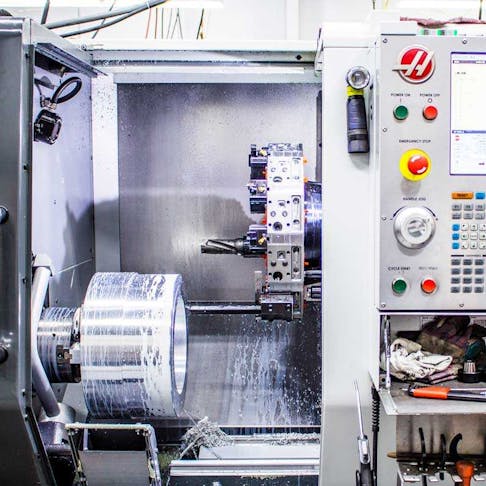
10 Tips For Selecting the Perfect CNC Machine
Selecting CNC machines is a serious financial commitment. However, the overall benefits that can be expected in terms of improved productivity, profitability, and increased product quality are well worth the investment.
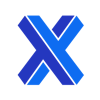
The 4th Industrial Revolution is currently in full swing, and manufacturers will need to automate if they hope to keep up with foreign and domestic competitors. One of the most accessible and impactful forms of automation is a CNC machine. A CNC machine can significantly increase overall productivity and profitability. This article will list some of the more important factors to consider when selecting CNC machines.
1. Determine Factory Requirements
The type of CNC machine required depends heavily on the nature of the work being undertaken. If parts are simple then a 3-axis milling machine or CNC lathe may be good enough. However, as complexity increases, it becomes more cost-effective to have equipment that can machine most parts in one setup. Five-axis CNC machines are best suited to this type of work. Other classes of products require specialized CNC machines. For example, if thousands of small, complex, cylindrical parts are required, a purpose-built Swiss lathe might be a better option.
2. Optimize Machine Cost
Cost is often the most important consideration when selecting CNC machines. CNC machines are generally significantly more expensive than manual machines. In addition to this, the cost of CNCs varies significantly depending on a number of factors. These factors can include the cost of tooling, cooling systems, chip conveyors, bar feeders, and automatic tool changers. Make sure that only the required add-ons are purchased. For example, a chip conveyor is not necessary if only small amounts of material are being removed.
3. Confirm Spare Parts Availability
Like any machine, CNC machines need to be maintained regularly to ensure that they operate optimally. For this reason, it is important to select a machine that has, at the very least, a local technical support division that stocks the spare parts most typically needed. This is even more critical if the machine breaks down, as every hour of downtime results in a loss of income. Competent and easily accessible technical support is also extremely valuable. Some companies charge extra for their technicians to be on call. This is well worth the cost when selecting CNC machines.
4. Plan Machine Placement
CNC machines take up significant amounts of space, especially if accessories like chip conveyors and tool changers are added to the machine, so it is necessary to plan ahead. Another factor to consider is machine weight. Large CNC machines are surprisingly heavy and require a concrete floor that is designed to support their weight. It is definitely worth the effort to pull up the factory plans to confirm that the foundation is sufficiently strong when selecting CNC machines.
5. Confirm Power Requirements
CNC machines are power-hungry and often run on 3-phase power. It is important to ensure that enough power is supplied to the building to serve the new equipment. It is also worth the effort to confirm current power consumption. There may be enough power supplied to the building when all the existing machines are running, but adding a new CNC might push consumption above the available level.
6. Machine Tooling
If multi-feature, complex parts are being machined it may be beneficial to add an automatic tool changer to the machine. This allows for continuous machining without operator intervention. For example, when the CNC is done machining a feature that requires one tool, it can be programmed to quickly retrieve the tool needed for the next process on its own instead of waiting for an operator.
7. Install a Reliable Air Supply
Most CNC machines require clean and dry pressurized air, typically around 90 PSI. Therefore, it is important to have a reliable supply of compressed air in a factory. If more machines are expected in the near future it may be worthwhile to size the compressor and the pressure lines to the machine accordingly in order to account for this future expansion. Consider installing a compressor with a larger air tank to allow for multiple machines to operate at once. A small tank will quickly be depleted if, for example, multiple machines perform a tool change at once. Think of future expansion and rather place the compressor in an area where it will not become a nuisance and pipe the compressed air to where it is needed.
8. Define the Materials Being Machined
The types of materials being machined are important factors when selecting CNC machines. Hard superalloys like Inconel require advanced machines with sufficient stiffness to machine accurate parts. If softer materials like aluminum or mild steel are being machined, cheaper machines can be considered that will still be able to maintain the required tolerances.
9. Control System
When selecting CNC machines, it is important to understand the implications of choosing one control system over another. CNC machines come with factory-installed controlled systems for example Fanuc, Haas, Heidenhain, etc. In most cases, the machine manufacturers will determine the control system but there are some manufacturers that give a few options regarding this. Haas control is known as being one of the easiest to use whereas Fanuc is more difficult but is packed with more features.
10. Train the Operators
It is important to ensure that existing operators are trained to use the specific type of CNC machine and its control system. If this is not possible, additional operators may need to be hired. Some machine suppliers will offer free training on their machines. Even if it is not free, it is well worth the cost.
Selecting CNC machines is a serious financial commitment. However, the overall benefits that can be expected in terms of improved productivity, profitability, and increased product quality are well worth the investment. Manual machining is no longer relevant in modern manufacturing and as such consider re-tooling to CNC machines to be part of the exciting future of automated manufacture.
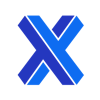