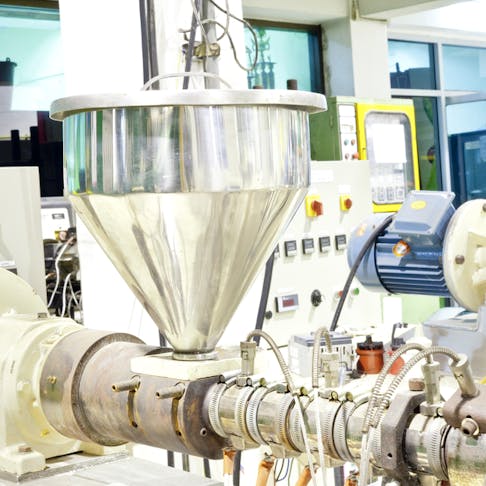
Extrusion Molding: Definition, How It Works, Applications, and Advantages
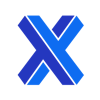
Extrusion molding is a very popular molding technique that is used to create a continuous profile of a desired shape. This method is commonly used to shape plastics into tubes, pipes, films, etc. It can also be used as a metal-forming technique.
This article takes a closer look at extrusion molding: defining the process, how it works, its applications, advantages and disadvantages, and so much more.
What Is Extrusion Molding?
Extrusion molding is a high-volume manufacturing process used to create objects with a fixed cross-sectional profile. It is a molding process that involves forcing a material, typically a thermoplastic or elastomer, through a shaped opening or die to produce a continuous length of the desired shape, which is typically tube- or rod-like. The material is heated until it becomes pliable or molten, and then it is forced through the die to create the desired cross-sectional profile. Besides using this method to shape plastic, it is also used on metals.
What Is the Other Term for Extrusion Molding?
Extrusion molding is also sometimes referred to as plastification extruding. Another name for extrusion molding is simply “extrusion.” The process is often referred to as extrusion when discussing the manufacturing of continuous lengths of products with a consistent cross-sectional profile, such as: tubes, pipes, or various profiles.
What Is the Importance of Extrusion Molding in Manufacturing?
The importance of extrusion molding as a process lies in its ability to produce continuous lengths of plastic with consistent cross-section profiles at a low cost. This process is particularly crucial for the cost-effective production of items such as: pipes, tubes, seals, and various profiles. Its continuous nature allows for high-volume production and seamless integration into various industries. Additionally, extrusion molding plays a key role in plastic recycling initiatives, contributing to sustainability by enabling the reuse of cleaned and sorted plastic waste.
How Does Extrusion Molding Work?
The plastic extrusion process can be divided into four main steps:
- Adding Additives: The base material is mixed with different additives like: colorants, stabilizers (for oxidative stability, heat, UV stability, etc.), fillers, flame retardants, reinforcements, lubricants, etc., which are chosen based on the specific requirements of the end product.
- Melting the Material: Plastic materials are fed into the hopper and directed through the feed-throat to the barrel. The material descends into the annular space between the screw and the barrel, confined by the screw channel. As the screw turns, it propels the polymer forward, subjecting it to frictional forces. The barrels undergo gradual heating with a temperature profile that increases steadily. Progressing from the feed zone to the metering zone, the combined effects of frictional forces and barrel heating induce plasticization, homogenization, and kneading of the material, preparing it for the subsequent stages of the plastic extrusion process.
- Shaping: Upon leaving the barrel, the molten material, driven by the rotating screw, passes through screens at the barrel's end. These screens serve a dual purpose: they eliminate foreign bodies and contaminants from the molten plastic while maintaining a uniform pressure throughout the system. The increased temperature and malleability achieved through this process prepare the material for the next crucial step—forming the desired shape by pushing it through a die. The shape of the die dictates the ultimate form of the extruded plastic product.
- Cooling: Following the shaping of the molten plastic through the die, the next phase is cooling. This can be achieved through several cooling rolls or a water shower. The cooling process is vital to ensuring that the extruded plastic profile retains its intended shape.
After the extruded product has been cooled it may undergo extra processes, such as: further flame treatment, cutting, printing, annealing, deodorization, etc. The extrudate will then be subject to inspections to ensure that the product meets the desired quality.
What Is the Machine Used for Extrusion Molding?
An extruder is used for extrusion molding. It uses a system of cylinders and barrels, heats the raw material, and propels it through the mold/die to create the desired profile. Different types of extruders can be used, including: single- and multiple-screw extruders, single- and multiple-ram extruders, disk extruders, drum extruders, diskpack extruders, and elastic melt extruders.
How Long Does the Extrusion Molding Process Last?
The time of a plastic extrusion process is influenced by factors such as: product complexity, plastic type, extrusion line speed, and manufacturer specifications. Generally, plastic extrusion is recognized for its efficiency in rapidly producing high volumes of continuous products. Simple items like pipes or profiles with basic shapes can be extruded quickly. In contrast, more complex products involving complex profiles, multiple layers, or post-extrusion modifications might take a little longer.
Is Extrusion Molding Continuous?
Yes, extrusion molding is a continuous production process that is especially useful in creating products like: drinking straws, pipes, hoses, or rods.
What Are the Common Materials Used in Extrusion Molding?
There are quite a few plastics that can be extrusion molded. Some of the common types of plastics include:
1. Polypropylene (PP)
Polypropylene is a ubiquitous plastic that is widely used in the plastic industry in processes like extrusion molding and injection molding. This plastic is inexpensive and easily accessible. It has a semi-crystalline property that imparts high flexural strength. PP is also resistant to moisture and chemical agents and has similar properties to polyethylene, but it is slightly harder and a little more heat resistant compared to polyethylene. Polypropylene strikes a balance between impact resistance, strength, color variety, and low-temperature performance. It is commonly found in: tubes, interior trim, metal replacement, living hinges, and more. It is often reinforced with either glass or carbon to increase its heat deflection temperature and tensile strength.
To learn more, see our guide on Polypropylene Plastic.
2. Nylon
Nylon, also known as polyamide (PA), is a translucent material with a fair amount of chemical resistance, and it performs well in high-temperature environments. This thermoplastic also has a high strength-to-weight ratio, excellent durability, and good electrical resistance. Nylon can be filled with up to 50% carbon fiber or glass to improve both operating temperatures and mechanical properties. Some of its common applications include reservoirs and tubes in automotive engines.
To learn more, see our guide on Nylon Plastic.
3. Acrylic
Acrylic is a relatively low-cost resin renowned for its clarity and light transmission. Extruded acrylic is thermoformable, displaying higher impact resistance than glass. It features good UV resistance, electrical resistivity, and excellent optical properties. In comparison to cast acrylic, extruded acrylic is more cost-effective, dimensionally stable, softer, easier to cut and polish, and has relatively high durability.
To learn more, see our guide on What is Acrylic.
4. Polyethylene (PE)
Polyethylene is a thermoplastic recognized for its flexibility, resilience, and resistance to chemicals. It offers a favorable combination of colorability, strength, and performance at low temperatures. It also has good impact strength and good chemical resistance. However, this plastic has poor heat stability, poor weatherability, and poor dimensional stability. Common applications of polyethylene include its use in: packaging films, pipes, containers, and various other products.
5. Polystyrene
Extruded polystyrene (XPS), which is denser than expanded polystyrene (EPS), is widely used in construction. XPS offers excellent insulation, contributing to energy efficiency in buildings. Its light weight, easy installation, and decorative applications make it favored in the construction industry. XPS is commonly utilized for long-term insulation in various building elements, reducing energy waste and fostering greener construction practices. Additionally, flame retardants are often added for enhanced safety against fire hazards.
To learn more, see our guide on Polystyrene.
6. Polycarbonate (PC)
Polycarbonate, a transparent thermoplastic, is recognized for its impact resistance and optical clarity. This plastic offers a set of characteristics, including: rigidity, resistance to abrasion, color adaptability, and stable performance in diverse temperature ranges. It is commonly used in automotive components and electronic enclosures.
To learn more, see our guide on Polycarbonate.
7. Acrylonitrile Butadiene Styrene (ABS)
ABS, or acrylonitrile butadiene styrene, is a relatively hard plastic that is created through the polymerization of styrene and acrylonitrile in the presence of polybutadiene. This creates a tougher material when compared to just pure polystyrene. The styrene element contributes to ABS's waterproof surface and glossy appearance. Meanwhile, the presence of polybutadiene enhances its toughness, ensuring resilience regardless of temperature variations. ABS is also especially known for its good abrasion resistance. Common applications of ABS include: electrical pipes, appliance cases, pipes, wire protection, and automotive trim. Take note that ABS is not as chemically resistant as PP and PE, so it’s best to be cautious in environments in which this plastic might come into contact with chemicals.
What Is Extrusion Molding Used For?
Extrusion molding is used to shape plastic materials into a predetermined form. It can also be used to shape metals.
What Are Examples of Extrusion Molding Products?
Extrusion products can be found in a wide range of industries. Some examples of these products include:
- Sheets and Cast Films: Plastic sheets are used in construction for: glazing on doors and windows, bulletproof sheets, and protective covers. Additionally, sheets serve as sound barriers, refrigerator liners, and decorative panels. Cast films are applied in: food wrapping, agricultural weed control, and protective packaging during shipments.
- Extrusion Coating and Lamination: Extrusion coating enhances product quality by applying a polymer layer to substrates like: paper, metal foils, and plastics. This process finds applications in: dairy packaging, juice cartons, carpet coating, frozen food containers, and heat-seal layers for general packaging.
- Wire and Cable Coating: Plastic extrusion coats wires and cables for insulation and protection. Common materials include: polyethylene, polyvinyl chloride, polyamide, and thermoplastic elastomers.
- Pipe and Tubing: Plastic extrusion is widely used in manufacturing pipes and tubing for applications ranging from water or sewage pipes to medical tubing. Materials like polyethylene, rigid polyvinyl chloride, and nylon are commonly employed for pipes, while thermoplastic resins are used for tubing, with options for both flexible and rigid forms.
What Are the Common Problems of Extrusion Molding Products?
Common problems in extrusion molding products can be categorized into 12 distinct defects, each of these are discussed below accompanied by troubleshooting recommendations:
- Interrupted Melt Output: Commonly caused by unbalanced barrel temperatures, interrupted melt output can be addressed by reducing the feed-zone temperature to ensure proper material transition. Additionally, it is essential to check the temperature resistance and cooling system. Regular inspection of the screen is crucial to capture any degraded or burned particles that might affect the extrusion process.
- Surging: Surging issues, attributed to contaminated material, incorrect temperature settings, or an unbalanced die exit, can be mitigated by gradually increasing barrel temperatures for each zone. What can also help is regularly checking and cleaning the screen, inspecting for blockages in the hopper, reviewing the screw configuration, and ensuring a clean screw before production.
- No Output: When facing no output due to a blocked die caused by solidification, it's important to inspect the material entrance from the hopper, clear any blockages inside the hopper, increase the die temperature to dissolve blockages, and consider changing the screen for uninterrupted production.
- Rough Surface Caused by Unmelted Particles: To address a rough surface resulting from unmelted particles, it’s necessary to do a thorough inspection of the screen for tears. Increasing temperatures, especially in the compression zone, checking zone temperature resistance, and adjusting screw rpm and zone temperatures to prevent degradation from cross-linked particles can all contribute to smoother extrusion.
- Burned or Discolored Extrudate: When dealing with burned and discolored extrudate the following can be done: reduce screw rpm and gradually lower the barrel temperatures until the desired color is achieved. Selecting an extruder with a lower L/D ratio for production can further enhance the quality of the extruded products.
- Die Lines: Die lines, a common defect, can be addressed by selecting a material with lower viscosity and increasing the die temperature to ensure a smoother extrusion process.
- Melt Fracture: Reducing barrel temperatures and changing the material by the die design helps mitigate melt fracture.
- Shark Skin: Shark skin, characterized by surface irregularities, can be minimized by reducing rpm, changing the screen, and increasing the melt temperature for improved extrusion results.
- Fish Eyes: For extrusion products showing “fish eyes,” it's crucial to check the material and screen for contamination, ensure proper drying of the material, and reduce temperatures to prevent material degradation during the extrusion process.
- Bubbles: Preventing bubbles on the profile surface involves proper drying of the material, reducing melt temperature, and adjusting the screw rpm for smoother and defect-free extrusion.
- Warpage: Warpage issues due to insufficient cooling can be alleviated by increasing the cooling bath length, reducing water temperature, and balancing the die according to part-wall thickness for uniform cooling.
- Orange Peel Surface: An orange peel surface, which is indicative of low die temperature, can be improved by increasing the die temperature and raising the temperature of zones close to the die. This results in a smoother and more refined extruded product.
What Is the Life Span of Extrusion Molding Products?
There is no one-size-fits-all answer here. The life span of extrusion molding products varies based on factors like: material type, environmental conditions, and manufacturing quality. Materials with higher durability, quality additives, and reinforcement generally contribute to a longer life span. Harsh environmental factors, including extreme temperatures and exposure to chemicals, can accelerate wear and affect longevity. However, to give an estimate of the expected lifetime, the average lifetime of plastic products tends to be around 10 years. However, this can vary greatly for different applications. Some plastics can remain fully functional for decades. One such example is pipe installations that can last between 50 to 100 years.
Are Extrusion Molding Products Durable?
It depends. Extrusion molding products can be highly durable, with their longevity depending on various factors. The choice of materials, environmental conditions, manufacturing quality, and intended applications all affect the durability of the product. Products made from high-quality materials and designed for specific purposes tend to exhibit robustness and resistance to wear.
Is Extrusion Molding Expensive?
No, extrusion molding, whether plastic molding or metal molding, is generally considered to be both efficient and cost-effective compared to other processes like injection molding or other metal forming processes.
What Are the Advantages of Extrusion Molding?
Extrusion molding has a few advantages compared to other manufacturing methods:
- A very efficient process, resulting in a low cost per part produced.
- Is suitable for big production batches.
- Excess plastic can be recycled and reused, cutting down on waste and production costs.
- Allows for complex shapes of many different materials and design parameters.
What Are the Disadvantages of Extrusion Molding?
Extrusion molding has the following disadvantages compared to other manufacturing methods:
- Parts can swell immediately after being extruded, resulting in inconsistencies in batches.
- The costs of purchasing the equipment for extrusion molding can be fairly high.
- The designs that can be produced are limited.
What Is the Difference Between Extrusion Molding and Injection Molding?
Extrusion and injection molding processes might seem similar at first glance due to both processes involving molten material being passed through machinery to manufacture low-cost components in the desired shape. Both methods also operate as continuous production processes, in which the cost-effectiveness improves with higher quantities of parts ordered. However, these processes are very different, and their main difference comes down to how the final shape is formed.
With injection molding, plastics are melted into a liquid form and shaped using a mold or a specially designed cavity. Once cooled, manufacturers eject the now-solid plastic material, forming intricate three-dimensional shapes with a smooth surface finish. The process is highly efficient and capable of rapid repetition, hundreds or thousands of times. This repetition helps amortize the mold-tool costs, leading to reduced overall expenses as the number of plastic products ordered increases. The use of a single mold tool for each part, coupled with the affordability of plastic pellets, makes this manufacturing method well-suited for producing economically viable parts with consistent quality.
Extrusion molding, on the other hand, involves the continuous extrusion of plastic material from a machine, forming a lengthy tube (or line bar) that is then cooled. Molten material passes through an extrusion machine and exits through a two-dimensional die opening, forming rod-like shapes with intricate cross-sections, outer shapes, and even inner voids. The shape and length of the final component are determined by the die in the extrusion machine. These elongated bars, often spanning lengths of 100 or 1000 feet, are typically cut using a band saw and can undergo further shaping, post-modification, or integration into assemblies.
What Is the Difference Between Extrusion Molding and Compression Molding?
The primary difference between extrusion molding and compression molding lies in their processes and applications. Compression molding involves using a two-piece mold heated to soften the molding material, which is then loaded into the mold's lower half. The two mold parts are brought together under pressure, welding the material into the desired shape. Hardening is achieved through further heating (for thermosetting plastics) or chilling (for thermoplastics) under pressure in the mold. This method is predominantly used for thermosetting plastics.
On the other hand, extrusion involves a continuous operation, with thermoplastic materials melted and forced through a forming die. Various products such as: pipes, tubing, plastic bottles, films, and profiles are produced through extrusion. The material, fed into an extruder, can be in pellet, powder, granulate, or melt form. Extruders must melt, homogenize, and pump the material through a die system to ensure acceptable output uniformity. Downstream equipment, including cooling rolls and cutting devices, continuously shapes and cools the extruded melt. The key difference is that compression molding is often used for thermosetting plastics, while extrusion is primarily employed for thermoplastics and involves a continuous shaping process.
Summary
This article presented extrusion molding, explained it, and discussed how it works and its applications. To learn more about extrusion molding, contact a Xometry representative.
Xometry provides a wide range of manufacturing capabilities, including extrusion and other value-added services for all of your prototyping and production needs. Visit our website to learn more or to request a free, no-obligation quote.
Disclaimer
The content appearing on this webpage is for informational purposes only. Xometry makes no representation or warranty of any kind, be it expressed or implied, as to the accuracy, completeness, or validity of the information. Any performance parameters, geometric tolerances, specific design features, quality and types of materials, or processes should not be inferred to represent what will be delivered by third-party suppliers or manufacturers through Xometry’s network. Buyers seeking quotes for parts are responsible for defining the specific requirements for those parts. Please refer to our terms and conditions for more information.
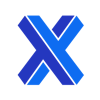