Large Part Injection Molding Service
Get custom plastic molded prototypes and production parts in as few as 10 business days. We provide expert engineering reviews and $500 off your first mold. Dozens of materials and finishes are available.
Large part injection molding is a type of thin wall, high-pressure injection molding process used for manufacturing large plastic components. For more information on the injection molding we offer, including lead times, machinery, and more, check out our main injection molding services page.
Since small details become even more crucial when molding large parts, this article will go through all the basics about this commonly used manufacturing method. More specifically, it will provide information on what large part injection molding is, its applications, different processes that might be employed, and the materials and machines that may be used.
What is Large Part Injection Molding?
Large part injection molding, also referred to as large-tonnage injection molding, is the production of large plastic components using the injection molding technique. When molding huge components, it involves more than just a bigger press; the complexity of the item doubles or even quadruples, and the smallest details become even more important. A proper mold design is crucial since even the smallest mistakes exaggerate possible problems, such as uneven texture, knit lines, gate blush or flow and weld lines. One of the most significant differences between small and large component molding is the cost quality, with the latter being notably higher. Initial lead times for this method will also be a bit longer than small part injection molding since this type requires larger blocks of steel that take more time to shape.
During the large injection molding process, the plastic resin is forced into the mold cavity by employing extremely high pressure. Since the mold is made up of two distinct parts, a certain amount of force must be applied in order to fixate the two halves of the mold together. This force is known as a clamping force and it can be used for easily calculating the quantity of tonnage needed - a number that grows in direct proportion to the size of the part that’s being produced. Large part plastic injection molding technology can be used throughout diverse industries for producing a range of products from automotive parts to overhead projectors.
Large Part Injection Molding Processes
Two of the most commonly used injection molding part processes are gas assist molding and pad printing. Each of these processes employs different tools and techniques and offers different advantages and applications. However, large parts can be produced with other manufacturing processes as well such as the blow molding process, which is not an injection molding process even though it can be confused with it. The processes for large part production in more detail:
Gas Assist
Gas assist injection molding is a subset of plastic injection molding that employs pressurized nitrogen gas. It creates large plastic parts with complex shapes and excellent aesthetic surface finishes. This process starts just like traditional injection molding – with mold clamping and resin injection. Plastic material starts to solidify as it reaches the mold’s walls. At this point the gas is injected into the mold through strategically designed gas channels, creating pressure that forces the plastic material into the mold extremities. Once the plastic dries, that gas is either released into the atmosphere or recycled and the molded plastics are ejected from the mold.
The parts created with this method can be either contained-channel, such as tubes, armrests, handles, and frames, or closed-channel: panels, shelves, and chassis. The primary benefit of this method is its ability to improve the part’s aesthetic by preventing possible surface blemishes, sink marks, and internal stress. Apart from the enhanced surface definition and improved quality of the molded product, this technique reduces part weight, while also reducing the overall costs and cycle times.
Pad Printing
Pad printing, often known as stamping, is a relatively quick, simple, and cost-effective secondary processing technique for applying color to plastic injection molded objects. Secondary processing is the final step in the process. Different secondary operations can be used to improve the surface quality and integrity, appearance, and dimensional tolerance by further modifying the output of primary manufacturing processes. Pad printing works by etching the desired image onto a flat printing plate, which will then be filled with ink. After that, an ink-carrying silicone pad (pad printer) with chemical resistance is utilized to transfer the ink from the plate onto the molded component. The main advantage of using this pad is that it does not absorb the ink into itself.
The pad printing technique is very widely utilized due to its adaptability – it can print on objects that would otherwise be impossible to print on using conventional printing or stamping procedures. Moreover, this process can be used on irregular surfaces and shapes, while providing high print quality and great handling of finely-detailed images. The flexibility of the process makes it applicable to numerous large plastic components, from tubs to trash cans to pallets and crates.
Blow Molding
Blow molding is a process that squeezes a heated, liquid material that into a mold cavity under pressure, like other molding techniques. However, it also takes advantage of the features of conventional glassblowing. This manufacturing method differs from injection molding methods in types of molds, the usage of air, and the desired properties of the end product.
Blow molding machines are made up of three main components: an extruder, an accumulator die, and a variety of injection molds in various shapes and sizes. Blow-molded containers require a parison, which is a heated and filled plastic tube. The parison is placed in the blow molding machine, and the mold is clamped around the tube until the parison is molded into the desired shape. The melted material is then pumped into a mold that is held under extreme pressure during the molding process. As soon as the material cools down and solidifies, it is ejected from the mold so that the mold can be filled again.
The most obvious difference between this technique and conventional injection molding is the type of product made. More specifically, blow molding should be utilized when hollow and flexible parts are to be produced, such as water bottles, watering cans, chairs, and coolers. Advantages of blow molding include lower costs, fast manufacturing, and a higher level of versatility.
Using an Injection Molding Machine for Large Tonnage
Within the last decade, the demand for large parts has surged due to advancements in metal-to-plastic conversions, enhanced thermoplastic characteristics, and manufacturer ability to produce big, energy-efficient machines with short cycle times. In order to produce large parts, large-tonnage injection molding machines with high clamping forces are necessary. The machines for large tonnage are evaluated according to the tonnage, or in other words, the clamping force or pressure, which is the force needed to hold the mold's two halves together. The basic rule is that the larger the surface area of the molded component, the more tonnage will be required. Xometry offers presses from five to 3500 tons or higher.
The clamping pressure of 100 tons can be delivered using a machine rated for the same weight. During the injection process, this pressure holds the mold tight. Too much or too little pressure can lead to poor quality and flashing. This pressure also affects the viscosity of the plastic product that’s being produced. The Melt Flow Index (MFI) is a measurement of a thermoplastic polymer's melt flowability. Depending on their MFI, plastic compounds react to pressure differently. The pressure required increases as the MFI rises.
Another factor that should be taken into account is the shot weight - how much plastic is going in during the shot of plastic into the mold. It’s important to ensure there’s enough plastic being melted at a time to fill the mold before it solidifies. Equipment manufacturers help with these calculations by including how many ounces of polystyrene the barrel holds. They use polystyrene because plastics are different densities and expand differently in heat. Since polystyrene has a density of one, manufacturers figure out how much plastic the machine will hold by multiplying or dividing it by the values of other plastics.
Industries and Applications of Large Part Injection Molding
A wide range of industries depends on injection molding when it comes to the production of large plastic parts, mainly due to its low part cost and high versatility. The automotive, aerospace, and electronics industries especially benefit from this type of molding process.
Automotive Industry
Injection molding is one of the most used processes for producing large plastic components in the automotive industry, where uniformity, safety, and quality are critical. Fenders, grilles, bumpers, door panels, floor rails, lamp housings, and other external car components are all manufactured using injection molding; so are splash guards. Rubber or other durable and flexible materials are frequently used in the components that prevent splashing and protect the automotive from road debris.
Aerospace Industry
Large plastic components are commonly used in the aerospace industry since aerospace polymers have the same strength as metal but a significantly lower weight. In the aerospace sector, improved aircraft performance and lower fuel costs are critical, and the special qualities of aerospace plastic components enable them to do both. Fuselages, airframes, wings, door fairings, and empennages are increasingly made of plastic. These large molded components have metal-like tensile and flexural strength at a fraction of the weight, and they require less maintenance. Polymers are also becoming more common in propulsion systems, such as turbines, propeller systems, and engine housings.
Electronics Industry
Within the electronics industry, injection molding large parts is used for creating parts for refrigerators, washing machines, televisions, phones, laptops, and other appliances. Plastic makes up the basic structure and the sections that keep all of the electrical components together. A plastic casing is required to keep all electronic components together. For example, the TV's base and frame are both made of plastic.
Materials for Injection Molded Parts and Components
Materials used in injection molding parts and components are mostly plastics, specifically plastic resins. Resins can be further grouped into thermoset and thermoplastic resins. Thermosetting plastics and thermoplastics are both polymers, but they react to heat in different ways. After cooling, thermoplastics can melt when exposed to heat, while thermoset plastics keep their shape and remain solid.
The best materials for large parts are plastics with good flow length, which is plastic that will stay molten in the mold for a longer period of time. Since there exist many different types of resin, as explained in our injection molded plastics and elastomers guide, it’s important to take into account the final product’s desired functionalities and main application before choosing the appropriate material. Should it be UV or heat-resistant? Should it be solid or flexible? Should it be food-safe?
Once a decision has been made on using a thermoplastic material, the next choice to make is which type of thermoplastic to employ. The two possible options are amorphous plastic and semi-crystalline plastic. Since amorphous materials don't have a distinct melting point, they shrink or expand less when heated or cooled, allowing for a more forgiving and progressive process. Semi-crystalline plastics, in contrast to amorphous plastics, have a substantially higher melting point and are known to expand and contract much more when subjected to temperature extremes. Some well-known amorphous plastics are polystyrene (PS), acrylic, and polycarbonate. On the other hand, polypropylene (PP), polyethylene (PE), nylon (Polyamide), and polyoxymethylene (POM) all belong to the semi-crystalline plastic family.
Some of the most popularly used plastics for large parts include:
High-Density Polyethylene (HDPE)
Polyethylene is the world's most widely used plastic. There are three major categories: Low density (HDPE, PEHD), high density (LDPE), and polyethylene terephthalate (PET, PETE). While both HDPE and LDPE have beneficial properties like chemical resistance, they differ in terms of hardness, flexibility, melting temperature, and optical transparency. Unlike HDPE and LDPE, PET is not defined by its density.
HDPE is the best material to use when a robust, heat-resistant plastic is required. When it comes to large part injection molding, high-density polyethylene is often used to make storage containers, cookware, and refrigerator shelves since it is food-safe plastic. Some of its advantages are:
- Heat resistant
- Low-cost
- Chemical resistant
- Food-safe
- Recyclable
Acrylic (PMMA)
Acrylic, commonly known as Plexiglas, is a transparent thermoplastic homopolymer that is frequently used as a more durable alternative to glass. Due to its inherent transparency and coloring qualities, acrylic is commonly used in the electronics and automotive industries, while also being employed in everyday items such as lenses, acrylic paint, and even acrylic nails. Acrylic can also be tinted to make it transparent or opaque. Acrylic products are:
- Transparent
- Chemical resistant
- Weather resistant
- Strong and rigid
Nylon Plastic (PA)
Nylon is one of the most versatile plastic injection molding materials. To increase certain properties, nylon is frequently mixed with other materials. Filling nylon with glass fibers, for example, boosts tensile strength while making it less flexible and brittle. It's a multipurpose, robust, and flexible material that's frequently utilized as a less expensive alternative to silk, rubber, and latex. Nylon polyamide also has the following advantages:
- Low friction
- Abrasion resistant
- Chemical resistant
- High melting temperature
Structural Foam
Structural foam is a simple and inexpensive option for the production of large components without compromising their strength, stiffness, or overall quality. During the molding process, a thermoset (but not necessarily thermoplastic) polymer is coupled with either an inert physical gas, such as nitrogen, or a chemical blowing agent to generate structural foam. The end result is a low-density, microcellular "core" with a high-density outside skin rather than a solid substance. When compared to typical polymers such as polyurethane, polyester, or epoxy, it is lightweight and flexible while maintaining good strength and stiffness. Vehicle roofs, interior and exterior body panels, medical equipment housing, and even skis have all benefited from structural foam's capacity to make pieces of enormous scale.
The material has a sandwich-like structure, with the low-density core fully covered by a higher-density skin. The texture of the core has been compared to that of a sponge or a honeycomb. Structural foam is often 20-40% lighter than solid polymers, aluminum, steel, sheet molding compound, or other regularly used materials due to its distinctive core texture, which significantly reduces the part’s overall cost. However, one must take into account that creating lighter parts might have a negative impact on their aesthetics. The basic material utilized in the manufacture of structural foam is often a thermoplastic polymer rather than a thermoset polymer due to its not-quite-solid state. Apart from its ability to create large plastic items, this material has a number of other benefits:
- Extremely lightweight
- Moldable
- Temperature resistant
- Low-cost
- Aesthetic and paintable surfaces
- Uses foaming agent to lighten the weight of the parts. This may impact cosmetics, however. Structural foam is beefed up foaming agent, so it adds bubbles to decrease part weight.
Why Choose Xometry For Large Part Injection Molding?
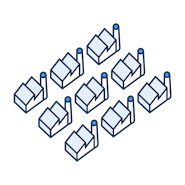
Endless Options
Choose from millions of possible combinations of materials, finishes, tolerances, markings, and certifications for your order.
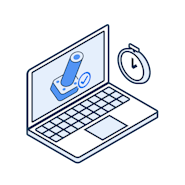
Easy to Use
Get your parts delivered right to your door without the hassle of sourcing, project management, logistics, or shipping.
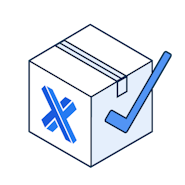
Vetted Network
We are ISO 9001:2015, ISO 13485, and AS9100D certified. Only the top shops that apply to become Suppliers make it through our qualification process.
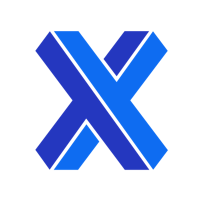