Magnesium Alloy Die Casting Services by Xometry
High Quality Magnesium Die Cast Metal Parts. Subject to availability. Xometry doesn't guarantee that we can provide this service at any given time.
What Is Magnesium Die Casting?
Magnesium die casting is the manufacturing process of injecting molten magnesium into a mold to create parts. The process is similar to casting processes, where the liquid material is poured into a cavity and takes on the shape of the desired product. The cavity itself is the negative shape of the intended product. In magnesium die-casting, magnesium alloys are melted either in a die-casting machine or in a separate furnace. The molten material is then poured and allowed to solidify in the mold (gravity-feed casting) or forced into the mold and held at high pressure by a hydraulic press (pressure die casting). When sufficient time has passed for the molten material to take on the shape of the intended product and solidify, the mold opens, and the part is removed, either automatically or manually.
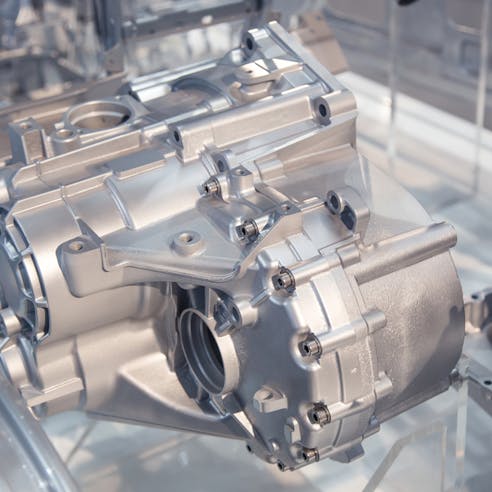
Types of Magnesium Die Casting
There are two main types of die casting: hot chamber and cold chamber. Magnesium alloys can be die cast using either process. The two methods are described in more detail below:
Hot Chamber Die Casting
Hot chamber die casting, also known as “gooseneck” or “hot” casting, is the more commonly used die casting method. In hot chamber die casting, one end of a gooseneck-shaped pathway is submerged in a closed bath of molten metal. To prevent freezing of the metal, the nozzle is heated to 400–500 °C with gas, electric, or by induction heating. When the die-casting process starts, a hydraulic piston forces the molten metal from the bath, through the gooseneck feed system, and into the cavity. Hot chamber die casting is primarily used with metals having low melting points such as zinc, tin, or lead (whose melting points are between 450°F and 787°F). However, magnesium, which has a melting point of around 1100°F, can also be used for hot chamber die casting.
Hot chamber die casting limits the molten material’s exposure to ambient air which helps to prevent oxide inclusions in the casting. This is because a cover gas, typically sulfur hexafluoride, is dispersed and protects the molten material.
Hot chamber magnesium die casting is great for producing large volumes of parts. This is because cycle times in hot chamber magnesium die casting are shorter compared to cold chamber die casting since the furnace and casting portion of the machine is integrated together. This prevents the need to transport molten material and superheat the material — two processes that are required in cold chamber casting and take additional time. However, hot chamber die casting produces parts that are more porous than cold chamber die casted parts since entrapped gases from the injection process are more likely to occur due to the high injection velocity. Additionally, hot chamber die casting is more expensive than cold chamber die casting since die casting machinery equipment is more likely to corrode due to continuous exposure to heightened temperatures. Consequently, maintenance is more costly in the long run.
Cold Chamber Die Casting
Cold chamber die casting, also known as cold casting, is the die-casting process that involves melting metal in a separate furnace and pouring the molten metal into an unheated chamber for injection into the mold under high pressure. It is best for metals with higher melting temperatures, like magnesium, aluminum, and copper. Like in hot chamber die casting, a cover gas is used to protect the molten magnesium and prevent oxides from forming in the casted part. Cold chamber die casting is the more cost-effective type of die casting since it requires less maintenance. However, cycle times with cold chamber die casting are longer, and product quality may be lower than that of hot chamber die casting. This is because the high pressure used in cold chamber casting can lead to an inability to vacate gases before the solidification process.
While magnesium alloys are suitable for both hot and cold chamber die casting due to the presence of alloying elements that can reduce the particular alloy’s melting temperature, cold casting is more commonly used in magnesium die casting due to the material’s high melting point. Die-casting machinery capable of melting metal in the same machine as the molding system, as is done in hot chamber die casting, is expensive. Many manufacturers opt to use the cold chamber process, in which the magnesium is melted in a separate furnace and transferred into the die-casting machine for molding.
Magnesium Alloy Properties
Magnesium Alloy | Density | Yield Strength | Elongation | Elastic Modulus | Melting Temperature |
---|---|---|---|---|---|
Magnesium Alloy AZ91D | Density 1.81 g/cm3 | Yield Strength 160 MPa | Elongation 3% | Elastic Modulus 45 GPa | Melting Temperature 875-1105 °F |
Magnesium Alloy AZ91HP | Density 1.81 g/cm3 | Yield Strength 160 MPa | Elongation 3% | Elastic Modulus 45 GPa | Melting Temperature 875-1105 °F |
Magnesium Alloy AM60B | Density 1.80 g/cm3 | Yield Strength 130 MPa | Elongation 8% | Elastic Modulus 45 GPa | Melting Temperature 1005-1140 °F |
Magnesium alloys have several desirable properties. Table 1 above shows some properties of magnesium alloys:
Advantages of Magnesium Die Casting
Magnesium die castings have numerous benefits. These advantages are listed below:
- Corrosion Resistance
- Light Weight
- Recyclable
- High Strength-to-Weight Ratio
- Abundant Material Supply
- Good Stiffness-to-Weight Ratio
- Heat Resistant Steel
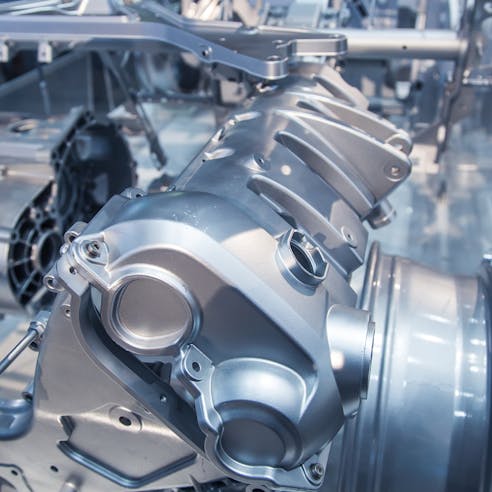
Corrosion Resistance
Magnesium alloy die-cast parts, like parts made from AZ91HP, are naturally corrosion-resistant in dry environments due to the oxide layer that forms on their surface. The oxide layer forms because magnesium readily reacts with oxygen in the atmosphere. However, magnesium is notorious for being susceptible to galvanic corrosion. Regardless, its natural corrosion resistance makes the material suitable for use in dry and corrosive environments such as in the automotive, electronics, and sporting goods industries.
Light Weight
Lightweight die-cast parts are another advantage of magnesium. Magnesium alloys have a density of about 1.8 g/cm3, making them one of the lightest metals suitable for structural applications. Compared to other light metals like aluminum, which has a density of 2.7 g/cm3, and titanium which has a density of 4.5 g/cm3, magnesium has a significant weight advantage. Its low density makes it a good choice for applications where weight is critical, especially in the aerospace industry.
Recyclable
Magnesium is easily recyclable, although magnesium dust can be an irritant to those that inhale it. Regardless, its eco-friendliness makes magnesium a great material choice for reducing human impact on the environment and for manufacturers looking to make their processes more environmentally friendly.
High Strength-to-Weight Ratio
Magnesium die-cast parts have a high strength-to-weight ratio. They are great for applications where weight reduction and strength are highly important, such as in the automotive or bicycle industry. The yield strength of magnesium alloys generally lies between 21-460 MPa. Depending on the particular alloy, magnesium alloy has similar strength as aluminum alloys, another popular metal with a high strength-to-weight ratio.
Abundant Material Supply
Magnesium is the 5th most abundant metal on Earth after aluminum, iron, calcium, and sodium. Its abundance, coupled with its popularity for non-ferrous casting processes, means it is both readily available.
Good Stiffness-to-Weight Ratio
Another advantage of magnesium is its high stiffness-to-weight ratio. A material’s stiffness-to-weight ratio also called its specific stiffness, is defined as the ratio of a material’s elastic modulus to its density. Magnesium’s high stiffness-to-weight ratio means stiffness values similar to aluminum or steel can be achieved with far less material weight. Its good stiffness-to-weight ratio means magnesium alloys are resistant to elastic deformation, making it great for applications where minimal deflection is required.
Heat Resistant Steel
In contrast with aluminum which reacts with steel, magnesium can be melted in heat-resistant steel crucibles. Moreover, the heat resistance of magnesium alloys, specifically its high thermal conductivity (~150 W/mK), makes it great for dissipating heat. This makes this metal great for parts that are subjected to high temperatures (150-200 °C) such as components in the automotive or electronics industries.
Ready to get started on your Magnesium Die Casting quote?
Disadvantages of Magnesium Die Casting
Magnesium die casting also has some disadvantages. These include:
- Stability
- Post-Production Processing
- Production Costs
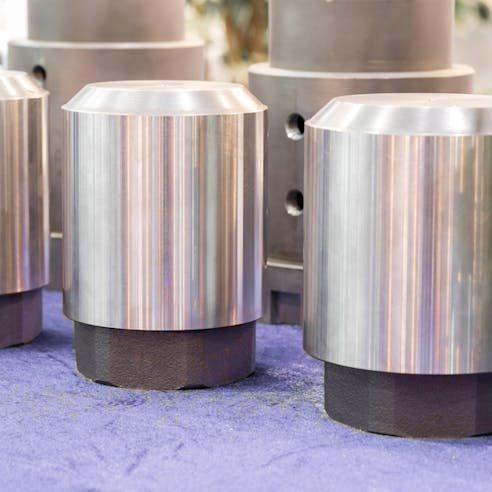
Stability
Magnesium die cast parts are less stable than similar casted parts made from aluminum. While magnesium has a high strength-to-weight ratio and stiffness-to-weight ratio, a force applied to magnesium parts may cause the parts to bend. However, the same behavior may not be observed if the same force is applied to aluminum cast parts.
Post-Production Processing
Post-processing is often required to obtain desired dimensions and part appearance. Post-processing includes trimming the sprue and possibly trimming flashing around the part, surface treatment like sandblasting or powder coating, plating, heat treatment, and more.
Production Costs
The machinery required for magnesium die casting can be expensive. Die-casting machines can easily cost $30,000 to over $1,000,000. The high cost of such equipment is precisely why many companies outsource their die-casting manufacturing operations to industry experts like Xometry. Additionally, the cost of producing magnesium alloys is higher than that for other lightweight metals commonly used for die casting, such as zinc or copper due to costs associated with refining pure magnesium and producing magnesium alloys.
Applications of Magnesium Die Casting
Magnesium die castings are an attractive option for making any type of product where minimizing weight is an important consideration. Listed below are some of the magnesium alloy die castings applications:
- Automotive Parts
- Bicycle Frames
- Sports Equipment
- Consumer Electronics
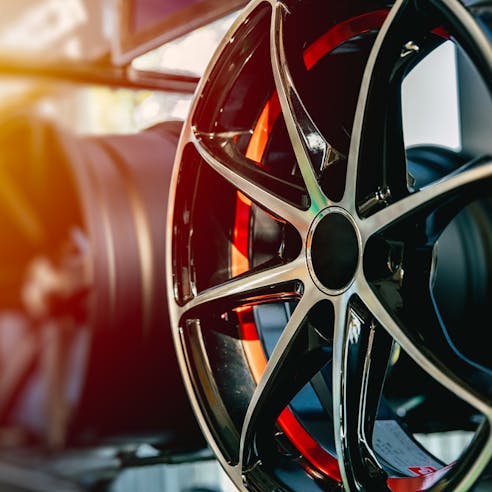
Automotive Parts
Magnesium die casting is often employed in the production of automotive parts such as: car wheels, gearboxes, steering columns, seat frames, fuel tank covers, and more. Magnesium’s light weight, high strength-to-weight ratio, and vibration-damping properties, coupled with its heat resistance up to 200 °C make it an excellent option for automotive parts. AZ91D is the magnesium alloy most commonly used for automotive die casting.
Bicycle Frames
Another common application of magnesium die-casting is high-performance, lightweight bicycle frames. The lightweight components made possible by using magnesium-based alloys lead to improved mobility and maneuverability of bicycles, especially racing bicycles, while their vibration-damping capacity allows for great shock absorption.
Sports Equipment
Sports equipment such as golf clubs, tennis rackets, and archery bows can be made from die-cast magnesium. Magnesium alloys are a great option for these products because their light weight and strength allow for increased mobility for people at the top of their sports, increased accessibility for people who cannot manage heavier equipment, and ease of use while still being able to maintain its intended function.
Consumer Electronics
Magnesium die casting is also used to make components for consumer electronics. It is used to make parts such as enclosures and housings for cameras and telecommunication equipment. Additionally, it can be used for housing components in TVs, mobile phones, and computers due to its heat resistance and dissipation properties.
Alternatives to Magnesium Die Casting
Xometry offers a few alternatives to magnesium die casting. These alternatives are listed and described below:
- Aluminum Die Casting
- Zinc Die Casting
- Injection Molding
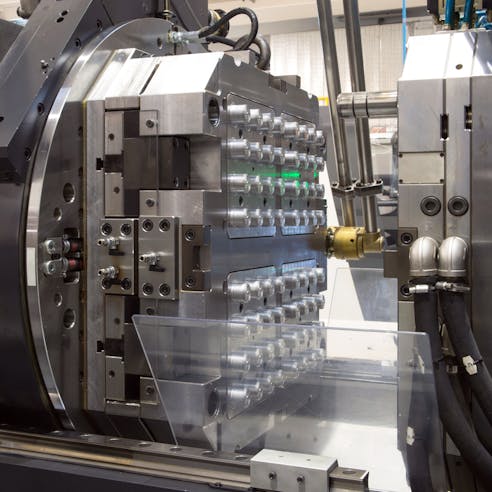
- Aluminum Die Casting: Like magnesium, aluminum is a low-density metal (but denser than magnesium). It is naturally corrosion-resistant and has a high strength-to-weight ratio. Aluminum is abundant, durable, and able to be in high-temperature environments, making it a great alternative to magnesium die-cast parts.
- Zinc Die Casting: Zinc is considered the easiest metal to die cast. Its low melting point (~420°C) and casting fluidity, coupled with its strength and stiffness make it a popular choice for many die-casting applications. Zinc die casting can be used to make large volumes of the same types of parts as magnesium die casting, but the parts will be heavier since zinc (7.14 g/cm3) is more dense than magnesium.
- Injection Molding: Injection molding is a process similar to magnesium die-casting processes except that in injection molding, thermoplastics are used for molding rather than molten metal. As in die casting, the material is melted, forced into a mold, and held under pressure until the product is formed. After the product has cooled sufficiently, it is ejected from the mold. Parts made by injection molding can satisfy extremely tight tolerances (+0.004”). As with die casting, it is a great way to make large volumes of parts in a short time.
Why Choose Xometry for Online Magnesium Die Casting Services?
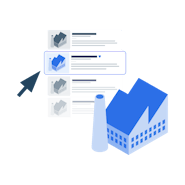
Endless Options
Choose from millions of possible combinations of materials, finishes, tolerances, markings, and certifications for your order.
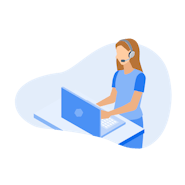
Easy to Use
Get started with our easy-to-use platform and let our experts take care of managing the project from locating the right manufacturing partner to delivery logistics.
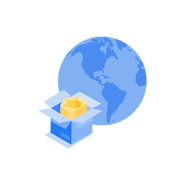
Vetted Network
We are ISO 9001:2015, ISO 13485, and AS9100D certified. Only the top shops that apply to become Suppliers make it through our qualification process.