Custom Hydroforming Services by Xometry
High quality hydroformed parts for use in your production projects. Subject to availability. Xometry doesn't guarantee that we can provide this service at any given time.
Xometry offers hydroforming services for a variety of metals and applications. Hydroforming is a specialized type of metal fabrication process where pressurized water forces sheet stock into predefined complex shapes. It is a deep drawing process where sheet stock is converted into single-stock metal parts in just a few minutes. Hydroforming creates uniform walls and sharp features and curvatures with even heavy gauge metal and is very popular for its extreme accuracy and repeatability. Hydroforming implements various materials including steel, stainless steel, aluminum, brass, copper, and many other alloys. Applications of hydroforming in industry include unibody automotive components, appliances, large metal fixtures, housings, aerospace parts, and much more.
What is Hydroforming?
Unlike stamping, die forming, and other metal forming techniques, hydroforming uses hydraulic fluid pressure to create weldless metal shapes. A piece of sheet metal is placed between a press, where one side contains a male die element (or punch) connected to a piston and the other side contains a chamber that will contain the hydraulic fluid. A rubber diaphragm and a wear pad are placed on top of the sheet metal, and the press is closed. The chamber is then pressurized with hydraulic fluid and the piston forces the punch into the pressurized cavity, creating a consistent deep-drawn profile in the shape of the punch. The rubber diaphragm and wear pad eliminate the scrapes and scratches typically associated with metal stamping procedures, and also support the part surface to ensure uniformity. After forming, the part is removed from the press and is ready for tapping, drilling, and other secondary processes and finishes.
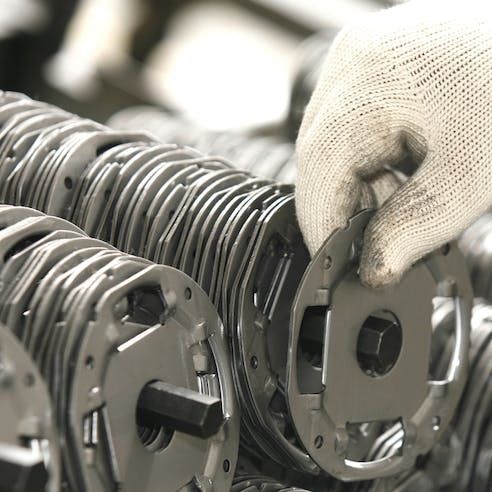
Advantages of Hydroforming Services
- Fast lead times
- High volume production
- Accuracy and repeatability
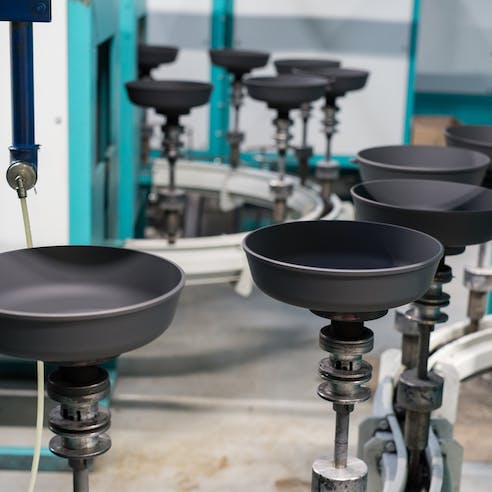
Fast lead times
Cycle times for hydroforming can be as quick as 30-60 seconds, meaning that parts leave our workshops as quickly as they arrive. Xometry’s Manufacturing Partner Network provides some of the fastest turnaround times available, putting parts in customers’ hands in as soon as a few days around the globe. Speed up your completion time by making parts with Xometry, freeing up business resources for more pressing matters (pun intended).
High volume production
Hydroforming is an ideal manufacturing process for high-volume parts production. Xometry’s hydroforming services start at hundreds of parts for larger designs and thousands of parts for smaller ones, allowing designers to make their money back on initial upfront tooling and designing expenses.
Accuracy and repeatability
Hydroforming is widely known for extreme accuracy and repeatability, as the process increases wall thickness uniformity and decreases defects like shock lines, draw lines, sheering, tearing, and others.
Hydroforming Materials
Hydroforming is typically used with ductile metals, but high-strength metals are also possible thanks to the increased control of pressurized fluid on the metal. Common materials include:
- Aluminum
- Stainless Steel
- Brass
- Bronze
- Carbon Steel / Stainless Steel, including 304, 316 and 409, 17-4, 17-7
- Copper
- Inconel
- High Nickel Alloys
- Titanium Grade 5, Grade 2
- Galvanized Steel
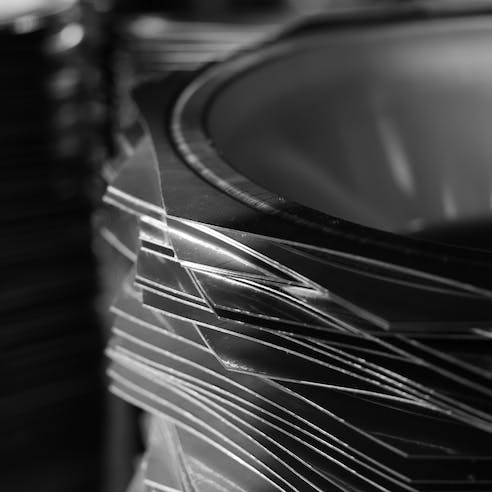
Hydroforming Shapes
Hydroforming can shape metals into precision parts that other job shops find difficult to produce. With hydroforming, Xometry can create complex shapes such as:
- Square enclosures
- Elliptical/Oval Shapes
- Parabolic Contours
- Irregular/ Asymmetric Shapes
- Multi-Layered Shapes
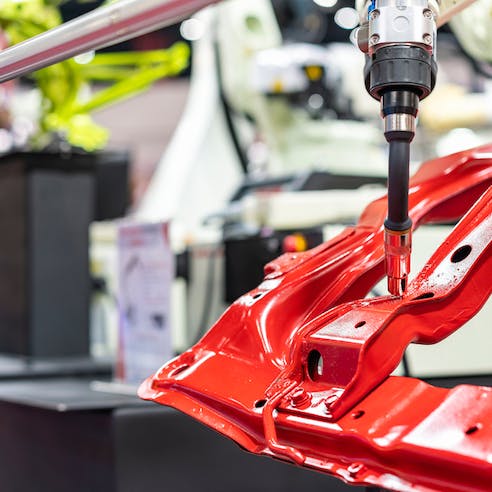
Ready to order custom hydroformed parts?
Hydroforming Industries
- Aircraft and Aerospace Industry
- Automotive
- Cookware
- Medical Industry
- Industrial Equipment
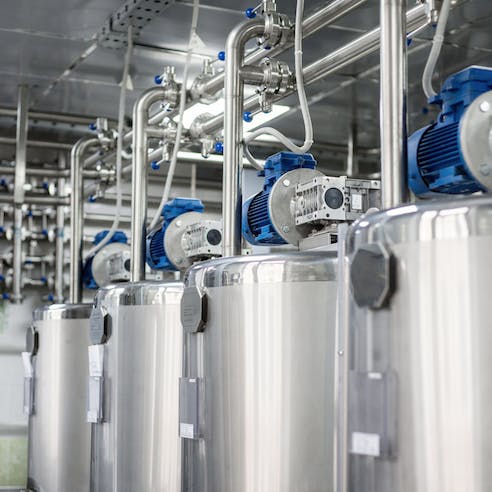
Aircraft and Aerospace Industry
The aerospace industry often requires complex shapes built from a single stock piece and other hig quality components that can survive extreme temperature and environmental changes. Hydroformed parts not only improve the structural integrity of parts by more regularly deforming material, but it also allows for the production on unibody parts built from high strength metals like titanium, aircraft aluminum, and other metals commonly used throughout the aerospace industry.
Automotive
The top application of hydroforming is in automotive manufacturing lines, as its quality and repeatability are ideal for large unibody components like panels, hoods, and other parts. Hydroformed parts are stronger and more uniform than other drawn or stamped metal parts and help keep both the cost and risk of part failure to a minimum. Since hydroforming is also a cold forming process, it allows for secondary heat treating procedures necessary for high-strength applications sucdhcas car frames and other structural components.
Cookware
Food processing equipment and food service parts are hydroformed to allow for manufacturer-specific design choices like asymmetrical inlet and outlets, piping, and more.
Medical Industry
Medical devices that require strong vessels such as medical pumps benefit from hydroforming to create the highly complex designs found in such applications. Xometry’s ISO 13485 certification means we are able to produce medical-grade parts with the high precision needed for these demanding products.
Industrial Equipment
Air ducts, HVAC equipment, plumbing stock, agricultural components, heat exchangers, and many other pieces of industrial equipment are hydroformed in industry to ensure these components meet or exceed national standards and safety regulations. The accuracy and reliability of hydroforming ensure each tool will not deviate from others in its manufacturing batch while also providing unmatched consistency and quality.
Hydroforming vs. Metal Spinning vs. Deep Drawing
Hydroforming involves using hydraulic pressure to evenly distribute pressing forces onto metal stock using equipment called fluid dies, forcing it into the desired shape of the male tooling. Materials such as mild steel up to high temperature alloys and superalloys can be used with hydroforming. Hydroforming is best suited for asymmetrical complex shapes that are difficult or impoassible to produce using other simpler techniques. The highly pressurized fluid of hydroforming allows for much more complex shapes, where hydroforming companies can meet exact specifications and tolerances thanks to the uniform effects of pressurized fluid shaping.
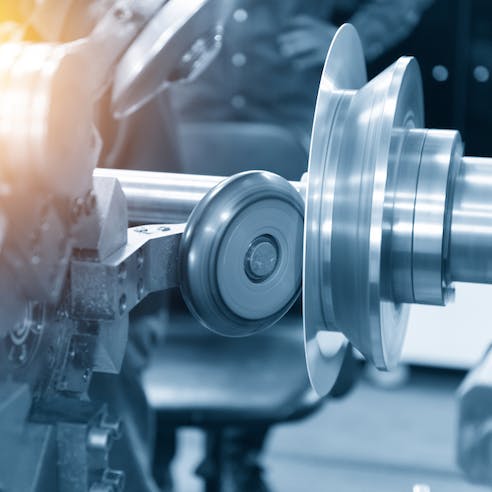
On the other hand, sheet metal spinning, stainless steel spinning, or more simply metal spinning is a metal forming technique where a disc of sheet metal is rotated at high speeds and pressed onto an axially-symetric mandrel in the shape of the end part (typically a bowl-like tool). Spun metal shapes are typically less complex and implement manual or CNC spinning equipment. Various spun metal shapes are used in decorative, architectural, or furniture applications, or can be used to make nose cones for rockets and planes, but can never be used to make asymmetrical designs. While users get minimal tooling costs with metal spinning, the variable cost per-part is higher than with hydroforming.
Deep drawing is a cold forming metalworking process that progressively forces a punch through a series of forming dies, creating a deep, weldless shape with little to no material loss. Best suited for simplistic, axially-symmetrical parts, deep drawing isa regularly used for pressure vessels and other tanks that require no seams or weld lines that could potentially be points of failure.
Alternatives to Hydroforming
Xometry has additional manufacturing processes if hydroforming does not fit your intended application. Below are some common alternatives to hydroforming.
- Metal Stamping
- Die Casting
- Metal Injection Molding
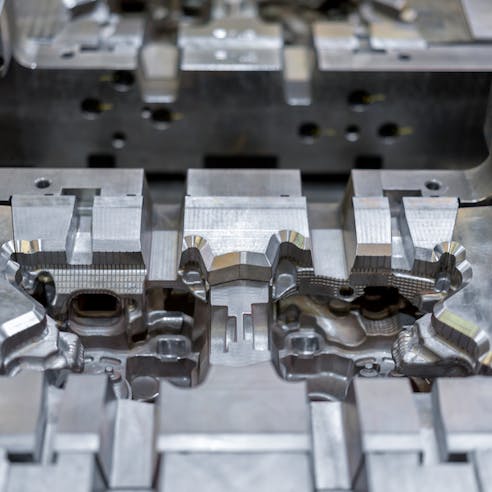
Metal Stamping
If part size and sharp angles are of key importance, then metal stamping offers a cost-effective and highly versatile manufacturing method for angled metal parts. Metal stamping creates thousands of parts in a single workday with complex angled and deep-drawn shapes with high repeatability. Learn more on our Metal Stamping Service page.
Die Casting
Die casting is a tried-and-tested manufacturing process that is widely used throughout automotive, construction, consumer, medical, and many more industries thanks to its variety of available materials, and versatility. To learn more, visit our page on Xometry’s Die Casting Capabilities.
Metal Injection Molding
Just like plastic injection molding, metal injection molding (MIM) is a multi-stage manufacturing process used to produce smaller, complex metal parts in high quantities. Polymerized metal powders are injected into molds, de-binded, and sintered, which allows for high-volume production in a range of materials. To learn more, visit our page on Xometry’s Metal Injection Molding Service.
Why Choose Xometry for Custom Hydroforming?
Endless Options
Choose from millions of possible combinations of materials, finishes, tolerances, markings, and certifications for your order.
Easy to Use
Get started with our easy-to-use platform and let our experts take care of managing the project from locating the right manufacturing partner to delivery logistics.
Vetted Network
We are ISO 9001:2015, ISO 13485, and AS9100D certified. Only the top shops that apply to become suppliers make it through our qualification process.