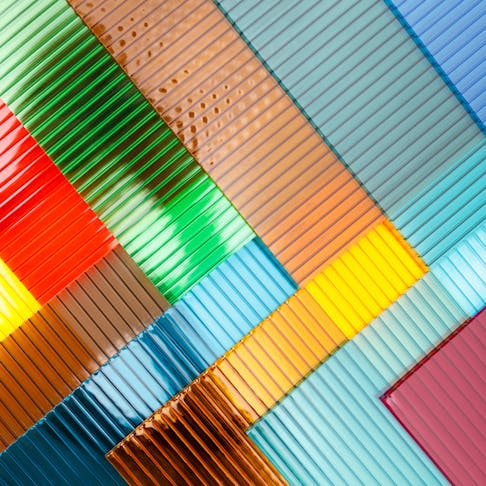
Polycarbonate 3D Printing: Definition, Purpose, How It Works, Advantages, and Examples
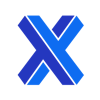
Polycarbonate (PC) is used in 3D printing with its inherent durability, heat tolerance, and resistance to chemicals, provided that certain guidelines are followed. It’s an excellent thermoplastic choice for producing mechanical components, molds (especially those utilized in thermoforming), functional prototypes, hinges, and even pulley bearings. PC is frequently combined with various other plastics to enhance its ability to withstand impacts. One example is PC-ABS. This alloy finds application in products like drone bodies and replacement parts that require greater durability than ABS alone can offer.
A printer capable of accommodating polycarbonate properties is essential to successful 3D printing with this material. An appropriate 3D printer will be equipped with a nozzle that can reach temperatures around 300 ºC, an enclosed printing chamber, and a robust temperature control system. These features enhance the likelihood of achieving a satisfactory print and ensure the material's unique requirements are met effectively.
In this article, we’ll take a closer look at polycarbonate 3D printing: its definition, how it works, its advantages and disadvantages, and examples of applications.
What Is Polycarbonate 3D Printing?
Polycarbonate 3D printing is a manufacturing process that utilizes polycarbonate (PC) material to create three-dimensional objects through additive manufacturing technology (layer-by-layer). The main 3D printing technology used to create objects made of this material is called fused deposition modeling (FDM). It uses polycarbonate filament as the raw material to build up the desired shape.
Polycarbonate (PC) boasts remarkable attributes—it's robust, with an ultimate tensile strength of 70 MPa and yield strength of about 63 MPa, and can withstand both high heat and impacts, maintaining structural integrity even at temperatures up to 150 °C (its glass transition temperature). Owing to these properties, PC has found extensive utility in a myriad of industries such as: aerospace, automotive, electronics, medical devices, and consumer goods.
What Is Polycarbonate 3D Printing Also Known As?
Polycarbonate 3D printing is also commonly referred to as PC 3D printing or PC filament 3D printing.
What Is the Purpose of Polycarbonate 3D Printing in Manufacturing?
The purpose of polycarbonate 3D printing in manufacturing is to harness the exceptional mechanical properties and thermal stability of PC through additive manufacturing techniques. Polycarbonate 3D printing allows for the creation of intricate geometries and complex internal structures that might be challenging or impossible to achieve through traditional manufacturing methods. This is particularly valuable for producing components with internal channels, lattice structures, or intricate designs that serve specific functions. Additionally, the additive nature of 3D printing enables rapid customization and the production of low-volume batches without significant setup costs. Finally, 3D printing PC allows for the quick iteration of designs with the same material that will be used for the final product. This helps in fine-tuning designs and assessing performance without the need for transitioning between different materials and manufacturing techniques.
What Are the Industries That Use Polycarbonate 3D Printing?
Polycarbonate finds application in a wide range of industries. The main industries that use polycarbonate include: aerospace, automotive, consumer goods, electrical devices and electronics, and medical devices. For example, polycarbonate proves to be an appropriate choice for applications within the electrical and automotive sectors due to its remarkable flame retardancy, heat resistance, light weight, and insulating properties. These applications encompass electrical housings, light fixtures, and even headlights in vehicles. Polycarbonate's transparent and shatter-resistant nature also makes it an excellent fit for protective equipment. This is specifically important in the safety and construction fields, where it is used in safety goggles and window materials.
How Does Polycarbonate 3D Printing Work?
3D printing with polycarbonate involves a layer-by-layer additive manufacturing process. The process starts with the creation of a digital 3D model of the desired object using CAD (computer-aided design) software. This digital representation serves as the blueprint guiding the printer's actions. Subsequently, the software is used to "slice" the 3D model into thin horizontal layers, which generates a set of instructions for the printer to follow.
During printing, the polycarbonate filament is heated within the printer's extruder. The molten material is then carefully deposited onto the build platform in precise accordance with the instructions derived from the sliced model. As each layer is added, the material begins to cool and solidify, bonding with the previous layer to gradually build the object's structure.
What Is the Step-by-Step Process for Polycarbonate 3D Printing?
Polycarbonate 3D printing typically involves several key steps:
1. Design
The process begins with creating a digital 3D model of the desired object using computer-aided design (CAD) software. This model serves as the blueprint for the subsequent printing process, defining the shape, dimensions, and internal structures of the object. The 3D model is then divided into thin horizontal layers using slicing software. Each layer's specifications are generated, including the path the printer's nozzle will follow to deposit the material accurately.
2. Preprocessing
Once the design is complete, the 3D model is prepared for printing. This involves tasks like scaling, orienting, and positioning the model within the build volume. Additionally, support structures may be generated to provide stability for overhangs and intricate features during printing.
3. Printer Setup
Before printing, the 3D printer must be calibrated and prepared. This involves a series of essential steps to ensure optimal printing conditions. Firstly, it's crucial to confirm that the print bed is perfectly level. This step is particularly critical when working with materials that can be sensitive to bed adhesion, like polycarbonate. Polycarbonate's tendency to warp during printing can lead to challenges in maintaining consistent layer adhesion.
In addition to bed leveling, it's important to ensure that the nozzle is clean and free from any residue that could affect the extrusion process. Proper nozzle maintenance is essential for achieving accurate and high-quality prints. Furthermore, selecting the appropriate printing parameters is essential. For polycarbonate, in particular, precise temperature settings are crucial for both the extruder and the build chamber. Polycarbonate's relatively high glass transition temperature requires careful temperature management to prevent warping and ensure proper layer bonding.
4. Printing
The actual printing process begins with the 3D printer's extruder or nozzle heating the polycarbonate filament to its melting point. The nozzle then moves to the printing positions defined by the machine instructions, depositing the molten material layer by layer onto the print bed. As each layer is deposited, the molten polycarbonate fuses with the previously deposited layers, creating a strong bond between them. This layer-by-layer approach leads to the gradual construction of the final object.
Once all layers are printed, the object is allowed to cool and solidify completely. This can take varying amounts of time depending on the complexity and size of the print. Additional mechanisms may be employed to regulate temperature, including the use of fans or even a heated build chamber, in order to uphold the ideal printing conditions.
5. Post-Processing
Once printing and cooling are complete, the object is removed from the build plate. Post-processing might involve removing excess support material, cleaning the part, and addressing any imperfections on the surface. This will depend on the complexity of the design and the presence of support structures.
6. Finishing
Finishing steps may be necessary to achieve the desired appearance and functionality. This can include sanding to smooth surfaces, painting or coating for aesthetics, and adding any required assembly components.
What Are the Materials That Can Used in Polycarbonate 3D Printing?
Polycarbonate 3D printing offers a range of material options beyond pure polycarbonate, including:
1. Polycarbonate (PC)
Polycarbonate is the primary material for polycarbonate 3D printing. PC is chosen for its exceptional strength, impact resistance, and heat tolerance. It is suitable for applications requiring durability and thermal stability.
2. Polycarbonate/ABS Blends
Blending polycarbonate with ABS (acrylonitrile butadiene styrene) can provide a balance between polycarbonate's strength and ABS's affordability and printability. This blend can be suitable for applications that demand a compromise between strength and cost.
3. Polycarbonate/Carbon Fiber Composites
Incorporating carbon fiber into polycarbonate can enhance the material's strength and stiffness while maintaining its heat resistance. Polycarbonate/carbon fiber composites are favored for producing lightweight, strong, and rigid components.
4. Polycarbonate/FR Blends
"FR" stands for “flame retardant.” Blending polycarbonate with flame-retardant additives makes the material suitable for applications where fire safety is a concern. These blends maintain polycarbonate's mechanical properties while reducing flammability.
5. Polycarbonate/Polyethylene Glycol (PEG) Blends
Adding polyethylene glycol to polycarbonate can improve its printability and reduce warping. This blend can be advantageous when working with complex geometries or large parts that tend to deform during printing.
How Long Does It Take for Polycarbonate 3D Printing To Print?
The time required to complete a polycarbonate 3D printing project can vary significantly based on a range of factors, including: the size and complexity of the object being printed, the layer height, print speed, density of infill, the 3D printer used, and the material’s unique requirements. As a general guideline, smaller and less complex objects may be completed within a few hours, while larger and more intricate designs could take several days. Many slicing software tools provide users with a rough "time to print" estimate based on the settings chosen, though this estimate should be viewed as an approximation rather than an absolute certainty.
How Much Does Polycarbonate 3D Printing Cost?
The cost of polycarbonate 3D printing is influenced by a range of variables, making its cost quite variable. The printing filament is a significant component of the total cost. Polycarbonate filament is expensive compared to other 3D printing materials. You can expect to pay around $30-$60 per spool of PC filament. Labor costs will include tasks such as printer setup, post-processing, and troubleshooting. Additional expenses stem from software and design tools, as well as finishing steps such as sanding, painting, or applying coatings.
Given all these factors, pinning down an exact cost for polycarbonate 3D printing without specific project details is challenging. A comprehensive cost assessment demands considering printer maintenance, energy consumption, labor, and supplementary processes.
Is Polycarbonate 3D Printing Expensive Compared to Die Casting?
It depends. Polycarbonate 3D printing can be more cost-effective for low-volume production runs, prototypes, and complex designs. It's advantageous for its design flexibility and rapid prototyping capabilities. Die casting, on the other hand, is more suitable for high-volume production due to lower material costs for bulk materials and the efficiency of batch processing.
What Are the Advantages of Polycarbonate 3D Printing?
Polycarbonate 3D printing offers a range of advantages that make it a sought-after choice for various applications:
- 3D-printed PC parts have good mechanical properties.
- It can withstand elevated temperatures, retaining structural integrity at temperatures as high as 150 °C.
- It demonstrates resistance to various chemicals, oils, and solvents.
- Polycarbonate's optical clarity makes it an excellent choice for applications requiring transparency.
- Good impact resistance makes PC suitable for components that may experience sudden forces or collisions.
- It is valuable as an electrical insulator.
- Despite its strength, PC filament's lightweight nature is advantageous for applications where weight reduction is desired.
- It is recyclable.
What Are the Disadvantages of Polycarbonate 3D Printing?
While there are some notable advantages associated with PC 3D printing, there are also some drawbacks that should be taken into account. These include:
- Polycarbonate filament is relatively more expensive compared to other 3D printing materials, which might affect the overall cost-effectiveness of projects.
- Polycarbonate filament is hygroscopic, meaning that it tends to absorb moisture from the surrounding air. It is essential to store polycarbonate in an airtight and moisture-free setting once its packaging is opened.
- It demands a considerably high-temperature hot end, ideally ranging between 290 °C and 300 °C. Slower printing speeds or the utilization of composite polycarbonate filaments might allow for slightly lower temperatures. Inadequate temperatures or excessively fast printing speeds could result in filament jamming within the printer's nozzle.
- Inadequate temperature control can lead to poor layer adhesion on the print bed and potential separation or cracking as the material cools and warps. Ideally, the bed temperature should fall within the range of 135-150 °C.
- Airflow in the print chamber during printing can lead to poor outcomes such as brittle prints. This occurs because rapid cooling can affect layer bonding and structural integrity.
- Susceptible to oozing during printing, where the printer's nozzle releases small amounts of filament even when not actively printing. This can cause unwanted strings or blobs on the printed object, impacting its appearance. Manual adjustments are often needed when printers lack PC presets. Limiting retraction distances to under 10 mm can prevent jams.
- When heated, polycarbonate can release BPA into the surrounding environment in the form of fumes (e.g. BPA), which can be harmful if inhaled. This makes proper ventilation and operating in well-ventilated areas essential.
What Are Examples of Polycarbonate 3D-Printed Products?
Some examples of polycarbonate 3D-printed products are listed below:
- Customized bulletproof eyewear
- Scuba mask prototypes for tailored fits
- Prototype electronic display screen casings
- Personalized eye protection gear for specific needs
- Custom-designed optical components for research
- Motorcycle helmet prototypes with unique designs
- Specialized protective screens for niche applications
- Tailored electrical and telecommunications prototypes
- Custom-designed sunglass frames or phone cases
What Is the Lifespan of Polycarbonate 3D-Printed Products?
Polycarbonate is expected to have a lifespan of 15 years on average, depending on storage and usage. It is expected to last considerably longer than PLA (polylactic acid) 3D-printed products, for example. PC demonstrates remarkable resistance to absorbing moisture from the environment. This attribute helps preserve the stability and performance of PC 3D-printed products over extended periods. PC also showcases exceptional UV resistance. As a result, PC 3D-printed products are anticipated to endure considerably longer, making them a more reliable choice for applications that demand durability and resistance to environmental factors.
Are Polycarbonate 3D-Printed Products Durable?
Yes. Polycarbonate 3D-printed products are durable. They are known for their tensile strength, heat resistance, impact resistance, and shock and scratch resistance.
What Are the Main Differences Between Traditional Polycarbonate and 3D-Printed Polycarbonate?
Traditional polycarbonate and 3D-printed polycarbonate exhibit distinct differences in properties stemming from their manufacturing methods. These differences lead to differences in the applications they can be used for. In traditional polycarbonate production, methods such as injection molding and extrusion involve shaping melted polycarbonate resin using molds or dies. This results in a material with uniform density and consistent mechanical characteristics, known as isotropic properties, which remain consistent in all directions.
3D-printed polycarbonate, on the other hand, is generated through additive manufacturing. Molten polycarbonate filament is layered to construct the final object. This technique introduces anisotropic properties, meaning that the material's characteristics can vary along different axes of the object due to the layered structure and layer adhesion. While a traditional polycarbonate part offers consistent strength and durability in all directions, the 3D-printed counterpart's mechanical properties can differ based on layer bonding quality, design intricacies, and print parameters. This variation in anisotropic properties underscores the importance of understanding the directional attributes of 3D-printed polycarbonate when considering its suitability for specific applications.
Traditional methods also necessitate molds and tooling, limiting customization and cost-effectiveness for small runs, whereas 3D printing enables personalized designs and rapid prototyping.
For more information, see our guide on Polycarbonate Cutting.
What Is The Difference Between Polycarbonate 3D Printing and 3D Printing?
Polycarbonate 3D printing is a specific subset of 3D printing. It makes use of polycarbonate as the raw material, whereas general 3D printing may be performed with any printable material.
Polycarbonate 3D printing is normally performed using the fused deposition method. In this process, polycarbonate filament is melted and layered to construct three-dimensional objects. On the other hand, general 3D printing, also referred to as additive manufacturing, encompasses a wider spectrum of materials and techniques. Such techniques include: digital light processing (DLP), direct metal laser sintering/selective laser melting (DMLS/SLM), electron beam melting (EBM), fused deposition modeling/fused filament fabrication (FDM/FFF), material jetting, binder jetting, stereolithography (SLA), and selective laser sintering (SLS).
While polycarbonate remains a material choice in this broader landscape, it shares space with other thermoplastics like PLA and ABS, as well as metals such as aluminum and titanium. The selection of material hinges on the object's intended functionality and the chosen printing method. Also, 3D printing is an umbrella term used to describe a wide range of different methods that “print” 3D products.
For more information, see our guide on the 3D Printing Process.
Summary
This article presented 3D printing polycarbonate, explained it, and discussed how it works and its advantages. To learn more about 3D printing polycarbonate, contact a Xometry representative.
Xometry provides a wide range of manufacturing capabilities, including 3D printing and other value-added services for all of your prototyping and production needs. Visit our website to learn more or to request a free, no-obligation quote.
Disclaimer
The content appearing on this webpage is for informational purposes only. Xometry makes no representation or warranty of any kind, be it expressed or implied, as to the accuracy, completeness, or validity of the information. Any performance parameters, geometric tolerances, specific design features, quality and types of materials, or processes should not be inferred to represent what will be delivered by third-party suppliers or manufacturers through Xometry’s network. Buyers seeking quotes for parts are responsible for defining the specific requirements for those parts. Please refer to our terms and conditions for more information.
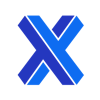