Surface Grinding Service by Xometry
High-quality Surface Grinding Services in Days Not Weeks | Free Standard Shipping on All US Orders | Subject to availability. Xometry doesn't guarantee that we can provide this service at any given time.
Xometry offers the highest standard of precision among surface grinding operations. Surface grinding is a precision machining process that very precisely removes small amounts of material from the surface of a workpiece. Such machines make multiple passes with a high-speed grinding wheel made of silicon carbide, aluminum oxide, or carborundum powders bonded into a porous and refreshable surface of extreme particulate hardness.
Xometry can create excellent flat surface finishes on hard materials such as normalized and hardened steels and stainless steels. The process also has some value for other materials such as brass, aluminum, and even certain plastics — although many softer materials clog the pores in the grinding wheel and then cause spalling and gouging that destroys the surface.
What Is Surface Grinding?
Surface grinding is an aggressive and highly controlled interaction between a rotating grinding wheel and the workpiece. The grinding wheel, typically composed of abrasive particles of aluminum oxide, silicon carbide, or carborundum, is mounted on a spindle and rotates at high speeds. The workpiece is securely held on a magnetic chuck or a clamping fixture and is fed against the rotating grinding wheel. The wheel is generally mounted on a horizontal axis so its dressed cutting face can be lowered onto the workpiece’s surface. You may also find vertically mounted wheels meant to grind side faces, but they’re less common.
Most grinders mount the grinding wheel on a fixed shaft that moves only in the Z direction. The workpiece clamping table below moves on the horizontal plane and can place any portion of the workpiece’s upper surface in contact with the grinding wheel.
Another common operational mode is to position the part between a grinding wheel and a traction/feed wheel. The feed wheel pushes the workpiece against the grinding wheel. This style is advantageous because the grinding wheels can be very wide and remove large swathes of material at a time.
A grinding wheel's abrasive particles act as minute cutting tools, gradually abrading the surface of the workpiece. It removes material through a combination of cutting, plowing, and rubbing actions. Since grinding generates considerable heat, the operation demands flowing coolant or other cooling methods to prevent overheating and damage to the workpiece.
By ‘dressing’ the surface of the grinding wheel, i.e. abrading away a layer of the abrasive particles of the wheel using a diamond bit, the wheel’s surface can be rendered flat in the axial direction. Multiple passes across a workpiece can then create a surface that’s equally flat.
Types of Materials for Surface Grinding
Listed below are some of the materials that accept surface grinding:
- Aluminum
- Brass
- Cast Iron
- Mild Steel
- Stainless Steel
- Plastic
- Titanium
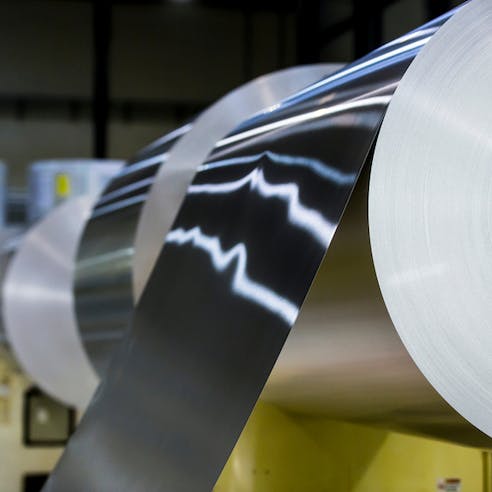
Aluminum
Surface grinding is not widely employed on aluminum parts. If the ‘ground’ surface finish is desired, this metal usually responds better to an abrasive particle-coated fabric belt, creating a so-called brushed aluminum surface. There are, however, ways to avoid the spalling that often mars ground aluminum surfaces. Some useful tips are:
- Use a porous, open-structured silicon carbide wheel.
- Dress the wheel freshly and be prepared to re-dress it if the work is extensive.
- Forestall clogging by rubbing the wheel surface with wax. This will fill in the pores with non-abrasive material rather than allowing them to collect metal shavings and cause spalling.
- Run the wheel at high speed and use very shallow cut depths on each pass.
- Run high coolant levels to flush debris aggressively away from the cut and reduce the chances of localized melting.
Brass
Brass can be surface ground effectively. This material poses similar clogging issues to aluminum, but they are less severe. Some useful tips to follow are:
- Silicon carbide wheels are more effective than aluminum oxide or carborundum.
- Shallow cuts are most effective, despite longer processing time.
- Results usually improve with faster wheel rotation and slower feed rates.
- Use coolant to clear cuttings effectively.
Cast Iron
Cast iron is among the most common targets for surface grinding. Cast Iron machine beds and slideways must have very smooth, flat surfaces. The grind is commonly followed by lapping and honing to further improve the finish. All forms of cast iron (nodular, grey, ductile) respond well to grinding.
Mild Steel
Mild steel responds well to surface grinding, although it is not common to use such a high-precision process on relatively low-quality material. An application that might require surface grinding is the manufacture of shaft keys such as woodruffs. These parts are designed to fail in shear, so they must resist shear less than the shaft/collar materials they lock together. Nevertheless, they still need to fit precisely and lock the shaft into a rotational position. Surface grinding the raw stock will provide that precision.
Stainless Steel
All stainless steels respond very well to surface grinding, although excessive heat buildup must be avoided if the material's hardness is to be unaffected. Many stainless plates are hard to machine, as they work harden at the cut and can adversely affect cutter sharpness. Grinding offers a way to machine stainless steel that does not suffer from this. Stainless steel slides and plain bearing surfaces for gas turbine engines often get a surface grinding treatment.
Plastic
Plastic components can be surface ground, although many polymers are too soft to respond well to the process. It is most common to grind thermoset polymers such as hard urethanes and epoxy resins.
The main reason for grinding plastic parts is cosmetic, or because additives within the material (such as high glass content) make other machining processes less feasible. Grinding is also a good way to give Nylon bearings the accuracy they need.
Titanium
Titanium is a difficult material to surface grind, as it tends to clog the wheel pores. However, grinding is still a useful technique for titanium alloys because they naturally work-harden and can have serious adverse reactions to some cutting tool materials — particularly cermets. Titanium is often ground for precision and flatness in the medical and aerospace sectors.
Advantages of Surface Grinding
Surface grinding offers several benefits across the manufacturing sector:
- Environment-Friendly
- High Accuracy
- Smooth Finish
- Tight Tolerances
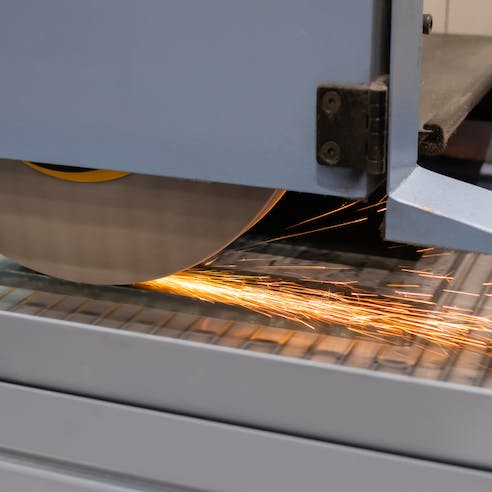
Environment-Friendly
Surface grinding, by nature, generates little in the way of pollution. The cutting swarf is essentially inert and washed off the part by coolant. It’s then filtered out and disposed of carefully. Energy requirements are lower than for some machining types. The machines rarely give off fumes and are even relatively quiet.
High Accuracy
Surface grinding can be used to trim parts to extremely precise dimensions. One approach starts by removing half of the planned material in the first pass, followed by half of the remainder, etc. Each pass removes half as much as the one before until the difference is so small as to be negligible. It creates an extremely precise tolerance.
Smooth Finish
Surface grinding can produce a smooth, flat, and high-quality surface finish on a workpiece that is otherwise very hard to perfect. Grinders can meet precise tolerances and very low roughness levels. Such perfection may be necessary for reference faces or in slideways and plane bearings.
Tight Tolerances
It is relatively easy to make cuts that meet half-micrometer tolerances via grinding. However, the process is not designed to remove large amounts of material. It should be considered a final stage in creating precision in parts rather than a bulk processing method.
In need of custom surface grinding services?
Disadvantages of Surface Grinding
Listed below are some of the disadvantages of surface grinding:
- Costly
- Surface Contaminants
- Local Heat Effects
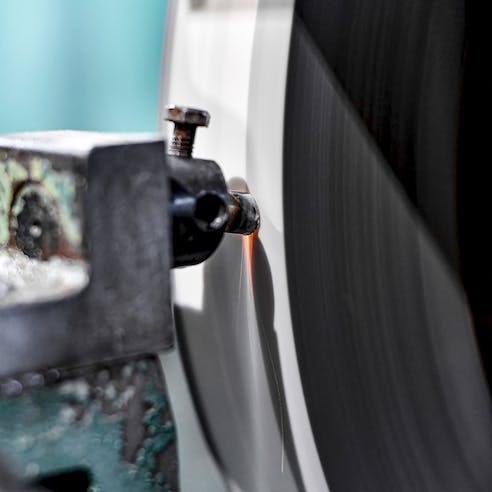
Costly
Surface grinding equipment is very precise and therefore costly.
Surface Contaminants
Residual abrasives embedded in the surface can disrupt the formation of a protective oxide film in stainless steel. This can invite corrosion when equipment is exposed to aggressive environments. These residual contaminants make surface grinding unacceptable as a finishing process for pharmaceutical processing equipment, among other sectors.
Local Heat Effects
Poor coolant supply and/or excessive cut depth can heat the workpiece enough to disrupt previous hardening effects. In the case of slides and plane bearings, that will compromise their resiliency.
Other Grinding Capabilities by Xometry
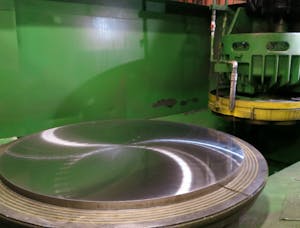
Blanchard Grinding Services
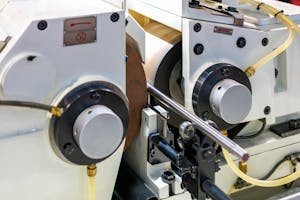
Centerless Grinding Services
Alternatives to Surface Grinding
Xometry offers several alternative finishing options to surface grinding, though they’re typically not as precise:
- Electropolishing
- Linishing
- As-Machined
- Grit Blasting
- Lapping/Honing/Scraping
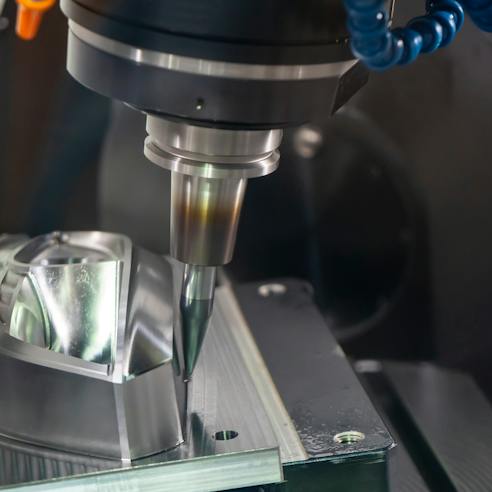
- Electropolishing: Electropolishing uses electrolytic erosion of the surface to remove a very fine layer of material. This will not improve the flatness of a part/surface but it can create a higher-quality surface finish.
- Linishing: This uses an abrasive belt to buff away the workpiece’s surface. This method cannot flatten it the way surface grinding does but can create a similar appearance.
- As-Machined: CNC milling devices can create very flat vertical and horizontal surfaces, though machining marks will remain.
- Grit Blasting: This will remove a fine surface layer and can leave an attractive surface, though it is of no use as a flattening process.
- Lapping/Honing/Scraping: These are the traditional techniques for flattening surfaces such as slideways in machine tools and measurement reference surfaces. These techniques can, in highly skilled hands, even out high and low points on a surface and produce outstanding flatness. However, the results depend heavily on the operator’s skill.
Why Choose Xometry for Surface Grinding Services?
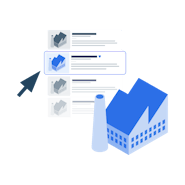
Endless Options
Choose from millions of possible combinations of materials, finishes, tolerances, markings, and certifications for your order.
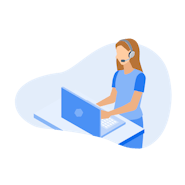
Easy to Use
Get started with our easy-to-use platform and let our experts take care of managing the project from locating the right manufacturing partner to delivery logistics.
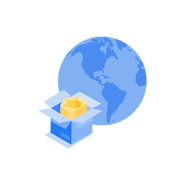
Vetted Network
We are ISO 9001:2015, ISO 13485, and AS9100D certified. Only the top shops that apply to become Suppliers make it through our qualification process.