Investment Casting Services by Xometry
Xometry offers the highest quality investment casting services and can assist in the production of parts with intricate and complex geometries and excellent surface finishes. Subject to availability. Xometry doesn't guarantee that we can provide this service at any given time.
Investment casting is a molding process that begins with a wax facsimile of the final part. The wax object is coated in a ceramic slurry to create a mold. Once the mold sets, the wax can be melted out and molten metal introduced in its place. After the metal solidifies, the mold is broken and the new part is extracted.
Xometry offers the highest quality investment casting services and can assist in the production of parts with intricate and complex geometries and excellent surface finishes. The process accepts many materials, including but not limited to stainless steel, aluminum, and brass. Some common applications include pump impellers, turbine blades, and automotive cylinder heads.
What Is Investment Casting?
Investment casting, also known as lost wax casting or precision casting, is a manufacturing technique that creates finely detailed or complex parts by casting them in molten metal. This contrasts with other casting techniques like sand casting which are only capable of limited detail and imprecise surface finishes. Investment casting stands apart from other casting techniques in the manner in which the mold is created. In short, a disposable wax copy of the part is produced and coated with a ceramic/sand matrix to make a mold. This wax is melted out leaving an empty cavity. Molten metal is cast into this cavity and the mold must be destroyed to free the new part. Minimal post-processing is required.
The Investment Casting Process
The investment casting process has multiple steps as described below:
- Create the Pattern
- Mounting the Wax Patterns And Creating the Tree
- Creating the Mold Shell
- Wax Removal
- Melt and Cast
- Final Operations
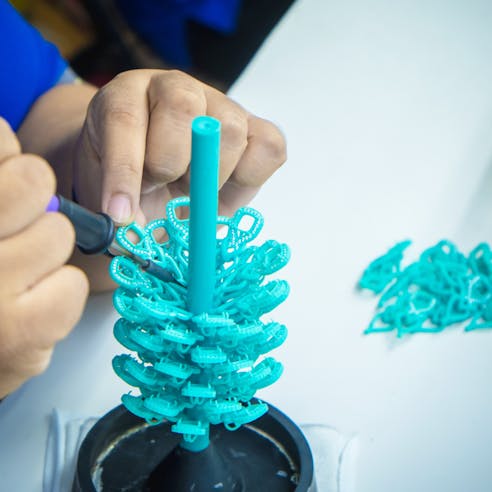
Create the Pattern
The pattern is a wax duplicate of the desired part. The pattern can be made using a purpose-built injection mold, by 3D printing the pattern with an SLA or SLS printer, or by carving it by hand. Depending on the metal being cast, the pattern may need to be slightly oversized to account for shrinkage during cooling.
Mounting the Wax Patterns And Creating the Tree
It’s rarely economical to cast a single part at a time. As such, multiple parts are cast at once. This is done by attaching multiple patterns to a sprue. A sprue is essentially a path for the molten metal to travel so that it will reach all the individual parts during casting. The sprue is also made from wax and each wax part gets attached to it via a gate (essentially a small sprue branch). The parts are attached by melting the ends of the gates to the sprue and parts. The completed wax assembly is known as a tree.
Creating the Mold Shell
To create the mold shell, the tree is then dipped into a liquid ceramic. The ceramic evenly coats the tree and is able to follow all of its intricate details. Next, while the coating is still wet, it is dipped into a bath of aerated refractory ceramic-like silica and/or alumina called stucco. This process is repeated multiple times until the coating reaches the proper thickness.
Wax Removal
After all the ceramic sets, the coated tree is placed into a furnace or an autoclave to melt the wax out. Once all the wax has drained, some molds receive heat treatment to prepare them for the thermal stress of casting.
Melt and Cast
The proper metal is melted using an induction or electric arc furnace. The molds are also preheated to a specific temperature that mirrors the metal’s melting temperature. This is done to ensure that the metal does not cool too quickly during casting. The metal is then poured into the mold where it travels along the sprue and into the individual part cavities via the gates.
Final Operations
Once the metal has solidified, the mold can be broken and removed. Many techniques can do the trick, including: mechanical shaking, high-pressure water jets, grit blasting, or manual removal. The individual parts are cut off the sprue and the protrusions left by the gates are removed by grinding them flush with the part. Some parts may need additional finishing operations like: machining, plating, painting, or heat treatment.
In need of custom investment casting services?
Investment Casting Materials
Listed below are some common investment casting materials;
- Carbon Steel
- Stainless Steel Alloys
- Brass
- Aluminum
- Glass
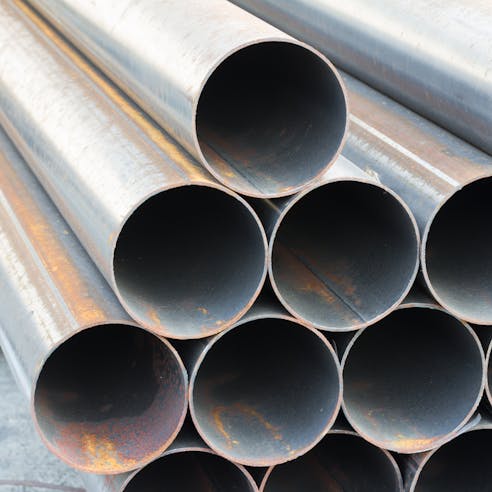
Carbon Steel
Carbon steel is a popular investment casting material. This is in part due to its low cost, mechanical strength, and the fact that cast parts can be heat treated or surface hardened after casting to improve their mechanical properties. Typical examples include valve bodies and pipe fittings.
Stainless Steel Alloys
Stainless steel is popular for its resistance to corrosion. However, stainless steel is significantly more expensive than carbon steel. Typical examples of stainless steel items include valve discs and corrosion-resistant pump bodies.
Brass
Brass alloys resist corrosion and conduct thermal energy well. They also have good mechanical strength. Due to their thermal conductivity, brass investment castings are often used in heat sinks or heat exchanger components.
Aluminum
Aluminum alloys have low melting points, good corrosion resistance, high thermal conductivity, and favorable strength-to-weight ratios. Aluminum also has a relatively low melting point which makes investment casting less energy-intensive. Typical applications can include heat exchangers and electric motor housings.
Glass
Glass can be cast using a number of techniques. However, investment casting produces parts with intricate and precise geometries that aren’t achievable through sand casting. Investment casting gets used to make designs that would be impossible using traditional glass forming techniques.
Investment Casting Advantages
Listed below are some common investment casting advantages:
- Size Range
- Versatile and Intricate Shapes
- Accurate and Smooth Surfaces
- Dimensional Accuracy
- Quality and Integrity
- Almost Any Metal Can Be Cast
- No Flash or Parting Lines
- Effective Utilization of Metal
- Fewer Environmental Hazards From the Foundry Process
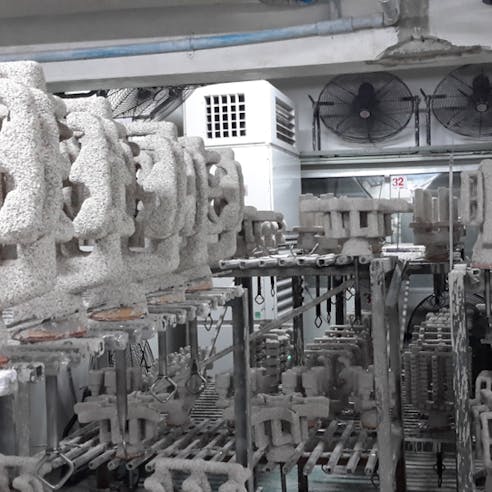
Size Range
Investment-cast parts can weigh anywhere from a few grams to a few hundred kilograms. Anything larger is better suited to other casting methods such as sand casting.
Versatile and Intricate Shapes
Investment casting is well suited to parts that have thin, intricate features and which require a smooth surface finish. Parts can be built from different wax patterns to produce complex designs.
Accurate and Smooth Surfaces
Investment casting patterns are often produced by injection molding wax into a polished mold. These patterns are then coated with a ceramic slurry that coats the surface of the wax pattern. As such, investment-cast parts can achieve a surface roughness of around 125 Ra (compared to sand castings that have a roughness of around 250 Ra).
Dimensional Accuracy
Investment-cast parts have excellent dimensional accuracy when the wax patterns are produced from the same set of precisely machined metal molds. Each time a wax pattern is molded, it will have consistent dimensional accuracy.
Quality and Integrity
Investment casting patterns are typically produced from high-quality steel molds which are machined to precise tolerances and can be polished to create parts with smooth surfaces.
Almost Any Metal Can Be Cast
Almost any metal can be cast using the investment process provided the metal's melting temperature is not too high for the ceramic mold. Metals like carbon steel and aluminum are common choices.
No Flash or Parting Lines
Because the investment casting mold is destroyed upon use, it contains only a single cavity; there are no parting lines or seams that could show up in the final part. This also prevents flash from forming which ultimately reduces the need for post-processing.
Effective Utilization of Metal
Unlike subtractive technologies like CNC machining, investment casting produces very little metal waste. Apart from the sprue and gates, all the metal is used in the final component, and very little post-processing is required. The material from the sprue and gates can also be remelted for use in the next production run.
Fewer Environmental Hazards From the Foundry Process
The wax used during investment casting can often be recycled and reused. It is inert and not hazardous. The ceramic mold material can also be recycled as a filler for concrete. This makes investment casting an environmentally friendly manufacturing process compared to many others.
Investment Casting Disadvantages
Listed below are some disadvantages of investment casting:
- Tooling Cost
- Size Limitations
- Timing
- Quality Management
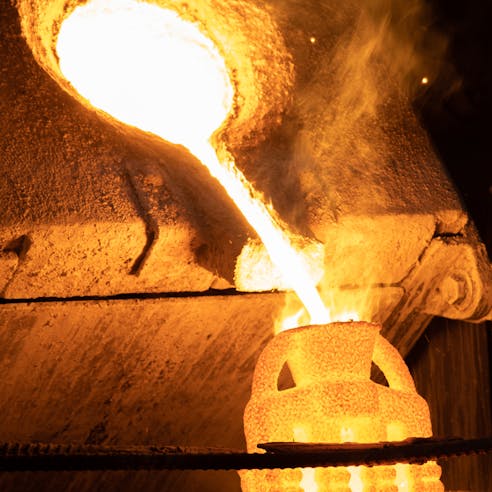
Tooling Cost
Investment casting can have high tooling costs. Firstly, the mold used to make the wax pattern must be precisely machined from metal. Next, the actual investment mold is destroyed after each casting. At low output volumes, the cost of the pattern can be reduced by 3D-printing the pattern. However, for large volumes, 3D printing is too slow for this task.
Size Limitations
Investment molding has an inherent weight limit and is not well suited to parts that exceed 200 kg. As such, it is best used for small, intricate components that can take advantage of the process’ surface finish and dimensional accuracy. However, it must be noted that there is also a lower limit on size for investment casting. Parts with holes smaller than 1.6 mm are hard to cast.
Timing
Investment casting is a multi-step process. Each component must have its own wax part. In addition, the sprue and gates must also be produced from wax and then carefully assembled into a wax tree. Once this is done, the tree must go through a multi-step dipping process to produce the mold. This all adds time, resulting in longer production cycles than many other manufacturing processes.
Quality Management
Investment casting is a complicated multi-step process. You must machine a steel mold, inject the wax, and produce the mold all before you even introduce the product’s actual material. Each of these processes must be monitored in order to ensure quality casting when it’s all said and done. This adds complexity to the quality management process.
Investment Casting Applications
Listed below are some common examples of investment casting applications:
- Aerospace Parts
- Military and Defense Equipment
- Process Equipment
- Triggers
- Medical Equipment
- Automotive Parts
- Turbine Blades
- Hand Tools
- Lock Parts
- Pipe Fitters
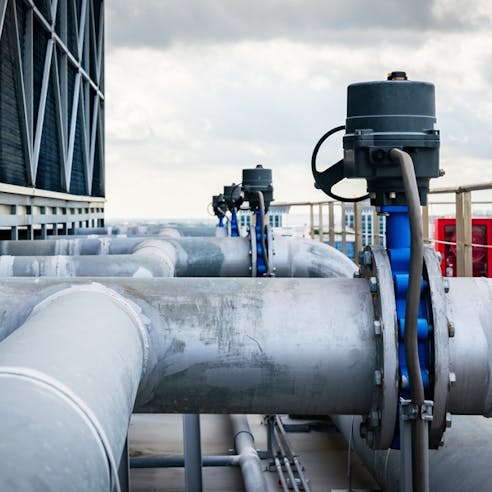
Aerospace Parts
Aerospace parts must meet stringent standards, so they need to be highly consistent and free of defects. Investment casting can meet these requirements. Common components include cooling tubes, engine rings, and valve nozzles.
Military and Defense Equipment
Military equipment must be manufactured to exact specifications in order to reliably operate in harsh conditions. Typical examples of investment-cast military components include missile fins, radar receivers, and firearm components.
Process Equipment
Process equipment like valves, heat exchangers, and pump impellers must often be made of corrosion-resistant materials like stainless steel or brass. Investment casting can meet both the material and precision needs.
Triggers
Firearm triggers are small, complex parts that need to fit into precisely machined assemblies and must perform consistently without jamming. Investment casting is ideally suited to firearm components because it produces precise and smooth surface finishes without the need for much post-processing.
Medical Equipment
Medical equipment must have excellent surface finishes to ensure it can be properly sterilized after use. Stainless steel medical devices are often produced using investment casting. Typical examples include surgical tools, diagnostic equipment, and orthopedic devices.
Automotive Parts
Investment casting is widely used in the automotive industry to produce such items as cylinder heads, rocker arms, and brake calipers. The process reduces the amount of machining required for complex automotive parts.
Turbine Blades
Turbine blades have complex geometries that must be precisely repeated to preclude balancing issues. In addition, these parts also have internal cooling channels. As such, investment casting is well suited to manufacturing turbine blades.
Hand Tools
Hand tools are typically machined or forged. However, investment casting offers an alternative that can produce accurate parts that require little to no post-processing. The manufacturing cost is also significantly lower than forging. Typical examples can include ratchet handles, hammerheads, and wrenches.
Lock Parts
Lock components need to be precisely manufactured to prevent them from being tampered with or picked. Locks are complex and include small features, making them ideal for investment casting. Typical examples include deadbolts, cams, and locking hooks.
Pipe Fitters
Carbon steel and stainless steel pipe fittings are often produced using investment casting. These parts have thin sidewalls that other casting techniques may not be able to achieve. Some pipe fittings like y-pieces have complex geometries that would be challenging and costly to produce using other casting techniques.
Alternative Casting Methods
Investment casting is a costly casting process intended for relatively low production volumes. As such, it may not always be the best choice for your application. Some alternative casting methods are listed below:
- Sand Casting
- Die Casting
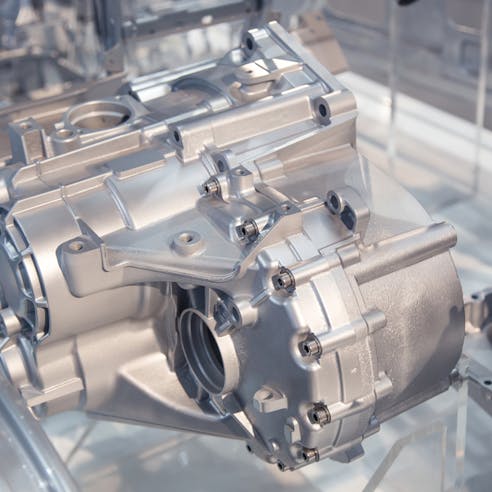
- Sand Casting: If precision and surface finish are not important, then sand casting can simplify production. Sand casting services consists of making a mold by packing refractory sand mixed with a binder around a pattern. Once casting is complete the mold is broken apart.
- Die Casting: If you need intricate parts made from non-ferrous metals at high production volumes, die casting could be a good alternative. Die casting is similar to injection molding, but instead of plastic, molten metal is injected into a metal mold.
Why Choose Xometry for Investment Casting Services?
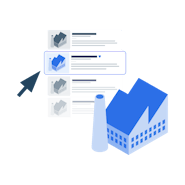
Endless Options
Choose from millions of possible combinations of materials, finishes, tolerances, markings, and certifications for your order.
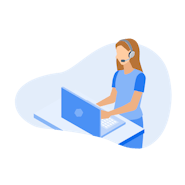
Easy to Use
Get started with our easy-to-use platform and let our experts take care of managing the project from locating the right manufacturing partner to delivery logistics.
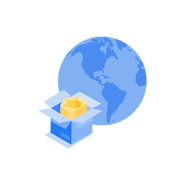
Vetted Network
We are ISO 9001:2015, ISO 13485, and AS9100D certified. Only the top shops that apply to become Suppliers make it through our qualification process.