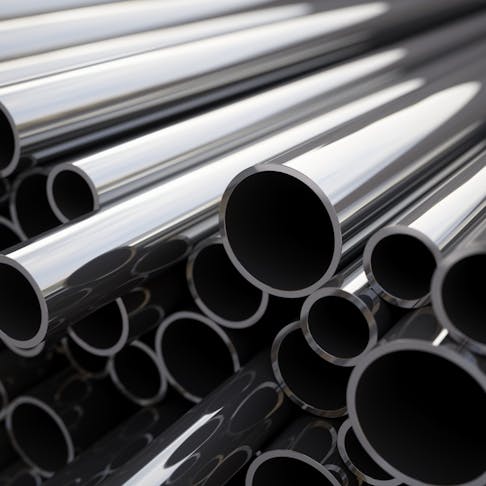
Stainless Steel: Definition, Composition, Types, Grades, Properties, and Applications
Learn more about this materials and its different grades available to manufacture.
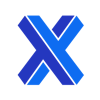
Stainless steel is the general name for a family of steels that are corrosion-resistant and contain a minimum of 10.5% chromium. The effect of this minimum level creates a chromium oxide layer on the surface, which is a self-healing oxygen barrier that stops further oxidation. Below 10.5% chromium, the oxide film is of insufficient durability to be self-healing.
Stainless steels are widely used in most industries, including: construction, marine, aerospace, automotive, and consumer goods. The material delivers high strength, durability, and resistance to corrosion, making it ideal for many cosmetic and open-environment components. Stainless steel is supplied in grades classed by their alloy content. The grade selected for an application depends on factors such as the environment in which it will be used, the required strength and durability, and the desired aesthetic standard. This article will define: What is stainless steel?, its composition, types, grades, properties, and applications.
What Is Stainless Steel?
Stainless steel is primarily made from medium and low-carbon steel. They are alloyed with a range of metals to alter the resulting properties. For example, chromium and nickel lend corrosion resistance and hardness. Other metals enhance malleability, toughness, ductility, tensile and shear strength, and other properties. Stainless steels are generally high strength, with some examples being among the highest tensile and yield strengths of all metals. They are also generally corrosion-resistant, with exceptional performance in particular environments according to grade/alloy type. Additionally, stainless steels are capable of high- and low-temperature performance, from cryogenic temperatures to 2,000 °C, depending on grade.
Depending on the definition, there are at least 60 and possibly over 100 distinct grades of stainless steel that continue to be developed for general and specific purposes. The study of stainless steel is among the most active areas in metallurgical research. These grades are covered by various national and international standards which are progressively becoming unified and generally define close or identical alloys/properties.
What Is the History of Stainless Steel?
The history of stainless steel began in 1912, when Harry Brearley, an English metallurgist leading the Brown Firth Laboratories in Sheffield, was researching hard-wearing steels for gun barrel improvements. Some of his experimental alloys were observed to be highly resistant to corrosion, and he saw and understood the wider implications of his work. He began experimenting with different compositions of steel and found that it was the addition of chromium to the alloy that created the biggest influence on the resulting resistance to corrosion.
Brearley patented his new alloy under the name “rustless steel” (later modified to stainless steel) in 1915. The research lab owners were Sheffield steelmakers, whose primary reputation was in weapons and table cutlery. It was in this market that the first application for stainless steel was developed, making good use of the strengths of the new alloys. During World War I, stainless steel was also used in military applications such as aircraft engines and gun parts.
Stainless steel is now a primary material in most industrial sectors, including appliances, medical equipment, automotive parts, and construction materials. Its resistance to corrosion, as well as its strength and durability, increasingly make it a popular choice for many industries.
What Is Stainless Steel Made Of?
Stainless steels are made of alloying elements such as: chromium, nickel, molybdenum, and titanium to achieve specific properties like improved corrosion resistance, higher tensile strength, or improved ductility/malleability. The exact composition of stainless steel is a wide-ranging topic, with small changes in constituent metals potentially making significant adjustments in properties.
How Is Stainless Steel Made?
Stainless steel is manufactured by a range of smelting methods that are typical of most metallurgical processing. Three of the common processes are listed below:
- An electric arc furnace uses a high current flowing between two carbon electrodes to heat the raw materials. Alloying elements of scrap and pre-made steel, chromium, etc. are added to the furnace crucible, along with iron ore and the necessary additions to refining this component, to create the stainless steel alloy. Melting and refinement occur in the furnace and the impurities float off as slag/clinker.
- Blast furnaces melt iron ore mixed with coke in the crucible, blowing oxygen through the molten iron to remove impurities that float off as slag. Once the ore has been purified, chromium and other alloying elements are added to the molten metal to create the stainless steel alloy.
- Vacuum induction melting and vacuum arc melting produce very high-purity metals, from already refined source materials (i.e., no ore is added). This process allows for more precision in the control of the composition of stainless steel alloys.
Once the stainless steel has been melted and refined, it will generally be rough cast into billets. These billets are then formed into various shapes and sizes using a range of manufacturing processes, including:
- The casting of stainless steel involves molten metal being poured into a cast cavity, to which it conforms and the cast retains the cavity shape when cooled.
- Rolling of stainless steel sees the raw billets pass through a series of precise pinch rollers, to reduce their thickness and shape the steel into sheets or other forms. This process can be performed hot or cold, to produce a variety of final materials of diverse strengths and crystalline structures.
- The forging of stainless steel requires it to be heated and then shaped by hammering or pressing it into the desired form.
- Machining stainless steel enables it to be cut and shaped using various machines, such as lathes and mills.
After the stainless steel has been formed into its final shape, it may undergo additional processing to improve its properties, such as heat treatment, polishing, or coating.
What Are the Characteristics of Stainless Steel?
Some of the characteristics of stainless steel include:
- Generally highly resistant to corrosion.
- Strong and durable—resistant to bending, cracking, and breaking.
- Non-porous and non-reactive—easy to clean and autoclave.
- Can achieve a range of quality finishes.
- Can withstand high temperatures without degrading.
- Suitable for use at cryogenic temperatures.
- Sustainable materials, in that they are 100% recyclable without loss or degradation.
What Is the Color of Stainless Steel?
Stainless steels are naturally a uniform silver in color, although various companies offer proprietary “stainless coloring” processes that are analogous to anodizing. A range of bronze to golden colors can be achieved by heating stainless steel in an oven to around 700 °C in an oxygen atmosphere. This will result in the formation of iron oxides in the surface film, which will stain with shades of yellow, gold, and brown depending on temperature and time. Stainless steel will also develop hues of blue when heated to 250 °C in air, also by an oxidation process.
What Does Stainless Steel Look Like?
Stainless steel parts are often polished to a mirror finish by electropolishing. This results in a reflective and generally silver color, but can be colored as described above. Stainless steel components can also have various types and levels of texturing added—from sandblasting to shot peening, brush finishing to photo etching.
A brushed or linished finish is often used on street furniture and building cladding, to reduce the appearance degradation that results from scratches. Figure 1 below are examples of stainless steel:
What Are the Different Types of Stainless Steel?
The basic nomenclature for broad grades of stainless steel is as follows:
1. Austenitic Stainless Steel
Austenitic stainless steel is the most common classification, offering high corrosion resistance, ductility, and toughness. It is alloyed with a minimum of 16% chromium and 6% nickel, with other metals/non-metals such as manganese, nitrogen, and sometimes molybdenum. These steels can handle salt exposure, although some brown staining is possible.
2. Martensitic Stainless Steel
This type of stainless steel is generally stronger and harder but suffers lower corrosion resistance. They contain 12–18% chromium and may also include nickel or molybdenum.
3. Ferritic Stainless Steel
Ferritic stainless steels can have a broad range of chromium content (10.5–27%) and use higher carbon content steels than austenitic types. This group is less ductile and tougher, but still has good corrosion resistance and is often used for automotive applications. These steels react less well to salt and are not generally used in marine environments.
4. Duplex Stainless Steel
Duplex stainless steels combine austenitic and ferritic stainless steels, with a carefully tuned proportion of both types of crystalline structure. They offer higher strength combined with great corrosion resistance and are often used in chemical processing and oil and gas applications.
5. Precipitation-Hardening Stainless Steel
Precipitation-hardening stainless steel is achieved by the formation of small particles, precipitated within the material, that increase its strength and hardness by inducing lattice stress. This can commonly deliver 3–4 times the strength of basic austenitic stainless steel.
What Does the Grade of Stainless Steel Mean?
The stainless steel grading system attempts to differentiate alloys by toughness, corrosion resistance, magnetic properties, and composition. The first grading system was developed by the SAE (US Society of Automotive Engineers) using a 3-digit code, with grades belonging to 100, 200, 300, 400, 500, and 600 series classifications. This was enhanced by ASTM (American Society for Testing and Materials) to a 6-digit code, known as UNS (Unified Number System) identifiers. In most cases, UNS identifiers share the same first three numbers as their AISI (American Iron and Steel Institute) equivalent.
What Are the Different Grades of Stainless Steel?
The different grades of stainless steel are listed in Tables 1-4 below:
SAE | UNS equivalent |
---|---|
SAE 201 | UNS equivalent S20100 |
SAE 202 | UNS equivalent S20200 |
SAE 205 | UNS equivalent S20500 |
SAE 254 | UNS equivalent S31254 |
SAE 301 | UNS equivalent S30100 |
SAE 302 | UNS equivalent S30200 |
SAE 302B | UNS equivalent S30215 |
SAE 303 | UNS equivalent S30300 |
SAE 303Se | UNS equivalent S30323 |
SAE 304 | UNS equivalent S30400 |
SAE 304L | UNS equivalent S30403 |
SAE 304Cu | UNS equivalent S30430 |
SAE 304N | UNS equivalent S30451 |
SAE 305 | UNS equivalent S30500 |
SAE 308 | UNS equivalent S30800 |
SAE 309 | UNS equivalent S30900 |
SAE 309S | UNS equivalent S30908 |
SAE 310 | UNS equivalent S31000 |
SAE 310S | UNS equivalent S31008 |
SAE 314 | UNS equivalent S31400 |
SAE 316 | UNS equivalent S31600 |
SAE 316L | UNS equivalent S31603 |
SAE 316F | UNS equivalent S31620 |
SAE 316N | UNS equivalent S31651 |
SAE 317 | UNS equivalent S31700 |
SAE 317L | UNS equivalent S31703 |
SAE 321 | UNS equivalent S32100 |
SAE 329 | UNS equivalent S32900 |
SAE 330 | UNS equivalent N08330 |
SAE 347 | UNS equivalent S34700 |
SAE 348 | UNS equivalent S34800 |
SAE 384 | UNS equivalent S38400 |
SAE - | UNS equivalent - |
SAE - | UNS equivalent - |
SAE | UNS equivalent |
---|---|
SAE 405 | UNS equivalent S40500 |
SAE 409 | UNS equivalent S40900 |
SAE 429 | UNS equivalent S42900 |
SAE 430 | UNS equivalent S43000 |
SAE 430F | UNS equivalent S43020 |
SAE 430FSe | UNS equivalent S43023 |
SAE 434 | UNS equivalent S43400 |
SAE 436 | UNS equivalent S43600 |
SAE 442 | UNS equivalent S44200 |
SAE 446 | UNS equivalent S44600 |
SAE - | UNS equivalent - |
SAE - | UNS equivalent - |
SAE - | UNS equivalent - |
SAE - | UNS equivalent - |
SAE - | UNS equivalent - |
SAE - | UNS equivalent - |
SAE - | UNS equivalent - |
SAE | UNS equivalent |
---|---|
SAE 403 | UNS equivalent S40300 |
SAE 410 | UNS equivalent S41000 |
SAE 414 | UNS equivalent S41400 |
SAE 416 | UNS equivalent S41600 |
SAE 416Se | UNS equivalent S41623 |
SAE 420 | UNS equivalent S42000 |
SAE 420F | UNS equivalent S42020 |
SAE 422 | UNS equivalent S42200 |
SAE 431 | UNS equivalent S41623 |
SAE 440A | UNS equivalent S44002 |
SAE 440B | UNS equivalent S44003 |
SAE 440C | UNS equivalent S44004 |
SAE - | UNS equivalent - |
SAE - | UNS equivalent - |
SAE - | UNS equivalent - |
SAE - | UNS equivalent - |
SAE - | UNS equivalent - |
SAE | UNS equivalent |
---|---|
SAE 501 | UNS equivalent S50100 |
SAE 502 | UNS equivalent S50200 |
SAE Duplex | UNS equivalent Duplex |
SAE 2205 | |
SAE Super duplex | UNS equivalent Super duplex |
SAE 2507 | UNS equivalent S32750 |
SAE - | UNS equivalent - |
SAE - | UNS equivalent - |
SAE - | UNS equivalent - |
SAE - | UNS equivalent - |
SAE - | UNS equivalent - |
SAE - | UNS equivalent - |
SAE - | UNS equivalent - |
SAE - | UNS equivalent - |
SAE - | UNS equivalent - |
SAE - | UNS equivalent - |
SAE - | UNS equivalent - |
What Grade of Stainless Steel Is Best?
The best grade for an application is a decision that requires careful consideration of requirements for: strength, corrosion resistance, cost, working methods, and tools. These are the typical considerations that must be integrated into a material selection process for a grade of stainless steel for any application, including the level of formability required and the degree of corrosion resistance.
What Are the Properties of Stainless Steel?
While there are well-prepared evaluations of all properties of all grades and types of stainless steel, the most important are reviewed below:
What Are the Physical Properties of Stainless Steel?
The physical properties of stainless steel are shown in Table 5 below:
Property | Value/Notes |
---|---|
Property Density | Value/Notes 7.75 x 103 to 8.05 x 103 kg/m3 |
Property Ductility | Value/Notes Typical annealed austenitic stainless steel delivers 70% elongation at break |
Property Malleability | Value/Notes Highly malleable when annealed, some grades work harden very quickly and lose malleability |
Property Tensile strength (general grades) | Value/Notes 500–750 MPa |
Property Yield strength (general grades) | Value/Notes 500–650 MPa |
Property Tensile strength (precipitation hardened) | Value/Notes 850–1,700 MPa |
Property Yield strength (precipitation hardened) | Value/Notes 520–1,500 MPa |
Property Melting point | Value/Notes 1,370–1,420 °C |
Property Thermal conductivity is poor (typical) | Value/Notes 15 W/(mK) |
Property Electrical conductivity is poor (typical) | Value/Notes 1.33 m/Ωmm² |
Property Magnetic permeability – austenitics (HIGHLY variable by grade and work hardening) | Value/Notes 1.003 to 1.005 when measured at magnetizing forces of 200 oersteds (16k A/m) |
Property Magnetic permeability – ferritics (HIGHLY variable by grade and work hardening) | Value/Notes Up to 6.0 for annealed 304 grade, when measured at magnetizing forces of 200 oersteds (16k A/m) |
Table Credit: https://matweb.com/
Property | Notes |
---|---|
Property Corrosion resistance | Notes Ranges widely from good to moderate in non-salt environments, through good to moderate in salt environments, and good to poor in hot/salt/caustic/acidic environments, depending on grade |
Property Chemical resistance | Notes Generally high to very high, various grades have particular resilience that suit selected difficult environments |
Property Heat resistance | Notes Generally high to very high. Up to 2,000 °C for 330 grade |
Property Cold resistance | Notes -200 °C for non-stabilized 304-grade |
Property Sensitization corrosion | Notes Can be severe in 304 and 316 grades at welds—requires low heat and low-carbon fillers |
What Are the Applications of Stainless Steel?
Some applications of stainless steel are listed below:
1. Kitchen Appliances and Utensils
Stainless steel is a widely employed choice in kitchen equipment of all kinds. It’s a durable and long-lasting material that can withstand heavy and constant use in the kitchen. It is resistant to corrosion, which is important in a food environment where there is constant exposure to water and other liquids. This results in no taint of food. It is a hygienic material that is easy to clean and maintain and withstands the most aggressive cleaning. It does not absorb food odors or flavors and is resistant to stains.
2. Medical Equipment
Stainless steel is a widely applied material choice in the medical sector for various equipment and devices. A main driver of this is its corrosion resistance, which prevents surface degradation by addition or pitting. It makes durable products that can tolerate the autoclave cleaning and aggressive chemical sterilization processes necessary for medical equipment. Since it is non-porous, it is easy to clean to extreme hygiene standards. Stainless steel is also a biocompatible material, so it is rarely actively rejected when implanted into patients. This property results in stainless steel being tolerated and durable in medical implants and devices that come into direct contact with the human body.
3. Automotive Industry
Stainless steel is an important material choice in many automotive components, due to its general strength, durability, and resistance to corrosion. It is used in exhaust systems, fuel tanks, external decorative/finishing applications, and sometimes in whole-body (monocoque) construction.
A primary benefit of stainless steel in automotive applications is corrosion resistance. The often high-salt environment results in rapid corrosion of even well-protected basic steels, quickly degrading vehicles. Stainless steel is resistant to rust and corrosion, making it an ideal material choice for automotive components that are exposed to harsh conditions, despite the mild salt vulnerability of some lower-cost alloys.
In exhaust, engine, suspension, and transmission parts it is durable and can withstand high temperatures and mechanical stresses. In exhaust systems, it can handle high-temperature, high-vibration applications without fracturing or corroding.
4. Construction Industry
Stainless steels are important in the construction sector in that they are widely used in sheet form for cladding purposes, lending high environmental resistance, but not as structural components. Stainless steels also feature extensively in “finishing” components such as flashings for window and door installations, and as structural and functional components for doors, windows, and balustrades/handrails. Stainless steels are widely employed in functional piping and exterior ducting, where corrosion resistance is paramount both from environmental causes and from potentially contaminated materials carried within pipes.
5. Aerospace Industry
Stainless steels find wide application in gas-turbine technologies, which have been a key driver of research into higher-performing alloys and processing methods, such as precipitation-hardening alloys. The materials compensate for their relatively high weight, in the highest-stress and higher-temperature applications by bringing extreme tolerances and strength to otherwise vulnerable parts. The use of stainless steel in landing gear is also critically important—high-stress tolerance is important, but landing gear encounters harsh conditions with complex mechanics exposed to runway environments that are wet, abrasive, and often chemically contaminated.
6. Chemical and Petrochemical Industry
Stainless steel is much favored in these sectors as good alloy selection and correct processing methods make remarkably stable and durable components for harsh conditions. It brings high-temperature tolerance, high resistance to vibration fatigue, great chemical resistance, and low maintenance needs to piping, valve gear, vessels, and structural parts.
7. Marine Industry
Stainless steel is a mainstay of small components in the marine sector. Marine environments are harsh in that materials undergo large temperature swings, constant wet-salt exposure, and high mechanical stresses. The material is widely used for engine parts, general fittings, anchors/chains, capstans, structural elements, and much more—from small pleasure craft to supertankers. Alloy selection is critical, in that some alloys have cosmetic and even pinhole/pitting sensitivity to salt environments. The use of the most chemically resilient alloys is important for both long-term durability and short-term cosmetic reasons.
8. Jewelry
Stainless steel is widely used in “costume” (i.e., non-precious) jewelry. It allows fine components of high strength and polished “silver” appearance, while being low cost to use, compared with precious metals of lesser corrosion resistance.
What Are the Benefits of Stainless Steel?
Listed below are some benefits of stainless steel:
- Corrosion Resistance: Stainless steel is highly resistant to corrosion and rust due to the presence of chromium in the alloy. This makes it suitable for use in harsh environments, such as marine or chemical industry applications (by careful alloy specification) and reduces the need for maintenance and replacement.
- Durability: Stainless steel is a strong and durable material with a high strength-to-weight ratio. It is resistant to deformation and can withstand high stress without breaking or cracking, making it suitable for use in demanding applications.
- High Cosmetic Facility: Stainless steels lend a modern and enduring appearance to many applications, being essentially unchanging and maintenance-free in the great majority of applications.
- Weldability: Most stainless steel alloys are highly weldable, making the assembly of complex systems from individual parts a clean, watertight, and permanent process. Care must be taken with the altered corrosion properties of welded areas.
- Formability: Being generally fairly malleable materials and in many cases of moderate to high ductility, stainless steels provide many options in manufacturing processes that allow the manufacture of complex and intricate components for a wide range of purposes—from valve gates to turbine blades, from jewelry to kitchen utensils.
What Are the Limitations of Stainless Steel?
Listed below are the limitations of stainless steel:
- Cost: Stainless steel can be more expensive than other materials, such as carbon steel or aluminum, depending on the specific grade and application.
- Hardness: Some grades of stainless steel can be too hard for certain applications, making them difficult to machine or shape.
- Work Hardening Embrittlement: Overstressed components that are repeatedly taken close to their elastic limit can, in some alloys, work harden severely, and this can lead to brittle failure.
- Weight: While stainless steel is often a preferred choice from a strength and corrosion perspective, its high density makes it impractical for lightweight equipment in many cases.
- Shape: Stainless steel is hard to work with and requires special tools and skills, compared with less intractable materials.
- Environment: While highly corrosion resistant, particular grades and types of stainless steel have poorer resistance to salt corrosion.
- Temperature: Some grades are suited to cryogenic applications, while others have extremely high-temperature limits for safe use. Care is needed in specifying alloys for extreme temperature applications.
Why Use Stainless Steel?
Overall, stainless steels offer huge benefits in a surprisingly wide range of environmental, structural, cosmetic, and engineering applications. They bring durability, low maintenance, high-quality cosmetics, and great design flexibility when used correctly.
How Long Will Stainless Steel Last?
Well-specified, well-designed, and well-cared-for stainless steel components have functional life expectancies that are essentially unlimited. Examples abound from the early stages of the widespread use of the materials in kitchenware. It is common for the “failure” of, for example, cookpots to be the result of handle attachment methods. The same is true for a common construction application of stainless steel, in window stays. It is common for these components to remain in service 30–50 years after they were made. It is also common for the stainless steel components of stays to remain serviceable when the bearings/couplings between them have failed. These design failure issues are not directly a result of the use of stainless steel, where the components themselves have unlimited endurance.
Is Stainless Steel Better Than Carbon Steel?
Choosing which is better between stainless and carbon steel depends on many factors. In contexts where the particular strengths of stainless steels compensate for the weaknesses of carbon steels, the upgrade to stainless is a wise choice for durability, lifespan, and cosmetic reasons. Carbon steels, on the other hand, are exactly the right solution for low-cost, high-strength, and highly durable components in many applications. However, where the risk of corrosion is present, the durability weakness of carbon steel is countered very effectively by the use of stainless steel.
Can Stainless Steel Get Rusted?
Yes, stainless steel gets rusted. Some stainless steels have particular chemical sensitivities and this can result in corrosion. For example, 316 stainless steel fuel tanks in marine environments can see a form of tunneling corrosion that leads to pinholes, due to rust. Stainless steel fittings on boats/ships can bleed brown (iron oxide) stains onto surrounding areas as the iron content responds slowly to salt presence. Welded stainless steel can develop localized sensitivities to corrosion in non-salt environments.
Is Stainless Steel Stronger Than Metal?
Stainless steels of the precipitation-hardening class are among the strongest metals available for mass-produced components. When specified for maximum strength, stainless steel can easily be the equivalent of the strongest carbon steel after heat treatment. For more information, see our guide on Metal.
Is Stainless Steel an Alloy or Metal?
Stainless steels are a broad family of complex alloys of medium- and low-carbon steels, chromium, nickel, manganese, molybdenum, copper, silicon, nitrogen, and other elements. For more information, see our guide on Alloys.
Is Stainless Steel Waterproof?
Yes, stainless steel is waterproof. All stainless steels resist corrosion from fresh water and all are impervious barriers to water unless mechanically pierced. No matter the thickness of the material, water will not pass through it.
What Is the Difference Between Stainless Steel and Ordinary Steel?
The addition of alloying agents such as chromium, nickel, manganese, molybdenum, copper, silicon, and nitrogen alters the properties of the steel, exploiting its fundamental strengths but enhancing various of its weaknesses. The most important change is the addition of chromium (without which the alloy is not stainless steel). This induces a high degree of corrosion protection, by forming a chromium oxide film on the steel in a self-healing coating that renews when scratched (in an oxygen atmosphere).
Summary
This article presented stainless steel, explained what it is, and discussed its various applications. To learn more about stainless steel, contact a Xometry representative.
Xometry provides a wide range of manufacturing capabilities and other value-added services for all of your prototyping and production needs. Visit our website to learn more or to request a free, no-obligation quote.
Disclaimer
The content appearing on this webpage is for informational purposes only. Xometry makes no representation or warranty of any kind, be it expressed or implied, as to the accuracy, completeness, or validity of the information. Any performance parameters, geometric tolerances, specific design features, quality and types of materials, or processes should not be inferred to represent what will be delivered by third-party suppliers or manufacturers through Xometry’s network. Buyers seeking quotes for parts are responsible for defining the specific requirements for those parts. Please refer to our terms and conditions for more information.
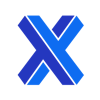