Nylon 3D Printing Service
Get instant online quotes on parts in nylon materials. Free shipping on all US orders. ISO 9001:2015, ISO 13485 and AS9100D certified.
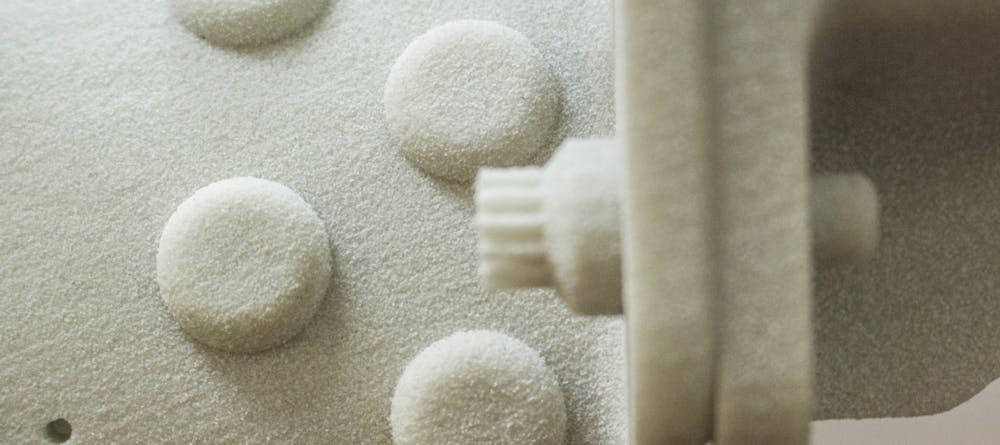
About 3D Printing Nylon
3D printed nylon comes in many different forms, namely as a filament for FDM (fused deposition modeling) or as a powder for SLS (selective laser sintering) and MJF (HP Multi Jet Fusion) printing. 3D printing nylon creates parts with excellent properties but it’s important to understand that the type of 3D printing process will determine the final part capabilities. For example, FDM prints will have an anisotropic structure caused by the extruded layer lines. Even SLS-printed parts will have a level of anisotropy between layers. MJF parts tend to have isotropic properties, meaning the material will behave the same regardless of the direction of the load. However, with correct setups and part orientation, anisotropic effects can largely be negated and parts can benefit from the excellent properties of nylon.
Nylon is a high-performance engineering thermoplastic found in a wide range of industries. Its popular usage stems from its excellent abrasion resistance, high fatigue resistance, and high load-bearing capacity. Due to these properties, 3D printing in nylon is a great way to make lightweight industrial and medical implements that are just as capable as heavier metal ones.
Nylon 3D Printing Materials
Xometry’s custom nylon 3D printing service is offered in a wide range of nylon materials, including MJF nylon 11 EX, FDM nylon 12, SLS nylon 12, and many more.
Tensile Strength (MPa) | Elongation at Break (%) | Hardness (Shore D) | Heat Deflection Temperature (℃) | Melting Point (℃) |
---|---|---|---|---|
Tensile Strength (MPa) 52 | Elongation at Break (%) 55 | Hardness (Shore D) 80 | Heat Deflection Temperature (℃) 185 | Melting Point (℃) 202 |
Tensile Strength (MPa) | Elongation at Break (%) | Hardness (Shore D) | Heat Deflection Temperature (℃) | Melting Point (℃) |
---|---|---|---|---|
Tensile Strength (MPa) 48 | Elongation at Break (%) 20 | Hardness (Shore D) 80 | Heat Deflection Temperature (℃) 175 | Melting Point (℃) 187 |
Tensile Strength, Yield (MPa) | Elongation at Break (%) | Hardness (Shore D) | Heat Deflection Temperature (℃) | Melting Point (℃) |
---|---|---|---|---|
Tensile Strength, Yield (MPa) 30 | Elongation at Break (%) 10 | Hardness (Shore D) 82 | Heat Deflection Temperature (℃) 174 | Melting Point (℃) 186 |
Tensile Strength (MPa) | Elongation at Break (%) | Hardness (Shore D) | Heat Deflection Temperature (℃) | Melting Point (℃) |
---|---|---|---|---|
Tensile Strength (MPa) 32 | Elongation at Break (%) 30 | Hardness (Shore D) N/A | Heat Deflection Temperature (℃) 75 | Melting Point (℃) 178 |
SLS Nylon 12 (PA 2200)
Much like its MJF counterpart, this SLS nylon offers good dimensional stability and maintains its properties over a long period of time. It does have a higher level of anisotropy than MJF and this must be taken into account when designing parts using this material. The upside is that it exhibits greater tensile strength than MJF nylon 12 version.
Tensile Strength (MPa) | Elongation at Break (%) | Hardness (Shore D) | Heat Deflection Temperature (℃) | Melting Point (℃) |
---|---|---|---|---|
Tensile Strength (MPa) 48 | Elongation at Break (%) 18 | Hardness (Shore D) 75 | Heat Deflection Temperature (℃) 154 | Melting Point (℃) 176 |
Tensile Strength (MPa) | Elongation at Break (%) | Hardness (Shore D) | Heat Deflection Temperature (℃) | Melting Point (℃) |
---|---|---|---|---|
Tensile Strength (MPa) 38.1 | Elongation at Break (%) 2 | Hardness (Shore D) 80 | Heat Deflection Temperature (℃) 179 | Melting Point (℃) 185 |
SLS Nylon 12 AF (PA 605-A)
This nylon for SLS printing has the unique property of being aluminum-filled and thus creates parts with a surface finish similar to cast aluminum, also gaining much of the metal’s excellent thermal conductivity. This makes it ideal for tooling, fixtures, or automotive components that get exposed to elevated temperatures.
Tensile Strength, Yield (MPa) | Elongation at Break (%) | Hardness (Shore D) | Heat Deflection Temperature (℃) | Melting Point (℃) |
---|---|---|---|---|
Tensile Strength, Yield (MPa) N/A | Elongation at Break (%) 3 | Hardness (Shore D) 76D | Heat Deflection Temperature (℃) 180 | Melting Point (℃) 181 |
SLS Nylon 12 CF (PA 602-CF)
This nylon for SLS printing uses carbon as its filler material. This has the benefit of stiffening the material and reducing overall part weight while also being highly resistant to warping at high temperatures. This makes it ideal for applications that demand low weight like sports equipment or racing components.
Ultimate Tensile Strength (MPa) | Elongation at Break (%) | Hardness (Shore D) | Heat Deflection Temperature (℃) | Glass Transition Temperature (℃) |
---|---|---|---|---|
Ultimate Tensile Strength (MPa) 85 | Elongation at Break (%) 4 | Hardness (Shore D) N/A | Heat Deflection Temperature (℃) 179 | Glass Transition Temperature (℃) N/A |
Ultimate Tensile Strength (MPa) | Elongation at Break (%) | Hardness (Brinell) | Heat Deflection Temperature (℃) | Melting Point (℃) |
---|---|---|---|---|
Ultimate Tensile Strength (MPa) 51 | Elongation at Break (%) 5 | Hardness (Brinell) 75 | Heat Deflection Temperature (℃) 184 | Melting Point (℃) 184 |
Finishes
Xometry offers a wide range of surface finishes for printing nylon, some of which are listed below. Follow this link to learn about our other finishing options.
Standard: This type of finish is possible for all 3D printing technologies listed above. Printing supports are removed from the part, but no additional work is done to the finish. Note that SLS and MJF parts have much better off-the-machine finishes than FDM and do not require the removal of support structures.
Nickel plating: This surface treatment is not for cosmetic applications as it creates a rough nickel finish. However, it adds additional durability, stiffness, and wear resistance. This finish is only available for SLS nylon parts.
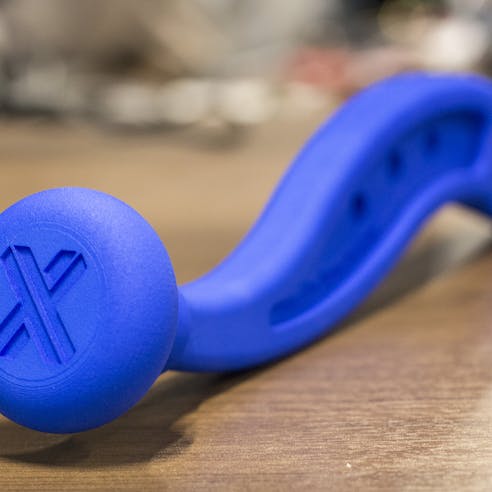
Cost-saving Design Tips
DFM: Each type of 3D printing technology requires special considerations during the design phase. FDM parts, for example, may need additional support as well as consideration for which layer orientation will generate maximum strength. SLS parts need drain holes to remove unused powder from internal cavities. Design-for-manufacturability (DFM) principles need to be applied from the start.
Choose the right plastic and process: Each of the above plastics and machine combinations is better suited to certain applications. If the goal is to produce a temporary tooling jig then FDM may be the best option. However, if a visual prototype is required, then SLS or MJF may better suit your needs.
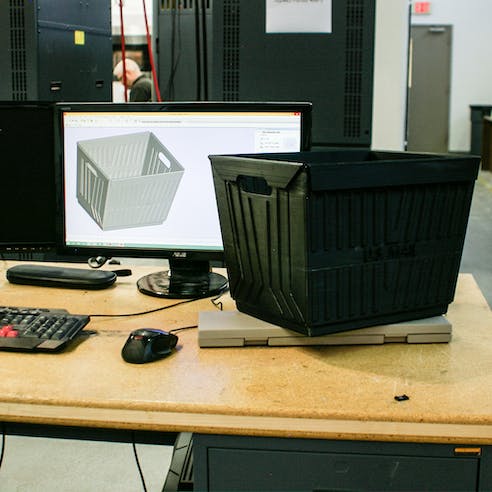