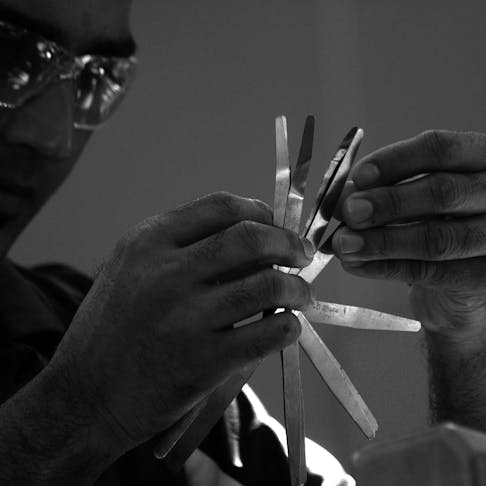
What Is Condition Monitoring?
Condition monitoring is the measurement of equipment parameters to identify signs of impending failure. Learn more about it here.
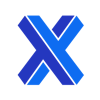
Powerful concepts like proactive and predictive maintenance were, until recently, more of a "nice to have" than a "need to have" for the majority of plant managers. It is now simpler than ever to implement this crucial strategy to safeguard plant investments, thanks to recent developments in the maintenance solutions sector.
Condition monitoring (CM), a preventive maintenance approach, forecasts machine health by fusing machine sensor data which can detect vibration and other system characteristics (in real-time) with state-of-the-art machine monitoring software. This method delivers a comprehensive, plant-wide view of mechanical processes and allows plant maintenance specialists to remotely check the health of any individual piece of machinery. Every time a change in machine health is detected, condition monitoring software sends an alert, allowing maintenance professionals to examine the problem right away and decide whether corrective action is necessary.
In this article, we’ll take a look at what condition monitoring is, how it works, and what types of techniques are associated with it. We’ll also take a look at its benefits and challenges it presents, to help you decide how condition monitoring can propel your manufacturing operation into the future.
So What Is Condition Monitoring?
Condition monitoring (CM) involves the continuous measurement or monitoring of key equipment parameters. For example, temperature and vibration at critical locations are used to identify signs of change that could indicate a potential fault or impending failure within the system. CM is a crucial part of preventive maintenance. Unplanned downtime can be avoided by identifying growing inefficiencies and symptoms of process problems by gathering and analyzing specific machine signal data.
When monitoring mechanical assets, a variety of signals can be taken into consideration. Traditional methods were mostly centered on vibration analysis, but more recent, creative methods emphasize ESA (electrical signature analysis).
Two popular techniques are used for condition monitoring:
- Trend Monitoring: Monitoring of trends is the regular, ongoing measurement and analysis of the equipment data. It entails selecting appropriate and quantifiable indicators of a component or machine deterioration and examining the trend in those indicators to determine when deterioration exceeds a critical limit. Trend monitoring is employed, for instance, in the routine observation of airplane engine data to identify and diagnose performance problems, and ideally, avoid more expensive — or even catastrophic — damage.
- Condition Checking: This method entails periodically checking the status of selected machine parameters to assess the current condition of a machine. Data from discrete points in time are used to determine the state of the machine in this method. Using an oil sight glass to manually monitor and periodically record the state of a machine's lubricant is an example of condition checking.
These two techniques of condition monitoring give you a close-up view of how your machines are performing. Over time, CM provides a historical picture of machine health.
How Does Condition Monitoring Work?
Conditioning monitoring depends on sensors to gather data for analysis. Relevant quantifiable factors like acoustic output, vibration frequency, amplitude, position, or oil level provide the foundation for this. This measurement data is subsequently analyzed by specialized software, which records its findings in the condition monitoring report.
The machine's condition is estimated using all of the sensor system's measured values To obtain accurate results, the sensors must be attached or integrated into the components they are measuring. It is decided in advance which elements are important for the evaluation and how they should be weighted. This means that a wide range of industries and businesses can use condition monitoring services.
However, in applied condition monitoring, actual values are crucial. This entails comparing the actual and reference values under the given conditions. After all, it is only when the normal situation is sufficiently known that deviations can be discovered. If so, the data that has been recorded can be used to make diagnoses and judgments. Condition monitoring makes it possible for many types of manufacturing operations to perform predictive maintenance in this way. Condition monitoring generally consists of the following three stages:
1. Set Up the Systems
Installing the sensors for the monitoring system onto your equipment is the first step in the condition monitoring process. Your current machines and equipment may need to be modified or retrofitted in order to accomplish this.
2. Measure Your Baseline Data
Once the monitoring system is set up, you can start evaluating how well your equipment is working. The information gathered may consist of vibration, temperature, rotor speed, and data from process sensors. Having done this, you will have a baseline to compare your equipment's current operating circumstances to in the future.
3. Implement Continuous Monitoring
With the help of your sensors and condition monitoring software, your CM setup is now ready to keep an eye on your systems, evaluate performance, and deliver diagnoses. When an operational irregularity is discovered, the system can also warn the user and analyze the data to decide whether immediate action is necessary or whether the machine can continue to function for a little longer while maintenance is planned.
Types of Condition Monitoring
There are numerous types and methods for machine condition monitoring, each with a specific method of data collection. These are the most common types:
1. Offline Condition Monitoring
This type of monitoring, which is sometimes also referred to as manual monitoring, is typically utilized for non-critical machines, where routine scanning is sufficient to monitor the state of the machine. Offline monitoring is appropriate when the time it takes for a process variable to change is relatively long, or when the parameter to be measured must be measured at a separate location, such as analysis of lubrication oil for contaminants. For basic results with the offline analysis of oil, several businesses analyze the viscosity and water content of certain oils locally using sampling kits. Wear metals, nitration, oxidation, and additive depletion can all be tested in-house by using semi-automated testing equipment.
2. Online Condition Monitoring
The online method variation uses sensors that are permanently installed in or on the machine, allowing for automatic, routine measurements to be taken without sending an engineer to check the machine out.
Online condition monitoring provides warnings in real time for things like: acoustic emissions, vibration analysis, ultrasound thermography, and infrared thermography. It involves the continuous evaluation of a machine by wirelessly linking machine-mounted sensors to integrated software. Numerous sensors and monitoring devices enable highly individualized online condition monitoring. When selecting an online monitoring system, factors including machine type, speed, and parts should be taken into account. You can also configure real-time warnings for distant devices.
3. Route-Based Condition Monitoring
Using a handheld instrument, such as an infrared imaging camera, a technician records data sporadically on the status of a route. This technique is frequently used to establish a trend pattern and decide whether a more in-depth investigation is required.
Different Condition Monitoring Techniques
Many different types of data can be gathered for condition monitoring. Here is a quick overview of some of the popular techniques:
- Vibration Monitoring: Vibration monitoring is a useful tool for detecting potential mechanical or maintenance problems with any rotating part. The slightest variations in vibration levels can be picked up by sensors and used to analyze and expose problems including incorrect calibration and damage to the rotating part.
- Electrical Monitoring: To identify flaws or defects, electrical monitoring makes use of electrical parameters such as: open circuit, short circuit, high voltage, and low voltage. To identify potential problems, these metrics include capacitance, induction, frequency response, pulse response, and resistance. To ascertain whether intervention is necessary to stop system failure, this method measures degradation patterns and looks for violations of absolute or relative thresholds.
- Monitoring of Temperature: The majority of equipment is intended to run at a constant temperature. Increased friction in moving parts can cause early wear and equipment failure, and higher-than-normal temperatures can indicate this. These problems can now be avoided by sounding an alert if the temperature increases above a safe level.
- Pressure Monitoring: Pressure monitoring offers a continuous, in-the-moment evaluation of the fluid and air pressures in hoses, tanks, compressors, and other pressure vessels. It allows for the monitoring software to issue an alert in the event of a pressure change larger than a predetermined amount.
- Ultrasonic Monitoring: Ultrasonic testing consists of directing high-frequency sound through a structure to detect leaks, holes, cracks, and delamination.
- Radiation Analysis: This type of condition monitoring, which is a thorough non-destructive testing technique, uses radiation imaging to discover internal flaws in machinery or component parts. This technique relies on differential radiation absorption through a material because corroded and flawed portions absorb radiation differently from undamaged untouched ones. These approaches can be used on sintered components, and weldments can all use these approaches to test and analyze the absorption rates to look for production defects or any flaws developed in the service environment.
- Motor Circuit Analysis: MCA, or motor circuit analysis, evaluates the health of electric motors. It can be used to examine the insulation, any electrical imbalances, and the condition of the motor (including rotors and coupling/belt issues). MCA can be used to reduce energy usage expenditures and increase equipment efficiency, in addition to preventing breakdowns.
- Thermographic Testing: Thermographic testing measures the amount of heat radiated from electrical components using infrared sensors. Electrical resistance will start to rise when these components start to wear, which in turn causes a rise in the quantity of heat produced at these wear spots. Thermographic testing enables the early identification and correction of these wear indicators.
- Oil Analysis: Using sensors, oil analysis measures the makeup and wear of engine oil, identifying problems that could result in insufficient lubrication and damage to engine components. Sensors in oil analysis can check for excess water, or coolant in the oil, and other undesirable components as well as the pH level of the oil. Operators can get a clear indication from these sensors of when the oil needs to be changed.
- Acoustic Emissions Analysis: The acoustic emissions from a target component can be measured. This form of ultrasonic testing relies on sound waves emitted from the material without actively directing ultrasonic energy at the target. This makes it possible for maintenance crews to identify the existence and precise location of equipment problems such as fractures, leaks, and fiber breakage.
- Laser Interferometry: Laser interferometry can be used to locate surface and subsurface flaws in materials, including corrosion pits and casting or welding voids. This sensing method is based on comparing the returning wavelengths of a split laser beam bounced off the target surface. Laser shearography, electronic speckle pattern interferometry, strain mapping, laser ultrasonics, and digital holography are all examples of interferometry.
The Advantages of Condition Monitoring
Manufacturers can gain from implementing a condition monitoring-based approach in a number of ways:
- Decrease or Avoidance of Machine Failure: Condition monitoring maintenance is specially created to identify the first signs of prospective equipment issues, long before they become production issues as a result of machine failure. Process parameters are optimized and machines are operational a higher percentage of the time when run-to-failure methods and simply reactive maintenance are reduced or eliminated.
- Reduced Downtime: Strategically planned downtime can be implemented using a condition monitoring maintenance plan. This tactic will increase production efficiency, freeing up resources and benefiting the bottom line.
- More Effective and Productive Maintenance: Condition-focused maintenance, in contrast to preventive maintenance, uses technology to identify the root causes of actual equipment problems, so maintenance only takes place as necessary. This increases the effectiveness and allocation of maintenance resources.
- A Better Understanding of Machine Performance and Health: Data is the foundation of condition monitoring. By comparing previous performance data and benchmarks with current performance, you can get in-depth knowledge of process and equipment performance, and can send alerts when anomalies arise.
- Accurate Maintenance, Repair, and Operations (MRO): MRO ordering of spare parts can be made more strategic and efficient using data from the condition monitoring program. This also allows for enhanced accuracy and efficacy in inventory operations.
- Increase Return On Investment (ROI): Utilizing condition monitoring for predictive maintenance may increase the return on investment for your mechanical equipment. You can inspect, repair, or replace your machine only when it is absolutely required by keeping an eye on its actual condition.
- Safety: By using condition monitoring, owners may schedule a repair before a failure that could endanger nearby workers occurs.
The Disadvantages of Condition Monitoring
Despite the many benefits of condition monitoring, there are certain disadvantages as well, especially with regard to the initial setup of condition monitoring systems. These shortcomings include:
- Costs of Installation: Equipment for condition monitoring can be pricey to purchase and install. In some cases, the monitoring systems may even call for the modification of the machines to retrofit them with sensors. The price of installation could also go up if additional sensors are needed to adjust for operating circumstances.
- Operational Expenses: It will be necessary to hire engineers with the necessary skills and experience to implement the ongoing data analysis needed for condition monitoring. Both of these will incur additional expenses, but the numerous financial advantages of condition monitoring usually outweigh these.
- Damage in Harsh Operating Conditions: Additionally, in particularly challenging operating conditions, condition monitoring sensors may not function effectively. Such circumstances can harm sensors, requiring you to repair them more frequently.
The Bottom Line
Industry-wide adoption of condition monitoring as a strategy to guarantee the safe operation of machines and boost productivity is on the rise. Condition monitoring allows maintenance personnel to schedule and perform only needed maintenance, helping to improve machine uptime and save money that might otherwise be spent on the repair of catastrophic failures, or on preventive maintenance that was not actually needed.
Many machine owners are beginning to see the advantages of condition monitoring systems, even though there are still some situations where preventive maintenance is favored over CM-assisted predictive maintenance. Any industrial organization can benefit from condition monitoring.
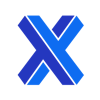