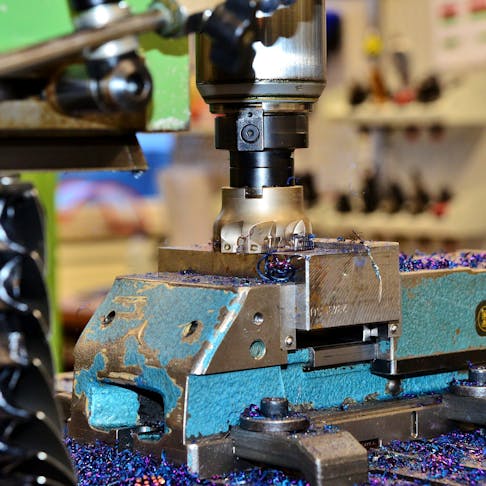
Keeping a Tool Probe and Other Tools Clean
Maintain high precision by keeping your tools clean. Read on for tips on ensuring your tools are in top shape!
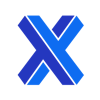
Machine shops have always been where precision work gets done. This fact dates back at least two millennia, as evidenced by the Antikythera mechanism. No precision workshop worth the name is ever a dirty or disorderly place. Since the 1960s a quiet revolution has transformed precision machine shops into high-tech laboratories, and the levels of housekeeping this requires have increased exponentially.
Machine shops are more capable now than they used to be. Highly precise measurement systems have enhanced machinists’ ability to deliver high precision. These are delicate instruments, though, and they must be carefully maintained to remain functional and accurate. A probe such as a coordinate measuring machine (CMM) stylus will give false readings if there is debris on either the stylus tip or the object being measured. These CNC measuring devices are great for process setup and validation, but they are also vulnerable.
Cleaning Tips for Shop Tools
The CNC machinist must keep all parts of their workspace tidy both for safety purposes and to keep things operating reliably. Some cleaning tips for shop tools are listed below:
- Daily cleanup is a must. Every machine and the entire surrounding workspace needs a thorough cleaning; all swarf, cutting debris, and coolants must be removed. Particular attention must be paid to the slideways and wipers, position sensors, clamping parts, and T-slots. Also, note that optical and inductive position sensors are the most sensitive devices, so be careful when cleaning them. Swarf residue and penetration can cause wear and disrupt their functionality.
- By keeping cutters and tool changers clean, you prevent handling and accuracy problems. Cutters must be free of debris so they and other tools fit properly in the tool rack. The tool change process is very position-sensitive and few machines can sense when a tool is out of place due to detritus. While tolerances are built into the tool pickup and return operations, too much debris can still cause failures.
- Onboard CMM instruments are perhaps the most sensitive to debris both on the part and on the probe. If precision tests of +/-0.05mm are to be performed regularly, a piece of cutting waste can generate enormous errors. Even fine particles can generate serious mismeasurements.
- Aside from the interior of the machine, the whole work area and all equipment must be kept in good order. While some areas are more critical than others, debris or misplaced items anywhere in a machine shop create potential hazards and eat up man-hours. Maintenance routines like 5S can enhance the workspace and productivity. Although ‘best practice’ doesn’t necessarily require more than good habits and attention to detail. A prime benefit of good cleaning habits — for space, machines, and tools — is that it helps you identify maintenance issues before they cause problems.
Cleaning Tips for Built-In CMM Setups
CMM setups that are built into the machine deserve special attention. Most important is to keep the probe clean and ready for use. For example, the Renishaw OTS 3D tool probe is a tool-setting probe. It is regularly used to validate tool diameters to confirm offsets but also evaluates reference materials and billets to speed setup. When not in use, the device can be exposed to cutting fluids and swarf, meaning it won’t be ready for subsequent measurements. One solution is to have a quick-release mounting on the machine bed, so the device can be precisely and quickly placed and removed. But that discourages the use of the device and disrupts the machining process. Good CNC operators try to avoid work disruptions like that.
Near identical issues apply to attached 3D laser scanners, features that are becoming increasingly popular. Optical systems are easier to disrupt than mechanical ones, so similar precautions are critical for all of them.
The common solution is a simple protective cover. Keep the following in mind:
- The cover should be custom-made for the particular machine setup and afford a level of protection that guarantees readiness whenever the instrument is needed.
- The machine should easily be able to open the cover as needed via a G-Code or (preferably) M-Code command in the machining cycle.
- Ideally, the cover should be opened by a pneumatically driven mechanism switched from a spare relay.
- An alternate opening method can be a simple tool nudge from the G-Code subroutine that allows the machine to lift and replace the cover. The code must be added to the machining sequence.
Keeping Tools Clean for Precision
The importance of tool cleanliness cannot be overstated. As CNC and evaluation equipment becomes increasingly capable and achieves ever greater levels of precision and productivity, the cleanliness issue will take on ever greater importance. Plan for the mess and learn how to clean your instruments when they accumulate any contamination. This understanding will ultimately improve your machining skills.
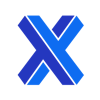