Small Batch CNC Machining Services by Xometry
Xometry offers the highest quality custom small batch CNC Machining services and can assist in the production of parts with intricate and complex geometries and excellent surface finishes.
In today’s manufacturing landscape, demand for short lead times for even customized and limited-run products is on the rise. Small batch CNC (computer numerical control) machining is important not just for introducing new products to the market, but also for ensuring quality in existing machined products, reducing manufacturing lead times and costs, and expanding a manufacturer’s brand and customer base.
Xometry offers the highest quality small batch CNC machining services for a variety of applications in different industries. Our expansive manufacturing network, coupled with our vast manufacturing experience, ensures that parts fabricated with our small batch CNC machining services are made to the highest standards of quality.
What Is Small Batch CNC Machining?
Small batch CNC machining makes use of computer-controlled turning, milling, drilling, and other machining techniques to produce small volumes of parts. Industries such as: medical, aerospace, automotive, construction, electronics, and consumer goods are just a few examples of sectors that utilize small batch CNC machining. As market demand for more customized products with reduced lead times becomes more intense, manufacturers must respond quickly to accommodate this demand and remain competitive.
Types of Small Batch CNC Machining
A number of CNC machining processes are compatible with small batch production. The various types of small batch CNC machining processes are listed and described below:
- CNC Turning
- CNC Milling
- CNC Drilling
- Sinker EDM Machining
- Wire EDM Machining
- Surface Grinding
- 3-Axis CNC Machining
- 4-Axis CNC Machining
- 5-Axis CNC Machining
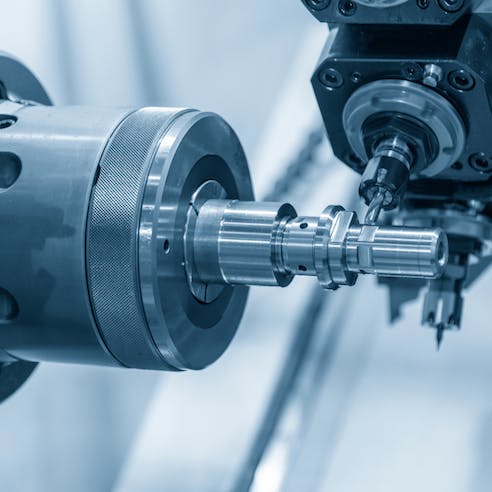
CNC Turning
CNC turning is a lathe process that is used to remove material from a cylindrical workpiece. In CNC turning, the workpiece is fixed in a rotating chuck on one end, while a cutting tool moves along the horizontal plane to remove material along the workpiece’s diameter. Parts solely produced from CNC turning are usually axisymmetric and are typically basic shapes like shafts and fasteners. Examples of parts made by CNC turning include: camshafts, crankshafts, custom vessels, and hand tools like: hammers, punches, gauges, screwdrivers, and more.
CNC Milling
CNC milling is the process of using a rotating cutting tool to remove material from a workpiece. In the CNC milling process, the workpiece is fed into the rotating tool in the same direction as the tool’s rotation. Two main components comprise a milling machine: a worktable in which the workpiece is fixed and a horizontally or vertically oriented spindle and tool holder. Multi-pointed cutting tools, such as end mills, chamfer mills, face mills, dovetail cutters, and more, are utilized to remove workpiece material. CNC milling is a useful process that can produce geometries more complex than turning and is used to make parts such as: gears, electronic enclosures, orthopedic implants, and more.
CNC Drilling
CNC drilling is the process of using a drill bit to create cylindrical holes in a workplace. In CNC drilling, a drill bit moves perpendicularly to the workpiece’s surface and creates vertically aligned holes. However, special machine configurations and tool holders can produce angular holes. Different types of drill bits exist to satisfy different purposes. For instance, spotting drills are used for creating shallow holes or pilot holes, while reamers are used for finishing the surface and obtaining precise dimensions in previously drilled holes. CNC drilling has many applications across a broad spectrum of industries.
Sinker EDM Machining
Sinker EDM (electrical discharge machining) machining is the process of utilizing spark erosion to cut features into metal workpieces. In sinker EDM machining, as well as wire EDM machining, a high-voltage spark is created between a workpiece submerged in a dielectric fluid and an electrically conductive electrode. The spark between the two melts the workpiece material away to create cavities in the workpiece. Sinker EDM machining is used for precise machining applications (tolerances as small as +0.004”), particularly for the creation of precise plastic injection molds.
Wire EDM Machining
Wire EDM machining is a similar process to sinker EDM machining. The biggest difference between the two is that in wire-cut EDM machining, the electrode is a continuously fed wire under tension. The voltage is applied to the wire to create a spark between the electrode and workpiece that melts the workpiece material near the wire. Wire EDM is commonly used for the precise machining of hard metals, particularly for mold and die tooling used in the automobile, medical, and electronics industries.
Surface Grinding
Surface grinding is the process of utilizing a rotating grinding wheel to remove small amounts of workpiece material by abrasion. There are many different types of surface grinding — from Blanchard grinding and cylindrical grinding to centerless grinding and spindle grinding. Computer numerical control helps make surface grinding an efficient process that can attain precise dimensions in parts with tolerances as small as +10 microns.
3-Axis CNC Machining
3-axis CNC machining is the process of cutting part features along three mutually perpendicular axes: both horizontal directions (X and Y) and the vertical direction, Z. In 3-axis CNC machining, features can only be cut up and down, left and right, and forward and backward. The tool can move simultaneously to positions along all three axes, producing such features as angle cuts, tapers, and convex surfaces.
4-Axis CNC Machining
4-axis CNC machining can cut features along the X, Y, and Z axes, as in 3-axis machining, but also along one rotational axis called the A-axis. The rotation of the workpiece around the X-axis constitutes the A-axis. As with 3-axis CNC machining, movement can occur simultaneously along all axes, which enables more efficient machining of features compared to 3-axis machining.
5-Axis CNC Machining
5-axis CNC machining is the machining of parts along 5 different axes: the 3 linear axes of X, Y, and Z, and two rotational axes, referred to as A and B. The A-axis is the rotation of the workpiece around the X-axis while the B-axis is the rotation of the workpiece around the Y-axis. 5-axis CNC machining is a more efficient process, removing material faster while still holding tight tolerances.
Small Batch CNC Machining Materials
Many different types of materials are compatible with small batch CNC machining. Some of them are listed below:
- Aluminum
- Stainless Steel
- Brass
- Mild Steel
- Alloy Steel
- Tool Steel
- ABS
- Nylon
- PTFE (Teflon®)
- POM
- Polycarbonate (PC)
- HDPE
- PEEK
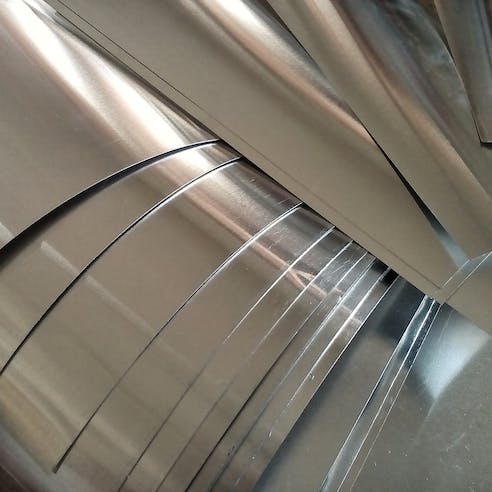
Aluminum
Aluminum is a popular metal used in numerous industries including: aerospace, automotive, electronics, consumer goods, construction, marine, and more. Its light weight, high strength-to-weight ratio, and natural corrosion resistance are some reasons why the material is so popular. Aluminum is a good candidate material for economical production in small batches because it is soft, has a high machinability rating, and requires less expensive tooling to shape it into the desired product. Small batch CNC machining is a good choice for the fabrication of custom-machined aluminum parts.
Stainless Steel
Stainless steel is a preferred metal used in many different industries when corrosion resistance is desired. Industries such as food and beverage processing, chemical processing, medical, automotive, construction, marine, and consumer goods all use stainless steel. Compared to plain carbon steel, stainless steel is an aesthetically appealing material that matches the high strength of carbon steel but also exhibits great corrosion resistance.
Brass
Brass is an alloy composed of varying concentrations of copper and zinc. Compared to other metals like steel and some aluminum alloys, brass is a soft material. Its softness makes brass an easier metal to machine. Brass is machined to make plumbing parts such as: pipe fittings and valves, electronic components like switches and terminals, door hinges and knobs, gears, and more.
Mild Steel
Mild steel refers to types of steel with low carbon percentages, between 0.05 and 0.20%. Also known as low-carbon steel, mild steel is the most commonly used type of steel and the easiest type of steel to machine. It’s used for structural applications in buildings and machinery, pipelines, electronics, power generation applications, and more.
Alloy Steel
Alloy steel refers to steel that may contain a number of pure elements besides iron and carbon. Other elements common in alloy steel are: nickel, chromium, molybdenum, silicon, tungsten, and many more. Different alloy steels have different properties depending on their chemical composition. For instance, chromium-nickel can make steel harder and stronger, and increase its corrosion resistance. Alloy steel is common in the automotive, rail, mining, and construction industries, among others.
Tool Steel
Tool steel refers to steel that is specially formulated for use in the production of tools. Compared to mild steel and alloy steel, tool steel has a high carbon percentage and contains alloying elements like: chromium, molybdenum, tungsten, and vanadium. The addition of these elements makes tool steels exhibit high hardness, great wear resistance, and thermal stability. Through small-batch machining processes, tool steels are first machined and then used to perform machining operations in the form of drills, machine dies, reamers, and various hand tools.
ABS
ABS (acrylonitrile butadiene styrene) is a thermoplastic known for its chemical and thermal stability, toughness, strength, ability to be machined, and glossy finish. It is a versatile material used in everything from automotive trim pieces and electronic housings to consumer products like bicycle helmets and toys. When it comes to prototyping or low-volume production of plastics, small batch CNC machining is preferred due to the ability to save money on expensive tooling and molds.
Nylon
Nylon (polyamides) are a group of thermoplastics valued for their mechanical strength, toughness, stiffness, and useful electric and thermal insulation properties. Additionally, nylon is easy to machine. Nylon has many uses, such as for mechanical components including washers, pulleys, rollers, and valve seats, as well as forming dies and insulators.
PTFE (Teflon®)
PTFE (polytetrafluoroethylene) is another popular and versatile engineering plastic. PTFE is known for its wide operating temperature range, water and chemical resistance, flexibility, machineability, and low friction. PTFE applications include: machined gears, slide plates, bearings, and more.
POM
POM (polyoxymethylene), also known as acetal, is a strong and stiff thermoplastic known for its dimensional stability, low friction coefficient, chemical and UV resistance, and high machinability. Examples of parts made from POM include: pulleys, rollers, gears, and snap fasteners like zippers and buckles.
Polycarbonate (PC)
Polycarbonate is often selected for its transparency and optical clarity as well as its tensile and impact strength, chemical and fire resistance, and recyclability. Polycarbonate parts include: machine safety guards, motorcycle windscreens and face shields, electronic housings, safety glasses, and more.
HDPE
HDPE (high-density polyethylene) is a thermoplastic known for its low melting temperature, high strength-to-weight ratio, recyclability, and corrosion-resistant properties. HDPE is a versatile material with many uses — from packaging and sporting goods to medical equipment.
PEEK
PEEK (polyether ether ketone) is unique among thermoplastics due to its strength, dimensional stability, and chemical resistance, even at high temperatures up to 250 °C (489 °F). Additionally, it is easy to machine. Uses of PEEK include: pump and valve components, bushings, bearings, seals, medical device components, electrical connectors, and more.
Types of Small Batch CNC Machining Finishes
A variety of machining finishes are available for small batch CNC machined parts. The ideal finish for a particular part largely depends on its functional requirements. The different types of machining finishes are listed and described below:
- Bead Blasting
- Anodizing Type III (Hardcoat)
- As-Machined
- Powder Coating
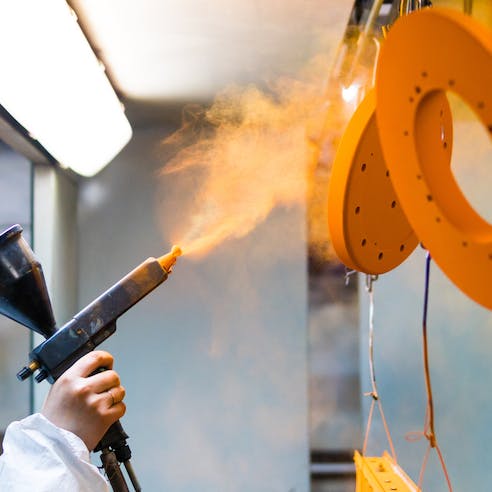
Bead Blasting
Bead blasting is a finishing process that uses compressed air and small glass or metal beads to pelt the surfaces of a machined part. Bead blasting is typically applied to metallic parts. The mechanical action of continuously blasting the part’s surface eliminates machining marks and contaminants to create a uniform surface by smashing down small ridges on the surface of the part. As a result, bead blasting finishes are often used to improve the aesthetic appeal of a part to create either a matte or lightly textured satin finish. However, if parts must meet strict dimensional tolerances, manufacturers must consider the amount of material that will be removed by the bead blasting process to ensure parts still meet the required tolerances.
Anodizing Type III (Hardcoat)
Anodizing is an electrochemical finishing process used to create a protective oxide layer on machined aluminum parts. Sulfuric acid is the most common type of anodizing type III that creates a clear finish available in a variety of colors. The oxide layer created by anodizing type III (hard coat) provides corrosion resistance and abrasion resistance but adds thickness to parts.
As-Machined
As-machined finishes on parts have minor tool marks that result from the cutting or grinding process. The surface roughness of an as-machined surface can range anywhere from Ra 0.2 µ-in to Ra 3.2 µ-in depending on the machining parameters and the tools used. The lower the Ra µ-in value, the smoother the machined surface. As-machined surfaces have lower aesthetic appeal compared to bead-blasted or anodized surfaces, and may not have sufficient protection against corrosive elements since there is no coating to protect the surface from elements in the atmosphere. However, as-machined surfaces may be the right choice for parts that must meet tight tolerances.
Powder Coating
Powder coating is a finishing process that uses static electricity to coat machined parts with powdered paint. After powder coating, the parts must be cured either by subjecting them to treatment with ultraviolet light or by baking them at temperatures between 325 and 450 °F. Different colors and gloss levels can be used to create aesthetically pleasing parts while also providing a smooth, durable coating that provides corrosion resistance and increases durability. However, powder coating makes parts thicker and impairs their electrical conductivity.
In need of custom Small Batch CNC Machining services?
Design Guidelines for Small Batch CNC Machining
Many manufacturers elect to fabricate small batches of products due to the flexibility and reduced lead times made possible by that strategy. However, there are specific guidelines for small batch CNC machining that differ from those customarily followed when machining larger batches or volumes of parts. Manufacturers must take into account these differences to get the most value out of small batch machining. The design guidelines that apply to small-batch CNC machining are listed below.
- Cavity Depth
- Materials and Surface Finish
- Feature Alignment
- Internal Edges
- Prevent Over-Tolerance of the Design
- Drawings
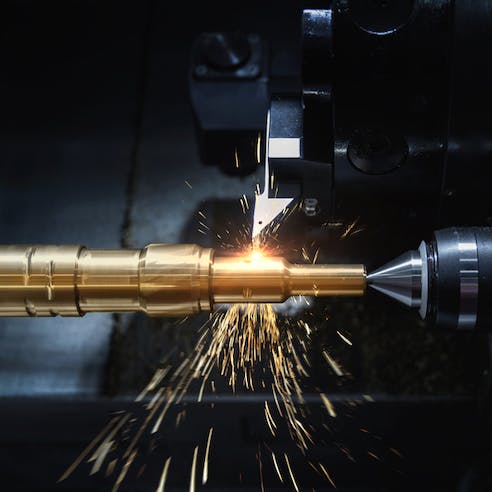
Cavity Depth
Cavity depth is an important factor to consider in both small batch and large batch machining. Cavity depth should be designed to make machining as easy as possible while still being able to satisfy the intended part function. A general rule of thumb is to keep cavities no more than four times deeper than the cavity’s width.
Materials and Surface Finish
Specify the material and surface finish requirements of the product. This includes any heat treatments, like annealing or tempering, and any finishing processes, such as powder coating or anodizing. Keep in mind that achieving a high-quality surface finish may require additional manufacturing time that can affect lead times.
Feature Alignment
Feature alignment and symmetry are important not just for part aesthetics and function, but also for optimizing the machining process. Asymmetric parts create more complicated machining programs and setups — and this is particularly true for parts fabricated using turning processes. Moreover, asymmetric parts can result in the uneven distribution of tool forces which can cause increased tool deflection and lower surface quality. If possible, designing asymmetric parts should be avoided.
Internal Edges
When it comes to cutting internal edges, ensure that the vertical corner radius is, at a minimum, one-third the depth of the cavity. Using a tool slightly larger than the radius of the part allows a circular path to be cut rather than a right angle. This leads to a better surface finish on the internal edge.
Prevent Over-Tolerance of the Design
Over-tolerancing a part can lead to unnecessary headaches for both the manufacturer and the customer. Establishing extremely small tolerances when they are not required not only makes parts take longer to produce but also makes the process more expensive. Therefore, designers should avoid over-tolerancing a design and only establish realistic, practical tolerances.
Drawings
2D drawings and 3D models showing the part’s dimensions and features, tolerances, finishing requirements, and more are commonplace for small batch parts. The more detail that is expressed on the drawing, the easier it will be for manufacturers to determine the best tools and tool paths to use to make the part.
Advantages of Small Batch CNC Machining
Small batch CNC machining has many advantages, such as:
- Low-Volume Production
- Cost-Effectiveness
- Shorter Lead Time
- Verification of Design
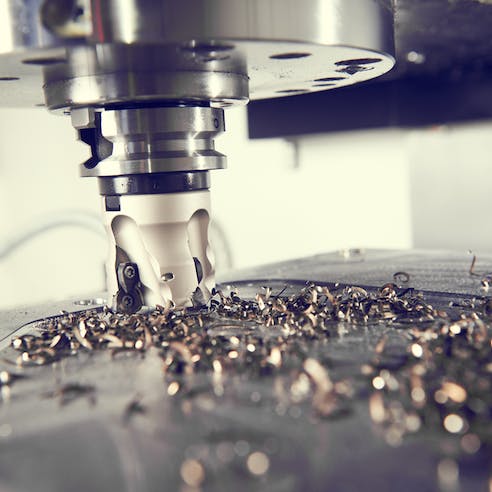
Low-Volume Production
One advantage of small batch CNC machining is the ability to rapidly fulfill low-volume production orders. Fulfilling small orders enables manufacturers to service many more customers in shorter time frames than when they are fulfilling larger orders. This can help manufacturers expand their customer base as well as improve their production efficiency and material usage.
Cost Effective
One of the primary benefits of small batch CNC machining is its cost-effectiveness. Small batch CNC machining requires less time to complete orders of parts since there are fewer parts to make and minimizes energy consumption. Both these things result in lower operating costs and overhead costs for manufacturers.
Increased Production Speed
Small batch CNC machining is an automated machining process. This means there is less downtime since tool changes, tool paths, workpiece reorientation, and sometimes workpiece fixturing and mounting all occur automatically. Additionally, since there are fewer parts to produce with small-batch CNC machining, shorter lead times are the norm.
Verification of Design
Small batch CNC machining aids in prototyping, allows manufacturers to quickly verify part design and function, and makes necessary adjustments to both design and tool paths. This reduces product development cycle times while also improving overall part quality.
Applications of Small Batch CNC Machining
Listed below are a few applications in which small-batch CNC machining can be used:
- Electronic Enclosures
- Electronic Component Racks
- Custom Storage Racks
- Mounting Brackets
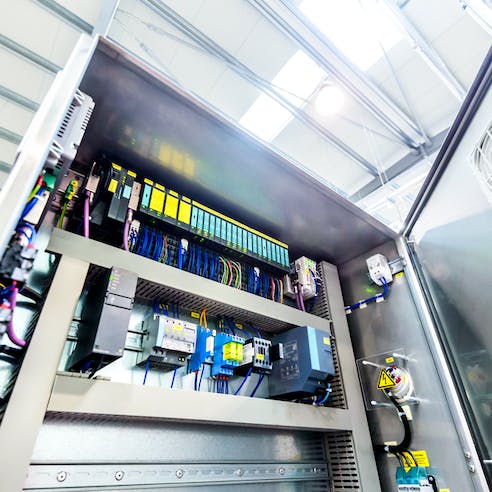
Electronic Enclosures
Small batch CNC machining is useful for the fabrication of electronic enclosures, especially one-off or special enclosures with small physical volumes. Milling and drilling are all applicable machining processes for electronic enclosures.
Electronic Component Racks
Electronic component racks are another application where small batch CNC machining is useful. Electronic component racks are storage solutions that hold sensitive electronic equipment.
Custom Storage Racks
Small batch CNC machining is also good for the fabrication of custom storage racks designed to accommodate specific tools, equipment, and various other items. Since these racks are tailor-made for specific items which may also be custom-made, manufacturing volumes of these racks will be small.
Mounting Brackets
Mounting brackets are another application where small batch CNC machining shines. Mounting brackets are relatively simple to produce. As such, manufacturers can create and alternate between many different types of mounting brackets with ease and efficiency.
Alternatives to Small Batch CNC Machining
Small batch CNC machining may not be suitable for some applications due to part complexity or specialized tooling required to produce parts. In that case, there are several alternatives to small batch CNC machining, depending on the part volume and lead times required. The alternatives are listed and described below:
- 3D Printing
- Small-Batch Injection Molding
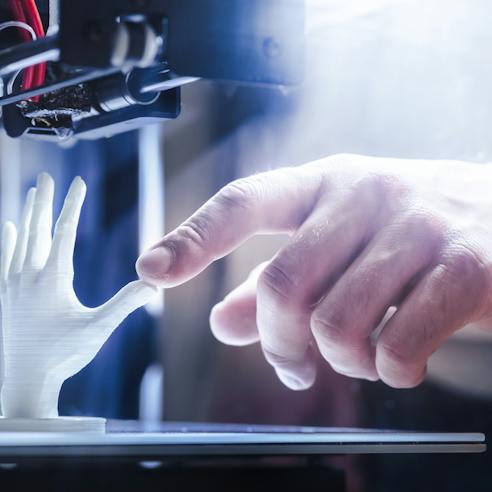
- 3D Printing: 3D printing enables the on-demand manufacturing of parts and components, and can be used to build almost any geometry. Consequently, 3D printing is a popular process for creating customized and limited-run products. Additionally, since 3D printing requires far less time to fabricate the tools necessary for manufacturing, and less time to develop the printing programs, lead times are exceptionally short.
- Small-Batch Injection Molding: Single cavity injection molds for specialized and custom products can be made in as little as 4-6 weeks depending on the mold manufacturer and part geometry. Once the mold has been fabricated and injection parameters have been established, small batch runs can be completed quickly.
Why Choose Xometry for Custom Small Batch CNC Machining Services?
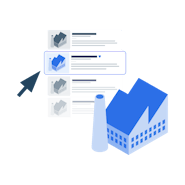
Endless Options
Choose from millions of possible combinations of materials, finishes, tolerances, markings, and certifications for your order.
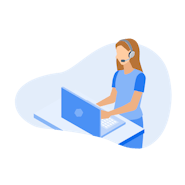
Easy to Use
Get started with our easy-to-use platform and let our experts take care of managing the project from locating the right manufacturing partner to delivery logistics.
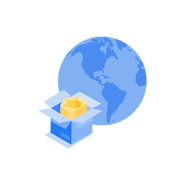
Vetted Network
We are ISO 9001:2015, ISO 13485, and AS9100D certified. Only the top shops that apply to become Suppliers make it through our qualification process.