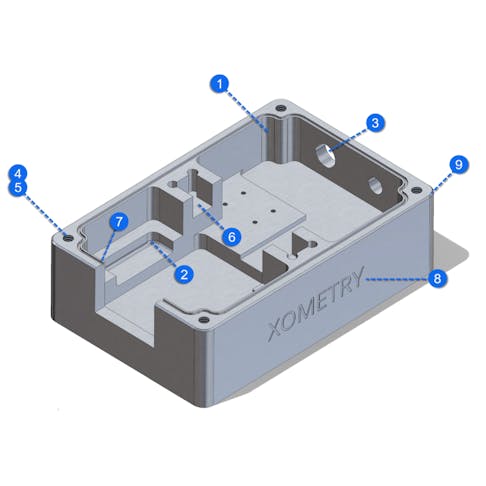
Webinar Recording - Trimming Costs, Keeping Quality: Smart Design Tips for CNC Machining
Listen in and discover how to design cost-effective CNC machined parts without compromising quality.
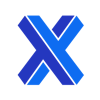
Unpack actionable strategies and best practices for CNC machining by listening to this insightful webinar.
Hosted by Xometry’s Greg Paulsen, Director of Applications Engineering, and Steve Zimmerman, Machinist, Toolmaker, and Senior Partner Support Lead, this session explored the elements that play a pivotal role in cost-effective CNC projects, such as material selection, feature complexity, and design guidelines. If you’re a designer or engineer seeking to improve design efficiency and leverage the full potential of CNC machining, this webinar recording was made for you.
Key Takeaways:
- Understand Cost Drivers: Learn the key elements that drive costs in CNC machining and how to implement them in your design process.
- Learn Efficient Design Techniques: Gain insights into Designing for Manufacturability (DFM), including material selection, feature-specific tips, and an understanding of 3-, 4-, and 5-axis features.
- Gain Technical Drawing Mastery: Learn key fundamentals to create concise, effective technical drawings.
Yes, here is a PDF version of the webinar, and we have linked useful resources within! "Trimming Costs, Keeping Quality: Smart Design Tips for CNC Machining."
Check out our CNC capabilities page for quick tips or you can download our CNC design guide PDF.
Please upload your model and configure the quote via our Xometry Instant Quoting Engine®. If your thread is not one of our standard threads, you can get a team to review it manually by contacting support@xometry.com or your sales lead. You may also be able to trigger a manual quote review by selecting "Other/Custom" under Finishes and writing in your needs.
Just because we can't machine sharp corners doesn't mean there aren't methods to fit sharp features together. I love seeing circular relief cuts in the corners of a square pocket. You can do the same thing for hex sockets and keyed features. They follow DFM best practices and ensure mating parts fit appropriately. Our CNC design reference poster shows that off well.
You will need to design in the radius appropriately for any sharp internal corners.
We can hit any standard machining practice; not all of them may autoquote. If you do not see the option you are looking for, we would request that you choose Other/Custom in your Finish tab and add the requirements for your examples. You also need to upload a technical drawing outlining the requirements for this.
You tell me! 2024 aluminum machined parts instantly quote at Xometry, and you can upload your file or take a Test Drive to see how it compares to commodity 6061 aluminum. You'll see that alloy prices are somewhere between 6061 and 7050 alloys.
This is where GD&T plays a huge role. Well-toleranced GD&T drawings can ensure you have location and fits between components even if they are manufactured at different locations. That, along with limit tolerances (e.g., +.000" / -.010"), can also ensure mating parts will have clearances.
Chamfers are easier to machine and lower cost, often producible in one machining pass vs several passes or surfacing for external radii.
Design in chamfers that hold a cosmetic purpose to your part. You do not need to model any edge breaks, Xometry will deburr every machined part you produce. If you prefer a machined edge break, make sure to call that out in a technical drawing.
Xometry uses AI and machine learning to build predictive pricing models for our instant quoting. This does not discretely break down machine or operations, but instead answers how a part like this prices on a competitive marketplace.
Hide the thread! We need a hole modeled to the correct drill size (or with enough material to cut on external threads). An accompanying technical print with the thread call out will be our guide for thread type, depth, and inspection requirements.
Taps are cheaper because they do not require extra setups and labor. Typically the use of a threaded insert, such as a helical insert or key set insert, is when you know in the use of the part the thread may wear out or need repair (e.g., the part will feel high shock and vibe). We also see threaded inserts on softer parts, like aluminum or even plastic, adding strength to the assembled components and preventing stripping.
At a minimum, the thread form, series, major diameter, threads per inch, class of fit, and depth should be specified. Thread depth is often symbolized with a ↧. E.g., 5/16-18 UNC - 2B ↧ .750" would indicate a thread depth of .75 inches.
Yes! We pair repeat work with suppliers to assure quality. Every uploaded part at Xometry gets its own unique Xometry part ID. Upon reorder, the previous manufacturer will get an exclusive offer for this part - a win-win. Pricing may not be affected from the first to the next order.
You can use any of Xometry's quoting tools to get pricing and lead times; they are free and do not require and order. Of course, when you're ready to move forward, we hope you choose Xometry!
That would be on the maximum end of our design recommendations: Length < 2x thread diameter. Be sue to add additional hole depth of at least 50% the hole diameter beyond your thread diameter.
Holes are holes and we do not have any constraints between units of measurements.
Absolutely. You can add "Limited dimensioned drawing, all non-dimensioned features are CAD-defined." to your drawing notes. At that point, we will follow our Manufacturing Standards for best practices. If you require a dimensional report of a complex curvature, you may need to do the GD&T call out for surface profile. This will require a CMM and extra costs to measure.
Xometry's CNC machining services assume we are milling all faces of the part. If you have a request to use a standard stock size and keep the top/bottom faces as-is we would need to manually review with our internal team to provide an accurate quote.
The finishing passes are dependent on the provided part geometry and strategy used by the Xometry Supplier on your specific project. We typically do not call this out up-front. Sometimes a surface roughness request may dictate the need for a specific pass.
125 Ra µin (or RMS) is a surface roughness measurement that dictates the average surface's deviation over a prescribed measurement length. 125 is typically the "as machined" look with standard toolpaths; we recommend 32 Ra µin for spots requiring seals or gaskets. Below 32 Ra µin will likely need manual polishing or grinding.
Mostly yes, however features that require splines, EDM requirements, porting holes, slitting saws, ACME threads, etc. will need a team review before finalizing the quote. Contact our support team or your sales lead for quick assistance!
Our capabilities are based on our broad network of thousands of suppliers and our costing model reflects these capabilities. We certainly have access to multi-axis machining, but the more demanding the design is the higher the price will be due to market factors like count of available shops and specialized overhead. Long story short: Xometry can make practically any machinable design, but designs that inherently add more constraints to how they can be made or sources will drive pricing.
We'll cut it all! We are agnostic of measurements and deal in both units all the time.
Usually a 4th axis requirement (for CNC) is dictated when there are non-planar holes across a single rotating axis compared a direct-on approach. In other words, if I can do most features from top down, but need to tilt the part in segments that are not 90 degrees, a 4th axis would be helpful. If I need to tilt, and rotate in angular segments, there is a benefit for a 5-axis CNC.
Note that a CNC lathe could be a great option to design around if you have several axial features on your part (e.g., a flanged circular housing). In this case, a CNC lathe is a 4-axis device but makes material removal very quick through turning then hits the details with milling.
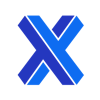