Custom Online Laser Welding Services by Xometry
Get quotes on custom laser welded parts with our Laser Welding Service. Subject to availability. Xometry doesn't guarantee that we can provide this service at any given time.
Laser welding is a highly precise and cost-effective joining process that fuses metals or thermoplastics together with a powerful beam of light energy. The localized heat generated by lasers produces welds enabling exceptionally thin materials to be welded rapidly with minimal thermal distortion. Additional laser welding advantages include the ability to join dissimilar metals and the versatility to weld thick or extraordinarily thin workpieces.
Xometry offers laser services for a variety of materials and a broad range of applications, such as the assembly of dental and surgical instruments for the health industry, microelectronic components in electronics, and superalloy components in jet engines. With Xometry, you are assured of precise and high-quality components, quick turnaround, and superb customer service.
How Does Laser Welding Work?
Laser welding is a process used to fuse metals or thermoplastics with electromagnetic energy to produce welds. The energy emitted from a laser is highly concentrated. It heats small, localized areas between adjoining parts to melt and fuse them together. Laser welding can be used for both thin materials, where rapid welding speeds are often measured in several hundred millimeters per minute, and thick materials, where welding speeds must be slower to produce deep joints between parts. Laser welding differs from arc welding in that heating is facilitated by electromagnetic energy rather than electrical discharges.
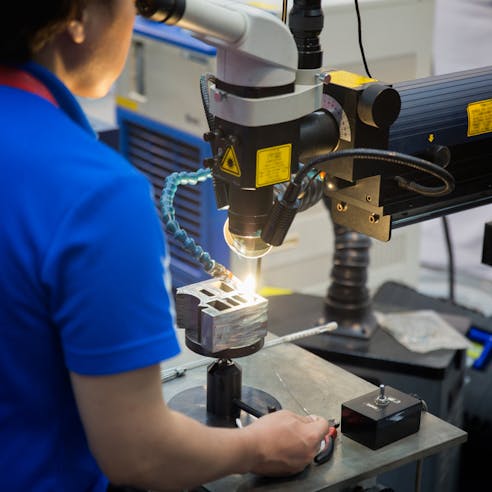
Advantages of Laser Welding
Laser welding offers several advantages compared to other joining processes such as arc welding or soldering. The advantages of laser welding are listed and described below:
- Cost Effective
- High Quality
- Extreme Precision
- Join Dissimilar Materials
- Speed
- Suitable for a Range of Material Thickness
- Versatility
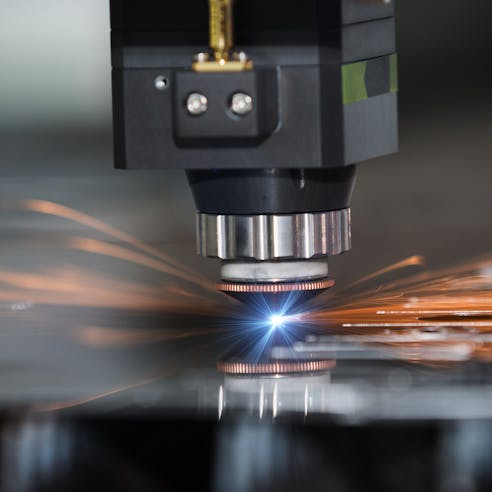
Cost Effective
Laser welding is a cost-effective process for large volumes of parts since materials can be joined rapidly with few errors. Additionally, energy from one laser beam can be shared to simultaneously weld two different areas. Both characteristics enable parts joined by laser welding to have a lower unit cost than other assembly methods.
High Quality
Laser welding is a precision joining process. Because the laser beam heats only a localized area, thermal distortion of the welded part can be minimized. Furthermore, since a laser welder is a CNC-driven machine, the weld path, and delivered energy are under tight control. This allows for high-quality welds with uniform bead sizes, little distortion, and high strength.
Extreme Precision
Laser energy is delivered in an extremely precise fashion to localized areas to weld two materials together. The small beam pot can make small welds on exceptionally small parts in precise locations in a repeatable fashion. Additionally, because the heat generated is isolated to small areas, the adjoining materials experience low thermal distortion. This allows for tighter control of tolerances in the assembly.
Join Dissimilar Materials
Unlike arc welding, laser welding can join dissimilar materials for economical, chemical, or structural reasons. Combinations like aluminum and copper, steel and aluminum, and titanium and steel are examples of materials that can be laser welded together.
Speed
Laser welding is a fast joining method. While welding speeds vary depending on the laser type, laser power, and the workpiece thickness, it is a much faster-joining method than manual processes such as arc welding or torch brazing. Thin materials can be welded at speeds of several hundred millimeters per minute while laser welding. Thick materials can be welded in a single pass using laser keyhole welding. Laser keyhole welding uses a powerful laser to heat localized areas to extremely high temperatures, creating a small hole. The small hole creates a vapor capillary that allows the thick materials to fuse faster.
Suitable for a Range of Material Thickness
Lasers are powerful tools that can be used to weld a wide range of material thicknesses. Materials with thicknesses as small as 1 mm to as large as 1” are weldable.
Versatility
Laser welding is a versatile process that can be used to weld metals or thermoplastics and can even weld dissimilar materials together. While lasers can be used for welding, the same laser source can be used for several other processes, such as laser cutting, laser engraving, laser marking, and laser heat treatment.
Need custom laser welding services?
Disadvantages of Laser Welding
Laser welding is not without its disadvantages. Some disadvantages of laser welding are listed and described below:
- High Upfront Cost
- Low Gap Tolerance
- Difficult to Laser Weld Highly Reflective Materials
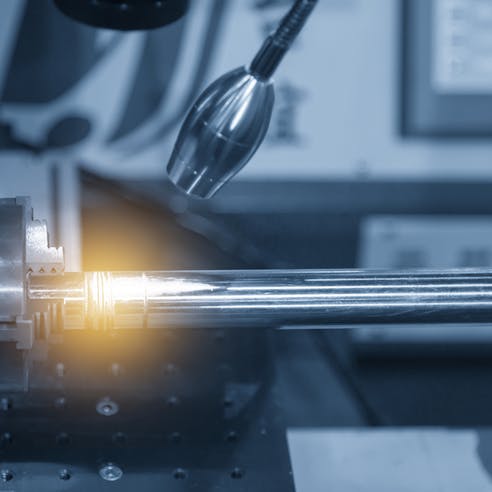
High Upfront Cost
Laser systems powerful enough to melt and fuse materials together at a reasonably fast pace have high upfront costs. CO2 lasers are best for welding thermoplastics and can cost anywhere between $10,000 and $200,000. Fiber lasers are best for welding metals and range in cost from $30,000 to $600,000. While CO2 lasers can easily weld most thermoplastics and can be used to weld metals, highly reflective metals are difficult to weld. This necessitates higher-power CO2 lasers or prior surface treatment to reduce reflectivity. Both instances lead to higher costs. Fiber lasers are more effective at welding metals since their wavelengths are readily absorbed by metals, but are more expensive. However, if production volumes are large enough, the high upfront cost of both types of laser systems can be offset by the lower production cost per product.
Low Gap Tolerance
Since laser welding is a precise joining method, its quality is highly affected by the positioning of workpieces before welding. If components are fitted together poorly, the welding quality and integrity will be diminished. Parts may have cracked, porous, or uneven weld beads. In laser welding, the low gap tolerance between parts means manufacturers must ensure upstream processes can dependably satisfy strict tolerances.
Difficult to Laser Weld Highly Reflective Materials
Laser welding is possible because materials absorb electromagnetic radiation by the laser beam and heat up as a consequence. The quality and speed at which a laser weld is completed depend on the adjoining materials’ reflectivity and the type of laser used. Highly reflective metals like copper, gold, silver, and brass readily reflect the long wavelengths produced by CO2 lasers which makes laser welding more difficult. Therefore, reflective materials must be surface treated to reduce reflectivity.
Applications of Laser Welding
Xometry offers high-quality laser welding for many different applications and industries. Some examples of the applications of laser welding are listed and described below:
- Dental Tools
- Surgical Instruments
- Delicate Diaphragm Assemblies
- Titanium Hip Prostheses
- Superalloy Jet Engine Impingement Tubes
- Transducers
- Butt Welding of Small Diameter Wires and Tubes
- Microelectronic Packages
- Bimetallic Strips And Thermocouples
- Thin Metal Foils
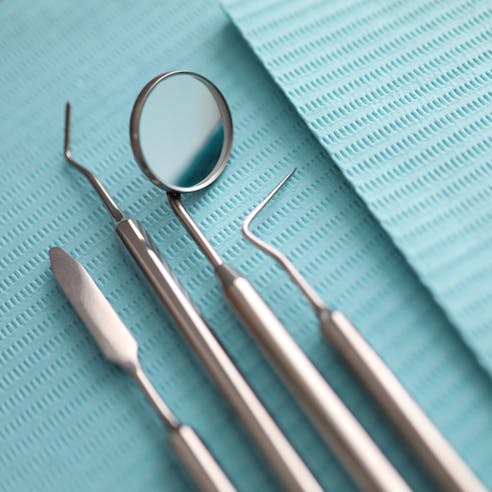
Dental Tools
Laser welding is often used in the fabrication of dental tools due to its high precision and ability to sustain large production volumes. Many dental tools and components have strict dimensional standards to ensure patient safety and usability. Additionally, laser welding’s ability to produce strong, defect-free, and aesthetically pleasing welds makes the process extremely desirable in the dental industry.
Surgical Instruments
As with dental tools, laser welding is commonly used to make surgical instruments. High precision and the ability to produce strong and defect-free welds are laser welding characteristics that satisfy crucial requirements for medical equipment. Minimal thermal distortion and precise dimensions in surgical instruments not only ensure patient safety but also result in ease of use for the surgeon.
Delicate Diaphragm Assemblies
Laser welding is ideal for delicate diaphragm assemblies. Diaphragms are used to control pressures within pressure regulators. Laser welding diaphragm assemblies remove the possibility of loosening the diaphragm, prevent fluid leakage, and ensure a strong bond for continuous, reliable pressure readouts.
Titanium Hip Prostheses
Laser welding is commonly used in joining prostheses due to its ability to join parts with minimal thermal distortion and its ability to produce clean and strong welds. Prostheses require extreme precision to ensure proper fit, form, function, and patient comfort.
Superalloy Jet Engine Impingement Tubes
Laser welding is used to join superalloy components in jet engine impingement tubes. This is because laser welding is a precise joining process that can quickly melt and fuse superalloys. Superalloy components are expensive compared to components made from more common alloys. Scrapping a superalloy component due to poor-quality welds is undesirable. However, laser welding is able to produce strong with few defects since it is a heavily automated process.
Transducers
Transducers are small components that convert attributes such as brightness, pressure, sound, and color to electrical signals. Because these devices are so small, laser welding is a good process choice because of its high precision and ability to produce joints with low thermal distortion. Additionally, since laser welding is a highly automated process, it can be used for manufacturing operations that produce large volumes of transducers.
Butt Welding of Small Diameter Wires and Tubes
Laser welding can quickly join wires or tubes because of its highly precise welds with low thermal distortion. Additionally, laser welding is great for butt welding small-diameter wires and tubes due to its small spot size, ability to limit the range of energy input, and ability to join dissimilar materials. These advantages make laser welding great for use in the electronics industry.
Microelectronic Packages
Laser welding is great for joining components within microelectronics packages due to its precision, speed, and ability to join dissimilar materials. The process’ ability to target highly localized areas reduces the likelihood of damage occurring in other components of the electronic device. Additionally, since laser welding does not require materials such as flux or filler materials to join parts such as in soldering, it is highly cost-effective.
Bimetallic Strips And Thermocouples
Bimetallic strips are a combination of temperature sensors and controllers that convert temperature changes to mechanical displacement. These components are often used in thermostats to monitor and regulate temperature.
Thermocouples are devices that use electrical voltage to measure temperature. Laser welding is great for both these applications due to its ability to join dissimilar materials, precision, speed, and ability to produce defect-free welds.
Thin Metal Foils
As many devices become more miniaturized, the use of smaller and thinner materials has become more common. Laser welding can be used to join thin metal foils and is ideal due to the localized heating produced by laser welding and the ability to control heat input.
Alternatives to Laser Welding
For applications not suited to laser welding, Xometry offers alternatives to laser welding such as:
- Arc Welding
- Brazing
- Soldering
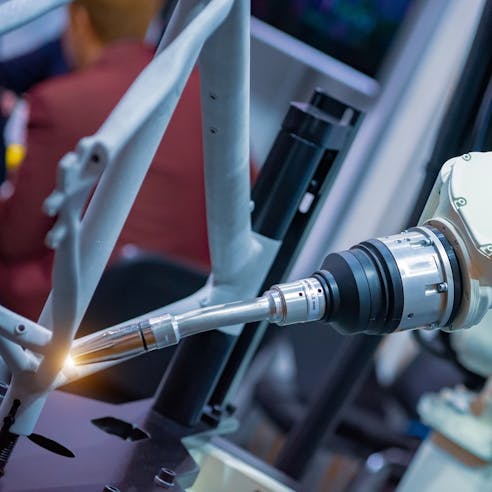
- Arc Welding: Arc welding is a metal joining process that involves melting two materials using the heat from an electrical arc discharge to fuse them together. While both arc welding and laser welding can be used for many of the same applications, arc welding may be better for lower volumes of parts. However, parts joined by arc welding are not as precise and often require post-processing to alleviate thermal stresses depending on the adjoining materials and the geometry of the parts.
- Brazing: Brazing is a joining process where the joints between two base materials are filled with molten filler metals or brazing alloys. Unlike arc and laser welding, brazing does not require the base materials to be melted. Instead, the base materials are heated to temperatures higher than the melting temperature of the brazing alloy, but lower than their own melting temperatures. Capillary action forces the brazing alloy to flow into the joint space and fill the tiny imperfections on the surfaces of the adjoining materials. The brazing alloy then cools, solidifies, and effectively joins the materials. Brazing is best for metals with poor weldability and low thermal resistance and for production environments that necessitate faster and more efficient production.
- Soldering: Soldering is a joining method similar to brazing. In soldering, a filler metal with lower processing temperatures (less than 450 °C) than those seen in brazing is used to join parts. Soldering alloys composed of tin are melted by a hot iron rod at around 316 °C. The molten soldering alloy on the tip of the hot iron rod is applied to join electronic components and pipes. Soldering is ideal for thin-walled parts and for joining dissimilar materials.
Why Choose Xometry for Laser Welding?
Endless Options
Choose from millions of possible combinations of materials, finishes, tolerances, markings, and certifications for your order.
Easy to Use
Get your parts delivered right to your door without the hassle of sourcing, project management, logistics, or shipping.
Quality Assurance
We are ISO 9001:2015, ISO 13485 and AS9100D certified.