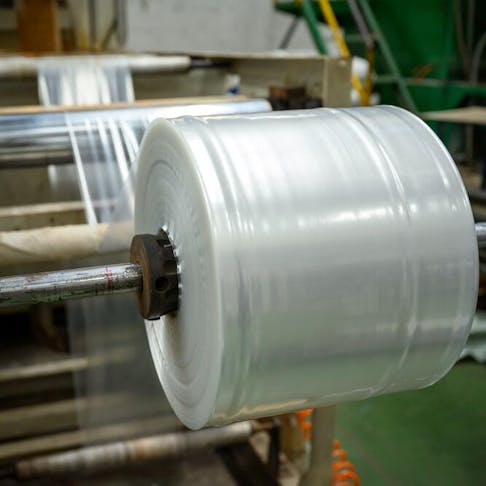
All About Linear Low-Density Polyethylene (LLDPE)
Learn about the material's properties, uses, advantages, limitations, and toxicity.
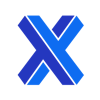
Linear low-density polyethylene is a commodity thermoplastic that is widely used in the packaging industry. It is valuable there because it can easily be formed into film-like materials that retain significant tensile strength. Its molecular chains contain relatively short branches when compared to other polyethylenes. This article will go into more detail about what this material is, its use cases, and its effect on human health.
Plastic film winder unit from LLDPE.
Image Credit: Tango Uniform India/Shutterstock.com
What is Linear Low-Density Polyethylene?
Linear low-density polyethylene is a semi-crystalline polymer with many short branches on its main molecular chains. This means that these linear molecules do not become entangled as easily as LDPE and HDPE. The figure below indicates the difference between LLDPE and other common forms of polyethylene.
Molecular chain comparison of LDPE, LLDPE, and HDPE.
Image Credit: Roman Hackl/ResearchGate.Net
LLDPE plastic is typically made from one of three different co-monomers classified as alpha-olefins. These are described below.
- Octene: This is the highest-performance co-monomer used, so it is by far the most expensive. The octene co-monomer has the longest branch chains.
- Hexene: This co-monomer provides a good middle ground between octene and butene, but is also categorized as a high-performance co-monomer.
- Butene: Due to its lower cost, butene is the most common co-monomer for commodity plastic applications. The butene co-monomer has the shortest branch chains.
Various blends of the above-mentioned co-monomers are also used to adjust the properties of LLDPE plastic, the most common being a blend of butene and hexene.
How is Linear Low-Density Polyethylene Made?
Linear low-density polyethylene is manufactured via the copolymerization of ethylene and an alpha-olefin such as butene, hexene, or octene co-monomers. The co-monomers are most often polymerized using the Unipol process, which is also known as the gas phase process. The catalyst (either Ziegler-Natta or metallocene) and ethylene are blown into a fluidized bed reactor where copolymerization occurs. The polymer then settles at the bottom and exits the reactor as a powder which is then pelletized. During the pelletization process, additives are added to the material.
This process occurs at low pressures and temperatures and is, therefore, more cost-effective than other polymerization techniques like the slurry and solvent processes. It must be noted that butene- and hexene-based LLDPE blends are typically manufactured using gas-phase polymerization and octene is manufactured using the solvent process.
Linear low-density polyethylene has unique melt flow properties (rheology) and is typically processed using blow molding, film extrusion, or injection molding. Film extrusion is the dominant processing method for LLDPE. LLDPE plastic has a high shrinkage rate in part due to the fact that this material is semi-crystalline and therefore takes up more volume in its melt state than in its solid state.
What Are the Properties of Linear Low-density Polyethylene?
Listed below are some common mechanical properties of LLDPE plastic. The properties listed are for the most common variation of LLDPE plastic – namely the formulation containing butene.
Material Property | Value |
---|---|
Material Property Density (g/cm3) | Value 0.92 |
Material Property Tensile Strength (MPa) | Value 20 |
Material Property Flexural Modulus (GPa) | Value 0.35 |
Material Property Elongation at Break (%) | Value 500 |
Material Property Maximum Operating Temperature (C) | Value 50 |
Material Property Heat Deflection Temp @ 0.45 MPa (C) | Value 45 |
Material Property Heat Deflection Temp @ 1.80 MPa (C) | Value 37 |
Material Property Plastic Melting Point (C) | Value 220 - 260 |
Material Property Mold Shrinkage (%) | Value 3 |
Table 1. LLDPE Properties
What Are the Uses of Linear Low-Density Polyethylene?
Linear low-density polyethylene plastic can elongate by a remarkable percentage but also retains high tensile strength. The linear nature of the polymer also makes this material ideal for walled applications like those listed below.
- Pallet stretch film
- Garbage bags
- Pond liners
- Buckets
- Floor tiles
- Shopping bags
- Industrial liners
- Cable jacketing
What Are the Advantages of Using Linear Low-Density Polyethylene?
Linear low-density polyethylene has many advantages and is well suited for thin-film applications. Properties like those listed below make LLDPE ideal for these types of applications.
- Puncture-resistant
- Good flexibility
- Resistant to oxidation
- Excellent barrier properties
- High impact strength
- Good environmental stress cracking resistance
- Retains strength when in film form
- UV resistant
What Are the Disadvantages of Using Linear Low-Density Polyethylene?
Once linear LLDPE stretches, it does not recover like other thermoplastics. This property can be desirable in some applications like stretchable pallet films but in general, this lack of memory retention is a distinct disadvantage.
LLDPE is not environmentally friendly and finds its way into many single-use applications. As such, it makes up a large percentage of environmental pollution. In addition, it does not degrade readily and is difficult to recycle.
How Does Linear Low-Density Polyethylene Affect Human Health?
Linear low-density polyethylene is non-reactive and can be stored without the risk of off-gassing. LLDPE is used in many applications in direct contact with foodstuffs. It also does not have any adverse effects on human health when in direct contact with skin.
However, there is some risk during the processing of linear low-density polyethylene products. Inhalation of the raw material’s dust can cause irritation to the respiratory system. Fortunately, ingestion of LLDPE does not have any adverse effects.
Is Linear Low-Density Polyethylene Toxic?
Linear low-density polyethylene does not contain any BPAs and can be considered non-toxic. However, as is the case with many thermoplastics, combustion of LLDPE can produce extremely harmful fumes. Exposure to burning LLDPE should be avoided.
What is the Difference Between Polyethylene and Linear Low-Density Polyethylene?
Linear low-density polyethylene (LLDPE) is one of the five groups in all polyethylene forms. Polyethylene is a broad category of plastic materials that consists of separate groups of specific materials, each with different properties and uses. Besides linear low-density polyethylene (LLDPE), the other four groups of polyethylene are:
- Low-density polyethylene (LDPE)
- High-density polyethylene (HDPE)
- Very low-density polyethylene (VLDPE)
- Ultra-high molecular weight polyethylene (UHMWPE)
The different molecular structures and molecular weights of these polyethylene groups determines their mechanical properties. As the molecular weight increases, the material strength of the material also increases, while its elasticity decreases.
What is the Difference Between Low-Density Polyethylene and Linear Low-Density Polyethylene?
The key difference between LDPE and LLDPE is the structure of their molecular chains. Low Density Polyethylene (LDPE) has significantly longer branching chains compared to the short branches of LLDPE. The long branches of LDPE cause them to get tangled far more often. In the macroscopic scale, that translates into less elongation before failure. The linear molecular structure of linear low-density polyethylene makes it great for thin-film applications. LLDPE has better tensile strength and impact strength when compared to LDPE and also has a higher density. LLDPE can stretch more easily without breaking which makes it ideal for stretchable packaging film.
Summary
This article summarized the properties, uses, advantages, limitations, and toxicity of linear low-density polyethylene.
About Xometry
Xometry offers plastic injection molding, 3D printing, and other manufacturing services for all of your project needs. Visit our website to learn more or to request a free, no-obligation quote for your part manufacturing requirements.
Disclaimer
The content appearing on this webpage is for informational purposes only. Xometry makes no representation or warranty of any kind, be it expressed or implied, as to the accuracy, completeness, or validity of the information. Any performance parameters, geometric tolerances, specific design features, quality and types of materials, or processes should not be inferred to represent what will be delivered by third-party suppliers or manufacturers through Xometry’s network. Buyers seeking quotes for parts are responsible for defining the specific requirements for those parts. Please refer to our terms and conditions for more information.
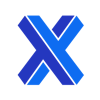