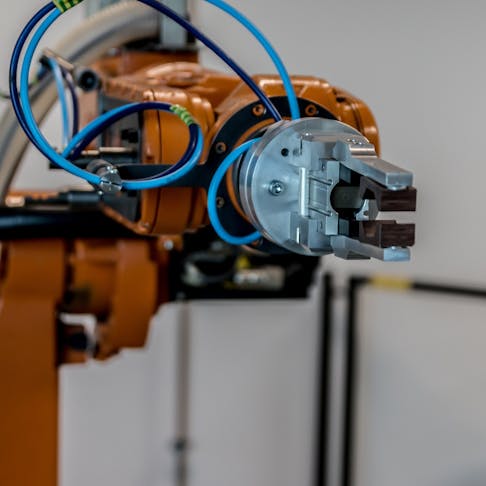
What Is Digital Transformation and How Can Machine Shops Benefit From It?
Digital transformation encourages manufacturers to use new technologies and methodologies to improve their processes and open new opportunities. Learn more about it here, including its benefits.
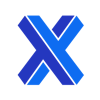
Digital transformation in manufacturing is the use of technologies and new methodologies to future-proof industries and open new opportunities in a more connected world. The digitization and automation of the manufacturing industry are accelerating. The post-COVID world has created many challenges in terms of supply chains, changing market trends, and rapid changes in customer sentiment. But this environment has also given businesses the impetus to take risks and try new things. This leaves other companies with no choice but to modernize and transform their practices.
The senior leadership in any business drives the real changes in culture and technology. This article will define and describe the digital transformation and how it applies to manufacturing, including its benefits, and the key challenges to be faced in the short to medium term.
What Does Digital Transformation Mean for Manufacturing?
There are four key areas in which manufacturing engineers and machine shops can implement digital transformation to take advantage of new technologies within their industries. These areas are listed below:
1. Equipment and Process Monitoring
Automated reporting on the status of manufacturing equipment and processes is the most basic level of digitization for a manufacturer. Collecting and analyzing live data on the status of assets gives a real-time account of the business, production output, quality monitoring, and other parameters.
Smart sensors have driven manufacturing companies to move from preventative maintenance routines to predictive maintenance. Critical machine component temperatures can be monitored over time, with coolant levels and usage optimized for the specific conditions being experienced by the equipment. In the near future, machine learning will replace traditional equipment monitoring processes. Equipment will learn from prior experience and adjust its own maintenance routines and settings. This allows businesses to use data rather than fixed time intervals to reduce the need for intervention when it is not actually required, or to alert the technician to take action when machine failure is predicted imminently.
2. Advanced Automation and the Internet-of-Things
Advances in motion control of robots, robotics, machine vision, and automated inspection have moved rapidly in the last 3-5 years. Artificial intelligence (AI) has advanced to the stage where the variability of input data is no longer a problem because of its capability to mimic the decision-making and problem-solving capabilities of men. This advancement has resulted in the designing of a more robust automated process. These systems are designed to be agile and adaptive to changes in incoming materials, design changes, variations in manufacturing conditions, and changes in processes and layouts. Connected devices and the Internet of Things (IoT) allow different devices to communicate effectively to create a coherent, connected manufacturing assembly line and supply chain.
3. Automating Business Processes
The digital transformation of business applies not only to the manufacturing and operations world but also to the management and administrative side of an organization. Many world-leading manufacturers are using digital transformation to integrate their business processes so that customer orders flow through phases in a modern, seamless way. Examples are:
- Customer orders are received online or electronically.
- Automated systems then schedule production (including management of inventory levels and the ordering of materials if required).
- Production orders are tracked through production, inspection, and quality control, with digital records for each batch leaving an audit trail.
- Labeling, packaging, shipping, and fulfillment of orders are carried out automatically, with the products and quantities reconciled with the orders received.
- Customers can be sent tracking updates and invoices using integrated accounting software.
All of the items above can be completed using software that will optimize key business performance parameters without ever needing intervention from staff.
4. Office Work and Collaboration
Manufacturing and machine shops are similar to many other businesses in terms of having complex supply chains, needing to respond to changing industry trends, and tracking dozens or hundreds of internal projects. The use of data and data systems means that the office teams can be more effective. All of the data needed for knowledge workers to perform their jobs is available at their fingertips. Teams are better able to collaborate across functions when data on the status of projects, production, and other metrics are immediately available to team members. Management can make better decisions when the data reaching them is accurate, up-to-date, and unbiased.
What Are the Benefits of Digital Transformation
Organizations derive many benefits from starting the journey of digital transformation. Some are immediately obvious, while others emerge over time:
1. Improved Cost and Efficiency
One of the most obvious and immediate benefits of digital transformation to an organization is the improvement in efficiency. Streamlined automated processes eliminate the majority of waste in an organization. Examples include:
- Ineffective processes, with staff checking and rechecking orders and processes.
- Faster, more repeatable processes, with automated equipment reducing errors.
- Reduction in waste due to processes being monitored live for defects, materials, consumables, and yield issues before they become a problem.
2. Increased Agility
Businesses become more agile when they can take custom orders or short runs of products from customers without the set-up time of current rigid manufacturing systems. Personalization, rapid prototyping, and agile design changes for specific regions or markets create strong brand satisfaction and repeat business. The ability to personalize product designs is becoming an expectation in the world of high-tech niche manufacturing.
3. Less Waste
From a sustainability perspective, adopting digital transformation reduces the overall waste within the supply change. Examples are:
- Ordering materials just in time.
- Creating “pull and flow” from customers.
- Minimizing work-in-progress.
Digital management of equipment and the ability to drive continuous improvement means that process yields rise, reducing the costs to the business and to the environment.
What Are the Key Challenges to Digital Transformation?
Transforming a business or organization in a significant fashion brings significant advantages, but can bring challenges too. Some of the key challenges are:
1. Changing Mindsets
Initially, for businesses, the biggest hurdle to overcome is the mindset shift needed to leave behind legacy systems and processes, potentially leaving behind some customers. Organizations must commit to adopting new ways of thinking, and build services and products to match. Many companies struggle to find the right starting point for digital transformation within their operations. It takes a strong vision and follow-up from top leadership to see the process through.
2. Initial Investment and Costs
Justifying the initial outlay of investment for digital transformation can be a stumbling block for many businesses. Creating business plans with clear returns on investment can be difficult when the future is so uncertain, and companies are reluctant to plan too far ahead. This may be overcome by demonstrating that the opportunity cost is much higher than the cost of modernizing and that companies must regenerate to compete with the inevitable disruptive technology changes ahead.
3. Lack of Standards and Best Practices
Currently, no organization has published a recognized and agreed-upon set of standards and practices for digital transformation that can be used as a blueprint for businesses wanting to make the leap. To make informed decisions, industries must clarify standards for dealing with fully digitized and automated systems. A lack of standards leaves businesses with ambiguous choices and they must then rely on the varied opinions of experts. Agreed-upon standards of industry best practice will also lead to reduced costs, as clarity on requirements will replace budget overruns.
Regulated industries must also adapt to the digitally transformed world. Regulators in life sciences, finance, and the automotive industry are struggling to keep up with the pace of technological change in the industries they are regulating. No longer can processes and designs be frozen when launched, and companies asked to justify each change or improvement. When autonomous systems use machine learning to constantly improve, the ways of the past no longer fit.
Adopting Digitalization
The digitization of many modern industries is progressing at a dizzying pace. The manufacturing industry is uniquely placed to capitalize on the convergence of automation, machine learning, big data, and integrated systems. This will lead to a reduction in lead times for customers and an overall reduction in waste and impact on the environment. Leaders within manufacturing must consider their vision for the future when choosing their next steps on this journey.
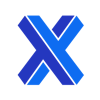