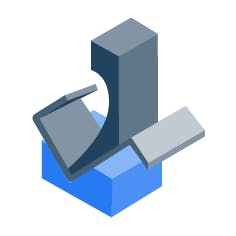
Video: 10 Design Tips for Sheet Metal Bending
Sheet metal bending is one of the most commonly used methods to form sheet metal fabricated parts. To avoid part deformation and unnecessary costs, we recommend following these design tips.
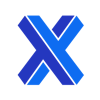
Sheet metal bending is one of the most commonly used methods to form sheet metal fabricated parts. The costs and quality depend on various factors, including setup costs, material costs, and design complexity. To ensure a trouble-free bend and to avoid deformation, we recommend following certain design tips for every type of sheet metal part feature.
2. Bends - Right Radius and Orientation
Keep a minimum bend radius to prevent parts from factoring or distorting. We typically recommend that the smallest bend radius should at least be equal to the sheet thickness. However, there are also various reference tables that show the minimum bend radii of the different materials and part thicknesses. Keeping the bend radius consistent makes the parts cost-effective, as you can use the same tool to bend it. Keeping bends in the same plane in one direction also helps to save time and money by preventing parts reorientation, especially for parts with complex bending.
5. Holes and Slots - the Correct Clearance
Holes and slots can deform if they are too close to a bend; we recommend placing holes at least 2.5 times the material thickness from the bend to the edges. Slots require more clearance, so we recommend placing them at least four times the material’s thickness from the bend edges. In addition, extruding holes or slots is an extremely high-pressure application, which can create a lot of friction and heat to avoid.
6. Countersinks: Clearance and Size
Countersinks are created with a drill press or punch press cooling. The basic rules for countersinks are as follows. Keep a minimum distance of three times the material thickness from a bend, 4 times from an edge, 8 times from each other, and they shouldn’t be deeper than 0.6 times the material thickness.
7. Curls: the Right Dimensions
Curled edges are stronger and safer for handling. They are often used to remove a sharp untreated edge and make it safe. The outside radius of the curls must be at least twice the size of the material thickness. If you add holes next to the curls, place them at least the size of the curl plus the material thickness from the curls. Other bends should be placed at least 6 times the material thickness, plus the radius of the curls from the curls
8. Hems - the Right Dimensions
Hems are often used to straighten the edges and make sharp edges safer. Closed hems are not recommended if they are to be painted or if the part is made of stainless steel or aluminum. Their flange length from the outside of the bend should be equal to or greater than 4 times the part thickness. The same flange length to sheet thickness ratio applies for open hem and teardrop hems. For open hems, the inside diameter should be at least the same size as the material thickness. it will lose its roundness when the inside diameter is greater than the thickness. For teardrop hems, the diameter should also be equal to the material thickness. The hem opening space between the hem edge and the part should be at least a quarter of the sheet metal thickness.
10. Tabs and Notches - Clearance
Notching is a shearing process that removes a section from the outer edge of the part. Distortion may occur if the distance between the notches and the bend is too small. To avoid this, the notch-to-bend distance should be at least three times the material thickness. Plus, the bend radius notches must be at least 3.175 millimeters away from each other. The minimum distance between tabs should be one millimeter or the material thickness, whichever is greater.
At Xometry, you can order from over 15 production technologies, over 100 materials, and dozens of finishing options. Get an instant quote and lead times in the Xometry Instant Quoting Engine® today.
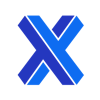