Urethane and Silicone Casting Services for Maryland
High Quality Urethane and Silicone Casting serving Maryland| ITAR Registered | Low Volume, Durable Parts with Production-Level Quality
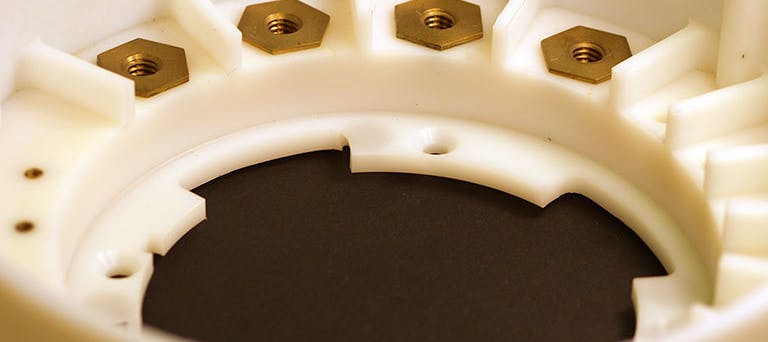
Your Maryland Urethane Casting Service
Urethane casting provides end-use, rigid plastic, rubber, and silicone parts with production-level quality. Xometry is a leader in urethane casting services with domestic (US-based) and international economy options to fit your timeline and budget. Urethane gives professional results for low-volume production using a soft-tooling approach. The urethane casting process uses a 3D printed master pattern and RTV silicone molds to deliver high-quality, short-run parts up to 30” long. The finished dimensions of urethane cast parts depend on the accuracy of the master model, part geometry, and casting material. In general, a shrinkage rate of + 0.15% is typical.
Cast urethane parts are ideal when color, surface quality, and toughness are required for quantities from one to one hundred. Urethane molding is a perfect alternative for insert molding or overmolding in low volumes with diverse material choices. Polyurethane or silicone casting can bridge production between a 3D printed rapid prototype and an injection molding with a balance of quality, cost, and time. Urethane cast parts can be clear, color-matched, painted (including EMI shielding), installed inserts, and custom finished.
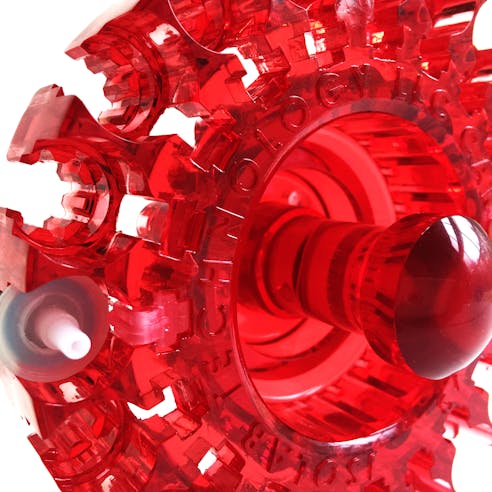
Urethane Casting Materials
Polyurethane is a widely used thermoset material grouping known for its strength, durability, abrasion resistance, and versatility. Different urethanes can mimic the properties of many common thermoplastics. For example, a stiff urethane cast part is “polycarbonate-like,” and a more flexible plastic may be “polypropylene-like.” We group our urethane materials into general categories to help you make quicker decisions and get the best performance on your project. The list below describes the categories of materials and technical examples when selecting polyurethanes.
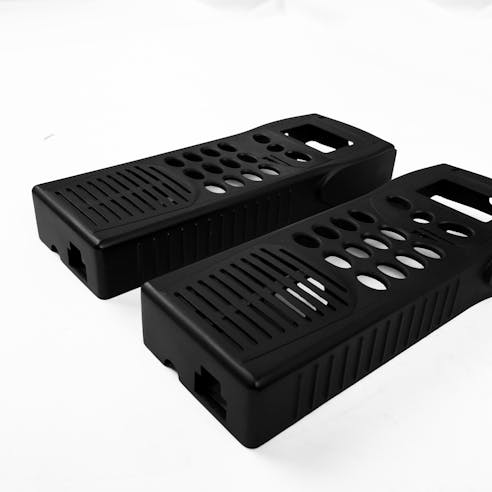
Material Name | Shore Hardness | Description | Technical Information | Data Sheets |
---|---|---|---|---|
Material Name General Purpose | Shore Hardness Shore D 76-80 | Description An impact-resistant Shore 78D material used for a variety of purposes, from enclosure housings to concept models. This material exhibits ABS-like properties. | Technical Information TC-878, TC-852, or equivalent | Data Sheets |
Material Name Rigid Clear | Shore Hardness Shore D 80 | Description A versatile, Shore D 80, clear polyurethane. A matte finish will give a frosted appearance and a higher gloss will increase its transparency. | Technical Information Poly-Optic 1410 or equivalent | Data Sheets |
Material Name ABS-Like, FR | Shore Hardness Shore D 78-82 | Description A tough Shore 80D flame retardant material that is UL Listed with a flammability rating at 1/16" (1.6 mm). | Technical Information TC-891-FR or equivalent | Data Sheets |
Material Name Polypropylene-Like | Shore Hardness Shore D 65-75 | Description A tough and abrasion-resistant flexible urethane with polypropylene-like ductility. | Technical Information TC-872, HP-2270D, or equivalent | Data Sheets |
Material Name Polycarbonate-Like | Shore Hardness Shore D 82-86 | Description A stiff, high impact, high HDT, material with a wide variety of uses. Simulates polycarbonate (non-clear), Shore 84D. | Technical Information TC-854 or equivalent | Data Sheets |
Material Name Glass-Filled Nylon-Like | Shore Hardness Shore D 85 | Description A stiff, USP Class VI, high-performance urethane with high impact strength and a HDT of 190°F (88°C). | Technical Information PT8902 or PT8952 (FR) | Data Sheets |
Material Name Rubber-Like Polyurethane | Shore Hardness Shore A 25-95 | Description A Shore A elastomer with a high elongation to break. | Technical Information F-130 to F-190 or equivalent | Data Sheets |
Material Name Clear Rubber-Like Polyurethane | Shore Hardness Shore A 40-95 | Description A colorless Shore A elastomer with a high elongation to break. Matte finish will give a frosted appearance, and higher gloss will increase its transparency. | Technical Information WC-540 to WC-595 or equivalent | Data Sheets |
Note: Equivalent materials may be used based on availability and the location of work performed.
Cast Silicone Materials
Silicone is not only used for making tools in casting, but it is also an excellent material for parts. Silicone is durable, stretchy, tear-resistant, inert, easy to clean, and has a high-temperature resistance. Silicone rubber can achieve ultra-soft durometers as low as Shore A 10 and up to medium-hard rubbers in the Shore A 60 range. Silicone casting is ideal for medical devices, surgical models, props, soft-touch housings, kitchen accessories, and more.
- Shore A 10 (TC-5005 or equiv.)
- Shore A 20-30 (TC-5130 or equiv.)
- Shore A 30-40 (TC-5140 or equiv.)
- Shore A 40-50 (TC-5150 or equiv.)
- Shore A 50-60 (Smooth‑Sil™ 960 or equiv.)
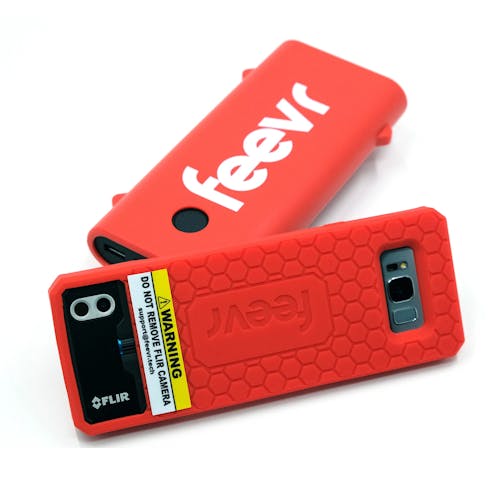
Parts have a smooth, satin-like finish due to the master pattern being bead-blasted matte. Transparent and translucent parts with this finish will appear frosted. Matte finishes are helpful for handheld and high-touch areas as it reduces fingerprint visibility.
Semi-gloss finishes include some sheen but not high reflectivity. Semi-gloss finishes are between high-gloss and matte, resulting in a smooth, easy-to-clean surface.
A highly reflective glossy finish requires polishing the master pattern before making the mold. The high gloss has a high sheen and will have the highest transparency for transparent parts. High gloss is helpful for cosmetic models, cleanable surfaces, and lenses.
Texture is applied via paint and manual techniques to the master pattern before making soft tooling. Texturing is useful for high-use surfaces, like handles, where the small raises and reliefs improve the grip and reduce fingerprint or scuff marks.
Xometry can provide additional processing, including secondary finishes, painting, and more.
Urethane Color Options
Polyurethanes can be blended with pigments to achieve a variety of colors. Naturally, a urethane may be amber to milky-white in color. Xometry's clear urethane options are formulated to be colorless. Below are Xometry's color options:
- Black
- Color-Match
- Natural (unpigmented)
- Clear (colorless)
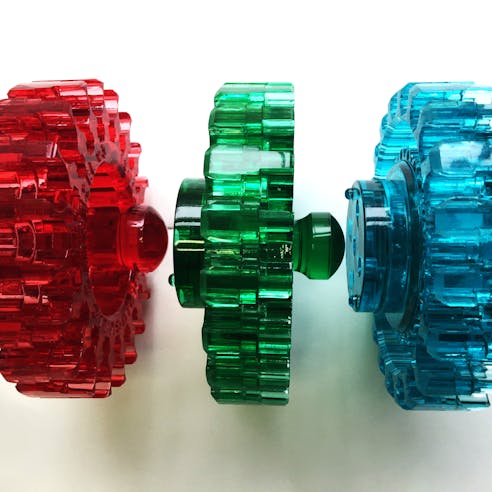
Urethane and Silicone Casting Services near Maryland
Ready to Get a Urethane Casting Quote?
Applications of Urethane Casting
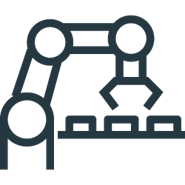
Low-Volume Production
Urethane cast parts are perfect for low-quantity production—when volumes do not justify investment in injection mold tooling—as well as for first run production parts, which can be completed weeks before production tooling is ready.
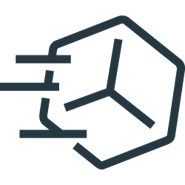
Advanced Prototyping
The urethane casting process and relatively inexpensive tooling involved makes it easy and economical to make any necessary design changes. Additionally, different materials can be used with the same mold, making it possible to test designs with a variety of materials.
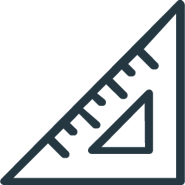
Market Testing
End-user functionality and a high-quality finish makes urethane cast parts ideal for consumer testing, user evaluation and concept models. Using the cast urethane process means that changes can be incorporated quickly for either further testing or market launch.
The Basics Of Urethane Casting
Urethane casting provides end-use, rigid, flexible, and rubber parts with production-level quality. The urethane casting process uses a 3D-printed master pattern to create a silicone mold that delivers high-quality, short-run parts as an economical alternative to low-volume injection molding.
How Urethane Casting Works
Urethane casting is similar to injection molding in that it requires a tool with a cavity in the shape of the final part. The major difference is that urethane casting uses a "soft" mold made of silicone whereas injection molding using a "hard" metal mold that has been CNC machined. The drawback to urethane casting, then, is that the mold wears out more quickly. However, it is vastly more cost-efficient for low-volume and prototype plastic parts that require production-level quality and surface finishes.
The urethane casting process has 3 major steps:
- The Master Pattern: In step one, a master pattern of the final part is made using an additive manufacturing process. Polyjet 3D or stereolithography (SLA) 3D printing processes are most often used due to their ability to produce high-resolution and naturally smooth finish parts. The master pattern is typically hand-finished to achieve optimal surface detail before the creation of the mold tool.
- Molding: In step two, the 3D printed master pattern is encased in liquid silicone that cures around the pattern, with the silicone encapsulating all the features of the printed parts. When the mold cures, it is cut into distinct halves and the master pattern or 3D printed part, is removed. This leaves an internal cavity perfectly shaped like the part.
- Pouring: In the final step of the urethane casting process, liquid urethane or silicone is poured into the silicone mold, and the mold is then placed in a chamber to help remove air bubbles in the liquid material. For opaque parts, the chamber is typically pressurized. For clear parts, the chamber typically pulls a vacuum to mitigate any bubbles and increase clarity. Once cured, the silicone halves are separated and the newly formed part is removed. This process is repeated until the desired quantity is achieved.
Benefits Of Urethane Casting
Urethane casting has a low-cost and quick turnaround for high-quality plastic parts compared to injection molding or 3D printing. Where injection molding requires an expensive upfront investment for the machining of the mold, the silicone mold required for urethane casting is inexpensive and easy to produce. Additionally, while most 3D printing processes require extensive post-processing to get to a near-finished state, urethane cast parts come out of the mold ready to go. Urethane casting is an excellent choice for creating high-quality prototypes or low-volume production of rigid, flexible, clear, colored, or rubber-like plastic parts.
Urethane Casting Tolerances
Description | Tolerance Notes |
---|---|
Description Distance Dimensions | Tolerance Notes =+/- 0.010” or +/- 0.003” per inch, whichever is larger, is typical. Irregular or overly-thick geometries may cause deviances or deflection due to shrinkage. |
Description Shrink Mitigation | Tolerance Notes A shrinkage rate of +0.15% can be expected due to thermal expansion of the liquid, and the response of the flexible mold. |
Description Surface Quality | Tolerance Notes Surface finish is externally smoothed to a satin or matte surface. Grow lines may be present on internal or difficult-to-access features. Polishing or custom finishes must be clearly defined and agreed upon at the point of order. |
Description Feature Definition | Tolerance Notes Sharp corners and text may appear slightly rounded. |
Description Size Recommendation | Tolerance Notes We can offer urethane cast parts as large as 30” (0.762 m) long. |
This table is based on the assumption that designs have an adequate draft, radii, and coring for manufacturability. Please see Xometry's Manufacturing Standards for more information on tolerances per process.
One of the most critical distinctions between urethane casting and 3D printing is material performance and quality. Urethane casting offers higher-performing materials that can better emulate those used in commercial products. In addition, the fit and finish are often better with urethane cast parts. If material performance and appearance are important to you, urethane casting should be a strong consideration.
The primary deciding factor between urethane casting and injection molding is quantity. Urethane casting is an excellent option for very low quantities (e.g., 50 pieces) of production-grade parts. Compared with urethane casting, injection molding will have higher upfront tooling costs that may not justify a low quantity run. Often, our customers use urethane casting as a stepping stone to test and refine their design before they invest in an injection molding tool.
Why Choose Xometry for Urethane and Silicone Casting Services near Maryland?
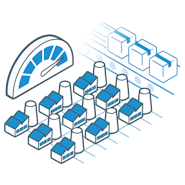
Endless Options
Choose from millions of possible combinations of materials, finishes, tolerances, markings, and certifications for your order.
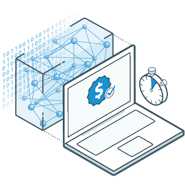
Easy to Use
Get your parts delivered right to your door without the hassle of sourcing, project management, logistics, or shipping.
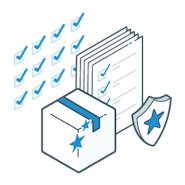
Vetted Network
We are ISO 9001:2015, ISO 13485, and AS9100D certified. Only the top shops that apply to become Suppliers make it through our qualification process.
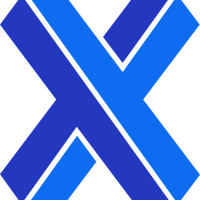