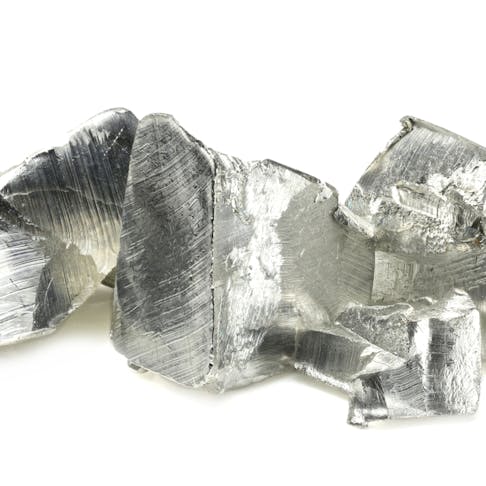
Tin Metal: Definition, Composition, Properties, and Applications
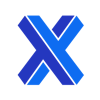
Tin is a chemical element with the symbol Sn on the periodic table and atomic number 50. It is a silver-white, malleable, and relatively soft metal. Tin ore is typically found in nature in the form of minerals like cassiterite (tin dioxide), which is the primary source of commercially mined tin. For a metal, it has a relatively low melting point and a density of about 7.3 g/cm3. Tin is malleable, so it can be rolled into thin sheets and drawn into wires.
Tin is particularly valuable as an alloying agent to be combined with other metals. Alloys that contain tin include: bronze, babbitt metal, pewter, and various solders. Tin compounds are used to produce various chemicals, such as organotin compounds, which are employed as stabilizers and catalysts.
This article will discuss tin metal, its composition, properties, and applications.
What Is Tin?
Tin is an elemental metal, so it cannot be subdivided into component elements. Tin atomic nuclei contain 50 protons and (on average) 69 neutrons.
What Is the Other Term for Tin Metal?
Another common term for tin is its Latin name, stannum. While tin is the more widely recognized name for the element, stannum is sometimes used in historical or scientific contexts, and it's the origin of the periodic table symbol, Sn.
What Is the Origin of Tin?
Tin is a nuclear decay product that forms during stellar novas, the explosive deaths of large stars. This is the case for all elements with atomic numbers greater than 26. It is a siderophile element, meaning it has an affinity for iron, so it tends to be associated with iron ores.
Most tin we use today has been there since the Earth’s crust solidified during the planet’s early history. Tin ores, like cassiterite, are typically found in granite rocks and pegmatites, often associated with hydrothermal veins that serve to concentrate the ores. These minerals were formed through the geological movement of fluids and the slow, water-driven deposition of minerals.
Humans have extracted tin from these ores for thousands of years. Since it’s relatively simple to refine, tin was one of the first metals humans learned to use.
What Is Tin Made Of?
As an elemental metal, pure tin is made of only tin atoms. It belongs to Group 14 on the periodic table. Listed as element number 50, it contains 50 protons. Most isotopes of tin are remarkably stable, so though a 69-neutron configuration is an average state, isotopes can be found with anywhere from 62 to 76 neutrons.
How Is Tin Metal Made?
The sourcing and refining of tin metal involves various steps. Tin ore is typically extracted from underground or open-pit mines. The primary tin ore mineral is cassiterite, which is usually mined as a mixture of ore minerals and gangue contaminants. The mined ore is processed to remove the gangue minerals and concentrate the tin-bearing rocks. This is performed through crushing and grinding, followed by gravity separation using relative buoyancy sorting techniques. This increases the tin content in the ore, reducing the bulk to be refined.
The concentrated tin ore is heated in a furnace with carbon (often in the form of coal or charcoal). This process reduces the tin oxide in cassiterite to produce tin metal and carbon dioxide gas, as the carbon preferentially oxidizes and leaves the tin as a pure metal. The resulting crude “tin” metal will contain impurities like iron, copper, and other metals. The next step refines the metal to remove these impurities. It’s most often done through temperature-controlled liquation, in which the metal is heated to liquefy the tin content but leaves the other elements as solids that can be separated.
For additional purification, electrolytic refining is often employed. In this process, impure tin is dissolved in an electrolyte solution, and a direct current is passed through it. Tin ions migrate to the cathode, forming pure tin metal without any non-metallic contaminants. Other metals are removed by careful electrode voltage and current control. The resulting high-purity tin is cast into various forms — ingots, bars, or sheets, depending on its intended use.
What Is the Color of Tin?
Tin in its unoxidized state has a lustrous, silver appearance. It reflects light with near mirror-like precision when polished.
What Does a Tin Look Like?
Tin is a silver-colored metal that becomes more gray or powdery white as it oxidizes.
What Are the Chemical Properties of Tin?
Table 1 below shows the chemical properties of tin:
Property | Description |
---|---|
Property Atomic Number | Description 50 |
Property Atomic Mass | Description 118.710 u |
Property Electron Configuration | Description [Kr] 4d10 5s2 5p2 |
Property Oxidation States | Description =+2, +4 |
Property Electronegativity | Description 1.96 (Pauling scale) |
Property Crystal Structure | Description Tetragonal (gray tin), Face-centered tetragonal (white tin) |
Property Phase at Room Temp. | Description Solid |
Property Solubility | Description Insoluble in water; soluble in concentrated acids |
Property Reactivity | Description Relatively unreactive in air and water at room temperature |
Property Corrosion Resistance | Description Resistant to corrosion in many environments |
Property Common Compounds | Description Forms various tin compounds, including oxides and salts |
Property Isotopes | Description Several isotopes exist, with Sn-118 being the most abundant and stable |
Property | Description |
---|---|
Property State at Room Temp. | Description Solid |
Property Color | Description Silvery-white |
Property Density | Description 7.3 g/cm³ |
Property Melting Point | Description 231.93 °C |
Property Boiling Point | Description 2,270 °C |
Property Hardness (Mohs) | Description 1.5 |
Property Malleability | Description Highly malleable, can be rolled into thin sheets |
Property Ductility | Description Ductile, can be drawn into thin wires |
Property Crystal Structure | Description Tetragonal (gray tin), Face-centered tetragonal (white tin) |
Property Electrical Conductivity | Description Good electrical conductivity |
Property Thermal Conductivity | Description Moderate thermal conductivity |
Property Magnetic Properties | Description Magnetic at low temperatures (gray tin) |
Property Sound Transmission | Description Excellent sound transmission properties |
Property Tin Pest | Description Subject to "tin pest" at low temperatures (below about -13.2 °C) |
Is Tin One of the Hardest Metals on Earth?
No, tin is a soft and malleable metal with low tensile strength and hardness.
Can You Laser Cut Tin?
Yes, you can laser cut tin in both pure and alloyed forms. It is also responsive to laser engraving.
Is Tin Magnetic?
It depends. Tin can exhibit magnetic properties, but its magnetic behavior depends on its allotrope and temperature. Gray tin (α-tin) is the stable form of tin at temperatures below approximately -13.2 °C. At these low temperatures, gray tin is magnetic. White tin (β-tin) is the stable form of tin at temperatures above -13.2 °C and up to its melting point of 231.93 °C. At these temperatures, tin is non-magnetic.
What Are the Applications of Tin?
Tin finds use in various industries due to its unique properties. Some of these applications are discussed below:
1. Solder
Tin is the primary component in most types of solder. Tin and other low-melting-point alloys are important in electronics and cosmetic and structural jointing in plumbing, jewelry, etc. In solder, tin is alloyed with several metals — lead, silver, copper, antimony, zinc, and more. These create specialist materials that can bond or join a huge range of metal components and conduct electricity.
Tin’s low melting point makes it suitable for precise and controlled soldering applications in electronics assembly and plumbing connections. Its ability to form strong, reliable, and electrically conductive bonds between components has made it indispensable in the manufacture and repair of electronic devices. It goes into everything from consumer gadgets to aerospace equipment. Tin-silver alloys are widely used in high-value and decorative applications.
2. Optoelectronics
Tin has significant value in optoelectronics, particularly as a component in advanced materials and devices. One notable application is in thin tin dioxide (SnO2) films, which are used in gas sensors for detecting pollutants and toxic gasses. The capacitive or conductive properties of the films vary according to the specific alloying chemistry.
Tin-based perovskite materials have also gained attention for their value in solar cells and light-emitting diodes (LEDs). These perovskite structures can be tuned to enhance the material performance. Tin’s unique properties, including its electrical conductivity and willingness to alloy with other metals, make it a valuable element in the development of cutting-edge optoelectronic technologies for energy conversion, sensing, and display applications.
3. Tin Plating
Tin plating or tinning is a surface finishing process that applies a thin layer of tin onto the surface of a substrate, typically copper or steel. It can be done to improve corrosion resistance (preventing the underlying metal from rusting or oxidizing), enhance solderability (making it easier to join components through soldering), or improve aesthetics.
Tin plating is common in electronic components, food and beverage cans, and various industrial applications that need to resist corrosion or improve solderability.
4. Glass Production
Tin compounds, particularly tin dioxide (SnO2), play a significant role in the glass industry. Tin dioxide is utilized as a transparent conducting oxide (TCO) coating for low-emissivity (low-E) glass. Low-E glass is designed to minimize heat transfer through windows, improving energy efficiency in buildings. This enhanced ability to reflect heat while allowing visible light to pass through can make buildings more energy-efficient and environmentally friendly. Tin compounds are essential for modern glass coatings used in architectural and automotive applications.
5. Dental Applications
Tin is employed in various dental applications due to its biocompatibility and safety for oral use. One common use is in dental amalgams — tin is a key component of the amalgam alloy along with silver, mercury, and other metals. Dental amalgams have been used for over a century because they’re durable and cost-effective, though they’re now often overshadowed by harder wearing and more robust polymer and ceramic solutions.
Tin-based compounds, such as stannous fluoride, are also used in toothpaste and mouthwash to prevent tooth decay and reduce sensitivity. They strengthen tooth enamel and have antibacterial properties.
6. Specialized Alloys
Some specialized alloys incorporate tin in varying amounts alongside other metals. It’s done to give the alloy specific properties.
Bronze is one of the oldest such alloys, consisting primarily of copper and tin, though modern interpretations also contain nickel and aluminum to enhance corrosion resistance and toughness. Bronzes are known for strength, corrosion resistance, and ease of working. Bronze is widely used in: bearings (alloyed with phosphor), marine equipment, water processing equipment, and decorative items.
Pewter is a tin-based alloy that includes small amounts of copper, antimony, and sometimes other metals. It is known for its low melting point and malleability. It used to be very common in: decorative items, utensils, and tableware, though its use is declining.
Babbitt metals are tin-based alloys with additions of antimony and copper. They’re used as plane-bearing surfacing materials due to their low friction, excellent conformability, self-healing properties, and load-bearing capacity. White metals are similar alloys that often get used interchangeably with babbitt metals.
Many other tin-centric formulations are alloyed with lead (e.g., Sn-Pb solder), silver, or other metals. These alloys have different melting points to suit various applications and are used to join components in electronics, plumbing, and metalwork or for preparing surfaces for soldering by pre-coating (tinning) for low oxidation and solder affinity.
How Is Tin Metal Used in TIG Welding?
Tin has a low melting point and has no relevance in TIG welding.
What Are the Advantages of Tin?
Tin offers several advantages that make it valuable in various applications:
- The excellent corrosion resistance makes it suitable for use in environments that would cause rust or corrosion in other metals. Though its oxide coating is not oxygen-proof, its corrosion rate is low in mild conditions.
- Tin lends its malleability to many alloys. It can be easily shaped, rolled, or drawn into thin sheets or wires, allowing it to be used in various forms and applications.
- Pure tin exhibits a low melting point (231.9 °C) and imparts this property on many of the alloys tin is part of.
- Because it’s biocompatible, tin is safe for use in: dental applications, food packaging, and medical devices.
- Tin conducts electricity, so it’s found in electrical and electronic components, including solder and coatings. Its conductivity is lower than copper, but it is rarely employed across large conductivity gaps, so the net resistivity of any joint is very low.
- It is readily miscible in alloys with various other metals, enhancing their properties. Bronze, babbitt metal, and pewter are examples of such alloys.
- Tin dioxide (SnO2) is used as a transparent conducting oxide (TCO) in optoelectronics devices like solar cells and touch screens. It combines transparency with electrical conductivity.
- Tin compounds have a wide spectrum of industrial applications, including: as catalysts, stabilizers, and pigments in paints.
- Tin's use in products like low-E glass can contribute to improved energy efficiency in buildings.
What Are the Disadvantages of Tin?
Listed below are the disadvantages of tin:
- It has very low tensile and shear strength compared to many other metals, making it entirely unsuitable for bulk structural applications.
- At low temperatures, tin becomes brittle, exhibiting “tin pest,” which can result in structural changes in some applications.
- Tin's low melting point makes it unsuitable for high-temperature applications.
- While not a precious metal, tin can be relatively costly compared to many industrial alloys.
- While tin is generally corrosion resistant, it may corrode in some aggressive environments, particularly if exposed to strong acids and alkalis.
- While tin is a good conductor of electricity, it is not as conductive as some other metals like copper or silver, so it cannot serve as a long-path conductor.
- Tin will progressively and rapidly oxidize when held at high temperatures, affecting its performance over time.
Is Tin a Cheap Metal?
No. Tin is not typically considered a cheap metal. While it is not as expensive as rare or precious metals, it is more expensive than abundant metals like: iron, aluminum, or copper.
Is Tin Worth More Than Gold?
No, tin has a typical spot price of $25.40 per kg whereas Gold has a spot price of around $70,000 per kg!
Is Tin a Rare Metal?
No. Tin is not considered a rare metal in the Earth's crust, as it is more abundant than many other elements. It is estimated that tin's abundance in the Earth's crust is about 2 parts per million (ppm), which places it in the category of moderately abundant elements.
However, while tin is not rare on a global scale, its distribution is not uniform, and economically viable deposits of tin ore (typically cassiterite) can be geographically limited. This has led to the development of tin mining operations in specific regions. The availability of tin can be influenced by geological factors and geopolitical considerations.
Does Tin Rust?
Yes, in certain conditions. Tin resists corrosion in dry air at room temperature, forming a moderately protective oxide layer on its surface. It is more susceptible to corrosion in the presence of moisture, acidic or alkaline environments, and elevated temperatures.
What Is the Difference Between Tin Metal and Tin Bronze?
Tin and bronze are distinct materials with different compositions, properties, and applications. Pure tin metal exhibits very low mechanical strength. While it enhances many other metals when alloyed with them, it has only decorative uses on its own. Bronze is a high-strength alloy composed of copper and tin. The pairing makes bronze considerably tougher and harder than either constituent metal. Tin has a low melting point, so the bronze alloy also melts at a lower temperature than pure copper, making it more workable. The addition of tin to copper enhances the ductility of the resultant alloy, improving its working properties and toughness.
Summary
This article presented tin metal, explained it, and discussed its various properties and applications. To learn more about tin metal, contact a Xometry representative.
Xometry provides a wide range of manufacturing capabilities and other value-added services for all of your prototyping and production needs. Visit our website to learn more or to request a free, no-obligation quote.
Disclaimer
The content appearing on this webpage is for informational purposes only. Xometry makes no representation or warranty of any kind, be it expressed or implied, as to the accuracy, completeness, or validity of the information. Any performance parameters, geometric tolerances, specific design features, quality and types of materials, or processes should not be inferred to represent what will be delivered by third-party suppliers or manufacturers through Xometry’s network. Buyers seeking quotes for parts are responsible for defining the specific requirements for those parts. Please refer to our terms and conditions for more information.
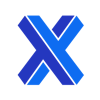