Inconel Metal 3D Printing
Get instant online quotes on custom 3D printed Inconel parts. Free shipping on all US orders. ISO 9001:2015, ISO 13485 and AS9100D certified. Subject to availability. Xometry doesn't guarantee that we can provide this service at any given time.
About 3D Printing Inconel Metal
Inconel is used extensively in the aerospace industry because of its high tensile strength, excellent fatigue and thermal fatigue resistance, and significant corrosion and oxidation resistance. Inconel parts are difficult to create due to their tendency to work-harden during machining—this makes 3D printing (a process that does not work-harden the material) an outstanding choice. The main alloying elements in Inconel are nickel, chromium, and molybdenum. Other industries that use Inconel metal are marine and energy.
DMLS Inconel 625
This Inconel alloy includes a small amount of niobium which interacts with molybdenum to harden the material without the need for precipitation hardening. This alloy is highly corrosion and oxidation resistant, making it ideal for corrosive conditions such as those found in the marine, energy, and chemical processing industries. Applications can include boat propellers and heat exchanger casings.
Tensile Strength, Yield (MPa) | Fatigue Strength (MPa) | Elongation at Break (%) | Hardness (Brinell) | Density (g/cm^3) |
---|---|---|---|---|
Tensile Strength, Yield (MPa) 980 ± 5 | Fatigue Strength (MPa) 720 ± 5 | Elongation at Break (%) 33 ± 2 | Hardness (Brinell) 264 | Density (g/cm^3) 8.4 |
DMLS Inconel 718
This Inconel alloy is known for its exceptional high-temperature resistance and overall strength. Mechanical properties are maintained at temperatures of up to 700°C. Precipitation hardening can further improve its mechanical properties. Inconel 718 can also be easily welded. Typical applications include gas turbine engine parts and rocket engines.
Tensile Strength (MPa) | Yield Strength (MPa) | Elongation at Break (%) | Hardness (Brinell) | Density (g/cm3) |
---|---|---|---|---|
Tensile Strength (MPa) 1060 ± 50 | Yield Strength (MPa) 780 ± 50 | Elongation at Break (%) 27 ± 5 | Hardness (Brinell) 287 | Density (g/cm3) 8.15 |
Finishes
Inconel 3D printing results in parts of equal density to machined parts. They can also just as easily be machined or polished after printing. It must be noted that Inconel tends to work-harden during machining.
Standard: The standard finish involves the removal of any support structures. The surface of the part is then medium blasted to create a uniform surface.
CNC Machining or Polishing: In some cases, CNC machining or polishing can be performed on specific features of the component. However, these are evaluated on a case-to-case basis.
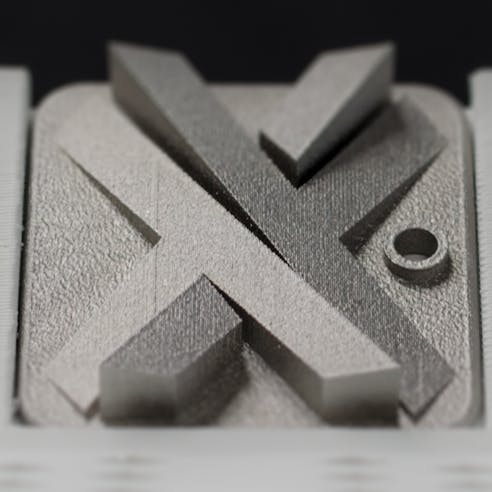
Cost-saving Design Tips
To reduce expenditures when Inconel 3D printing, follow these cost-saving design tips:
DFM: DMLS Inconel metal 3D printing can produce extremely high-strength functional parts that can be used in the most demanding applications. When designing parts for metal 3D printing, make sure that any enclosed areas have holes from which to remove unfused powder after printing. DMLS prints generally require support structures to prevent warping as well as to support overhangs.
Limit Post Machining: Metal printed parts are often post-processed on CNC machines to create accurate features, threaded holes, or other features not possible on metal 3D printers. Since Inconel tends to rapidly work-harden during the machining process, such operations can become very expensive. Parts must be designed to limit the amount of machining required.
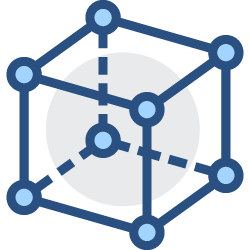