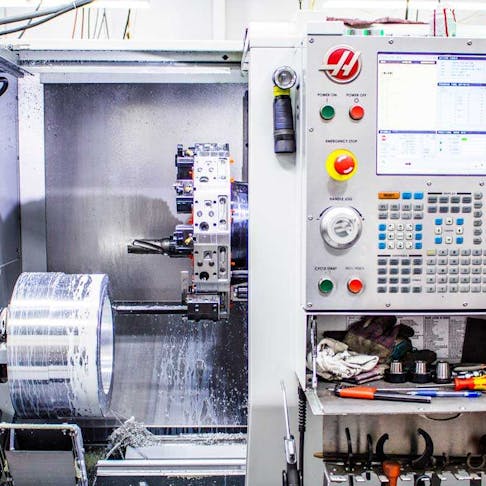
5 CNC Machine Maintenance Tips for Manufacturers
CNC machines are an invaluable part of any manufacturing operation. Therefore, it is imperative to conduct routine maintenance to avoid excessive machine downtime and costly machine repairs. Here are 5 maintenance tips to keep your CNC machines in top-notch shape.
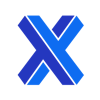
For many manufacturers, CNC machines are the beating heart that keeps a company alive. Without them, the company would struggle to be competitive in the global marketplace. These machines are used for the fabrication of products through processes such as drilling, milling, reaming, and turning. CNC machines are an invaluable part of any manufacturing operation. Therefore, it is imperative to conduct routine maintenance to avoid excessive machine downtime and costly machine repairs that could severely depress production efficiency and profits. In this piece, we offer 5 CNC machine maintenance tips to keep your CNC machines in top-notch shape.
1. Keep CNC Machines Clean
Perhaps the easiest way to maintain a CNC machine is to keep it clean and well lubricated. This includes cleaning every part of the machine: viewing windows, cutters, spindles, tool holders, fixtures, and jigs. CNC machines contain a number of moving parts, many of which must be lubricated to ensure optimal performance. Chips and other debris can impede the movement of these moving parts, cause premature tool wear, and affect part quality. Simply keeping the machine clean of debris and oils and replenishing lubricants as needed can go a long way toward prolonging the life of a CNC machine.
2. Develop a Routine Maintenance Schedule
Keeping up with CNC machine maintenance can be challenging in a fast-paced manufacturing environment. Nevertheless, manufacturers can benefit greatly from developing a schedule of routine preventative maintenance tasks that help to both improve production efficiency and ensure the longevity of the machine. Keeping CNC machines clean is one form of preventative maintenance, but other tasks could include replacing worn parts, reapplying and refilling necessary lubricants and oils, checking that the machine is level with respect to the floor, and inspecting the alignment of spindles and cylinders, among other things.
Newly purchased CNC machines often come with a manual that details recommended maintenance procedures and when to complete them. It is important to reference this manual when creating your own routine maintenance schedule. However, if such a manual is not available, developing your own procedures and strictly adhering to them can be a tremendous help.
3. Maintain Accurate Maintenance Records
Keeping accurate records is essential to a robust and effective maintenance program. By keeping a detailed record of which machines have been inspected and serviced, manufacturers can effectively plan future maintenance and allocate necessary resources for future work, such as tools or supplies. Strong, detailed records can also help manufacturers be more confident in their decision-making when it comes to CNC machine maintenance.
4. Establish Clear Maintenance Procedures
Creating a solid work request process, with clear communication about who is responsible for what is an important part of a good machine maintenance policy. While sensors and preventative maintenance schedules can help identify and prevent potential problems in machines, operators can also be critical in preventing unplanned downtime. Often, operators are the first ones to notice problems in machines - from unusual sounds to jammed movements. By having an easy way to report machine problems, maintenance or repair can be performed quickly to prevent an incipient machine problem from turning into a complete breakdown.
5. Keep a Spare Parts Inventory
The saying “time is money” is especially true in manufacturing. When CNC machines are down for repair for an extended duration, parts aren’t being produced, and consequently, parts aren’t being sold. Extended downtime can severely impact a manufacturer’s bottom line. To help alleviate the potential damage caused by downtime, consider keeping a spare parts inventory for your CNC machines. By having immediate access to spare parts, downtimes can usually be shortened. Prioritize stocking those parts that wear out or fail most, while also keeping on-hand parts that are harder to come by because of required long manufacturing lead times.
Maintaining a spare parts inventory is one way to make CNC machine maintenance less of a headache.
CNC Machine Maintenance Made Easy
For many manufacturers, CNC machines are the lifeblood of the operation. Without regular maintenance, CNC machines are prone to frequent breakdowns, and they may not have the expected longevity. However, by implementing the five tips above, you can stop reacting to machine mishaps, and instead focus on your preventive maintenance routine from the moment your new equipment is installed in your facility. CNC machine maintenance can be a challenge, but it doesn’t have to be. Contact a Xometry representative today to learn more about how to keep your CNC machines in top shape.
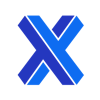