
Ceramic Coating: Purpose, How It Works, Benefits, and Downsides
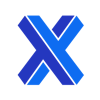
Ceramic coatings are coatings made of ceramic material, which are used to coat metals to improve their physical properties. Ceramic coatings are widely used as a protective layer to improve corrosion and chemical resistance, add thermal and electrical insulation, reduce friction, and increase surface hardness and wear resistance.
This article will discuss ceramic coatings, how they work, their applications, and the benefits and downsides of using them.
What Is Ceramic Coating?
Ceramic coating refers to coating materials with any of several ceramic compounds, to improve certain physical properties of the materials. Ceramic coatings add electrical and thermal insulation to materials, reduce friction, and improve corrosion and chemical resistance. It is commonly used to protect the exteriors of cars, as a coating for non-stick cookware, and as an electrical and thermal insulator for components and equipment in industrial applications.
What Is the Other Term for Ceramic Coating?
Other terms for ceramic coating include: nano coatings, hydrophobic coatings, silica coatings, glass coating, and quartz coating. These terms mostly come from the automotive ceramic coating industry and are generally used interchangeably.
What Does Ceramic Coating Do?
Ceramic coating creates a thin protective layer of ceramic material on a component or product. This layer adds several properties to the product, such as: electrical insulation, protection against corrosion, protection against the elements, surface hardness, and reduction of friction. The variety of properties that ceramic coating can add makes it a popular process for a range of applications.
How Does Ceramic Coating Work?
In a nutshell, ceramic coating works by applying a coating compound onto a substrate, whereby the compound binds to the substrate, and hardens into a thin, hard, hydrophobic layer on top of the material. The application methods can vary widely, with two common methods being as follows:
- Thermal Spray: Refers to several methods in which the coating compound is heated by some means, and then propelled onto the substrate at high speed, where it cools off rapidly to form the ceramic coating. Examples of thermal spray methods include the detonation gun method and plasma spraying.
- Resin: This application method is specific to ceramic coatings for cars. Here, the ceramic coating comes in a liquid form which contains the resin and additives. The resin contains the polymer that ultimately provides the desired physical properties. The additives help to provide extra adhesion. When the coating is applied onto the surface of a car, it forms a bond over the painted surface, resulting in the protective ceramic coating after it has cured.
What Is the Composition of Ceramic Coating?
The typical composition of ceramic coating is silicon dioxide (SiO2). Other compositions that are commonly used include titanium dioxide (TiO2), Al2O3, and ZrO2. For industrial ceramic coating applications, these coatings usually come in powdered form. The powder is heated until soft and propelled at high speeds onto a material, where it rapidly cools and bonds to the material to form a hard protective layer.
For ceramic coatings used on cars, the coating may come in liquid form. In these types of coatings, the liquid coating contains the ceramic coating resin itself, as well as additives that improve the adhesion of the coating to a car’s surface.
Does Ceramic Coating Contain PTFE?
No, ceramic coatings do not contain PTFE. PTFE, also known as polytetrafluoroethylene, is a hydrophobic composition used to reduce friction on materials. It is commonly used as a non-stick coating for cookware or as a lubricant in manufacturing or components. There are many different compositions of ceramic coatings, but none of them contain PTFE; they rely on other materials for their friction-reducing properties.
Where Is Ceramic Coating Used?
Ceramic coatings are used in many different industries to take advantage of specific properties that ceramic coatings impart onto components. One of the most common applications is ceramic coating for cars. This involves treating a car with a liquid ceramic coating which cures into a hard protective layer. The ceramic coating provides paint protection, prevents dirt adhesion to a degree, and offers a cost-effective way of protecting a car.
Ceramic coating is also used in non-stick cookware, offering an alternative to compounds such as Teflon®. In this case, the coating is used to prevent food from sticking to cookware. Other uses of ceramic coating include: as a means of corrosion protection for pipelines and equipment, to reduce friction between mechanical components, and to add electrical insulation to components in electrical, industrial, and automotive applications.
How Is Ceramic Coating Used in Manufacturing Industries?
Ceramic coating offers many desirable properties that are useful in manufacturing. One of the main ways ceramic coatings are used is to reduce friction between mechanical parts. This reduces wear, increasing the life span of components, as well as reducing maintenance requirements.
Other ways that ceramic coatings are used include adding corrosion and chemical resistance, as well as thermal insulation. These also increase the longevity of components and are especially useful for harsh applications.
What Effect Does Ceramic Coating Have When Applied to Aluminum Alloys?
Ceramic coating improves the surface hardness and wear resistance of aluminum alloys. Aluminum alloys are prone to surface wear due to the brittleness of their surface. This can lessen the life span of aluminum alloys, making them unsuitable or undesirable for certain applications. By applying a ceramic coating to aluminum alloys, their surface hardness is increased, improving wear resistance and increasing their life span.
To learn more, see our Aluminum Alloy guide.
Can Ceramic Coating Be Used on Kitchenware?
Yes, ceramic coating is commonly used on non-stick kitchenware. Ceramic coatings add lubricity to cookware, preventing food from sticking to it. This by itself makes ceramic coatings very useful for kitchenware. Additionally, ceramic coatings are non-toxic, especially compared to traditional non-stick compounds such as PTFE.
How To Apply Ceramic Coating?
Ceramic coatings can be applied in several ways, depending on the application. The following list summarizes some of the application methods:
- Ceramic Coating a Car: The ceramic coating for cars comes in liquid form, which is applied to the painted surface of a car in straight-line motions. After application, the excess must be wiped off with minimal pressure, and the car should be left to cure for at least two days before being allowed to get wet. The car must first be thoroughly cleaned and detailed to prevent any dirt or debris from being sealed underneath the coating.
- Plasma Spraying: Plasma spraying is a process of applying coatings to components by using a plasma flame to heat particles to extremely high temperatures. These heated particles are then sprayed onto a material, where they cool off rapidly to form a coating.
- Detonation Gun (D-Gun): The D-Gun method is one of the most popular thermal spray processes for applying coatings to materials. It works by heating and spraying powder onto a material via a detonation of oxygen and fuel. After detonation, an inert gas is pulsed through the barrel of the sprayer to purge it. This cycle of detonation and purging is repeated rapidly and allows for a very strong and dense coating.
- Chemical Vapor Deposition (CVD): CVD is a process of applying coatings, including ceramic coatings. It involves supplying reactive gases to form a chemical reaction with the substrate of the material to be coated. This chemical reaction then forms a film over the material, which results in a very thin coating.
How Long Does Ceramic Coating Last?
Ceramic coatings last a long time, in the order of years. However, the exact life span will depend on the application, type of ceramic coating, and other factors over the life span of the coating. The average life span of ceramic coatings on cars is two to five years. This can be reduced by the use of harsh chemicals, extreme weather conditions, and incorrect maintenance, such as polishing the coating. For ceramic-coated cookware, one to three years is realistic, depending on how well the cookware is maintained. For industrial applications, the answer is a bit more vague, as many factors can affect the life span. Exposure to chemicals, high temperatures, or mechanical impacts can all reduce the longevity of the coating. However, the life span of these ceramic coatings is also generally measured in years.
What To Do To Maintain Ceramic Coating?
To maintain a ceramic coating, care should be taken to do the following:
- Avoid using harsh chemicals on the ceramic coating, as this can deteriorate the coating.
- Avoid using sharp implements or abrasives on the coating, as this can lead to scratches.
- Avoid polishing or other abrasive methods of cleaning, as this can scratch and deteriorate the coating.
- For a ceramic coating on a car, surface debris should be cleaned off every few weeks.
- Ceramic-coated cookware should be washed with warm, mild soapy water after each use.
Is Ceramic Coating High Maintenance?
No, ceramic coating is not high maintenance, but care should be taken to use the correct maintenance techniques. Certain maintenance techniques, such as the use of harsh chemicals, high-speed polishers, or hard implements, can wear out the ceramic coating or cause scratches, which can lead to deterioration of the coating and its properties.
What To Avoid After Ceramic Coating?
After ceramic coating a car, the coating should be left to cure before getting the car wet. This takes about two days, although the coating will continue to cure over several days. The car should not be washed for two weeks, and exposure to water and rain should be limited as much as possible. Lastly, avoid any debris, such as tree sap, bird droppings, or bug splatter, removing these contaminants as soon as possible.
How Much Does Ceramic Coating Cost?
The cost of ceramic coatings depends on many factors, such as: the application, type of ceramic coating, application method, size of product to be coated, and geographical location. Ceramic coating a car professionally can cost up to $5,000, while doing it yourself can cost under $100 depending on the supplies and materials used.
For industrial ceramic coatings, the costs can vary significantly depending on the method of application, the product to be coated, and the composition of the coating.
Is Ceramic Coating Expensive?
Industrial ceramic coatings can be an expensive process. This is largely due to the complexity of applying ceramic coatings correctly, as well as the cost of the coating compounds themselves. However, the unique benefits that ceramic coatings give can offset these costs and can prove to be quite cost-effective compared to replacing a component with a different material for example.
What Are the Benefits of Ceramic Coating?
Ceramic coatings provide several benefits, such as:
- Improves surface hardness, which reduces wear and increases the longevity of certain materials.
- Reduces friction, which is useful for non-stick cookware, as well as reducing wear on mechanical parts.
- Thermal insulation — protects components when used in high-temperature applications.
- Electrical insulation, provides insulation for tools and equipment in the electrical industry, as well as components in the automotive and industrial industries.
- Corrosion and chemical resistance, which is useful for protecting components and materials in a wide range of industries.
What Are the Downsides of Ceramic Coating?
Ceramic coating does have a few downsides:
- It is fairly complex to apply correctly and requires professional application for the most part.
- Ceramic coatings form a semi-permanent bond with the substrate of the material it is applied to, which makes it irreversible except via abrasive methods, which could lead to damage to the underlying material.
- Tend to be fairly expensive due to the complexity and composition of the coating.
Is It Okay To Wax Over Ceramic Coating?
Yes, it is okay to wax over a ceramic coating on a car. Waxing a car can add to the aesthetics of the finish. However, a ceramic coating should never be polished, as this is a sure way to deteriorate the coating.
Is It a Good Idea To Pressure Wash a Ceramic-Coated Car?
Yes, a ceramic-coated car can be pressure washed without any concerns for damaging the ceramic coating, as long as the coating has been fully cured. The curing process can take two weeks to complete, during which a car should not be washed at all.
What Is the Difference Between Ceramic Coating and Teflon Coating?
Ceramic coating is a coating that consists of a ceramic compound such as SiO2 or TiO2. Teflon® coating is a PTFE coating that is commonly applied to non-stick cookware. Both ceramic coatings and Teflon® coatings are used to apply non-stick properties to cookware, however, Teflon® generally lasts longer than ceramic coatings and performs better at preventing food adhesion. However, Teflon® consists of PTFE, which can potentially release harmful fumes. Ceramic coatings are non-toxic and are generally marketed as the safer option despite being more expensive and not lasting as long.
Summary
This article presented ceramic coating, explained it, and discussed how it works and its benefits. To learn more about ceramic coating, contact a Xometry representative.
Xometry provides a wide range of manufacturing capabilities, including machining and other value-added services for all of your prototyping and production needs. Visit our website to learn more or to request a free, no-obligation quote.
Copyright and Trademark Notice
- Teflon® is a registered trademark owned by Chemours (formally DuPont)
Disclaimer
The content appearing on this webpage is for informational purposes only. Xometry makes no representation or warranty of any kind, be it expressed or implied, as to the accuracy, completeness, or validity of the information. Any performance parameters, geometric tolerances, specific design features, quality and types of materials, or processes should not be inferred to represent what will be delivered by third-party suppliers or manufacturers through Xometry’s network. Buyers seeking quotes for parts are responsible for defining the specific requirements for those parts. Please refer to our terms and conditions for more information.
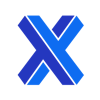