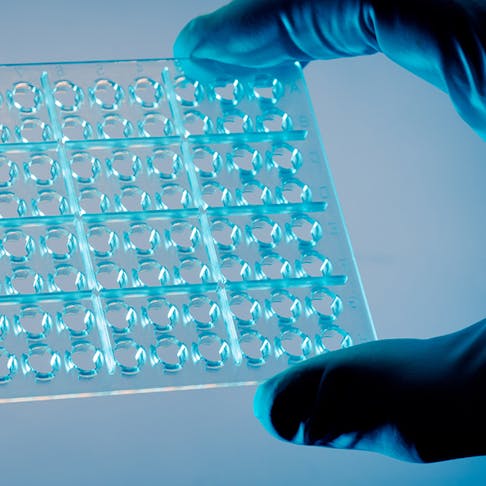
What are ISO 7 and ISO 8 Medical Cleanrooms?
ISO-certified cleanrooms in your medical device manufacturing facility are the easiest way to ensure that regulatory compliance is achieved. Here’s a quick look at the various levels of ISO cleanrooms and how you can go about getting yours certified.
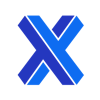
Medical device manufacturing requires an exceptional level of cleanliness. This is due to the severe medical complications that can arise if a contaminated medical device is used by a patient. One of the methods used to control the possible introduction of unwanted particles is to have a series of cleanrooms. This article will focus on the ISO standards concerning cleanrooms.
What is a Medical Cleanroom?
A cleanroom is essentially a controlled-access area with a clean environment that is maintained following a relevant standard to limit the introduction of contaminants. The most widely accepted standard for the specification of medical cleanroom cleanliness is ISO 14644-1, which is often expressed by the cleanroom levels it specifies. The ISO standard aims to classify different levels of room cleanliness by creating multiple levels, from ISO 9, which represents the lowest level of cleanliness, to ISO 1, which has the most stringent control of cleanliness.
In some cases, the old terminology related to Federal Standard 209 is still used – in which case ISO 7 is referred to as Class 10,000 and ISO 8 as Class 100,000. The cleanliness is quantified by measuring the concentration of airborne particles that typically have a size of 0.1 to 0.5 microns.
What Makes a Medical Cleanroom?
A medical cleanroom differs from a normal room primarily due to its advanced HVAC system and filters.
- HVAC System: The HVAC system used in a cleanroom is different from a standard system due to its ability to provide higher volumes and pressures of air when compared to normal HVAC systems. Each ISO level specifies the number of air volume changes per hour (ACH). This means that in the space of an hour the HVAC must cycle the entire volume of air by a defined number of times.
- Filters: HEPA (High-Efficiency Particulate Air) filters are normally used in cleanroom applications. This is due to their ability to remove up to 99.97% of airborne particles with a size of 0.3 microns.
- Construction Materials: A cleanroom needs to be constructed from materials that do not give off particulate matter, as this will degrade the performance of the room and reduce the effectiveness of the filters. In addition to this, the materials need to be easily cleanable.
How to Determine the Required ACH?
ISO 14644-1 clearly defines the required range of ACH for each level of a medical cleanroom. Specifically, ISO 7 and 8 requirements are listed below. More detail can be obtained here.
- ISO 7: Between 60 and 90 air volume changes per hour required
- ISO 8: Between 5 and 48 air volume changes per hour required
How to Size the HVAC Unit?
HVACs are sized by their volumetric flow rate, i.e. CFM (cubic feet per minute). To determine the CFM required for a specific cleanroom, the total volume of the room needs to be determined in cubic feet. Multiply this number by the required ACH as listed in ISO 14644-1 and then divide by 60 minutes. The answer will then be the CFM required to achieve the stated ACH level.
How to Size the Filters?
The number of filters required depends on the amount of airflow moving through the room. HEPA filters typically have a set flow rate that they can effectively handle; this information is available from the filter supplier. Simply divide the CFM of the HVAC by the amount that can be handled by one filter to determine how many filters are needed.
Medical Cleanroom Configurations
Cleanrooms work on the principle of cascading airflow. For example, if an ISO 7 cleanroom is required, the room before it should be an ISO 8 cleanroom. However, a key factor is that the ISO 7 cleanroom needs to have a higher pressure than the ISO 8 cleanroom before it. This means that contaminated air cannot move from the dirtier room to the cleaner room due to the pressure differential. In most cases, an additional gowning room is used where employees can get dressed without dirtying the cleanroom.
It must be noted that in some cases negative-pressure rooms are required to stop the escape of harmful particles from a cleanroom. In this case, an ISO 7 room would have a lower air pressure than the ISO 8 room so that particles cannot travel from the ISO 7 room to the ISO 8 room.
Who Needs to Have ISO Cleanrooms?
As mentioned previously, the medical industry has stringent cleanliness requirements due to the potentially life-threatening consequences of contamination that can cause infection. This is especially applicable to invasive medical implants and devices. One of the methods of controlling contaminants is the implementation of cleanrooms. Cleanrooms can either be mandated by governmental regulations or by industry standards. As such, it is the responsibility of the manufacturer to determine which laws and standards apply to their specific field.
In general, manufacturers of Class 1 or 2 medical devices often require ISO 7 and 8 cleanrooms, in which case the ISO 8 cleanroom can be used as the gowning room.
How to Certify a Cleanroom
As with any ISO certification, the onus is on the manufacturer to implement the recommendations as listed in the standard. Once all the recommendations are implemented, an audit can be requested. This audit is performed by a certified ISO inspector, and they will perform various air tests to classify the air quality and thereby determine if it meets the requirements of the standard.
The Benefits of Medical Cleanrooms
Having ISO-certified cleanrooms in your medical device manufacturing company is the easiest way to ensure that regulatory compliance is achieved. In addition to this, devices are manufactured in a way that limits the potential for harm being caused to customers, which can invite costly litigation and reduce customer confidence. It is critical to become familiar with local regulatory requirements before implementing a cleanroom within your facility as the requirements can change from region to region. It is important to note that having an ISO-certified medical cleanroom is only one part of a fully ISO-accredited medical device manufacturing facility. To learn more refer to our guide on implementing ISO 13485 certification.
Installing ISO 7 & 8 cleanrooms in a medical device manufacturing facility helps keep contaminants out of sensitive equipment while also ensuring that local or international best practices are followed. In some cases, these medical cleanrooms are legally required and, as such, it is important to check with local regulations.
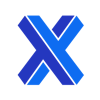