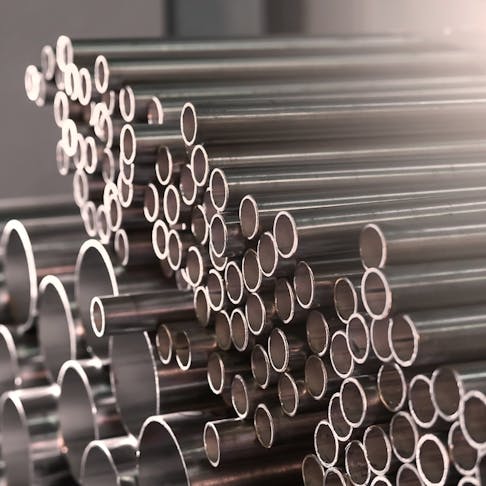
Types of Stainless Steel and Stainless Steel Grades
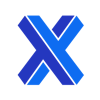
The term stainless steel is applied to a family of carbon steel alloys that contain large amounts of chromium. The alloys can have different compositions but all exhibit some of the same behaviors. Stainless steels are iron-based alloys with a minimum chromium content of 10.5%. The chromium generates a self-healing chromium-oxide layer on the surface that prevents the underlying iron from rusting. Stainless steel types fall within three single-phase structure classes, a two-phase structure class, and a single heat treatment class. These five classes of stainless steel are: martensitic, austenitic, ferritic, duplex, and precipitation-hardenable.
This article will discuss the different types and grades of stainless steel.
Martensitic Stainless Steel
This group of stainless steels has a martensitic crystalline structure in the hardened conditions. Martensitic stainless steel has a body-centered tetragonal (BCT) crystalline structure composed of iron, chromium, and carbon. Chromium content ranges from 10.5-18%, with carbon not exceeding 1.2%. The 403 grade is the basic martensitic stainless; others differ in their alloying compositions to achieve different effects. The martensitic group includes: 403, 410, 414, 431, 422, 420, 416, and 440.
This group is typically used in applications like: jet engines, gas turbines, valve trains, cutlery, petrochemical equipment, and medical instruments.
Useful mechanical properties of martensitic stainless steel include:
- Moderate work hardening rate
- Heat treatability
- Good ductility and toughness
- Good tensile strength
- Good creep and fatigue resistance
- Magnetic response
Austenitic Stainless Steel
Austenitic stainless steels are the most widespread types in terms of alloys and usage. They possess an austenitic crystalline structure (face-centered cubic or FCC) similar to that of high-temperature iron. This group can be divided into two categories based on the main alloying elements: chromium-nickel (Cr-Ni) alloys and chromium-manganese-nitrogen (Cr-Mn-N) alloys.
The general composition of the austenitic stainless steel group consists of: 16-26% chromium, up to 0.15% carbon, up to 35% nickel, up to 15% manganese, 0.75-3% silicon, and 0.045-0.2% phosphorus. Additionally, some types include other alloying elements like: sulfur, nitrogen, molybdenum, selenium, copper, titanium, tantalum, niobium, and cobalt. The standard austenitic group includes: 201, 202, 205, 301, 302, 303, 304, 305, 308, 309, 310 314, 316, 317, 321, 330, 347, 348, and 384.
Applications include: cutlery, fasteners, pressure vessels, chemical mixing vessels, exhaust systems, and hydraulic components.
Mechanical properties that make austenitic stainless steel useful include:
- Excellent work hardening rate
- Good ductility and toughness
- Good tensile strength
- Good creep and fatigue resistance
- Moderate corrosion resistance (up to 650 °C)
- Moderate temperature resistance (up to 650 °C)
- Excellent weldability
Ferritic Stainless Steel
Ferritic stainless steels possess a ferritic body-centered cubic (BCC) crystalline structure. The main alloying element, chromium, makes up between 10.5% and 30% and carbon never exceeds 0.2%. These metals are thus classed as iron-chromium (Fe-Cr) alloys. Other common alloying elements include: molybdenum, silicon, aluminum, titanium, and niobium. Titanium and aluminum are important elements for ensuring a ferritic structure. The base ferritic stainless steel grade is 430 and alterations to the alloying formula are made to achieve certain effects. 430 and 434 are first-generation standard-grade ferritic stainless steels, while 409 and 439 are second-generation standard grades. 444 is a third-generation superferritic stainless steel. The superferritic stainless steel class remains free of austenitic structures at all temperature ranges.
Applications include: food handling equipment, aqueous chloride solution piping, moderate-temperature chemical heat exchangers (up to 250 °C), domestic ovens, kitchen sinks, and solar panel support frames for desert environments.
Mechanical properties of ferritic stainless steel are:
- Low work hardening rate
- Moderate ductility and toughness
- Good tensile strength (low temperature)
- Good creep and fatigue resistance (low temperature)
- Moderate corrosion resistance
- Moderate temperature resistance
- Poor weldability
- Excellent magnetic response
Duplex Stainless Steel
Duplex stainless steel possesses a mixture of ferritic structure (body-centered cubic), and austenitic structure (face-centered cubic). The amount of each phase is dependent on composition and heat treatment. Duplex steel’s corrosion resistance is similar to that of austenitic stainless steel but it has better tensile and yield strengths and improved resistance to chloride stress corrosion cracking (SCC). Duplex steels also exhibit strong resistance to pitting corrosion. Its toughness rating falls roughly between ferritic and austenitic steels.
The principal alloying elements are chromium and nickel. Typical compositions of duplex stainless steels include: 22-26% chromium, 4-7% nickel, up to 4.5% molybdenum, ~0.7% copper, ~0.7% tungsten, and 0.08-0.35% nitrogen. Carbon is intentionally kept below 0.06%, which markedly improves corrosion resistance. Duplex stainless steels may be grouped into four classes according to composition. These are also known as: lean duplex 2304, standard duplex 2205, super duplex class 2505, super duplex class 2507, and hyper duplex class which includes 2707.
Applications include: the oil and gas industry, aqueous chloride plants, seawater desalination plants, and holding tanks for wet CO₂ gasses.
Mechanical properties of duplex stainless steel are:
- High work hardening rate
- Not heat treatable
- Good ductility and toughness
- Excellent tensile strength (moderate temperature)
- Good creep and fatigue resistance (moderate temperature)
- Excellent corrosion resistance
- Moderate temperature resistance
- Moderate weldability
- Moderate magnetic response
201 Stainless Steel
201 stainless steel is an austenitic formulation that contains chromium, nickel, manganese, and nitrogen. Manganese and nitrogen replace some of the nickel in its structure in order to lower nickel content but retain corrosion resistance. Lowering the nickel content makes the steel more cost-effective.
201 steel falls within the Cr-Mn-N alloy group of austenitic stainless steels. The designations vary by organization; it’s known as 201 for AISI, X12CrMnNiN17-7-5 for DIN, and 1.4372 for EN. The typical composition of 201 SS is: 0.15% C, 5.5-7.5% Mn, 1% Si, 16-18% Cr, 3.5-5.5% Ni, 0.045% P, 0.015% S, and 0.25% N. 201 stainless steel is primarily used for: food-handling components such as washing sinks, decorative architectural elements, and deep-drawn, cold-formed components.
Annealed 201 is nonmagnetic but becomes moderately responsive to magnets as the material is cold-worked. 201 steel is also hardened through cold working, and thermal treatment will not alter it. Some properties of 201 steel are:
- Good work-hardening rate
- Moderate corrosion resistance
- Good ductility
- Low-temperature resistance
- Good weldability
202 Stainless Steel
202 stainless steel is an austenitic type that contains chromium, nickel, manganese, and nitrogen. Nickel and iron are partially replaced by manganese and nitrogen to lower nickel content and retain corrosion resistance.
202 steel falls within the Cr-Mn-N alloy group of austenitic stainless steels. The different standardization models for 202 stainless steel are: 202 AISI, X12CrMnNiN18-9-5 DIN, and 1.4373 EN. A typical composition for 202 stainless steel is: 0.15% C, 7.5-10% Mn, 1% Si, 17-19% Cr, 4-6% Ni, 0.045% P, 0.015% S, and 0.25% N.
Annealed 202 is nonmagnetic but becomes weakly responsive to magnets as the material is cold-worked. A few other properties are as follows:
- Cold working hardens the metal
- Good work hardening rate
- Moderate corrosion resistance
- Good ductility
- Low-temperature resistance
- Good weldability except through oxyacetylene welding
202 stainless steel is primarily used for: restaurant equipment, vitreous safety railings, and hotel equipment.
205 Stainless Steel
205 stainless steel is an austenitic style that contains chromium (16.5-18%), nickel (1-1.75%), manganese (14-15.5%), and nitrogen (0.4%). Nickel is largely replaced by manganese and nitrogen to lower nickel content but retain corrosion resistance.
205 steel falls within the Cr-Mn-N alloy group of austenitic stainless steels. Annealed 205 is nonmagnetic but becomes weakly responsive to magnets if the material is cold-worked. 205 steel is hardened through cold working, and thermal treatment will not work on it. Other properties of 205 steel are:
- Good work hardening rate
- Moderate corrosion resistance
- Good ductility
- Moderate temperature resistance
- Good weldability through conventional welding techniques
205 stainless steel is primarily used for: cookware and cutlery, decorative architectural elements, deep-drawn and cold-formed components, and food and beverage equipment.
2507 Stainless Steel
2507 stainless steel is a duplex type that contains chromium (25%), nickel (7%), molybdenum (4%), nitrogen (0.28%), tungsten (0.7%), and copper (0.7%). 2507 steel falls within the Fe-25Cr-7Ni-3.5Mo-0.25N-W-Cu alloy group of super duplex stainless steels. The different standardization models for 2507 stainless steel are: 2507 AISI, X2CrNiMoCuWN25-7-4 DIN, and 1.4501/1.4410 EN.
2507 is magnetic because the duplex stainless steel contains ferritic structures as well austenitic ones. Duplex 2507 is hardened through cold working and thermal treatment. Some of its properties are:
- Low work hardening rate
- Excellent corrosion resistance
- Less ductile than normal austenitic stainless steel
- Excellent temperature resistance with a PREN (Pitting Resistance Equivalent Number) of 43
- Good weldability through conventional welding techniques
2507 stainless steel is primarily used in: desalination plants, coal power plants, chemical process plants, and the pulp and paper industry.
301 Stainless Steel
301 stainless steel is an austenitic steel that contains high levels of chromium and nickel. It contains the lowest Cr-Ni alloying content of the Cr-Ni austenitic group. 301 SS is composed of 0.05-0.15% C, 2% Mn, 2% Si, 16-19% Cr, 6-9.5% Ni, 0.045% P, 0.015% S, 0.11% N, and 0.8% Mo. The different standardization models for 301 stainless steel are: 301 AISI, X10CrNi18-8 DIN, and 1.4310 EN.
AISI 301 is nonmagnetic because of its austenite structure. Its properties include:
- High work hardening rate
- Good corrosion resistance
- Good ductility
- Good temperature resistance with retained toughness
- Can be tempered through cold working
- Good weldability through conventional welding techniques
301 stainless steel is primarily used for: springs (such as in toys, office equipment, and medical instruments), utensils, watchbands, and spring washers.
302 Stainless Steel
302 stainless steel is an austenitic stainless steel that contains high levels of chromium and nickel. Its typical composition is: 0.15% C, 2% Mn, 1% Si, 17-19% Cr, 8-10% Ni, 0.045% P, and 0.03% S.
It is part of the Cr-Ni austenitic stainless steel group and is therefore not magnetic. Other properties of 302 are:
- Good work hardening rate
- Good corrosion resistance
- Moderate ductility
- Excellent temperature resistance with retained toughness
- Can be hardened through cold working
- Excellent weldability through shielded gas welding techniques
302 stainless steel is primarily used for: household equipment (i.e., dishwashers, blenders), formed wire, cryogenic applications, and in the stamping industry.
302B Stainless Steel
302B stainless steel is an austenitic type that contains high levels of chromium (17-19%) and nickel (8-10%). Other elements are: 0.15% C, 2% Mn, 2-3% Si, 0.045% P, and 0.03% S.
302B is very similar to 302 but has a greater silicon content. It is part of the Cr-Ni austenitic stainless steel group and is not magnetic. 302B alloy has the following properties:
- Good work hardening rate
- Good corrosion resistance
- Moderate ductility
- Excellent temperature resistance with retained toughness
- Can be hardened through cold working
- Excellent weldability through shielded gas welding techniques
302B stainless steel is primarily used for: mesh (i.e., wire mesh, screen mesh, perforated sheet mesh), formed wire (i.e., springs, wire rope), cryogenic applications, and as part of the stamping industry.
303 Stainless Steel
303 stainless steel is a general-purpose free-machining austenitic stainless steel that contains high levels of chromium (18%) and nickel (9%) with increased sulfur content (0.15-0.35%) and added copper (1%). It is part of the Cr-Ni austenitic stainless steel group. The different standardization models for 303 stainless steel: are 303 AISI, X8CrNiS18-9 DIN, and 1.4305 EN.
303 SS is primarily used for: shafts, aircraft components, bushings, and fasteners. Some of its properties are:
- Nonmagnetic
- Moderate work hardening rate
- Moderate corrosion resistance
- Good ductility
- Good temperature resistance
- Can be hardened through cold working
- Very poor weldability
303Se Stainless Steel
303Se stainless steel is a general-purpose free-machining austenitic stainless steel. Sulfur content (0.06%) is reduced and copper is removed while selenium (0.15%) is added. A typical composition includes: 0.15% C, 2% Mn, 1% Si, 17-19% Cr, 8-10% Ni, and 0.2% P. The different standardization models for 303Se stainless steel are: 303Se AISI, X9CrNi18-9 DIN, and 1.4325 EN.
303Se stainless steel is part of the Cr-Ni austenitic stainless steel group and is not magnetic. Some of its properties are:
- Moderate work hardening rate
- Good corrosion resistance
- Good ductility
- Good temperature resistance
- Can be hardened through cold working
- Very poor weldability
303Se stainless steel is primarily used for: shafts, aircraft components, bushings, and fasteners.
304 Stainless Steel
304 stainless steel is a general-purpose austenitic stainless steel that contains high levels of chromium (18%) and nickel (10%). The typical composition of 304 stainless steel is: 0.07% C, 2% Mn, 1% Si, 17.5-19.5 Cr, 8-10.5% Ni, 0.045% P, and 0.015% S. The different standardization models for 304 stainless steel are: 304 AISI, X5CrNi18-10 DIN, and 1.4301 EN.
304 is part of the Cr-Ni austenitic stainless steel group and is not magnetic. Other properties include:
- Moderate work hardening rate
- Good corrosion resistance
- Good ductility
- Excellent temperature resistance with retained toughness
- Can be hardened through cold working
- Excellent weldability through conventional welding techniques
304 stainless steel is primarily used for: pressure vessels, high-pressure flanges, pumps, and petrochemical processing plants.
304H Stainless Steel
304H stainless steel is an austenitic stainless steel that is similar to 304 alloys but contains more carbon. Its typical composition is: 0.04-0.08 C, 2% Mn, 1% Si, 17-19% Cr, 8-11% Ni, 0.035% P, 0.015% S, and 0.1% N. The different standardization models for 304H stainless steel are: 304H AISI, X6CrNi18-10 DIN, and 1.4948 EN.
It is part of the Cr-Ni austenitic stainless steel group and is not magnetic. Other properties include:
- Good work hardening rate
- Good corrosion resistance
- Moderate ductility
- Excellent temperature resistance with retained toughness
- Can be hardened through cold working
- Excellent weldability through conventional welding techniques
304H stainless steel is primarily used for: pressure vessels, high-pressure flanges, pumps,
304L Stainless Steel
304L stainless steel is austenitic stainless steel that is similar to 304 alloys except with less carbon. Its typical composition includes: 0.03% C, 2% Mn, 1% Si, 17.5-20% Cr, 8-12% Ni, 0.045% P, 0.015% S, and 0.11% N. The different standardization models for 304L stainless steel are: 2CrNi18-9 and X2CrNi19-11 for DIN, and 1.4307 and 1.4306 for EN.
It is part of the Cr-Ni austenitic stainless steel group and is not magnetic due to the austenitic crystal structure. 304L alloy’s properties are:
- Moderate work hardening rate
- Good corrosion resistance
- Good ductility and excellent temperature resistance with retained toughness
- Hardenable through cold working
- Highly weldable using conventional welding techniques.
304H stainless steel is primarily used for: pressure vessels, medical equipment, mining equipment, and nuclear power generation.
304N Stainless Steel
304N stainless steel is an austenitic stainless steel that is similar to 304 alloys but with more nitrogen. Its typical composition is 0.06% C, 2% Mn, 1% Si, 18-20 Cr, 8-11% Ni, 0.045% P, 0.015% S, and 0.12-0.22% N. The different standardization models for 304N stainless steel are: 304N AISI, X5CrNiN19-9 DIN, and 1.4315 EN.
This alloy is part of the Cr-Ni austenitic stainless steel group and is therefore not magnetic. Some of its properties are:
- Low work hardening rate
- Good corrosion resistance
- Good ductility
- Good temperature resistance
- Can be hardened through cold working
- Excellent weldability through conventional welding techniques
304N stainless steel is primarily used for: pressure vessels, liquid natural gas production and storage, vacuum testing chambers, and natural gas denitrogenation and decarburization columns.
S30430 Stainless Steel
S30430 stainless steel is an austenitic stainless steel that is also known as 304 Cu. S30430 is similar to 304 alloys but its carbon (0.04%), chromium (17-19%), nickel (8.5-10.5%), and iron (63.9 to 72%) are partially substituted with copper (3-4%). The different standardization models for S30430 stainless steel are: S30430 AISI, 3CrNiCu18-9-4 DIN, and 1.4567 EN.
304Cu is part of the Cr-Ni austenitic stainless steel group. It is not magnetic due to the austenitic structure. Other properties include:
- Poor work hardening rate
- Good corrosion resistance
- Excellent ductility
- Good temperature resistance
- Can be hardened through cold working
- Good weldability through conventional welding techniques
S30430 stainless steel is used in the production of light machine screws, self-tapping screws, set screws, bolts, rivets, and specialized fasteners.
305 Stainless Steel
305 stainless steel is an austenitic metal that contains high levels of chromium (17-19%). Its typical composition is: 0.06% C, 2% Mn, 1% Si, 11-13% Ni, 0.045% P, 0.015% S, and 0.11% N. The different standardization models for 305 stainless steel are: 305 AISI, X4CrNi18-12 DIN, and 1.4303 EN.
It is part of the Cr-Ni austenitic stainless steel group and is not magnetic. Other properties include:
- Poor work hardening rate
- Good corrosion resistance
- Excellent ductility
- Good temperature resistance.
- Can be hardened through cold working
- Poor weldability through conventional welding techniques
305 stainless steel is primarily used in: acid production machinery, food and beverage equipment, and deep-drawn components.
308 Stainless Steel
308 stainless steel is an austenitic type that contains high levels of chromium (19-21%). Its typical composition also includes: 0.08% C, 2% Mn, 1% Si, 10-12% Ni, 0.045% P, 0.03% S. The different standardization models for 308 stainless steel are: 308 AISI, 1.4303 DIN, and 1.4316 EN.
This alloy is part of the Cr-Ni austenitic stainless steel group and is nonmagnetic. Some of its properties include:
- Moderate work hardening rate
- Good corrosion resistance
- Good ductility
- Excellent temperature resistance with retained toughness
- Can be hardened through cold working
- Excellent weldability through conventional welding techniques
308 stainless steel is primarily used for welding, so it’s found in filler wires and electrodes.
309 Stainless Steel
309 stainless steel is an austenitic steel that contains high levels of chromium (19-21%) and nickel (11-13%). It typically also contains: 0.2% C, 2% Mn, 1.5-2.5% Si, 0.045% P, 0.015% S, and 0.11 N. The different standardization models for 309 stainless steel are: 309 AISI, X15CrNiSi20-12 DIN, and 1.4828 EN.
309 is part of the Cr-Ni austenitic stainless steel group and thus is not magnetic. Some of its properties are:
- Moderate work hardening rate
- Good corrosion resistance
- Good ductility
- Excellent temperature resistance with retained toughness
- Can be hardened through cold working
- Moderate weldability through conventional welding techniques
309 stainless steel is primarily used for: waste treatment (i.e., incinerators, kilns, calciners), power generation (coal burners), paper mill equipment, and fluidized bed furnaces (i.e., grid, piping, wind boxes).
310 Stainless Steel
310 stainless steel is a general-purpose, temperature-tolerant austenitic metal that contains high levels of chromium (24-26%) and nickel (19-22%). The remainder is usually: 0.25% C, 0.2% Mn, 1.5% Si, 0.045% P, and 0.03% S. It is part of the Cr-Ni austenitic stainless steel group, so it is not magnetic. Some 310 properties are:
- Moderate work hardening rate
- Good corrosion resistance
- Good ductility
- Excellent temperature resistance with retained toughness
- Can be hardened through cold working
- Moderate weldability through conventional welding techniques
310 stainless steel is primarily used for: furnaces (i.e., burners, doors, recuperators, coal combustors), cryogenic components, thermal processing (i.e., burner grids, doors, fans), and cement plants (i.e., burners, shields, feeders).
314 Stainless Steel
314 stainless steel is an austenitic type that contains high levels of chromium (24-26%), nickel 19-22%, and silicon (1.5-2.5%). Its typical composition includes: 0.2% C, 2% Mn, 0.045% P, 0.015% S, and 0.11% N. The different standardization models for 314 stainless steel are: 314 AISI, X15CrNiSi25-21 DIN, and 1.4841 EN.
As part of the Cr-Ni austenitic stainless steel group, it is not magnetic. Other properties include:
- Moderate work hardening rate
- Good corrosion resistance
- Good ductility
- Excellent temperature resistance with retained toughness
- Can be hardened through cold working
- Good weldability through conventional welding techniques
314 stainless steel is primarily used for: furnace conveyors, heat exchangers, and high-temperature applications.
316 Stainless Steel
316 stainless steel is an austenitic steel that falls within the Cr-Ni alloy group. It contains chromium (16.5-18.5%), nickel (10-13%), and molybdenum (2-2.5%). Other components include: 0.07% C, 2% Mn, 1% Si, 0.045% P, 0.015% S, and 0.11% N. The different standardization models for 316 stainless steel are: 316 AISI, X5CrNiMo17-12-2 DIN, and 1.4401 EN.
Annealed 316 stainless steel is nonmagnetic due to its austenitic structure. Some of its properties are:
- Good work hardening rate
- Good corrosion resistance
- Good ductility
- Good temperature resistance
- Hardened through cold working, and thermal treatment will not work
- Good weldability through conventional welding techniques
316 stainless steel is primarily used for: pumps, high-pressure flanges, pressure vessels, and heat exchangers.
316F Stainless Steel
Alloy 316F is similar to 316, but nitrogen is partially substituted with carbon and nickel. Its typical composition is: 0.08% C, 2% Mn, 1% Si, 16-18% Cr, 10-14% Ni, 0.2% P, 0.1% S, and 1.75-2.5% Mo. The different standardization models for 316F stainless steel are 316F AISI and 1.4427 EN.
316F stainless steel is a nonmagnetic austenitic member of the Cr-Ni alloy group. Its properties include:
- Moderate work hardening rate
- Good corrosion resistance at elevated temperatures
- Good ductility
- Good temperature resistance
- Hardened through cold working, and thermal treatment will not work
- Good weldability through conventional welding techniques
316F stainless steel is primarily used for rubber processing and surgical implants and in the pulp and paper industry.
316H Stainless Steel
Alloy 316H is similar to 316 but contains more carbon (0.04-0.08%) and is stabilized by boron (0.0015-0.005%). Its typical composition includes: 2% Mn, 1% Si, 16.5-18.5% Cr, 10-13% Ni, 0.035% P, 0.015% S, 0.11% N, 2-2.5% Mo. The different standardization models for 316H stainless steel are: 316H AISI, X6CrNiMoB17-12-2 DIN, and 1.4919 EN.
It is nonmagnetic due to the austenite steel structure. Alloy 316H has the following properties:
- Moderate work hardening rate
- Good corrosion resistance at elevated temperatures
- Good ductility with excellent temperature resistance
- Hardened through cold working, and thermal treatment will not work
- Good weldability through conventional welding techniques
316H stainless steel is primarily used for: power generation, wastewater treatment, medical equipment, and in the pulp and paper industry.
316L Stainless Steel
Alloy 316L is similar to 316 but contains less carbon (0.03%) than 316 and slightly more molybdenum (2-3%). The remainder of its composition is usually: 2% Mn, 1% Si, 16.5-19% Cr, 10-15% Ni, 0.045% P, 0.015% S, and 0.11% N. The different standardization models for 316L stainless steel are shown in Table 1:
AISI | DIN | EN |
---|---|---|
AISI 316L | DIN X2CrNiMo17-12-2 | EN 1.4404 |
AISI 316L | DIN X2CrNiMo17-12-3 | EN 1.4432 |
AISI 316L | DIN X2CrNiMo18-14-3 | EN 1.4435 |
AISI 316L | DIN X3CrNiMo17-13-3 | EN 1.4436 |
316L is nonmagnetic due to the austenite steel structure. Other properties are:
- Moderate work hardening rate
- Good corrosion resistance at elevated temperatures
- Good ductility
- Good temperature resistance
- Hardened through cold working, and thermal treatment will not work
- Good weldability through conventional welding techniques
316L stainless steel is primarily used for marine applications, petroleum refining, textile production, and chemical processing (i.e., pressure vessels, holding tanks, heat exchangers).
316Ti Stainless Steel
316Ti stainless steel is a nonmagnetic austenitic stainless steel that is similar to 316, but is stabilized by titanium (0.7%). Typical compositions contain: 0.08% C, 2% Mn, 1% S, 16.5-18.5% Cr, 10.5-13.5% Ni, 0.045% P, 0.015% S, and 2-2.5% Mo. The different standardization models for 316Ti stainless steel are: 316Ti AISI, X6CrNiMoTi17-12-2 DIN, and 1.4571 EN.
316 stainless steel does work harden and is not hardenable through heat treatment. Its properties include:
- Good corrosion resistance at elevated temperatures
- Good ductility
- Excellent strength at elevated temperatures
- Good weldability through conventional welding techniques
317 Stainless Steel
317 stainless steel is an austenitic stainless steel that falls within the Cr-Ni alloy group. It contains chromium (18-20%), nickel (11-15%), and molybdenum (3-4%). Other components include: 0.08% C, 2% Mn, 1% Si, 0.045% P, 0.03% S, and 0.11% N. The different standardization models for 317 stainless steel are: 317 AISI, 1.4449 DIN, and 1.4449 EN.
Annealed 317 stainless steel is nonmagnetic due to the austenite structure. Here are a few other key properties:
- Good work hardening rate
- Moderate corrosion resistance
- Good ductility
- Moderate temperature resistance
- It hardens of cold worked, and thermal treatment does not work
- Weldable via conventional welding techniques
317 stainless steel is used in various industries, including: oil and gas, chemical, pulp and paper production, and food and beverage preparation.
317L Stainless Steel
Alloy 317L is similar to 317 and 317LMN, but contains less carbon than 317 and less molybdenum and nitrogen than 317LMN. Its typical composition includes: 0.03% C, 2% Mn, 1% Si, 17.5-19.5% Cr, 13-17% Ni, 0.045% P, 0.015% S, 0.11% N, and 3-4% Mo. The different standardization models for 317L stainless steel are: 317L AISI, X2CrNiMo18-15-4 DIN, and 1.4438 EN.
317L stainless steel is nonmagnetic due to its austenitic microstructure. Other properties are:
- Moderate work hardening rate
- Good corrosion resistance at elevated temperatures.
- Good ductility
- Good temperature resistance
- Hardened through cold working, and thermal treatment will not work
- Good weldability through conventional welding techniques
317L stainless steel is primarily used for: explosives, petroleum refining, condensers, and pulp and paper processing.
317LMN Stainless Steel
AISI 371LMN is a commercially important austenitic stainless steel that contains high levels of molybdenum (4-5%), and nitrogen (0.12-0.22%) for use in chloride containment devices. Also in the alloy is: 0.03% C, 2% Mn, 1% Si, 16.5-18.5% Cr, 12.5-14.5% Ni, 0.045% P, and 0.015% P. The different standardization models for 317LMN stainless steel are 317LMN AISI, X2CrNiMoN17-13-5 DIN, and 1.4439 EN.
317LMN stainless steel work hardens at a moderate rate. It is not hardenable through heat treatment. Other properties are:
- Excellent corrosion resistance at elevated temperatures
- Good ductility
- Moderate strength at elevated temperatures
- Good weldability through conventional welding techniques
317LMN stainless steel is primarily used for: pharmaceutical equipment, food and beverage processing, petrochemical processing, and air pollution control.
321 Stainless Steel
321 stainless steel is an austenitic metal that is stabilized by titanium (0.7%) and is nonmagnetic. Typical composition includes: 0.08% C, 2% Mn, 1% Si, 17-19% Cr, 9-12% Ni, 0.045% P, and 0.015% S. The different standardization models for 321 stainless steel are 321 AISI, X6CrNiTi18-10 DIN, and 1.4541 EN.
321 steel is work hardenable but is not hardenable through heat treatment. Its properties are:
- Good corrosion resistance at elevated temperatures
- Good ductility
- Good strength at elevated temperatures
- Good weldability through conventional welding techniques
321 stainless steel is primarily used for: aircraft piston engine manifolds, expansion joints, food processing and storage equipment, and polythionic acid service for petroleum processing.
347 Stainless Steel
347 stainless steel is an austenitic formulation that contains chromium (17-19%) and nickel (9-12%). Niobium (1%) is added to improve sensitization and to stabilize the carbon content (0.08%). The remainder of its constituents are: 2% Mn, 1% Si, 0.045% P, and 0.015% Si. The different standardization models for 347 stainless steel are 347 AISI, X6CrNiNb18-10 DIN, and 1.4550 EN.
347 is very similar to 18/10 stainless steel. It falls within the Cr-Ni alloy group of austenitic stainless steels and is nonmagnetic. Other properties are:
- Good work hardening rate
- Moderate corrosion resistance
- Good ductility
- Good temperature resistance
- Hardened through cold working, and thermal treatment will not work
- Good weldability through conventional welding techniques
347 stainless steel is primarily used for: chemical processing equipment, kitchen utensils, heat exchangers, and catalytic cracking units.
348 Stainless Steel
Alloy 348 is a tantalum- and niobium-stabilized austenitic alloy similar to 347/347H with the addition of cobalt (0.2%). Its typical composition includes: 0.08% C, 2% Mn, 1% Si, 17-19% Cr, 9-13% Ni, 0.045% P, 0.03% S, 0.8% Nb, and 0.1% Ta.
AISI 348 is part of the Cr-Ni austenitic stainless steel group and is nonmagnetic. Other properties include:
- Good work hardening rate
- Good corrosion resistance at elevated temperatures
- Good ductility
- Good temperature resistance
- Hardened through cold working, and thermal treatment will not work
- Moderate weldability through shielded gas welding techniques
348 stainless steel is primarily used for reactor linings and fuel cell linings in nuclear reactors.
330 Stainless Steel
AISI 330 is a high-nickel Cr-Ni stainless steel with extra silicon content (0.75-1.5%). The heavy nickel percentage (34-37%) improves chloride corrosion resistance. The rest of its composition is typically: 0.08% C, 2% Mn, 17-20% Cr, 0.03% P, and 0.03% S. The different standardization models for 330 stainless steel are 330 AISI, X12NiCrSi35-16 DIN, 1.4864 EN.
330 stainless steel is not magnetic thanks to the austenite structure. Some of its properties are:
- High work hardening rate
- Excellent corrosion resistance
- Good ductility
- Good temperature resistance
- Good weldability through conventional welding techniques
330 stainless steel is primarily used for: petrochemical processing (cracked ammonia components, furnace components), power generation (boiler fixtures, turbine components), thermal treatment plants (salt pots, fan components, heat exchangers), and chemical processing (waste remediation unit components).
384 Stainless Steel
384 stainless steel is part of the Cr-Ni austenitic stainless steel group. With its high nickel content (17-19%), the alloy exhibits strong chloride corrosion resistance. A typical composition also includes: 0.08% C, 2% Mn, 1% Si, 15-17% Cr, 0.045% P, and 0.03% S. The different standardization models for 384 stainless steel are 384 AISI, X6NiCr18-16 DIN, and 1.4389 EN.
384 steel’s properties are:
- Low work hardening rate
- Good corrosion resistance
- Good ductility
- Good temperature resistance
- Hardened through cold working, and thermal treatment will not work
- Moderate weldability through shielded gas welding techniques
384 stainless steel is primarily used for fasteners and steam turbine blades in power generators.
409 Stainless Steel
409 stainless steel is a general-purpose ferritic formulation that contains chromium (10.5-12.5%) and is stabilized by titanium (0.65%). Its typical composition also includes: 0.03% C, 1% Mn, 1% Si, 0.04% P, and 0.015% S. The different standardization models for 409 stainless steel are: 409 AISI, X2CrTi12 DIN, and 1.4512 EN.
Its properties include:
- Magnetic due to the ferritic stainless steel structure
- Does not work harden and is not hardenable through heat treatment
- Excellent corrosion resistance at elevated temperatures
- Good ductility
- Moderate strength at elevated temperatures
- Moderate weldability through conventional welding techniques
409 stainless steel is primarily used for: automotive exhaust systems, heat exchanger tubing, agricultural equipment, and fuel filters.
410 Stainless Steel
410 stainless steel is a general-purpose martensitic steel that contains chromium (11.5-13.5%) as the main alloying element. It typically also contains: 0.08-0.15% C. 1.5% Mn, 1% Si, 0.75% Ni, 0.04% P, and 0.015% S. The different standardization models for 410 stainless steel are: 410 AISI, X12Cr13 DIN, and 1.4006 EN.
It is magnetic due to the martensite structure. Other important properties are:
- Does not work harden but can be hardened by heat treatment
- Moderate corrosion resistance at moderate temperatures
- Moderate ductility at low temperatures
- Good strength at low temperatures
- Poor weldability through conventional welding techniques
410 stainless steel is primarily used for: petroleum refinery plants, scissors, springs, and Belleville washers.
420 Stainless Steel
420 stainless steel is a slight alteration of 410 for increased functionality and resistance. The increased carbon content (0.15-0.42%) of 420 steel imparts durability. Its typical composition also contains: 1-1.5% Mn, 1% Si, 12-14% Cr, 0.04% P, and 0.015% S. The different standardization models for 420 stainless steel are shown in Table 2 below:
AISI | DIN | EN |
---|---|---|
AISI 420 | DIN X20Cr13 | EN 1.4021 |
AISI 420 | DIN X30Cr13 | EN 1.4028 |
AISI 420 | DIN X39Cr13 | EN 1.4031 |
The martensite structure makes 420 magnetic. Other properties include:
- Cannot be work hardened but can be hardened through heat treatment
- Moderate corrosion resistance at moderate temperatures
- Moderate ductility
- Good strength at low temperatures
- Poor weldability through conventional welding techniques
420 stainless steel is primarily used for: needle valves, knives, hand tools, and wear plates.
430 Stainless Steel
AISI 430 is a commercially important ferritic stainless steel with moderate performance properties that comes at a relatively low cost. 430 stainless steel contains high levels of chromium (16-18%) to impart corrosion resistance. Its typical composition also includes: 0.08% C, 1% Mn, 1% Si, 0.04% P, and 0.015% S. The different standardization models for 430 stainless steel are 430 AISI, X6Cr17 DIN, and 1.4016 EN.
It is magnetic due to the ferritic stainless steel structure. 430 steel’s properties include:
- Work hardens at a low rate
- Not hardenable through heat treatment
- Moderate corrosion resistance at elevated temperatures
- Good ductility
- Moderate strength at elevated temperatures
- Moderate weldability through conventional welding techniques
430 stainless steel is primarily used for: lashing wires, chimney liners, gas nozzles, and dishwashers.
434 Stainless Steel
434 stainless steel is a commercially important ferritic stainless steel that strikes a balance between value and performance. It contains high levels of chromium (16-18%) and is stabilized with molybdenum (0.9-1.4%). The remainder of its typical composition includes: 0.08% C, 1% Mn, 1% Si, 0.04% P, and 0.015% S. The different standardization models for 434 stainless steel are 434 AISI, X6CrMo17-1 DIN, and 1.4113 EN.
434 steel is magnetic due to the ferritic structure. AISI 434’s properties include:
- Low work hardening rate
- Cannot be hardened through heat treatment
- Good corrosion resistance at elevated temperatures
- Moderate ductility
- Good strength at elevated temperatures
- Moderate weldability through conventional welding techniques
434 stainless steel is primarily used for: furnace combustion chambers, automotive trim, exhaust systems, and medical equipment.
440C Stainless Steel
440C stainless steel is a high-carbon martensitic type that contains chromium (16-18%) as the main alloying element. Typical composition also includes: 0.95-1.2% C, 1% Mn,1% Si, 0.04% P, 0.03% S, and 0.4-0.8% Mo. The different standardization models for 440C stainless steel are 440C AISI, X105CrMo17 DIN, 1.4125 EN.
It cannot be work hardened but can be hardened through heat treatment. The martensitic microstructure also makes it magnetic. Other properties include:
- Poor corrosion resistance at moderate temperatures
- Poor ductility
- Excellent strength at low temperatures
- Poor weldability through conventional welding techniques
440C stainless steel is primarily used for: knives, roller element bearings, valve seats, and chisels.
904L Stainless Steel
904L stainless steel is a highly alloyed, non-stabilized austenitic metal. The copper (1.2-2%) adds good resistance to reducing acids. The increased nickel (24-26%) improves chloride corrosion resistance. Its typical composition includes: 0.02% C, 2% Mn, 0.7% Si, 0.03% P, 0.01% S, 19-21% Cr, 4-5% Mo, 0.15% N, and 1.2-2% Cu.
AISI 904L is part of the Cr-Ni austenitic stainless steel group and is not magnetic. Some of its properties include:
- High work hardening rate
- Good corrosion resistance
- Good ductility
- Good temperature resistance
- Good weldability through conventional welding techniques
904L stainless steel is primarily used for: seawater and brackish water equipment (condensers, heat exchangers, and piping), chemical processing plants (acid production), coal power plants (flue-gas desulfurization systems), and pulp and paper bleaching equipment.
18/10 Stainless Steel
18/10 stainless steel is an austenitic steel that contains chromium (17-19%) and nickel (9-12%). Niobium (1%) is added to improve sensitization and to stabilize the carbon content (0.08%) as well. It also contains: 1% Mn, 1% Si, 0.045% P, and 0.015% S. 18/10 is very similar to AISI 347 stainless steel. The different standardization models for 18/10 stainless steel are: 18/10 AISI, X5CrNiNb18-10 DIN, and 1.4546 EN.
18/10 steel falls within the Cr-Ni alloy group of austenitic stainless steels and is nonmagnetic when annealed. 18/10 steel’s properties are:
- Good work hardening rate
- Moderate corrosion resistance
- Good ductility
- Good temperature resistance
- Hardened through cold working, and thermal treatment will not work
- Good weldability through conventional welding techniques
18/10 stainless steel is primarily used for: cookware, bakeware, kitchen utensils, fasteners, and brewery equipment.
What Are the Different Standards for Stainless Steel Grades?
The different standards for stainless steel grades are as follows:
- Austenitic Stainless Steel - Group A
- Duplex Stainless Steel - Group AF
- Ferritic Stainless Steel - Group F
- Martensitic Stainless Steel - Group C
The naming conventions for stainless steel in different standards are as follows:
- The European Standard (EN) for stainless steels is governed by EN10088. Stainless steels are identified numerically by 1.4. That number is then followed by three digits that indicate the composition. For example, AISI 304 will be 1.4301 for EN.
- The Japanese International Standard (JIS) adopts the AISI as the standard for stainless steels, yet adds the SUS prefix. For example, SUS304 is equivalent to AISI304.
- The British Standard (BS) for stainless steel is governed by BS 970. BS has adopted the AISI standard for stainless steel as well, with its own postfix added.
- Codes used in the Chinese National Standard (GB) depend heavily on which industry and material stock type the stainless steel comes from.
- The German Standard (DIN) for steel is governed by DIN17006. High alloy steels start with X, followed by the alloying elements, then the numerical content of any alloying element that makes up more than 5% of the content. For example, AISI 301 is DIN X12CrNi17-7.
- The International Organization for Standardization (ISO) for stainless steel is governed by ISO15510. ISO has adopted the DIN standard for stainless steel.
Summary
This article presented different types of stainless steel and grades, explained each of them, and discussed each of their advantages. To learn more about stainless steel, contact a Xometry representative.
Xometry provides a wide range of manufacturing capabilities and other value-added services for all of your prototyping and production needs. Visit our website to learn more or to request a free, no-obligation quote.
Disclaimer
The content appearing on this webpage is for informational purposes only. Xometry makes no representation or warranty of any kind, be it expressed or implied, as to the accuracy, completeness, or validity of the information. Any performance parameters, geometric tolerances, specific design features, quality and types of materials, or processes should not be inferred to represent what will be delivered by third-party suppliers or manufacturers through Xometry’s network. Buyers seeking quotes for parts are responsible for defining the specific requirements for those parts. Please refer to our terms and conditions for more information.
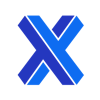