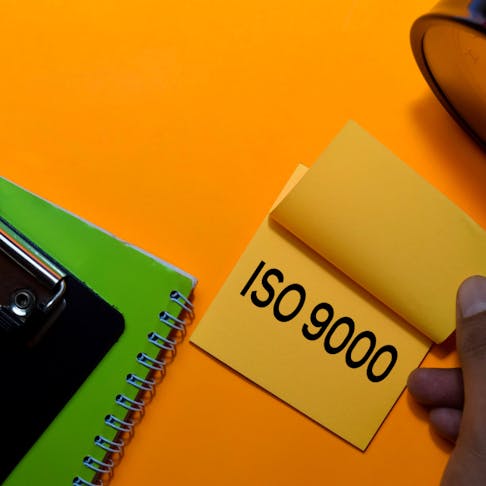
ISO9000 Certification: Standard Definition, Audit Requirements, Benefits
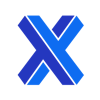
ISO 9000 is a family of standards developed by the International Organization for Standardization (ISO). These standards specify the functional details of a generalized quality management system (QMS). The ISO 9000 series integrates several standards, including ISO 9001:2015: Quality Management Systems - Requirements, ISO 9000:2015: Quality Management Systems - Fundamentals and Vocabulary (definitions), ISO 9004:2018: Quality Management - Quality of an Organization - Guidance to Achieve Sustained Success (continuous improvement), and ISO 19011:2018: Guidelines for Auditing Management Systems.
ISO 9001 is the key standard, outlining requirements for a QMS. An organization’s adherence means they can be expected to consistently provide products and services that meet customer and regulatory requirements, enhance customer satisfaction, and continually improve their processes.
This article will discuss the standard’s definition, audit requirements, and benefits.
What Is a ISO 9000 Certification?
The ISO 9000 certification is an official acknowledgment that the certified organization complies with ISO 9000 standards and requirements. Given the “International Organization for Standardization” moniker, it should come as no surprise that ISO 9000 is meant as a set of international standards to define quality management systems.
ISO 9000 compliance can only be certified through an accredited third-party auditor. The audit assesses whether the organization's QMS meets ISO 9000 requirements. Certification is not legally mandated, but many organizations pursue it because it can provide a competitive advantage by: demonstrating their commitment to quality and continuous improvement, meeting customer and regulatory requirements, and opening access to new markets.
What Are Quality Management Systems?
Quality management systems are used by companies to ensure that their products or services consistently meet or exceed customer expectations. At a minimum, a QMS should: provide an operational framework to establish and maintain quality objectives, monitor and control quality processes, and continuously improve overall performance.
The first purpose of a QMS is to satisfy customers by fulfilling their requirements. A well-implemented and systematic approach to quality will be consistent, efficient, and productive while simultaneously minimizing errors, defects, waste, and customer complaints.
What Industries and Companies Is ISO9000 Relevant For?
QMS such as this is particularly relevant to;
- Manufacturing: ISO 9000 applies to manufacturing industries, including automotive, aerospace, electronics, pharmaceuticals, food and drink, industrial machinery, and consumer goods.
- Healthcare: ISO 9000 fits well into the healthcare sector. It serves to ensure quality management in hospitals, clinics, laboratories, medical device manufacturers, and pharmaceutical developers/manufacturers.
- Construction: Larger construction operations typically benefit from the implementation of a QMS such as ISO 9000. Most large construction firms adopt it.
- Information Technology: ISO 9000 can be effective and relevant in the IT industry, both in software development and service management companies. Large and medium-sized organizations typically hold ISO 9000 accreditation and smaller service providers aiming to serve larger clients tend to see value in this too.
- Consulting/professional services: ISO 9000 is widely implemented by consulting, accounting, legal, and other professional service providers. It is generally seen as a way to enhance client satisfaction, streamline processes, and improve the quality of outcomes for clients and providers.
- Education/training: ISO 9000 can be helpful in educational institutions and training centers to improve processes, curricula, and student learning/satisfaction. Many universities and wider training organizations — particularly those serving blue-chip clients — implement ISO 9000.
Types of ISO 9000 Certifications
The ISO 9000 standard encompasses many subsections that apply to different types of QMS operations. These are listed below:
ISO 9001
ISO 9001 codifies the criteria for establishing, structuring, and maintaining a high-functioning QMS focused on meeting customer requirements, enhancing customer satisfaction, and improving overall operational performance. It defines key aspects such as: customer focus, process-based approaches, continual improvement, risk-based thinking, leadership and engagement, documentation and records, internal audits, and management reviews.
ISO 9002
ISO 9002 is no longer an active standard or available for certification. It has been replaced by the updated ISO 9001:2015 standard. ISO 9002 was specifically focused on the requirements for quality management systems (QMS) in production, installation, and servicing operations. It provided guidance for organizations involved in manufacturing and service industries but without design control. Since the release of ISO 9001:2015, ISO 9002 stopped being maintained as separate standards.
ISO 9003
ISO 9003 was another part of the 1994 ISO 9000 series which has been superseded by the updated ISO 9001:2015. ISO 9003 is related to the final inspection and testing of products, providing QMS guidance for manufacturing organizations that do not have design control.
ISO 9001:2015
ISO 9001:2015 is the current version of the ISO 9001 standard, which is a part of the ISO 9000 family of standards for quality management systems (QMS). It was released in September 2015 and replaced the 2008 version. The release of ISO 9001:2015 brought various revisions and updates that superseded previous versions. The key changes are in these categories: high-level structure (HLS), risk-based reasoning, organizational context, leadership and commitment, process approach, documented information, continuous improvement, and performance evaluation.
Industry-Specific Versions of ISO 9000
These industry-specific versions build upon the foundation of ISO 9001:
- AS9000 & AS9100: AS9000 was a quality management system standard that was developed specifically for the aerospace industry. AS9000 is no longer in use or supported, having been replaced by the AS9100 standards. AS9100D is the most current version. It builds from ISO 9001:2015 with additional user/life risk emphasis criteria in quality, safety, and reliability. AS9100 covers aerospace-specific methodologies.
- PS9000: PS9000, also known as "Pharmaceuticals – Good Manufacturing Practices for Packaging Materials," is a QMS for the pharmaceutical packaging sector. It prescribes approaches for ensuring quality and safety in packaging materials for pharmaceutical products.
- QS9000 & IATF 16949: QS9000 is no longer active or maintained because it was superseded by IATF 16949:2016, which is closely aligned with the ISO 9001:2015 structure. ISO/TS 16949 is an automotive industry-specific standard. It was developed by the International Automotive Task Force (IATF) and is based on ISO 9001:2008. It covers product design, development, and production, as well as customer-specific processes and methods.
- TL 9000: This guidance was developed for the telecommunications sector. It builds on the requirements of ISO 9001 by adding specific criteria related to product reliability, network availability, and performance measurement. TL 9000 is managed by the Quality Excellence for Suppliers of Telecommunications (QuEST) Forum.
- ISO 13485: This is specific to medical device manufacturers and designers. It specifies the requirements for a QMS in the design, development, production, installation, and servicing of medical devices. ISO 13485 focuses closely on regulatory compliance, risk management, and product safety.
- ISO/IEC 20000: Specifies the requirements for an IT service management system. It reflects the ISO 9001 principles, with an increased focus on the delivery of IT services, service agreements, service continuity, and customer satisfaction.
- ISO/IEC 90003:2014: Titled "Software engineering – Guidelines for the application of ISO 9001:2008 to computer software." This standard helps people interpret ISO 9001:2008 as it applies to the development, supply, and maintenance of software. This is not a stand-alone certification standard. It advises and assists software organizations to align their practices with ISO 9001.
- ISO/TS 29001: ISO/TS 29001, also referred to as "Petroleum, petrochemical, and natural gas industries - sector-specific quality management systems - requirements for product and service supply organizations," is an industry-specific QMS. It ensures consistent quality, safety, and reliability in the development of fields and the supply of products and services.
- ISO 18091: This is an implementation process for ISO 9001 for use in the public sector. It’s meant to provide context that local governments need to implement the standards. It has been updated to include the requirements of ISO 9001:2015. Included in the annex sections are analysis tools for local governments to assess and improve their processes and services. In particular, it emphasizes that users evaluate their progress across the 17 UN Sustainable Development Goals (SDGs).
- ISO/TS 54001: This International Standard specifies quality management requirements for organizations that are responsible for electoral processes. Particular requirements go beyond the generic standard ISO 9001:2015 to assist in effective implementation. The standard, along with ISO 9001:2015, allows electoral organizations to demonstrate their ability to consistently meet customer needs and applicable statutory and regulatory requirements.
- ISO 17025:2017: ISO/IEC 17025:2017 specifies general requirements for the capability and effectiveness of testing/calibration laboratories. It enables laboratories to demonstrate their capability, reliability, and accuracy. The accreditation is world-acknowledged and gives clients confidence in the competence and reliability of a laboratory's services, across multiple fields/sectors.
What Are the ISO 9000 Audit Criteria?
ISO 9000 is a family of standards that includes ISO 9001, ISO 9004, and other related documents. It is these subordinate standards that carry audit requirements. ISO 9001 is the most widely adopted standard within ISO 9000 and it details all component requirements for a QMS.
When conducting an audit of an organization's ISO 9001:2015 QMS, auditors apply the requirements outlined in the standard. The standard consists of ten clauses that outline the functional requirements for a QMS. These clauses cover all aspects of quality management, including organizational context, leadership, planning, support, operation, performance evaluation, and continuous improvement.
Auditors evaluate the organization's processes, documentation, and practices against the standard. They assess both the implementation and maintenance of the QMS. They may also consider other criteria, such as law, accrediting organizations’ regulations, customer requirements, and industry standards.
The ISO 9000 Audit and Accreditation Process
The ISO 9000 audit and accreditation process involves multiple steps and is conducted either by certification bodies or registrars. The process is outlined below:
- The organization seeking ISO 9000 certification must prepare for an audit by establishing and implementing an ISO 9001 QMS. This requires that they enact and document relevant processes, procedures, and policies throughout the organization.
- The first-stage audit, or documentation review, is sometimes referred to as the readiness audit. It is often performed remotely. The auditor reviews the documented QMS to assess whether it should, on paper, meet the requirements for a full audit. This stage highlights shortfalls early on and allows the processes to be improved.
- The second-stage audit, or the certification for on-site audit, is a deep assessment of the QMS implementation and operations. The auditor verifies compliance with the QMS along with its effective implementation through interviews, records reviews, and observations of active processes. The auditor also identifies areas for improvement and will highlight any non-conformities they find.
- Corrective actions are required when non-conformities are identified during the second-stage audit. The organization must provide the auditors or certification authority with documentary evidence of the actions they’ve taken, showing clearly that the non-conformities have been resolved.
- After the second-stage audit and satisfactory correction of non-conformities, the certification body decides whether to grant ISO 9000 certification. If granted, the certification body issues the certificate.
- Regular surveillance audits are required in order to maintain certified status. The same certification body will typically perform these audits as well. Surveillance audits are conducted at specified intervals (generally annually) to ensure continued compliance with ISO 9001 in maintaining and operating the QMS.
What Are the Benefits of a ISO 9000 Certification?
ISO 9000 certification offers various benefits to the holder:
- Since the standard is globally recognized and demonstrates robust and effective QMS, it acts to enhance the holder’s reputation. Customers, stakeholders, and potential partners gain confidence in the organization because ISO certification is given by an impartial third party. It demonstrates a commitment to quality and customer satisfaction.
- It signals to customers a focus on delivering quality products or services consistently. Customers who believe that their requirements will be met and that their satisfaction is prioritized are more likely to commit.
- Certification pushes the organization toward efficient and effective processes, error reduction, and improved productivity. A systematic approach to quality focuses employees on identifying areas for improvement, reducing operational costs, and improving resource allocation. This can result in cost savings, better productivity, and reduced waste.
- Enhanced risk management methods in the QMS help push the culture toward a risk-vs-reward mindset. It ultimately drives them to assess and address risks and opportunities systematically. This leads to better decision-making, improved resilience, and healthier risk management.
- Certification is often a de-facto requirement for participating in tenders, contracts, or supply chains, particularly in certified and constrained markets and with government organizations.
- Strengthened internal processes and communication drive improved team and team/client coordination, better clarity about responsibilities, and a more adaptive and flexible environment. Teams will better recognize their individual and collective purpose if they also understand other stakeholders’ responsibilities.
- Continuous improvement becomes a culture, rather than an idea. Performance monitoring at all levels, strengthened data/evidence analysis, and corrective and preventive actions all drive ongoing improvement. A culture of learning, innovation, and customer service can radically change a business.
When Are ISO 9000 Certifications Required?
Here are some situations where ISO 9000 certifications may be required or beneficial:
- Some large B2B and government contracts require that participants be ISO 9000 certified as a pre-condition. ISO 9000 certification is often seen as a way to filter out weaker and less orderly contributors.
- In some sectors, outside regulators specify ISO 9000 certification as a compliance requirement. Medical device manufacturers generally demand that ISO 9000 suppliers conform with regulatory standards like ISO 13485.
- ISO 9000 functions as a baseline indicator of competence. A lack of certification is commonly seen as grounds to exclude groups from participation in the automotive, aerospace, and pharmaceutical industries.
- Successful ISO 9000 ratings often confer competitive advantages, especially in spaces where they are less common. It is a mark of organizational capability and maturity that implicitly marks the holder as better.
- Customer expectations often demand ISO 9000 certification. Many ISO 9000-registered companies would struggle to strike deals with non-certified partners because of the optics among stakeholders.
- Internal improvement initiatives often have a marked effect on company culture and efficacy. Even if external requirements are not driving factors, pursuing ISO 9000 certification as part of your internal improvement initiatives can benefit your business.
What Accrediting Body Issues ISO 9000 Certifications?
ISO 9000 certifications are issued by certification organizations who in turn are licensed by accreditation bodies. These certifiers are independent and evaluate/verify an applicant's compliance with the ISO 9001 standard. Organizations that issue ISO 9000 certifications vary by industry, geography, and capability. In the US, these organizations are accredited by ANAB and IAS. There are currently 29 accredited service providers, a few of whom are listed below:
- Bureau Veritas Certification Holding SAS
- Intertek and Intertek SAI Global
- QMI-SAI Canada Ltd (SAI Global)
- TUV Rheinland of North America, Inc.
- TUV USA, Inc.
- World Certification Services Ltd.
- GCert
- SARA Registrar
- TCB Audit Services, LLC
- The Paragon Group Registrar
- Verisys Registrars, LLC
Similar Certifications and Accreditations to ISO9000
Some sectors may need separate or additional certifications. Here are a few:
- ISO 14001: The standard for environmental management systems (EMS) demonstrates a commitment to sustainability.
- ISO 45001: This is the standard for occupational health and safety management systems (OHSMS), promoting a safe work environment.
- ISO/IEC 27001: This standard for information security management systems (ISMS) ensures the confidentiality, integrity, and availability of data/information systems.
- ISO 22000: A standard for food safety management systems can be critical. It helps ensure the safety of food products, prevent foodborne illnesses, and maintain industry and regulatory compliance.
- AS 9100: The standard specific to the aerospace industry covers aerospace-related quality and safety considerations.
- IATF 16949: This one is a standard for quality management systems in the automotive industry, emphasizing defect prevention, continuous improvement, and supply chain management.
In addition to certifications for organizations, there are accreditations for certification bodies, including:
- ANSI National Accreditation Board (ANAB)
- International Accreditation Service (IAS)
- United Kingdom Accreditation Service (UKAS)
- National Accreditation Board for Certification Bodies (NABCB)
- Deutsche Akkreditierungsstelle (DAkkS)
- Joint Accreditation System of Australia and New Zealand (JAS-ANZ)
Other Certifications That Related to the Industries/Companies and/or Processes/Systems That ISO9000 Relates To
Your organization may wish to consider other industry- or process-specific certifications such as:
- ISO/IEC 20000 is the standard in IT service provision.
- ISO 50001 is a standard for energy management systems (EMS) meant to establish systems and processes to improve energy efficiency, reduce consumption and manage energy costs and environmental impacts.
- ISO 22301 covers business continuity management systems (BCMS). It helps businesses, government departments, and NGOs create plans and procedures to identify and manage potential disruptions so their critical activities are not interrupted.
- ISO 27001 is a standard for information security management systems (ISMS). It’s meant to improve information systems’ confidentiality, integrity, and availability.
- ISO 31000 focuses on risk management. It codifies guidelines to implement effective risk management processes, better equipping users to identify, assess, and mitigate risks.
- ISO 13485 is a standard for quality management systems for medical devices. It applies to their design, development, production, installation, and servicing.
- ISO 45001 is a standard for occupational health and safety management systems (OHSMS). The purpose is to make the work environment safer.
Summary
This article presented the ISO9000 certification, explained it, and discussed the audit requirements to become certified. To learn more about ISO9000, contact a Xometry representative.
Xometry provides a wide range of manufacturing capabilities and other value-added services for all of your prototyping and production needs. Visit our website to learn more or to request a free, no-obligation quote.
Disclaimer
The content appearing on this webpage is for informational purposes only. Xometry makes no representation or warranty of any kind, be it expressed or implied, as to the accuracy, completeness, or validity of the information. Any performance parameters, geometric tolerances, specific design features, quality and types of materials, or processes should not be inferred to represent what will be delivered by third-party suppliers or manufacturers through Xometry’s network. Buyers seeking quotes for parts are responsible for defining the specific requirements for those parts. Please refer to our terms and conditions for more information.
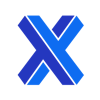