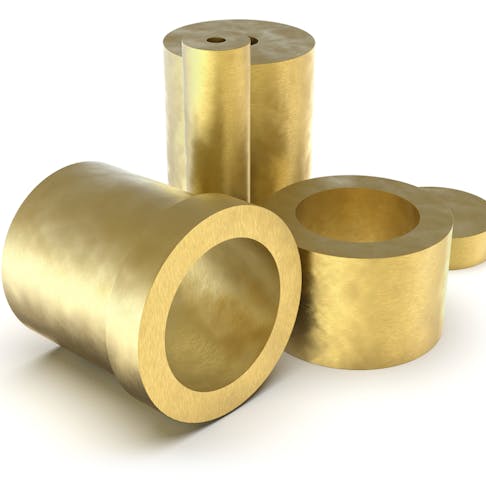
Phosphor Bronze: Definition, Composition, Properties, and Applications
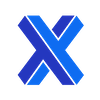
Phosphor bronze is a versatile family of alloys, valued for unique properties in a wide spectrum of applications. It is primarily composed of copper (typically around 85–95%), tin (usually 4–10%), and a small percentage of phosphorus (usually 0.1–0.35%). The addition of phosphorus enhances the alloy's strength, and wear and corrosion resistance.
Phosphor bronze is utilized in many sectors for bearing/bushings, electrical contacts, musical instruments (such as strings for acoustic and classical guitars and valve components in brass instruments), coil and sheet springs, marine equipment, and fasteners.
This article will discuss what phosphor bronze is, its composition and properties, and its common applications.
What Is Phosphor Bronze?
Phosphor bronze is a group of bronze alloys characterized by composition. This is typically copper (85–95%), tin (4–10%), and a small percentage of phosphorus (0.1–0.35%).
The addition of phosphorus greatly improves mechanical properties, making it stronger, more wear- and corrosion-resistant than regular bronze. The bulk of the changes result from the effect of phosphorus as an intermediary between copper and tin, increasing the miscibility and atomic level diffusion of the two metals into each other.
Is Phosphor Bronze and Tin Bronze the Same Thing?
No. Phosphor bronze and tin bronze are not the same. Tin bronze is the older and more commonly understood type. Phosphor bronze contains the described trace amount of phosphorus, which disproportionately enhances its strength and wear resistance. The changes are at an atomic matrix level and result from better diffusion of the tin component into the majority of copper, greatly altering the material.
The two alloy groups have distinct properties and applications.
What Is the Origin of Phosphor Bronze?
Phosphor bronze originated in the early 19th century when metallurgists were exploring ways to improve the properties of traditional bronze alloys. This period showed extraordinary growth in alloy types, as metallurgists chased improved alloys for industrial and military applications. The addition of phosphorus to bronze was a deliberate experimental effort to enhance its mechanical characteristics, including: strength, hardness, and wear resistance.
The exact origin is poorly attributed to the 1830s and 1840s through the work of various metallurgists and inventors. Samuel Morley is often credited with the development of phosphor bronze in the United Kingdom, while John B. Dancer and Benjamin Huntsman were doing the same in the United States.
What Is Phosphor Bronze Made Of?
Table 1 below shows the composition of phosphor bronze:
Element | Composition Range (%) |
---|---|
Element Copper (Cu) | Composition Range (%) 85.0–95.0 |
Element Tin (Sn) | Composition Range (%) 4.0–10.0 |
Element Phosphorus (P) | Composition Range (%) 0.1–0.35 |
How Is Phosphor Bronze Made?
Typically for most alloys, phosphor bronze is generally made by batch mixing alloying against a crucible or furnace, following a prescribed “recipe” using high-purity components.
The primary raw materials used in phosphor bronze production are copper, tin, and phosphorus. These materials are sourced in their pure forms or as alloys. The required proportions of copper, tin, and phosphorus are carefully measured and co-melted in a furnace. Additives for degassing and slag formation are often included. During melting, the alloying elements are mixed thoroughly either by stirring or crucible motions, to ensure homogeneity. Phosphorus is typically added as a master alloy to control the precise amount — a master alloy being a pre-made and precision-quantized blend of copper and phosphorus to increase the precision and miscibility of the phosphorus addition. Once the alloy is homogenized, it is cast into various forms, such as ingots, bars, or billets, depending on the intended application. For particular applications, a spectroscopic analysis of constituents is performed to ensure the proportions are as desired.
The precise details of the alloying process will vary depending on the specific requirements of the alloy and its intended applications. As an example, various additives for degassing are used and for the highest purity alloys vacuum arc remelting may be applied.
What Is the Color of Phosphor Bronze?
Phosphor bronze typically has a reddish-brown or golden color, reflecting its copper-rich composition and its state of oxidation. The exact shade may vary depending on the specific alloy and surface finish.
What Does a Phosphor Bronze Look Like?
When polished, phosphor bronze has a lustrous golden color and offers a matte to mirror surface depending on the state of polish. As it oxidizes, the luster is lost and the metal progressively darkens to a deeper, more brown, and increasingly matte color. When exposed to corrosive attack, including long-term water exposure, a green copper oxide surface that is powdery and fragile develops.
How Does Phosphor Bronze Differ From Bronze?
The only significant difference between the two is that phosphor bronze contains trace phosphorus as an alloying element that adjusts the atomic-level behavior of the bulk alloy. This imparts several key differences:
Phosphor bronze is stronger and harder than traditional bronze due to the altered dissolution/diffusion of the tin into the bulk copper. These alloys offer superior wear resistance, making them suitable for applications such as ball bearings and plain bushings. Both alloys are corrosion-resistant, but phosphor bronze's resistance can be even better, particularly in salt and acidic environments. Phosphor bronze has better electrical conductivity than bronze, due to greater uniformity at an atomic matrix level.
What Are the Different Phosphor Bronze Grades?
Phosphor bronze grades can vary depending on regional or industry-specific standards. Table 2 below highlights some of these phosphor bronze grades and their composition:
Grade | Composition (Percentages) | Industry Standards |
---|---|---|
Grade C51000 | Composition (Percentages) Cu 94.7%, Sn 5.0%, P 0.3% | Industry Standards ASTM B103, B139, B159 |
Grade C51900 | Composition (Percentages) Cu 89.8%, Sn 10.0%, P 0.2% | Industry Standards ASTM B103, B139, B159 |
Grade C52100 | Composition (Percentages) Cu 87.0%, Sn 8.5%, P 4.5% | Industry Standards ASTM B103, B139, B159 |
Grade C54400 | Composition (Percentages) Cu 80.0%, Sn 10.0%, P 10.0% | Industry Standards ASTM B103, B139, B159 |
Grade C5101 | Composition (Percentages) Cu 95.8%, Sn 3.5%, P 0.7% | Industry Standards JIS H5111 |
Grade C5191 | Composition (Percentages) Cu 88.5%, Sn 10.0%, P 1.5% | Industry Standards JIS H5111 |
Grade C5212 | Composition (Percentages) Cu 86.0%, Sn 7.5%, P 6.5% | Industry Standards JIS H5111 |
Grade PB102 | Composition (Percentages) Cu 88.5%, Sn 10.0%, P 1.5% | Industry Standards BS 2874 |
Grade PB104 | Composition (Percentages) Cu 87.0%, Sn 9.5%, P 3.5% | Industry Standards BS 2874 |
Chemical Property | Description |
---|---|
Chemical Property Composition | Description copper (Cu), tin (Sn), and phosphorus (P) |
Chemical Property Corrosion Resistance | Description Excellent corrosion resistance, particularly in marine and acidic environments |
Chemical Property Oxidation Resistance | Description Forms a protective oxide layer upon exposure to air |
Chemical Property Chemical Reactivity | Description Generally unreactive with common chemicals, acids, and alkalis |
Chemical Property Biocompatibility | Description Phosphor bronze is often used in medical applications due to its biocompatibility |
Physical Property | Description |
---|---|
Physical Property Color | Description Typically reddish-brown or golden when unoxidized |
Physical Property Density | Description Generally ranges from 8.75 to 8.94 g/cm³ |
Physical Property Melting Point | Description Typically between 920 °C and 980 °C (1,688 °F–1,796 °F) |
Physical Property Electrical Conductivity | Description Good electrical conductivity, suitable for electrical contacts and connectors |
Physical Property Thermal Conductivity | Description Moderate thermal conductivity, used in heat-transfer applications |
Physical Property Tensile Strength | Description High tensile strength, making it suitable for springs and high-stress components |
Physical Property Hardness | Description Relatively high hardness, providing wear resistance |
Physical Property Coefficient of Friction | Description Low coefficient of friction, advantageous in bearing applications |
Physical Property Magnetic Properties | Description Non-magnetic |
Is Phosphor Bronze Stronger Than Stainless Steel?
It depends. Phosphor bronze and stainless steel have quite divergent properties and advantages, and their relative strength depends on the fine details of alloy constituents. Stainless steel is useful due to its higher tensile strength compared to phosphor bronze. Phosphor bronze is selected for its unique combination of properties, including: good strength, wear resistance, and corrosion resistance.
The application-specific benefits of the two materials result from the precise requirements of the use and the desired balance of properties.
Is Phosphor Bronze Magnetic?
No, phosphor bronze is typically non-magnetic and is a non-ferrous alloy. This non-magnetic characteristic makes it suitable for applications in which magnetic interference or attraction is undesirable, such as in certain electrical and electronic components and medical imaging applications.
Can You Laser Weld Phosphor Bronze?
Yes. Laser welding of phosphor bronze can be challenging due to the material's high reflectivity to some frequencies of laser light and its high thermal conductivity. However, with specialized laser welding equipment and parameters, it is possible to achieve successful laser welds. This requires careful control of laser power, pulse duration, and beam focusing to overcome the material's reflectivity and achieve a quality weld.
Notably, the reflectivity is greatly reduced when the material approaches the liquidus state, so the initiation of welds is the major challenge.
Does Phosphor Bronze Rust?
No, phosphor bronze does not “rust” in the mode that ferrous metals like iron and steel corrode. However, phosphor bronze is particularly corrosion-resistant among copper alloys. This corrosion resistance results from the formation of an impermeable protective oxide layer on the surface of the bronze when exposed to air or moisture, which acts as a moisture and oxygen barrier.
Phosphor bronze is often chosen for applications in environments in which corrosion is a concern, such as marine and outdoor settings.
What Are the Applications of Phosphor Bronze?
Phosphor bronze is a widely used material but is not commonly known outside engineering experience. It has a long list of engineering and decorative applications as discussed below:
1. Wire
Phosphor bronze wire is a type of wire known for its excellent combination of properties, including: high tensile strength, good electrical conductivity, corrosion resistance, and fatigue resistance. Phosphor bronze wire is commonly used in electrical connectors, springs, musical instrument strings, and valves, in which its combination of strength and electrical conductivity is applicable.
2. Springs
Phosphor bronze springs are highly regarded for their excellent spring properties, combining good elasticity, high tensile strength, cycle fatigue endurance, and corrosion resistance. Phosphor bronze springs are widely used in electrical contacts, switches, mechanical components, and instruments. They are valued for their durability, reliability, and ability to maintain their spring properties over time, even in challenging environments. Typically, phosphor bronze is one of the two sheet materials in a thermal change bi-metallic component that operates as a very stable and precise thermal sensor.
3. Marine Products
Phosphor bronze is extensively used in the marine industry due to its exceptional chloride ion corrosion resistance. Phosphor bronze is often used to manufacture marine propellers due to its resistance to corrosion in saltwater environments and relatively low cost. Marine fasteners like: screws, bolts, and nuts can be made from phosphor bronze to withstand the corrosive influence of seawater. Bushings and bearings made of phosphor bronze are used in various sectors to provide reliable, durable, and low-friction movement. Various marine fittings and hardware components, such as: cleats, hinges, and moderate load chains can be made from these alloys, for their corrosion-resistant properties. Phosphor bronze drive shafts are used in marine applications in which corrosion resistance and durability are essential, as the shaft traverses the “stuffing” and is exposed to seawater.
4. Dental Products
Phosphor bronze was formerly used in the production of dental equipment products, having been displaced by stainless steel, titanium, and dental-grade plastics due to their better biocompatibility, durability, and ease of sterilization.
5. Musical Applications
Phosphor bronze is widely used in the manufacturing of various musical instruments, particularly for its exceptional acoustic properties. It is frequently used to make acoustic guitar strings. It provides a warm, rich tone with good sustain and clarity, resulting from the high spring modulus and low damping behavior. Phosphor bronze is used in piano strings, contributing to the instrument's resonance and durability for the same benefits as in guitar strings. It is employed in the production of cymbals, offering a bright and resonant sound that benefits from the same range of properties and considerable work-hardening, evident in the rolled, spun, or hand-planished finishes. Some brass instruments, such as trumpets and saxophones, may incorporate phosphor bronze components to enhance their acoustic properties and resistance to saliva-induced corrosion.
6. Fuse Clips
Phosphor bronze is widely used as an electrical corrosion-resistant alternative to plated, hardened steel for the spring clips that retain fuses. Good conductivity and great spring resilience add to this for long life and use-tolerant clips that solder easily.
7. Industrial Applications
Phosphor bronze finds various industrial applications due to its unique combination of properties, including strength, corrosion resistance, and electrical conductivity. Its wear resistance and lubricity make it ideal for use in roller/ball bearings and plain rotating and sliding bushings, reducing friction and wear in machinery. Phosphor bronze springs are used in various industrial equipment, including: valves, switches, and automotive components due to excellent spring properties and durability. It is commonly used in electrical connectors and switches for its good electrical conductivity and spark erosion-corrosion resistance. Tubes and fins made of the materials are used in heat exchangers, in which corrosion resistance and thermal conductivity are important.
8. Electrical Applications
Phosphor bronze is extensively used in electrical applications due to its excellent combination of electrical conductivity, thermal conductivity, and corrosion resistance. Phosphor bronze is widely employed in electrical connectors and contacts, ensuring reliable electrical conductivity and durability. These are often gold plated to improve connectivity and reduce connect/disconnect “noise”. It is used in switches for its spring-like properties, allowing for smooth and reliable electrical contact with high and enduring spring forces and fatigue resilience. Phosphor bronze terminal blocks are used for wire connections in electrical panels and distribution systems. Phosphor bronze springs are widely used in electrical switches and relays, industrial equipment, and consumer products, providing precise and repeatable performance.
9. Relay Contacts
Phosphor bronze spring contacts are commonly used in relay contacts, specifically in electromagnetic relays and switchgear. These applications exploit the electrical and mechanical strengths of the materials
10. Circuit Breaker Contacts
Phosphor bronze is used in high-power circuit breakers, particularly in their contact materials. The combination of good electrical conductivity, low erosion by contact arcing, durability and longevity, and relatively low price is a winning group of advantages.
How Can Xometry Help You With Your Phosphor Bronze Needs?
Xometry is a leading manufacturing marketplace that can assist with your phosphor bronze needs in various ways. Xometry connects you with a vast network of validated suppliers and material providers to source high-quality phosphor bronze materials. We offer a range of material-relevant manufacturing services, including: CNC machining, 3D printing, sheet metal fabrication, and heat treatment. You can use our platform to get custom phosphor bronze parts or components fabricated to your exact specifications. Our platform allows you to upload your design, receive rapid quotes, and confidently place orders for your parts. Our approach ensures that all manufacturing partners adhere to strict quality standards, guaranteeing the quality and reliability of your deliverables.
Xometry simplifies the process of procuring and manufacturing phosphor bronze components, providing a one-stop solution for your material and manufacturing needs.
What Are the Advantages of Phosphor Bronze?
Phosphor bronze offers several advantages such as:
- Has excellent electrical conductivity, making it ideal for electrical contacts, bus bars, and connectors.
- Resists corrosion, particularly in moist or aggressive environments, ensuring durability.
- Exhibits spring-like characteristics, so it returns to its original shape after deformation with no loss of strength and no fatigue response, making it optimal for springs and contacts.
- The materials are generally highly workable and can be work-hardened and heat treated to alter properties significantly.
- Has great wear resistance, reducing friction for rolling elements and sliding parts.
- Is biocompatible and can be used in medical devices.
- Has desirable acoustic qualities such as low damping and high resonance, making it suitable for musical instrument strings.
What Are the Disadvantages of Phosphor Bronze?
While phosphor bronze offers some critically important advantages, it also has some disadvantages:
- Can be more expensive than other materials like steel or aluminum, which can impact the overall cost of manufacturing.
- Compared to more common metals like steel, phosphor bronze may have limited availability, leading to longer lead times for sourcing.
- Is generally denser than some alternative materials, which can be a drawback in weight-sensitive applications.
- While highly workable, it can be more challenging to machine than softer materials, which may require specialized tooling and expertise.
- In rare cases, individuals with copper allergies may experience skin reactions when in contact with phosphor bronze.
How Much Does Phosphor Bronze Cost?
The material cost is highly dependent upon form and traded quantity. For example, hot rolled C52100 phosphor bronze bar round/square/hex costs US$10.50–$12.00 per kg. Typically traded ingots of phosphor bronze of moderate to good purity and general grade cost around US$7,000 to $9,000 per metric tonne.
Is Phosphor Bronze Cheap?
It depends. Phosphor bronze is a relatively high-cost metal when compared with more generic basic stainless steels, mild steels, etc. However, it carries a similar cost to moderate-grade stainless steel, other bronze materials (nickel-aluminum bronze), and brass.
This makes it a moderate-cost material, considerably lower in price than precious metals, and generally prices per kg or ton.
Is Phosphor Bronze Worth More Than Inconel®?
It depends. Phosphor bronze and Inconel® are quite different materials with distinct properties and applications, so their comparative value depends on the specific requirements of your project or application.
Phosphor bronze is best used for its electrical conductivity, corrosion resistance, and spring properties. Inconel®, on the other hand, is a family of nickel-based superalloys with exceptional high-temperature strength and corrosion resistance. Inconel alloys were developed for extreme environments, such as: aerospace, chemical processing, and high-temperature industrial applications.
The relative value of these materials depends on factors like: the application's temperature, corrosion-resistance requirements, mechanical properties, and budget constraints. Inconel® is generally more expensive than phosphor bronze, but it offers unique properties that can justify its cost in specific demanding applications. The choice between the two should be based on the specific needs of your project.
Is Phosphor Bronze Rare?
No, phosphor bronze is a widely utilized and commodity-level material. While it tends to be reserved for tasks in which corrosion resilience and wear resistance are paramount, it is commonly and easily purchased in various grades with precisely defined properties and optimal applications
What Is the Difference Between Phosphor Bronze and Brass?
Phosphor bronze and brass are both copper alloys, but they have distinct differences in terms of composition, properties, and applications.
Phosphor bronze is a copper-based alloy. The addition of phosphorus gives it its name and contributes to its unique properties. Brass is also copper-based, but the primary alloying agent is zinc rather than the tin typical of bronze.
Phosphor bronze typically has a reddish-brown or gold color. Brass can vary in color from yellow to a similar reddish-brown to phosphor bronze, varying considerably with the zinc content.
Phosphor bronze is known for its excellent spring properties, high electrical conductivity, and corrosion resistance. It is often used in springs, electrical contacts, and components requiring both strength and electrical conductivity. Brass is valued for its malleability, corrosion resistance, and acoustic properties. It is used in musical instruments, decorative items, and plumbing fixtures not subject to acidic or salt conditions.
Phosphor bronze is commonly used in applications in which a combination of strength, electrical conductivity, and corrosion resistance is required. Brass is used in a wide range of applications, including: musical instrument tubes (brass instruments and some woodwind types), plumbing fittings, decorative hardware, and ammunition casings.
Summary
This article presented phosphor bronze, explained it, and discussed its composition and properties. To learn more about phosphor bronze, contact a Xometry representative.
Xometry provides a wide range of manufacturing capabilities and other value-added services for all of your prototyping and production needs. Visit our website to learn more or to request a free, no-obligation quote.
Copyright and Trademark Notice
- Inconel® is a trademark of the Special Metals Corp.
Disclaimer
The content appearing on this webpage is for informational purposes only. Xometry makes no representation or warranty of any kind, be it expressed or implied, as to the accuracy, completeness, or validity of the information. Any performance parameters, geometric tolerances, specific design features, quality and types of materials, or processes should not be inferred to represent what will be delivered by third-party suppliers or manufacturers through Xometry’s network. Buyers seeking quotes for parts are responsible for defining the specific requirements for those parts. Please refer to our terms and conditions for more information.
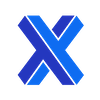