Laser Cladding Services by Xometry
Xometry offers the highest quality laser cladding services and can assist in the production of parts with intricate and complex geometries and excellent surface finishes.
Laser cladding is a high-precision process that involves melting a layer of metal powder onto a substrate, creating a strong and durable bond. This technique is crucial in the manufacturing industry because it enhances the properties of metal components. It can improve surface finish, wear resistance, corrosion resistance, and overall durability, extending the life span of critical parts and reducing maintenance costs. Furthermore, laser cladding enables the restoration of worn or damaged components, saving both time and resources by avoiding the need for costly replacements.
With Xometry's extensive network of manufacturing partners and our vast industry experience, you can be confident that our laser-clad components consistently meet the highest standards. Our precision laser cladding services are your gateway to achieving top-tier surface enhancement and additive manufacturing solutions.
Laser Cladding Process
In laser cladding, the laser generates a molten pool on the workpiece's surface, into which the chosen feedstock—either wire or powder—is simultaneously introduced. Despite the immense power of the laser as a heat source, the exposure time is brief, resulting in rapid solidification and cooling. This rapid solidification contributes to the creation of a tough, high-quality metallurgical bond, surpassing the capabilities of thermal spray methods and avoiding the health hazards associated with hard chromium plating.
Conventional laser options for surface protection applications include CW CO2 and Nd:YAG lasers. However, High-Power Diode Lasers (HPDLs) have gained popularity, particularly in industrial settings. This is due to their cost-effectiveness, high energy efficiency, and compact size.
In contrast to thermal spray alternatives, the laser cladding process offers precision and control over material deposition. Laser cladding utilizes laser energy to create metallurgical bonds at lower temperatures, ensuring minimal porosity and corrosion resistance. It excels at thicker build-up (typically from 50 µm–2 mm) in a single pass with a fusion bond and high precision. In contrast, thermal spray offers a wide variety of materials, thin coatings, and versatility but requires more steps and operates at higher temperatures. To choose between them, it's crucial to focus on specific application requirements: laser cladding for a metallurgical bond and lower temperature needs; thermal spray for thin coatings, and a broader array of material options.
Materials Suitable for Laser Cladding
Laser cladding materials play a critical role in the process, determining the performance and characteristics of the clad surface. The following materials are suitable for laser cladding:
- Metal Alloys
- Wear-Resistant Coatings
- Corrosion-Resistant Coatings
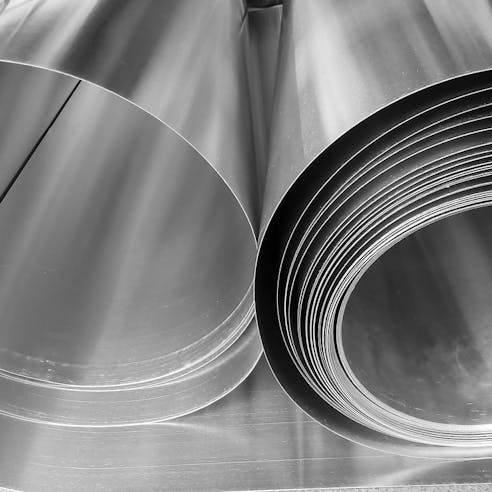
Metal Alloys
Metal alloys are commonly used for laser cladding due to their adaptability and wide-ranging applications. Among the popular choices for laser cladding are: stainless steel, nickel-based alloys, titanium alloys, cobalt-chromium alloys, and aluminum alloys. These materials are carefully selected based on the specific requirements of the cladding task. For example, stainless steel alloys, consisting of iron, chromium, and nickel, are widely used in laser cladding. They offer excellent corrosion resistance and are often applied for anti-corrosion solutions in components exposed to harsh environments. Laser cladding with nickel-based alloys is chosen for their corrosion resistance and high-temperature properties. These alloys find applications in aerospace and industrial equipment subjected to extreme conditions.
Alloy selection plays a critical role in achieving the desired characteristics in laser cladding. By tailoring the alloy composition, the cladding can enhance wear resistance, heat resistance, and corrosion resistance.
Wear-Resistant Coatings
Laser cladding is a go-to process for creating wear-resistant coatings. It plays a crucial role in protecting components subjected to abrasive forces, ensuring longevity and performance. Tungsten carbide, a hard and wear-resistant material, is often incorporated into metal matrix composites. The dispersion of tungsten carbide in a metal matrix provides exceptional wear resistance, making it ideal for coating applications that require superior wear protection. This application, known as hardfacing, is particularly useful in industries like: mining, agriculture, and construction, in which components endure significant wear and tear.
Corrosion-Resistant Coatings
Corrosion-resistant coatings produced through laser cladding are vital for safeguarding components in environments prone to chemical exposure and rust. Stainless steel and nickel-based alloys are frequently used for creating corrosion-resistant coatings. These coatings act as a barrier between the component's surface and corrosive agents, ensuring the longevity and integrity of the part. The ability of laser cladding to provide anti-corrosion solutions is crucial in industries like: chemical processing, marine, and offshore engineering.
Advantages of Laser Cladding
Laser cladding offers a multitude of advantages. These benefits include:
Surface Enhancement
Laser cladding significantly enhances the properties of a component's surface, resulting in improved wear resistance, corrosion resistance, and overall durability. This process can transform the surface of an existing component, extending its life span and ensuring it can withstand harsh environmental conditions. By reinforcing the surface, laser cladding contributes to enhanced material performance, allowing components to endure the rigors of demanding applications.
Precision Coating
Precision is one of the main advantages of laser cladding, allowing for the controlled deposition of materials to meet exacting specifications. Whether it's adding a wear-resistant layer to a critical part or creating intricate geometric designs, laser cladding ensures that the coating adheres precisely as required. This level of precision is invaluable in industries that demand accuracy, as it reduces the need for extensive post-processing or additional machining.
Material Efficiency
Laser cladding minimizes waste by depositing material only where needed, thus reducing the consumption of costly resources. This efficiency is particularly advantageous for both cost-effective processes and environmental sustainability. By focusing material application with pinpoint accuracy, laser cladding optimizes the use of resources, ultimately leading to a more economical and eco-friendly approach to manufacturing.
Reduced Waste
Traditional manufacturing methods often generate substantial waste due to material removal or imprecise deposition. In contrast, laser cladding minimizes waste by directly applying material to the target area, eliminating the need for extensive machining or removal processes. This reduction in waste not only reduces environmental impact but also contributes to overall sustainability, making laser cladding a responsible choice for modern manufacturing practices.
Disadvantages of Laser Cladding
While laser cladding offers numerous advantages, it's important to consider its limitations and disadvantages, which include:
High Equipment Cost
One of the primary disadvantages of laser cladding is the high cost associated with the equipment. The initial investment in laser cladding machinery and infrastructure can be substantial, which can pose financial challenges for smaller businesses or those with budget constraints. These high equipment costs may necessitate careful financial planning and assessment of the return on investment.
Skilled Labor
Laser cladding is a complex and precision-driven process that requires a skilled workforce with expertise in operating the equipment and managing the intricacies of the process. Hiring and retaining such skilled labor can be challenging, as well as costly. Additionally, specialized training is often required to ensure that personnel can handle the technology effectively. This reliance on skilled labor can be a potential disadvantage for companies seeking to adopt laser cladding.
Material Compatibility
Material compatibility is a key challenge in laser cladding. Not all materials are suitable for this process, and the selection of the right material is critical to achieving the desired results. Material compatibility issues can limit the range of applications for laser cladding, making it essential for manufacturers to carefully consider material selection.
Limited Layer Thickness
Laser cladding, with its ability to lay down thick layers in one pass, can face challenges when thin coatings are needed. The high build rate can result in difficulties achieving thin layers and it may also increase the risk of cracking in certain cases. So, while laser cladding offers advantages in building up thick layers, it may not be the ideal choice for applications requiring very thin coatings.
In need of custom laser cladding services?
Applications of Laser Cladding
Laser cladding is a versatile technology with a broad range of applications across various industries. Key applications include:
- Aerospace Industry
- Automotive Industry
- Oil & Gas Sector
- Tool and Die Manufacturing
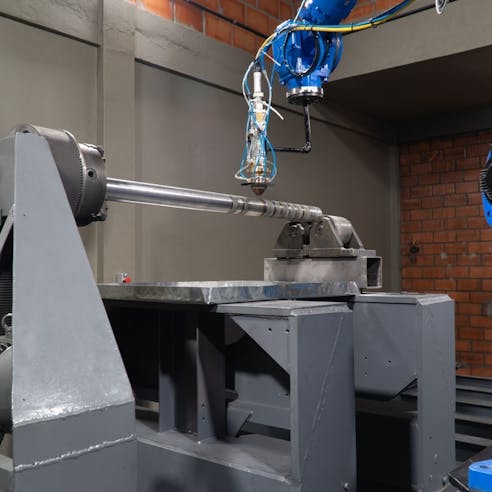
Aerospace Industry
Laser cladding is extensively utilized in the aerospace sector for its precision and ability to enhance components. It plays a crucial role in the manufacturing and maintenance of turbine components, in which it is employed to add wear-resistant coatings, extending the life span of these critical parts. Furthermore, laser cladding is instrumental in aircraft maintenance, rejuvenating, and repairing damaged components to ensure optimal performance and safety.
Automotive Industry
The automotive industry benefits from laser cladding in multiple areas. Engine components, such as cylinder bores, are treated with laser cladding to improve wear resistance and reduce friction, ultimately enhancing engine performance and longevity. Laser cladding is also a valuable tool in automotive repair, in which it is used to restore worn or damaged parts to their original specifications. Surface modification of automotive components is another application, contributing to increased durability and efficiency.
Oil & Gas Sector
In the oil & gas sector, laser cladding is used to enhance various components. Drill bits, for instance, are coated with wear-resistant materials through laser cladding, improving their durability and extending their operational life. Valves and downhole equipment benefit from laser cladding as well, providing corrosion protection and enhancing performance in challenging, corrosive environments.
Tool and Die Manufacturing
Tool and die manufacturing leverages laser cladding for a multitude of applications. Laser cladding is frequently employed in die repair, extending the life of critical components. It is also used to enhance mold surfaces, creating smoother and more durable surfaces that lead to higher-quality products. Tool restoration and precision manufacturing are additional areas in which laser cladding's precision and material-enhancing capabilities are invaluable.
Alternatives to Laser Cladding
When considering surface treatments and cladding methods, it's important to be aware of alternative techniques that can address specific application needs. Listed below are some alternatives to laser cladding:
Thermal Spray Coating
Thermal spray coating presents an alternative to laser cladding. In this method, a material in the form of a wire, powder, or rod is melted and sprayed onto a surface using a high-velocity gas or flame. This technique excels when versatility and cost-efficiency are key and thinner coatings are required. The advantages of thermal spray coatings include their adaptability to a wide array of substrates, the capability to achieve thinner coatings with ease, cost-effectiveness for large-area applications, and the availability of various materials, from metals to ceramics and polymers. On the flip side, thermal spray coatings may lack the precision offered by laser cladding and are primarily suited for surface treatments. They are often favored in scenarios in which cost-effectiveness, versatility, and thinner coatings are essential.
Chemical Vapor Deposition (CVD)
Chemical Vapor Deposition (CVD) emerges as another noteworthy alternative for surface treatments. In CVD, thin layers of material are deposited onto a substrate through controlled chemical reactions. This method shines in situations that demand atomic-level precision and highly uniform coatings, making it ideal for complex shapes and applications requiring high-purity coatings. The advantages of CVD include: its atomic-level precision, uniform and conformal coatings, and suitability for various materials. Nevertheless, CVD can be equipment-intensive, involving high temperatures and slower processes, which may pose limitations. CVD is often chosen for applications in which precise and uniform coatings are imperative, such as in semiconductor manufacturing and the aerospace industry.
Plasma Transferred Arc (PTA) Welding
Plasma Transferred Arc (PTA) welding, an alternative for cladding and hard facing, uses a plasma arc to melt a filler material that is then deposited onto the substrate. PTA welding excels when high deposition rates, versatile material options, and minimal heat-affected zones are required, making it suitable for industries like: oil & gas, mining, and manufacturing. Challenges may include complex system setups and slightly less precision compared to laser cladding. PTA welding is often chosen for applications that necessitate the efficient build-up of wear-resistant coatings and hard facing, where precision may be somewhat less critical than deposition rate and durability.
Why Choose Xometry for Laser Cladding Services?
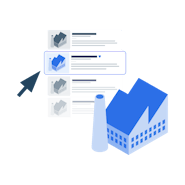
Endless Options
Choose from millions of possible combinations of materials, finishes, tolerances, markings, and certifications for your order.
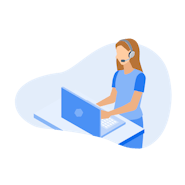
Easy to Use
Get started with our easy-to-use platform and let our experts take care of managing the project from locating the right manufacturing partner to delivery logistics.
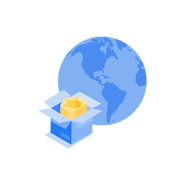
Vetted Network
We are ISO 9001:2015, ISO 13485, and AS9100D certified. Only the top shops that apply to become Suppliers make it through our qualification process.