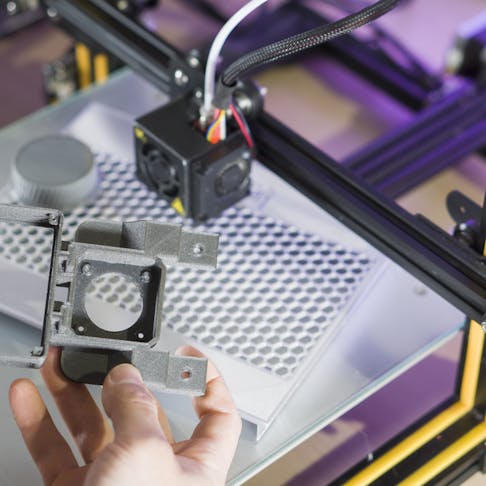
What Is the Strongest 3D Printer Filament?
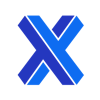
Printers of the FDM/FFF (Filament Deposition Modeling/Fused Filament Fabrication) variety build parts using strands of plastic feedstock known as filaments. The plastic is melted and extruded to build the 3D model. There are several types of 3D printer filaments that are known for their strength and durability. Your definition of the strongest one, however, depends on the printed part’s specific application and requirements.
There are two basic interpretations of ‘strength’ that can apply to the tensile behavior of 3D printer filaments. They depend on the eventual tensile loading of the finished part.
In one case, the part is loaded in a direction that aligns with the filaments. When this is the case, high tensile strength in the raw filament will translate into good tensile strength in the finished item as well.
The other case occurs when the part is loaded perpendicular to the print’s layers. At this point, the ‘strongest 3D filament’ becomes an expression of the adhesion strength between adjacent bonded filaments, rather than the intrinsic filament strength. This latter situation leads to a definition that looks at the strength issue as ‘which filament bonds most securely.’
Both of these filament properties (along with others) are critical if you want to build high-resilience, flex-tolerant, and abrasion-resistant models. You must balance the demands in the final build, targeting tensile strength, bending strength, hardness in wear, toughness in impact, and more. Each filament type can give your models different advantages, but no one will suit all situations. Remember, too, that your printer may not accept all possible build materials, and some filaments have more design constraints than others. And no matter which types you choose, the final product’s properties will depend heavily on the design’s quality and the thought you put into design-for-manufacturing (DFM) principles.
This article will examine several 3D print filaments that are considered to have a balance of properties and review some of the concepts you’ll need to keep in mind when designing for them.
What Are the Types of 3D Printer Filament?
FDM/FFF filaments come in many materials, with an even wider range of additives that enhance particular properties such as: abrasion resistance, tensile strength, and flexural toughness. Below are the filament base materials that are widely considered to offer the highest strength, toughness, and durability in 3D-printed models:
1. Polycarbonate
Polycarbonate (PC) filaments produce models of high strength, toughness, and heat resistance. Along the filament’s axial direction, it has a tensile strength of 66 MPa. Its advantages include: high strength, temperature tolerance, and optical clarity. On the other hand, PC can be hard to print with and has a bad tendency to absorb moisture. PC costs $70-200 per kg at 1.75 mm diameter. For more information, see our guide on What is Polycarbonate?
2. Nylon
Nylon-filament-built models are known for their strength and wear resistance. The material has a tensile strength of 50-90 MPa depending on grade. Nylon is a tough, inexpensive material. It can be difficult to print quality models, however, and the material weakens severely when its moisture content falls too low. Nylon can be bought at $40-100 per kg at 1.75 mm diameter. For more information, see our guide on All About Nylon 3D Printing Filament.
3. TPU
Thermoplastic polyurethane (TPU) builds highly resilient and elastic items that can withstand significant impacts and abrasion. Its inherent elasticity makes this a ‘strong’ material in many regards. TPU has a tensile strength of 50 MPa. The trouble is it can easily clog printer nozzles and must be printed slowly. TPU goes for $30-60 per kg at 1.75 mm diameter. For more information, see our guide on Thermoplastic Polyurethane, Engineering (ETPU).
What is Meant by Tensile Strength for the 3D Printer Filament?
The tensile strength of a 3D print filament describes the maximum tensile load that a filament can withstand before it either fractures or undergoes permanent (inelastic and unrecoverable) stretching. Thermoplastic polymers, such as those used in FDM/FFF printing, have elastic extension load limits. When the load is below the filament’s elastic limit, it will return to the original dimensions once that load is removed. When its elastic load stress is exceeded, permanent deformation or fracture occurs.
What is Meant by Impact Strength for the 3D Printer Filament?
Impact resilience for a 3D print filament is the measure of the filament’s reaction to sudden impact or shock loading. A strong material should absorb the impact energy and deform without fracturing. It is an important property for materials used in mechanical parts, toys, and protective gear, for example.
It should be noted that the impact resilience of a 3D-printed item is not solely determined by the standalone filament. Factors such as: build direction relative to the impact, ‘internal’ lattice fill construction/density, and filament layer fusion also affect its performance. In many cases, these factors will be collectively more significant than the raw filament’s impact characteristics.
What Are Other Strength Metrics Used for 3D Printer Filaments?
Printer filaments have other strength-related properties that may be critical to your design process. There are also strength-maintaining properties that should be taken into account in this analysis. While these can be properties of the filament, it is more useful to view these as properties of a model, built using a filament type. These strength metrics are listed below:
- Flexural Strength: Measures a filament or model's resistance to fracture or permanent distortion when subjected to a bending force.
- Elongation at Break: Measures a filament or model's ability to resist fracture under steady tensile loads by suffering permanent (inelastic) distortion as load increases. When a fracture eventually occurs, plastic deformation will be measurable on either side of the fracture.
- Shear Strength: Measures a material's or model’s ability to resist fracture or deformation under shear loading. The shear strength of the bulk material is only slightly related to the shear strength of a printed part. Shear-load situations are often complex and don’t represent pure shear of the material. This makes actual test results far more dependent on printing orientation, part design, and loading scenarios than the basic filament property.
- Compressive Strength: Measures a filament or model's ability to withstand forces that compress or crush it. This is distinct from the model’s propensity to flex as a whole under compression — a situation that relies on flexural resilience instead. In reality, the compressive strength of the filament will relate only slightly to that of a 3D print, unless the print is solid and extremely simple in terms of cross-section.
- Abrasion Resistance: Measures a filament model's surface resistance to failure by spalling or grinding when repeatedly abraded by a similarly hard (or harder) material.
- Fatigue Resistance: Defines the material’s tolerance toward cyclic loading that approaches its physical limits. Strain rate, recovery time, and total cycle count for such loading can all negatively affect the material. That can be a function of build direction and other build parameters as much as the key properties of the material itself.
- Tear Strength: Measures the ability of a filament and the model to resist tearing. This will be a function of printing parameters when the tear is along the layer planes. Only when the tear happens in the filament’s axial direction is this strength entirely based on the material’s intrinsic properties. Tearing and shear are closely related modes.
- Heat Resistance: Defines a model's ability to retain its other properties as temperatures rise. If the polymer has a high glass transition temperature, it will tolerate higher usage temperatures before weakening.
- Creep Resistance: Defines a model’s ability to retain its dimensional stability under a steady load that continues over prolonged periods.
- Chemical Resistance: Defines a material’s ability to maintain its properties when exposed to harsh chemicals such as solvents, acids, and bases, or conditions like UV exposure.
Some of the above parameters will closely align with the filament material’s basic properties while others are extremely dependent on the printed item’s design and configuration.
What is Filament for 3D Printers?
3D printer filament is the polymer feedstock that is fed through the printer extruder and melted for the construction of printed models. This feedstock can be any one of a range of polymers and may contain other additives that modify the polymer properties. The filament feedstock is delivered on ready-to-install rolls that supply material to the extruder from a fixed position, through a guide. The filament is gripped by a feeder mechanism of gears or pinch wheels that pull it from the reel and push it through the extruder's heated nozzle when required.
What is a High-Performance Polymer?
High-performance polymers are differentiated from more pedestrian materials by a number of possible material characteristics. High-performance materials are usually superior in at least one of these characteristics:
- Tensile strength
- Shear strength
- Bending strength
- Temperature limit before properties begin to degrade
- Chemical resilience
- Wear resilience
- Creep resistance
- Elasticity
What is Composite Filament?
Composite filaments for FDM/FFF are 3D printing filaments that include additives within the basic filament polymer. Additives such as wood fiber, metal powders, carbon or Kevlar® fiber, and many other materials are used to enhance particular properties of basic and high-performance printing polymers. The composites are meant to improve the properties or functionality over that of pure polymers.
Wood fibers with round cross-sections and smooth surfaces improve the strength, stiffness, and density of printed parts. Kevlar®, carbon fiber, or graphene-loaded filaments tend to have superior strength, toughness, and stiffness. In large enough proportions, graphene can even make the material electrically conductive. Filaments that contain powders of bronze, copper, and stainless steel do not offer enhanced strength but can create metal-like appearances. Composite filaments allow you to modify one or more properties of 3D printed parts, but there are printing issues that may make such materials hard to use in simpler machines.
What is the Strongest 3D Printer Filament I Can Choose?
The strongest 3D printer filament will depend on specifics such as: expected loading type, loading intensity, design-build orientation and fill density of the 3D printed part. However, the following are the strongest 3D printer filaments currently available:
- Carbon Fiber Reinforced Nylon: This combines the strength enhancement of carbon fiber additives with the toughness and durability of nylon, making it generally the strongest 3D printing material.
- Polycarbonate: PC is a tough and durable filament that can withstand high temperatures. It offers excellent impact resistance, among other high-level performance properties.
- Polyetherimide (Ultem / PEI): A thermoplastic with excellent strength, heat resistance, and chemical resistance, Ultem sees wide use in aerospace component prototyping.
It's important to note that these filaments will often require specialized printer settings and may well not be compatible with simpler FDM/FFF printers. They can be considerably more difficult to print, so it's important to practice with these high-performance materials before attempting to build functional models under time constraints.
How Long Does the Strongest Filament Last?
The longevity of filament materials (and therefore models) can depend on a variety of factors. They’ll last longer if the material’s service parameters are not exceeded and the part doesn’t get used in a way that generates much wear. Conditions that can pose issues for various materials are:
- Water exposure for hygroscopic and soluble materials.
- Excess temperatures approaching the glass transition temperature.
- UV or chemical attack that the materials cannot tolerate.
- Overloads in tension, compression, shear, or bending.
- Fatigue — many filament materials and printed models can sugar from cyclic loading damage.
- Excessively dry conditions — some filaments require that their moisture content stays above certain levels (nylon needs at least 8% for example). Drying out will weaken these materials.
Is the Strongest 3D Printer Filament Expensive?
It depends. The prices of FDM/FFF filaments vary considerably. Lower-volume orders and more complex materials, however, tend to be more expensive. The max price is rarely more than double the minimum price. For example, PETG filament commonly goes for around $40-50 per kg, Ultem filament is $50-70 per kg, and carbon fiber-loaded nylon is typically at $60-100 per kg.
Are the Strongest 3D Printer Filaments Compatible with All 3D Printer Brands?
No, temperature limits, table adhesion properties, and a variety of other machine settings can limit the machine’s ability to print with advanced materials. It is often possible to use after-market printer modifications to expand your printer’s compatibility range. It’s a good idea to consult user groups and specialist component suppliers before making modifications, though. For more information, see our guide on Best Cheap 3D Printer.
Summary
This article presented the strongest 3D printer filament, explained it, and discussed its various properties and how its strength is measured. To learn more about 3D printer filaments, contact a Xometry representative.
Xometry provides a wide range of manufacturing capabilities, including 3D printing and other value-added services for all of your prototyping and production needs. Visit our website to learn more or to request a free, no-obligation quote.
Copyright and Trademark Notices
- KEVLAR® is a trademark of E. I. du Pont de Nemours and Company
Disclaimer
The content appearing on this webpage is for informational purposes only. Xometry makes no representation or warranty of any kind, be it expressed or implied, as to the accuracy, completeness, or validity of the information. Any performance parameters, geometric tolerances, specific design features, quality and types of materials, or processes should not be inferred to represent what will be delivered by third-party suppliers or manufacturers through Xometry’s network. Buyers seeking quotes for parts are responsible for defining the specific requirements for those parts. Please refer to our terms and conditions for more information.
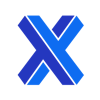