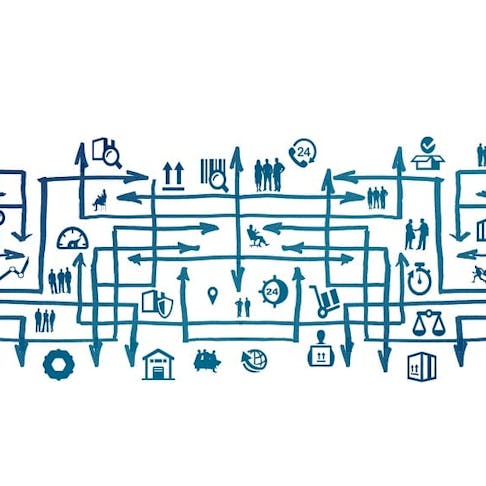
The Basics of Production Planning
Production planning is the process of detailing the strategies needed to deliver the company’s products and services. Learn more about it here.
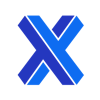
Production planning is the process of developing an overall plan that details the exact strategies needed to deliver the company's products and services to a waiting market. Formerly, production planning was a manual-and-document tool used by larger enterprises, with complex market engagements and a high volume/range of outputs. Today, production planning is increasingly an easy, software-supported process that is highly accessible to SMEs and eases their path to deliverable outcomes.
Production planning encompasses all aspects of manufactured product outputs, from pies to cell phones, from ships to broccoli. Through systematic and evidence-based demand forecasting, a well-operated plan will help in quantity and supply chain management for materials, staffing, production plant, and detailed stages in the making process.
Types of Production Planning
There are essentially five modes of production:
1. Job-Based Planning
Job or project-based production is a style that gets a single product built by one person or a small group. This could be a craftsperson making a piece of jewelry, it could be a cell team in a car factory building the whole vehicle, or it could be a house construction. Smaller scale tasks, with limited complexity and a single builder/assembler, can be planned relatively easily. Larger and more complex tasks will likely have many more inputs and complexities, making a detailed plan much more applicable and useful.
2. Batch-Based Planning
The term batch production describes products assembled in groups of like or related products. Bread is usually produced in batches, where each step is performed on the whole batch as a group. The tasks in this production method are either collective (making dough) or batched.
Batch production planning can raise challenges in planning resource use, without over- or under-use of resources. Production bottlenecks arise at the slowest process point, where duplication can be beneficial and a production plan should highlight this.
3. Flow Method
Flow manufacturing is characterized by a continuous flow of products along a production line. Materials are supplied at appropriate stations along the line. Each station is a clearly defined step in the assembly and the product moves along the line, often conveyorized. Cars, whiteware, and consumer electronics are often made in this style of process.
This method minimizes work-in-process and finished goods held in inventory, reduces costs, and can help reduce manufacturing lead times. Balancing the flow is often a difficult task, but well-planned and managed JIT (just-in-time) materials delivery to the workstations results in a clear, efficient production method.
4. Mass Production Method
Mass production is essentially flow production but for regular and large numbers of the same items, made at a fast pace. It is commonly automated, so labor costs for complex products approach zero. Such operations are scheduled based on the demand, the resources, and the overall build time from start to finish.
5. Process Manufacturing Method
This type of production typically involves the manufacture of a product that is fluid, small particle, or gas-based—“things” that cannot be counted. A chemical plant producing detergents or a polymers plant making plastic granules would be applying process manufacture planning. The process method is costly to establish and offers no room for error. Materials, services, and maintenance planning must be first-class to avoid disruptions.
Production Scheduling
Production scheduling is a detail-loaded process—particularly for complex products, for which very complex interdependencies and layered risks arise in more intricate and multi-product environments. The production schedule defines the dates and times when the production plan gets executed as a work process. It delineates the staffing levels, equipment, material resources, and services that must be provisioned.
Production scheduling software takes the burden of the detail off you, so a schedule can be written in such a way that when an input or output must be rescheduled, the planning software can self-adjust and present options that allow you flexibility.
Demand Forecasting
Demand forecasting involves estimating the amount of a product or service that customers will need in the future. This information is used to develop a production plan that will meet customer demand while avoiding overproduction or underproduction. In many cases, seasonal and annual fluctuations in demand can establish a pattern that allows some degree of accuracy in forecasts. In many companies, the demand rises or falls (or both) in response to less predictable stimuli, making forecasts little more than guesswork.
Capacity Planning
Capacity planning involves determining the amount of resources, such as labor, materials, and equipment, that will be needed to meet the demand forecast. Capacity planning also involves identifying any bottlenecks or constraints in the production process that may limit the amount of output that can be produced. There are three types of capacity planning:
1. Lead Capacity Planning
Lead capacity strategy or lead capacity planning involves increasing production output in expectation of a rise in demand. A farmer may need to hire seasonal workers for the harvest. A Christmas-goods manufacturer is likely to ramp production volumes around mid-year. Predictable fluctuations enable strategic ramp-up and ramp-down in production capacity.
2. Lag Strategy Planning
A lag strategy increases capacity in response to increased demand, rather than ahead of it. This is more secure but can mean lead time blowouts as the capacity increase isn’t timely. Lag strategy planning is commonly used in the restaurant sector, medical care, and other areas in which on-call staff or resources are available or subcontract suppliers are idle and waiting.
3. Match Strategy Planning
Match strategy planning carefully merges lead and lag planning to slowly increase capacity in small increments, so production reaches the desired levels. This reduces the risk of lead time blowout and also the risk of sudden overcapacity. This type of approach is often used in a slow ramp-up as a product hits the market. Initial demand can fluctuate, so resources are increased carefully as peak demand is not predictable and cannot be resourced in a lead-strategy way.
Scheduling
This involves developing a detailed schedule for the production process, including the timing of each activity and the allocation of resources. The schedule should take into account any constraints identified during capacity planning. In larger organizations, scheduling can be a challenging and complex task, balancing a range of product types, processes, and materials supplies. In other cases, it is relatively easy to schedule work. When there is a queue, the process is moderately predictable and the lead time is not considered a challenge by the market.
Inventory Management
A company's inventory is usually among the most valuable assets on its books. Work in progress can often be the most significant line item of a company’s P&L (profit and loss statement). Inventory is also often treated in accounting as a liability. Heavy inventory represents risk through changes in demand, damage, or simply time, and so must be insured. Offloading of surplus inventory can turn some back into cash, but then the “asset” becomes a concrete liability and loss.
This makes inventory management a critical task for any business. Optimizing stock, controlling low-availability commodities, stock’s end of life, and issues like “last buy” all require close management to protect profitability. Stock control can be an intensive manual task set, including the reordering of points and quantities controlled in simple spreadsheets. It more often involves enterprise requirements planning (ERP) software, such as SiteLine and SAP.
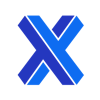