laser Cutting?
Depending on the exact application, similar, alternative materials can be substituted where polycarbonate usually gets used. In laser cutting, the best alternatives to polycarbonate are as follows:
- Acrylic/PMMA
- ABS
- Polypropylene
What Is the Main Difference Between Polypropylene and Polycarbonate?
The main difference between the two is that polycarbonate has a significantly higher impact strength than polypropylene. Polycarbonate also resists temperatures up to 240°F while polypropylene’s strength fades above 190°F. Both are quite chemically resistant, but polypropylene tends to have better resistance.
Polypropylene is widely used as a thin, flexible packaging film and in clear containers.
What Is the Difference Between Polycarbonate and Acrylic in Laser Cutting?
The difference between polycarbonate and acrylic in laser cutting is that acrylic is much easier to cut and does not leave behind discolored edges. This is because acrylic evaporates directly, rather than leaving melt and decomposition products along the cut edge.
What Are the Best Materials for Laser Cutting, Including Polycarbonate?
Wood and plastics are generally the best-suited materials for laser cutting. With wood, care must be taken to prevent surface burns. Some plastics, meanwhile, should not be laser-cut because they form hazardous decomposition products. PVC, for instance, releases chlorine gas when melted by a laser. The best materials for laser cutting are given below:
- Paper
- Solid wood sheets
- Acrylic/PMMA
- Cloth
- Magnetic sheeting
Summary
This article presented polycarbonate laser engraving, explained what it is, and discussed the various materials and applications of this process. To learn more about polycarbonate laser engraving, contact a Xometry representative.
Xometry provides a wide range of manufacturing capabilities, including sheet cutting and other value-added services for all of your prototyping and production needs. Visit our website to learn more or to request a free, no-obligation quote.
Copyright and Trademark Notices
- LexanTM is a trademark of SABIC Global Technologies B.V.
- MakrolonTM is a trademark of Covestro Intellectual Property GmbH.
Disclaimer
The content appearing on this webpage is for informational purposes only. Xometry makes no representation or warranty of any kind, be it expressed or implied, as to the accuracy, completeness, or validity of the information. Any performance parameters, geometric tolerances, specific design features, quality and types of materials, or processes should not be inferred to represent what will be delivered by third-party suppliers or manufacturers through Xometry’s network. Buyers seeking quotes for parts are responsible for defining the specific requirements for those parts. Please refer to our terms and conditions for more information.
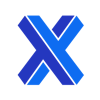