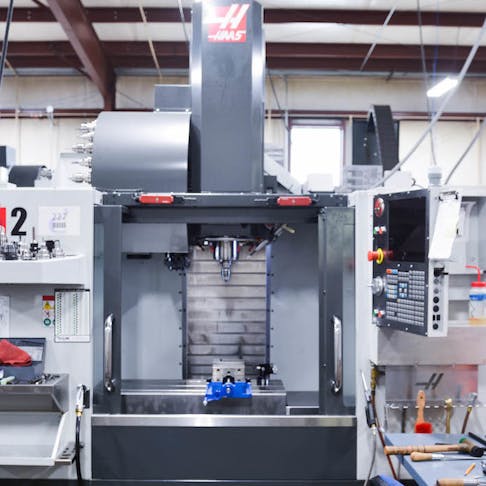
Manufacturing Tools of the Trade: Machines to Buy in 2020
Xometry recommends these 5 machines to build your machining portfolio. These machines are predicted to maintain capacity because of the high demand for customer parts that are suited for these machines.

As we saw in Smarter Machining Episode 4: The Best Machines to Buy in 2020, there are 5 machines that Xometry recommends buying in 2020 to build your machining portfolio. These machines are predicted to maintain capacity because of the high demand for customer parts that are suited for these machines.
5-Axis Machine
5-axis machines are often the flagships of a machine shop. They allow machinists to mill parts that require simultaneous 5-axis tool paths. 5 axes allow the machine to access and cut nearly every visible surface, which reduces the number of setups and errors due to handling, and also allows for automation of the job. But importantly, the machine can cut multiple datum surfaces in one operation, making it easier to hold tight tolerances.
Xometry receives many orders that can be machined most efficiently on a 5-axis machine due to the parts’ high complexity and tight tolerances, especially for parts that require assembly and mission-critical components across aerospace, automotive, medical, and consumer products industries. When parts have added surface finish requirements, 5-axis machines are ideal for producing parts with better surfaces since the rotating fourth and fifth axes allow path optimization for the cutting tool. This allows for a shorter cutting tool with lower vibration which allows for a less chattered finish.
A Dedicated 4-Axis or Add a Trunnion to Your 3-Axis Mill
For a cheaper alternative to a 5-axis machine, Xometry recommends adding a trunnion to a 3-axis milling machine to make it a 4-axis machine. Much like a 5-axis machine, adding an axis offers the benefits of being able to machine precision parts that hold higher tolerances, especially along the radial axis.
An extra rotary axis also offers more angles for your machine to cut the workpiece, which can significantly decrease run time and the number set-ups, allowing you to automate the work, decrease the chance of human error, and eliminate the need for special fixtures. Feature-to-feature accuracy increases when the same tool alignment, based on the same “home” location, is retained for the entirety of the machining set-up.
Live-action Lathe
Lathes alone are helpful for creating cylindrical parts, grooves, threads, and knurling. Live-action lathes combine the best of lathes and mills with live-action tooling. These add milling tools with a lathe to cut out non-concentric features like off-axis holes, right-angled pockets, gears, and angular features. These live-action lathes can take milling work when your mills are at capacity, allowing you to adapt to customer needs and job availability. With a lathe’s ability to feed rod stock without an operator and have multiple spindles, a live-tooling lathe can even become the shop’s busiest production platform, running multiple shifts with little intervention.
Wire EDM Machine
Xometry has been seeing an increasing amount of wire EDM work, so we recommend this for your portfolio. These machines work by feeding a metal wire charged with electricity through conductive metal while the workpiece is submerged in de-ionized water. An EDM wire machine allows you to access work that requires more specialized features with greater width and depth ratios, such as square internal features, splines, or small holes with extremely tight tolerances.
These machines are not only very efficient for manufacturing parts like extrusion dies and blanking punches, but also can handle anything from prototypes to critical, high-precision production runs. A Wire EDM allows machinists to distinguish their shops and maintain a higher shop capacity.
Waterjet or Laser Cutters
Waterjet and laser cutting machines are time savers and moneymakers. They can precisely cut material blanks, including internal through channels, making a net shape of the object for finish milling or turning. Because of significantly reduced material removal, waterjet and laser cutting machines can conserve tool life that would otherwise fracture or cause heeling. Custom cut shapes for milling can allow for higher part yield from raw stock material. With 4+ axis cutters, angled features can be achieved, complementing duties typically reserved for EDM or 5-axis machining.
Often used for sheet metal cutting, waterjet and laser cutting offer precisely the right amount of energy for thinner metals and plastics that require cutting on only one axis. Waterjetting is versatile and can cut materials with a thickness between 0.4” and 8.0” while laser cutting can typically handle materials between 0.12” and 0.4” thick. Waterjets can cut other materials like foam or gasketing without causing a melted edge like most lasers.
What Will Your Next Machine Be?
When looking for your next major capital investment, Xometry manufacturing partners, as well as any manufacturer looking to diversify their machine portfolio, should consider 5-axis, 4-axis, live-action lathe, wire EDM, and waterjet or laser cutting machines for their shop. These machines are likely will bring more diverse jobs your way and reliably fill with shop work.
