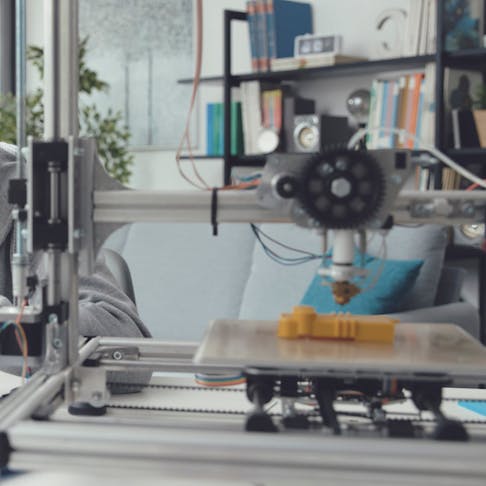
Gantry System for 3D Printing: Advantages and Disadvantages
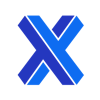
Gantry systems are an approach to creating a precision motion system for machine tools, such as 3D printers. The terminology is not a precise definition of a structure, as there are various approaches to creating precision motion gantries that diverge in key regards. Gantry systems can also be used for point application print systems such as FDM/FFF but they are also used for supporting area application printheads such as those used in diverse printing systems like SLS, SLM, and DMLS, for material jetting systems like OBJET®, binder jetting systems such as MetalX, and even laminated object manufacture (LOM). In some regards, the robot arms used in robotic additive manufacturing can also be considered as a gantry system, despite often using partially polar coordinate geometry rather than 3-axis orthogonal positioning. This article will discuss what a gantry system for 3D printing is, as well as its advantages and disadvantages.
What Is a Gantry System for 3D Printing?
Gantry systems support the point or area application 3D printhead. It provides at least some of the axes of motion that allow the head to traverse the build area to place the material application at precisely the required point in the build. Often, one or more axes are handled by the motion of the table. This is mounted to the gantry frame, however, and can be considered essentially integral to the gantry. For more information, see our guide on How 3D Printing Works.
What Are the Advantages of Gantry Systems for 3D Printing Projects?
There are various advantages to building a 3D printer based on using a gantry system, including:
- Widely considered to be a low-cost method of providing precise positioning and motion control over the printhead or extruder of a 3D printer. This allows for a relatively low-cost structure to provide accurate and repeatable positioning and control of fast motion. This results in better reproduction of the file being printed, without the need for high-cost equipment.
- Enables the printhead or extruder to accelerate and decelerate quickly, without misplacement due to reaction forces. Allowing faster printhead positioning in movement between printing operations reduces overall printing times.
- Can be used to accommodate variations of print bed sizes and shapes without major redesign. This enables the commonality of parts and motion controls over a family range of machine sizes. As most gantries are made of extruded or laser cut and folded materials, increasing machine size can be achieved simply by lengthening the structural members and drive mechanisms. This option is only limited by the loss of stiffness that will eventually result in a less accurate motion.
- The rigid construction of a gantry system must be designed to provide structural stability during printing operations and particularly during positioning moves. This reduces the risk of oscillations that will otherwise disturb the quality of the print.
- Offer open access to drive, bearing, and transmission parts. This makes gantry-based machines easier to maintain. Design that involves minimal moving parts and visible, accessible mechanisms also facilitates easier cleaning and inspection.
What Are the Disadvantages of Gantry the System for 3D Printing Projects?
Gantry systems have various advantages in 3D printer construction and operation, including:
- More complex and rigid gantry systems can be quite large and heavy. This makes them difficult to place and move and requires larger space for installation.
- Larger machines built using gantry systems can be more costly than other approaches to machine structure, because of their size and complexity.
- Machines with cube-form gantry systems can restrict user access to the print bed. This obstructs the removal of finished prints or makes necessary adjustments during the printing process difficult for users.
- Open gantry printers can produce more noise and vibrations during printing. Particularly in amplifying the resonance of stepper motors that are usually hard-mounted to the frame parts. This can be distracting or disruptive in otherwise quiet environments.
What Are the Different Types of Gantry Systems for 3D Printing?
There are a range of specific gantry systems that are employed across the 3D printing market. This includes:
1. Cartesian-XY-Head
A Cartesian-XY-head gantry system is a type of motion control system commonly used in 3D printers (and a wide variety of other classes of CNC machines). This construction approach moves the printhead or extruder along the X-axis of the gantry and moves the Y-axis by moving the entire gantry. This can involve moving a high mass on the Y-axis and may result in a greater risk of machine vibrations, especially during high acceleration maneuvers.
In such a gantry system, the print bed is fixed and the printhead or extruder moves along two perpendicular axes, typically running on ground shafts with recirculating ball linear bearings. Higher-priced versions often use V rails with externally V-grooved roller bearings as guides, resulting in reduced bearing wear. The X axis is usually defined as across the machine, while the Y axis is oriented backward/forwards relative to the device. The Z axis positions the vertical height of the printhead or extruder and is carried on the X motion of the gantry.
Cartesian-XY gantry systems are simple and easy to construct and operate. They also provide good precision and repeatability, allowing high-precision positioning of the printhead. However, they have limitations in terms of speed and acceleration and may lack stiffness in some respects.
2. Ultimaker-Style Crossed
The Ultimaker-style crossed gantry system is a mechanical structure and axis motion system less commonly used in 3D printing. It features two parallel gantries that position the printhead or extruder along the X and Y axes. The gantries are connected by a crossbar, which is intended to stabilize movement along both axes by sharing stiffness. The Z-axis motion is usually carried on these two axes, rather than delegated to a rising and falling print bed.
In this system, the print bed is typically fixed and stable. The printhead or extruder moves along both the X and Y axes. They are driven by stepper motors transmitting motion through toothed belts. The two gantries are able to move simultaneously. This allows for smooth curvature and jerk-free motion between print operations, as sudden directional changes are minimized. The approach also offers good stability during printing, benefitting the quality of printed outcomes.
This design approach is more complex and requires more effort in setup and calibration than simpler designs. This is particularly affected by the belt drives requiring very good alignment to ensure accurate and repeatable motion. Some users also report difficulty in accessing the print bed to make adjustments during printing, as the two gantries can block access at times during printing.
3. CoreXY
A CoreXY gantry system is a structure used in 3D printer design that has stationary stepper motors to drive the X and Y axes. This reduces the mass in motion in the gantry during Y-axis movements, as the Y-axis drive remains fixed in place. This enables higher acceleration and more precise movements of the printhead, providing higher-quality printed outcomes.
The CoreXY system works by using a series of pulleys and recirculating (loop) belts arranged so that the drive belts cross over each other at the core or center of the system. Driving the toothed belts moves the printhead in both the X and Y directions with lower inertia.
Moving less mass allows for a lighter gantry structure. There is less moving mass to resist at high acceleration moments. This approach is more sensitive to belt tension and slide condition than other systems and can be complex to set up and calibrate. The acceleration capacity is considered enough of an advantage to outweigh the setup issues, so this system is popular among some users in the more advanced category.
4. i3-Style Cartesian-XZ-Head
The i3-style Cartesian-XZ-Head is very widely used in 3D printer design. In this approach, the print platform itself is lifted and lowered (Z-axis motion), while the printhead is separately transported on the gantry for the X and Y axes. The extruder is mounted on a carriage that moves along the X and Y axes on precision-ground shafts, using recirculating ball bushes. On larger and higher-priced machines, the rails can be in V form, with roller bearings running on these rails.
This design is simple and easy to construct, making it a popular choice for home/hobby 3D printers. It delivers good accuracy and precision in smaller machines, but generally, it require moderation in acceleration and direction changes due to relatively low stiffness and high inertia.
The primary drawback to this design is that it can be very difficult to maintain a level bed and achieve consistent layer thicknesses. The poor rigidity, compared with other, higher-price 3D printer designs can have very significant effects at higher axis speeds/accelerations.
5. H-Bot
The H-bot is a gantry system employed in some 3D printers. It uses belt drives and linear rails in a layout that, similar to the CoreXY system, has stationary motors to drive the X and Y axes.
The two belts for X and Y form the shape of an "H." One belt is attached to the printhead and moves along the Y-axis. The other belt is attached to the other end of the gantry and moves along the X-axis. The printhead is carried on a Z drive that moves along the two main axis rails.
The H-bot layout can be more stable and rigid than other 3D printer designs, providing higher-quality printed outcomes. Stationary motors reduce the system inertia, allowing higher accelerations and requiring less stiffness for good stability.
The H-bot design is complicated to set up and hard to calibrate and is reported as requiring more maintenance. Any slight slack that develops in the belts will disrupt X-Y precision significantly, which is a particular issue in maintenance as belts can stretch. However, when well maintained, the H-bot is an effective gantry system that is capable of delivering high quality and high speed.
How Is a Gantry System Being Maintained?
3D printer axis drive systems need regular checks and maintenance to ensure effective operation. It is advisable to check with the OEM’s recommended maintenance procedure. Listed below are some general tips on how to maintain a gantry system:
- Check the drive belt tensions regularly. Overly tight belts cause excess wear, and loose belts influence accuracy and repeatability.
- Ensure all bearing surfaces are lubricated to maintain smooth motion and reduce wear. Use the manufacturer-recommended lubricant and don’t over-lubricate.
- Check drive belts for wear, fraying, cracking, and stretching.
- Ensure alignment of belt idler and drive pulleys. Misalignment will cause belts to slip or wear faster and could affect axis responsiveness or overheat motors.
- The temperature of the axis drive stepper motors can be an indicator of drive problems. Watching for hot motors can help warn the user of a range of issues.
- Clean the entire printer, particularly concentrating on the axis drive system. Most wear (and later failure) is a direct result of dirt in moving and bearing parts.
How Does a Gantry System Work for 3D Printing?
The gantry system provides the carriage and drive capability that moves the printhead. The specific process varies depending on the type of gantry system for 3D printing. Gantry systems in 3D printers fall into four basic categories:
- In desktop FDM/FFF printers, the gantry is often an arch that carries the printhead. It moves the printhead axially across the build table (in the X direction) and raises and lowers it (Z direction). The Y axis of motion is then handled by the movement of the build table. This allows the gantry to be stationary on the Y axis, reducing the need for structural stiffness.
- In other FDM/FFF printers, the Y axis is handled by moving the entire gantry in the Y axis. This requires that the gantry be stiffer in the Y direction, to avoid oscillation in the Y axis as it accelerates and decelerates.
- The stiffer form of gantry structure that will allow faster traverse without rocking or oscillation is a cube frame that holds the motion of all three axes rigid. This system is more commonly used on mid-size and larger machines. It can deliver faster motion and acceleration, with higher-precision printhead positioning results.
- The final form of structure that is essentially a gantry is a polar motion arm carrying the printhead. This is suited to larger build areas. It is only found at the higher-value end of the market. It is generally reserved for non-polymer-based print media, metals in particular, but also concrete printing.
What Are the Software for Robot Arm 3D Printing?
The momentum toward robot-arm-based 3D printing is increasing. Various software packages are available to help in the process of driving the robot through multi-axis routing. This delivers 3D prints that are constructed with the truly 3D application of build material, rather than the slice-by-slice approach that is required in orthogonal printing systems. Examples of software to perform this process are:
- Robotmaster
- AI Build
- Adaxis
For more information, see our guide on the Best 3D Printing Software.
How Long Does 3D Printing Gantry Systems Could Last?
Gantry-based 3D printers can have an essentially unlimited functional lifetime, with conditions. These conditions are: maintenance is regular and thorough, parts remain available, and there is a commercial value in performing the required maintenance and repairs. Gantry-based 3D printers are a collation of functional and structural parts, and the overall durability of the system depends on the weakest link.
Is Gantry System Able to Print Houses?
3D printing can undertake some aspects of house building. The 3D printing of large structures like houses is an area of increasing research and early attempts at commercialization. There are good reasons to think that this is how some houses will be built, within the foreseeable future.
The 3D printer systems used to perform this task use a form of FDM/FFF printing, extruding a bead of concrete as a filament, from which a complete structure can be printed. Some aspects are currently performed by manual intervention. Items such as window and door lintels must be fitted by hand, as no “support” printing under overhangs is currently possible.
The approaches currently being taken can only print vertical walls and cannot handle roof structures. All other aspects—from plumbing and electrical, through window installation and lining and all finishing tasks are manual, with no immediate prospect of automating these.
For more information, see our guide on 3D Printing in Construction.
Does Gantry System Have Limited Printable Area?
Yes, there is a very restricted volume within the gantry that is printable. The gantry is a structure that generally sits considerably outside the printable area/volume of a typical 3D print machine. These machines cannot reach even the inner extent of the gantry to print, as there are machine and structural elements that limit the reach.
Do Gantry Systems Depend on 3D Software for Quality?
Yes, gantry systems depend on 3D software for quality. Any printer must have a software component in the preparatory process that turns the desired 3D model into a series of direct instructions. These can be used to drive axis motors and material feeds, heaters, blowers, and other functions of the printer.
What Is the Difference Between Gantry System From Gantry System for 3D Printing?
There are a few major differences between the different gantry systems available for 3D printing. There are various types of gantry systems employed in the construction of 3D printers, each with its own strengths and shortcomings. The main differences are:
- Stiffness: Additional flexibility reduces the acceleration tolerance of a printer, as high accelerations will disrupt the structure and induce vibrations/oscillations that can disturb the printing process.
- Weight: Higher machine weight can be an advantage in assisting with stability. Higher moving parts weight, however, requires larger drive forces and greater stiffness to avoid shaking at acceleration points or direction changes.
- Cost: Lighter and simpler structures cost less, but insufficient structure will result in low accuracy and poor performance.
- Maintenance: Some gantry systems allow for easy maintenance, while others can make the process much more difficult.
For more information, see our guide on Robotic Arm vs. Gantry Systems for 3D Printing.
Summary
This article presented gantry systems, explained what they are, and discussed how they work and the various types. To learn more about gantry systems, contact a Xometry representative.
Xometry provides a wide range of manufacturing capabilities, including 3D printing and other value-added services for all of your prototyping and production needs. Visit our website to learn more or to request a free, no-obligation quote.
Copyright and Trademark Notices
- OBJET® is a registered trademark of Stratasys, Inc.
Disclaimer
The content appearing on this webpage is for informational purposes only. Xometry makes no representation or warranty of any kind, be it expressed or implied, as to the accuracy, completeness, or validity of the information. Any performance parameters, geometric tolerances, specific design features, quality and types of materials, or processes should not be inferred to represent what will be delivered by third-party suppliers or manufacturers through Xometry’s network. Buyers seeking quotes for parts are responsible for defining the specific requirements for those parts. Please refer to our terms and conditions for more information.
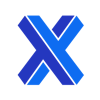