Best Practices for Oversized Hole Diameters
The strategic and proper use of oversized holes or slots according to established engineering standards makes part assembly easier and can save time and money without compromising structural function and safety. In this article, we explain the best practices for reliably forming high-quality oversized hole diameters.
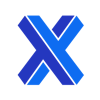
Components joined by threaded fasteners are held together by a clamping force that is the result of tensile stresses developed in the fasteners when the fasteners are tightened. These tensile stresses are known as “pretension” or “bolt preload.” It is critical that the clamping force be sufficient to hold the components tightly together. In some applications, any slippage between the two fastened components is considered a failure. In others, such as in transportation applications like bridges, the fastened parts are intended to move relative to each other along a specific axis.
The strategic and proper use of oversized holes or slots according to established engineering standards makes part assembly easier and can save time and money without compromising structural function and safety. Oversized hole diameters can account for slight deviations in the positions of mating holes after fabrication and help keep components in their correct positions after they are assembled. In this article, we explain the best practices for reliably forming high-quality oversized hole diameters.
Why use an oversized hole diameter?
According to the American Institute of Steel Construction (AISC), the diameters for oversized bolt holes depend on the diameter of the standard bolt hole and can be used to account for minor misalignments in assembly. However, larger oversized holes may be needed to accommodate construction tolerances, or for allowable misalignments. Oversized holes are also best for the types of slip-critical joints commonly found in road bridges that experience high cyclical loads due to passing cars and trucks. Oversized bolt holes are also best for parts that will be heat-treated or plated due to shrinkage that may occur within threads.
Oversized holes serve an important function when manufactured as specified by the designer or engineer. However, if a hole is cut too large for a specific bolt size, the bolt preload can be reduced because of the diminished contact area between the washer under the bolt head and the surface of the mating part. Similarly, holes that are larger than the allowable tolerances can increase stress concentrations in the joint. Both scenarios can lead to parts within an assembly becoming loose over time or a loss of structural integrity. Therefore, designers need to model bolted joints and understand the tolerances that can be safely specified, and that manufacturers need to meet these requirements.
Four Best Practices for Cutting Oversized Holes
While holes can be made with both conventional and CNC milling and turning machines, more complex part geometries may require holes to be cut on more specialized machines such as 5-axis milling machines or Swiss lathes. The typical process for cutting oversized holes is the same as cutting standard holes - that is, holes are drilled and then reamed to obtain the final dimensions. Before this happens though, parts need to be properly prepared by other machining processes and have the correct amount of stock material left for a reamer to open a hole to size, among other things.
The most critical part of creating any finished hole is to meet the required hole position, angle, and size tolerances. With that taken as a given, the manufacturer must seek ways to make the process as cost-efficient as possible. Here are three best practices manufacturers should use when cutting oversized holes:
1. Machine holes as close as possible to required dimensions
To obtain the desired fine balance between cycle time and part quality, manufacturers should perform their initial machining to bring the hole as close as possible to the required dimensions while using the minimum number of operations. This establishes an efficient process for each hole - and when an array of holes must be cut, this can save a considerable amount of time.
No matter the hole size to be cut, the process should start with a drill bit that is approximately half of the required hole size. Attempting to immediately drill a hole with a tool that matches the prescribed hole diameter can lead to too heavy a cut. This imposes extremely high forces on the cutter and can overheat it, which can lead to severely decreased tool life. Once a hole approximately half the required size is cut, manufacturers can keep increasing drill bit sizes to obtain a hole as close as possible to the required dimensions. A general rule of thumb is for holes to be cut about 0.010” to 0.015” undersized. From that point, manufacturers can then ream holes to the required final sizes.
FREE CNC Machining Design Guide
2. Use a boring head
While boring sometimes isn’t required, it is preferred for larger oversized holes where using reamers to obtain final dimensions isn’t feasible. In this case, it would be better to use a boring head, which is great for cutting larger holes that have tight tolerances. However, boring is also a good option for correcting alignment between the axis of the hole with the cutter or for short-run jobs that require cutting multiple holes. After cutting a “starter hole” with a drill bit, a boring head can be used to obtain final dimensions and, as with reamers, clean up the interior surface of the hole.
3. Use a reamer to obtain final hole dimensions
Unlike boring, holes should always be reamed. Once holes have been roughed in to near their final size, reamers can be used to enlarge the hole to obtain final dimensions and clean the hole’s surfaces. When using a reamer, manufacturers should use slower speeds and higher feeds than for similar-sized drills. Higher speeds cause the chip to cling to the edges of the reamer, leading to dulled tool edges and rough holes. Similarly, slower feeds can cause tool marks and undesirable surface finishes.
Depending on the type of reamer, manufacturers can obtain a lighter or deep depth of cut and better chip removal. For instance, floating and structural reamers can be used to clean hole surfaces and correct misalignment between the axis of the reamer and a drilled hole, however boring may be a more suitable process for this. Manufacturers should learn which type of reamer is best for obtaining their oversized hole diameters.
4. Tap, counterbore, or countersink the hole
Once the final dimensions for oversized holes are obtained, manufacturers can use any combination of tapping, counterboring countersinking to finish the hole according to the customer’s specifications. When tapping oversized holes, designers must use oversize taps that are 0.003” to 0.005” larger than the standard pitch diameter of the corresponding bolt. For counterboring and countersinking oversized holes, manufacturers should follow the same procedure as for non-oversized holes.
Cutting oversized holes, as opposed to standard holes, requires manufacturers to do a little more homework to obtain final dimensions. Therefore, when manufacturers receive drawings from designers stating holes are undersized, they need to follow best practices when cutting these to avoid part rejection.
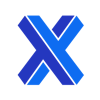