HDPE Injection Molding Services
Get custom HDPE injection molded prototypes and production parts in as few as five business days. Dozens of materials and finishes are available.
Xometry offers the highest quality HDPE injection molding service and is able to assist with the design of the part and tooling to ensure it follows DFM (Design for Manufacturing) best practices. This will help ensure the product can be successfully manufactured with no defects. Thereafter, Xometry can facilitate manufacturing with one of our trusted partners to ensure the parts are produced to the required specifications. HDPE is a popular injection molding material as it has excellent processability. HDPE also has a low moisture absorption rate and is lightweight, making it ideal for a wide range of applications.
What Is High-Density Polyethylene (HDPE)?
High-Density Polyethylene (HDPE) is a thermoplastic polymer supplied in pellet form for injection molding. HDPE is widely used for injection molding due to its low cost, chemical resistance, high tensile strength, impact resistance, and low moisture absorption. In addition to its physical properties, HDPE has excellent processability due to its relatively low melt temperature and low viscosity.
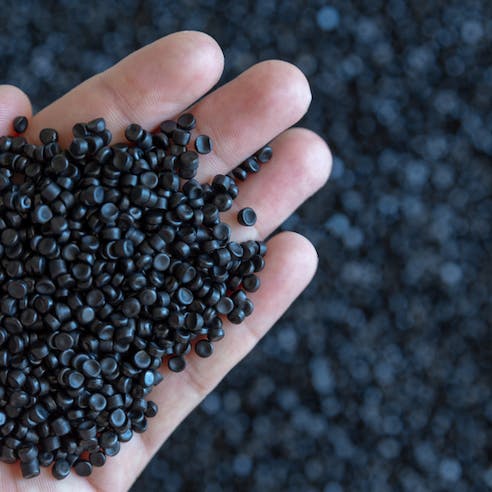
Injection Molded HDPE Material Properties
Each HDPE formulation will have a unique set of material properties depending on their intended application. Table 1 below lists some common material properties of standard HDPE:
Chemical Formula | (C2H4)n |
Color | Naturally translucent with a milky white appearance. Can be colored using pigmentation additives. |
Density (g/cm3) | 0.96 |
Melting Point (°C) | 126–135 |
Ultimate Tensile Strength (MPa) | 31.7 |
Izod Impact (Notched) (J/cm) | 0.69 |
Hardness (Shore D) | 70 |
Max Service Temperature (Air) (°C) | 71.1 |
Melting Temperature (°C) | 180–205 |
UV Resistance | Poor without additives |
Chemical Resistance | Resistant to diluted and concentrated acids like hydrochloric acid as well as some reducing agents and oxidants. |
Water Absorption (ASTM D570) (% by weight) | 0.1 |
Table Credit: https://matweb.com/
Advantages of HDPE Injection Molding
HDPE is a popular injection molding material due to its many advantages, some of which are listed below:
- Weather-Resistance
- Lightweight
- Cost-Effective
- Recyclable
- FDA-Approved
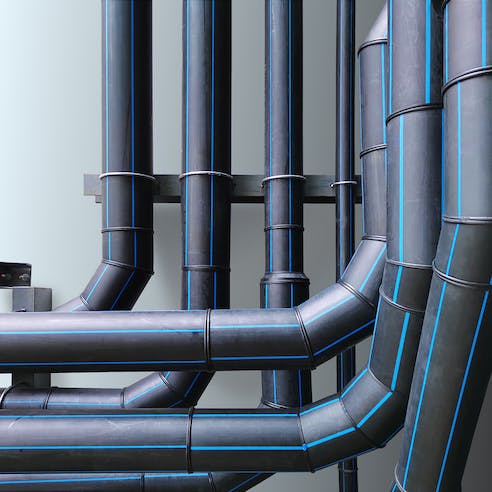
Weather-Resistance
HDPE is highly resistant to moisture ingress. Also, with the addition of UV (ultraviolet) stabilizers, HDPE can be made resistant to UV radiation, making it an ideal material for outdoor applications.
Lightweight
HDPE has a density of around 960 kg/m3. This is lightweight compared to metals and even some plastics. HDPE also has a high strength-to-weight ratio which means it can be used to produce thin-walled products like bottles or chemical tanks but still maintain high levels of strength and rigidity.
Cost-Effective
HDPE is considered a commodity plastic and is relatively low-cost when compared to other plastics like polypropylene, for example. This makes it a cost-effective material to use for injection molded products. It must, however, be noted that the tooling required for injection molding is often the largest contributor to initial set-up cost.
Recyclable
HDPE is a thermoplastic. It can be remelted and reused if properly processed at a recycling plant. Most recycling plants will accept HDPE due to its widespread use, in addition to HDPE being one of the easiest plastics to recycle. HDPE can also be downcycled, i.e., reused on lower-value items like imitation plastic lumber.
FDA-Approved
HDPE is considered food-safe by the FDA (Food and Drug Administration) and is widely used to store food items. HDPE is highly inert and stable and as such does not leach dangerous chemicals into food products.
Ready to make custom HDPE injection molded parts?
Disadvantages of HDPE Injection Molding
Despite its many advantages, HDPE has some disadvantages as listed below:
- Poor UV Resistance
- High Shrinkage
- Susceptible to Environmental Stress Cracking
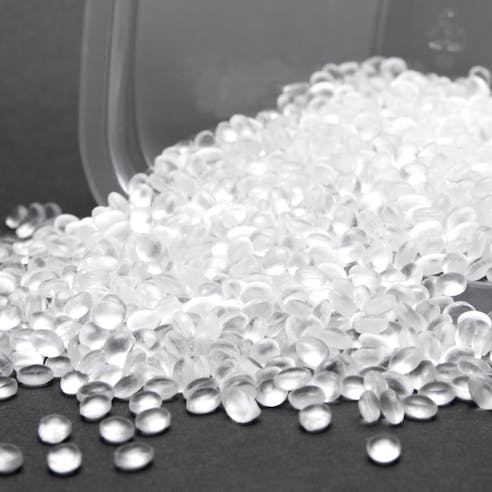
Poor UV Resistance
HDPE has poor UV resistance as the carbon-hydrogen bonds are attacked by UV radiation. The breaking of these bonds ultimately causes photo-oxidation which degrades the material over time. Additives like UV stabilizers can be incorporated into the HDPE formulation to improve its UV resistance.
High Shrinkage
HDPE has low thermal conductivity. If cooling is too quick or uneven, this can result in the part warping or shrinking during injection molding. HDPE can have a shrinkage rate of between 1.5% and 4.0%.
Susceptible to Environmental Stress Cracking
HDPE is susceptible to environmental stress cracking. When exposed to long-term tensile loads, cracks can form in the material. This is further exacerbated if the HDPE is exposed to a corrosive environment. These cracks can develop at loads much lower than the tensile strength of the material.
Applications of HDPE Injection Molding
Listed below are some common uses for injection molded HDPE:
- Hard Hats
- Plastic Piping
- Plastic Bottles
- Food Storage Containers
- Furniture
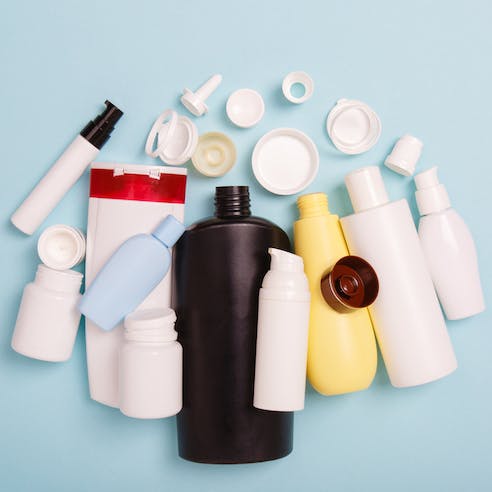
Hard Hats
Hard hats must be able to withstand sudden impacts and must also absorb as much of the impact energy as possible. As such, HDPE is an excellent choice for hard hats as it is a highly durable and impact-resistant material.
Plastic Piping
HDPE is highly resistant to moisture and is relatively flexible. As such, it is widely used for piping to transport large volumes of water. Individual pipe sections are welded together to eliminate potential leaks. These pipes are often buried underground.
Plastic Bottles
Plastic bottles are one of the most popular uses for HDPE. While most bottles are formed using blow molding techniques, the blank tubes used to make these bottles must be injection molded. HDPE does not leach into the stored liquid and is highly moisture-resistant, making it ideal for bottling applications.
Food Storage Containers
HDPE is considered food-safe and is approved by the FDA. It is widely used for both single-use and long-term food storage applications. In addition, HDPE is very tough and can protect the food contents during transportation.
Furniture
HDPE is a popular material for garden furniture due to its low cost. The strength and toughness of HDPE make it possible to produce lightweight and low-cost furniture without compromising mechanical strength. HDPE can also be downcycled for use in imitation lumber that can be used to produce low-cost furniture.
Alternatives to HDPE Injection Molding
Injection molding HDPE requires a large amount of initial capital investment as the tooling can be very expensive. It is only cost-effective for larger production volumes. Listed below are two potential alternatives to HDPE injection molding:
- Vacuum Forming
- CNC Machining
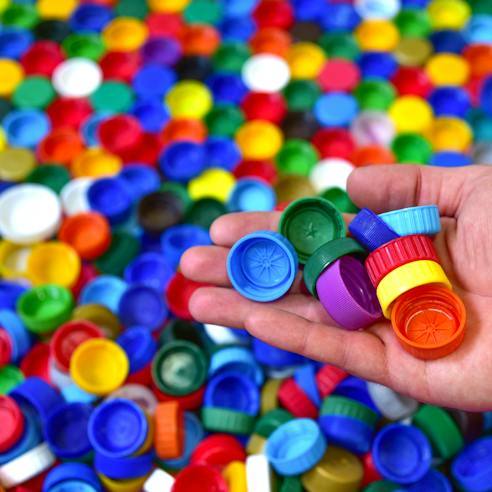
- Vacuum Forming: Vacuum forming can be used to manufacture hollow components cost-effectively. This process can be used to create boat hulls or chemical storage tanks.
- Plastic Machining: HDPE can be machined. This is especially useful for complex parts with relatively low volumes. HDPE machines easily so do not cause significant wear on tooling.
- Plastic Extrusion: Plastic extrusion can be used to manufacture components with a constant cross section. Tooling costs are also significantly lower when compared to injection molding.
Why Choose Xomety for HDPE Injection Molding?
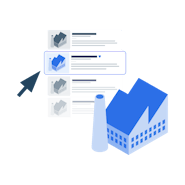
Endless Options
Choose from millions of possible combinations of materials, finishes, tolerances, markings, and certifications for your order.
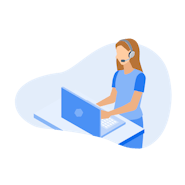
Easy to Use
Get your parts delivered right to your door without the hassle of sourcing, project management, logistics, or shipping.
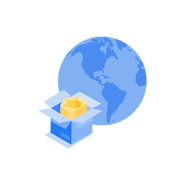
Quality Assurance
We are ISO 9001:2015, ISO 13485 and AS9100D certified.