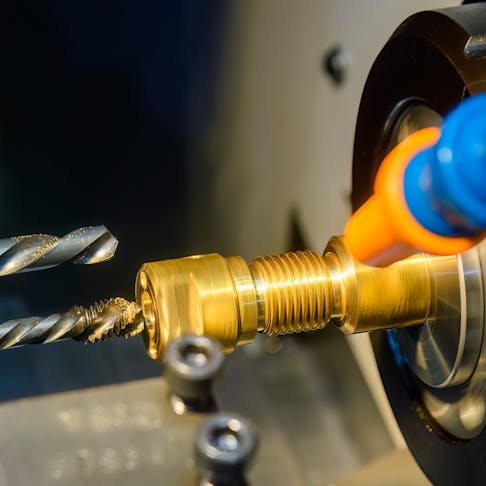
Silicon Bronze vs Brass: What Are the Key Differences?
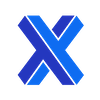
Silicon bronze and brass are copper-based alloys, but they have significant differences in composition, properties, and applications. Silicon bronze is composed of copper (Cu), silicon (Si), and small amounts of other elements such as zinc (Zn) and tin (Sn). Brass is also primarily composed of copper, but with a significant proportion of zinc, with various proportions of these elements leading to different types of brass alloys. Silicon bronze offers excellent corrosion resistance, especially in marine environments. It possesses high strength, ductility, and weldability. Brass, on the other hand, is malleable and exhibits good corrosion resistance, in non-aggressive environments. It is often chosen for its decorative properties and ease of machining, having only moderate strength and toughness.
This article will discuss the difference between silicon bronze vs brass in terms of composition, applications, advantages, and disadvantages.
What Is Silicon Bronze?
Silicon bronze is a primarily copper (Cu) alloy with a small proportion of silicon (Si) and trace amounts of other elements like zinc (Zn) and tin (Sn). It is known for its exceptional corrosion resistance, particularly in marine environments, making it an invaluable material for various outdoor and marine applications.
To learn more, see our full guide on Silicon Bronze.
What Is Another Name for Silicon Bronze?
Silicon bronze is also known by several other names and trade names, including: Everdur, C65500, and siliconized bronze. Everdur is a trademarked name for a specific type of silicon bronze alloy with particularly high corrosion resistance and durability. C65500 is a common designation for a silicon bronze alloy by ASTM (American Society for Testing and Materials) standards. The siliconized bronze name reflects the high silicon content in the alloy. These names may be used interchangeably, but they typically refer to a family of copper alloys with a significant silicon content.
What Is Silicon Bronze Made Of?
Table 1 outlines the typical composition of silicon bronze:
Element | Composition Range (%) |
---|---|
Element Copper (Cu) | Composition Range (%) 88.0% to 96.0% |
Element Silicon (Si) | Composition Range (%) 2.5% to 4.5% |
Element Zinc (Zn) | Composition Range (%) 0.5% max |
Element Tin (Sn) | Composition Range (%) 0.05% max |
Element Phosphorus (P) | Composition Range (%) 0.03% max |
Element Lead (Pb) | Composition Range (%) 0.05% max |
Element Iron (Fe) | Composition Range (%) 0.8% max |
Element Aluminum (Al) | Composition Range (%) 0.005% to 0.5% |
Element Others (Total) | Composition Range (%) 0.5% max |
Exact compositions vary moderately between various specific silicon bronze grades.
What Does Silicon Bronze Look Like?
Silicon bronze typically has a distinctive red-brown or golden color when freshly manufactured. Over time, when exposed to the environment, it develops a darker patina with shades of brown or green due to oxidation and the formation of copper compounds. This patina contributes to its corrosion resistance, forming a barrier to oxygen, moisture, and mild acids/alkalis.
The exact color/shade appearance of Silicon bronze can vary depending on factors like alloy composition, surface finish, and exposure to environmental conditions. Figure 1 shows a silicon bronze propeller:
Silicon bronze propeller.
Image Credit: Shutterstock.com/ZHMURCHAK
Silicon Bronze Grade | Other Designations | Composition (Typical) |
---|---|---|
Silicon Bronze Grade C65100 | Other Designations ASTM B98 | Composition (Typical) Cu - 96.0%, Si - 3.0% |
Silicon Bronze Grade C65500 | Other Designations ASTM B96, ASTM B248, ASTM B98, SAE J461, SAE J463 | Composition (Typical) Cu - 94.6%, Si - 3.0%, Zn - 0.5% |
Silicon Bronze Grade C65600 | Other Designations - | Composition (Typical) Cu - 93.0%, Si - 3.5%, Mn - 2.0% |
Silicon Bronze Grade C65700 | Other Designations - | Composition (Typical) Cu - 91.0%, Si - 4.0%, Zn - 4.0%, Pb - 1.5% |
Silicon Bronze Grade C65620 | Other Designations AMS 4616 | Composition (Typical) Cu - 87.0%, Si - 2.5%, Sn - 10.0%, Pb - 0.5% |
Grades may vary in composition based on the specific manufacturer and are selected based on the desired properties and intended applications.
How Does Silicon Bronze Differ From Bronze?
Silicon bronze differs from traditional bronze primarily in its composition. While both are copper alloys, silicon bronze contains silicon (Si) as a significant alloying element and minimal to no tin (Sn).
Silicon bronze is known for its improved corrosion resistance and strength compared with basic bronze, making it suitable for applications in which durability and resistance to environmental factors are demanded. Traditional bronze may have different properties depending on the specific tin content and may be chosen for its historical significance, aesthetic appeal, lower cost, or specific mechanical properties.
To learn more, see our guide on the Composition of Bronze.
What Are the Advantages of Silicon Bronze?
Silicon bronze offers several advantages that make it a desirable material for various applications. These advantages include:
- Highly corrosion-resistant, making it ideal for use in marine environments and other applications exposed to moisture and harsh conditions.
- Has good mechanical properties, including high tensile strength and hardness, contributing to its beneficial durability and long service life.
- Retains its strength and properties at elevated temperatures.
- Biocompatible and safe for use in medical and dental applications, other than in rare cases of patient sensitivity to copper and its salts.
- Has an attractive red-brown or gold color that can enhance the visual appeal of products and architectural elements.
- Easily machinable and weldable, and can be fabricated into various shapes and forms.
What Are the Disadvantages of Silicon Bronze?
While silicon bronze offers numerous advantages, it also has some disadvantages. These disadvantages include:
- Can be more expensive than other copper alloys.
- Is denser than many materials, making it heavier and potentially less suitable for weight-sensitive applications.
- Certain exotic grades may have limited availability compared to more common metals.
- Can be more challenging to machine than softer materials, requiring specialized tooling and expertise.
- While silicon bronze has good electrical/thermal conductivity, it may not be as conductive as materials like pure copper or phosphor bronze.
Is Silicon Bronze Heavier Than Brass?
It depends. The density of materials can vary depending on their composition and specific alloy. The density of silicon bronze typically ranges from 8.82 to 8.92 g/cm³. Brass alloys can have varying densities depending on the specific composition. On average, the density of brass ranges from 8.49 to 8.92 g/cm³. Therefore silicon bronze can have a higher density than brass for some grades.
What Is Brass?
Brass is an alloy primarily consisting of copper (Cu) and zinc (Zn). It is a versatile material with a wide range of applications. It has a distinctive yellow to red-brown color, which can vary depending on the zinc content. Brass is highly malleable, allowing it to be easily shaped, formed, and machined into various forms. It exhibits good resistance to corrosion in mild environments. Additionally, brass has excellent electrical conductivity and is frequently chosen for its aesthetic appeal in decorative art, architectural elements, and jewelry. Certain brasses are prized for acoustic qualities (excellent resonance, low damping, and a smooth frequency response), leading to their use in musical instruments like trumpets and saxophones.
To learn more, see our full guide on Brass Material.
What Is Another Name for Brass?
Brass is known by various names and designations depending on its specific composition and applications. Some of its different names include yellow brass, cartridge brass, and architectural bronze.
What Is Brass Made Of?
Table 3 outlines the typical composition of brass alloying elements:
Element | Composition Range (%) |
---|---|
Element Copper (Cu) | Composition Range (%) 55% to 95% |
Element Zinc (Zn) | Composition Range (%) 5% to 45% |
Element Lead (Pb) | Composition Range (%) Up to 3.5% (in some free-cutting brass) |
Element Tin (Sn) | Composition Range (%) Up to 2% |
Element Aluminum (Al) | Composition Range (%) Up to 1.5% |
Element Nickel (Ni) | Composition Range (%) Up to 1% |
Element Iron (Fe) | Composition Range (%) Up to 1% |
Element Manganese (Mn) | Composition Range (%) Trace amounts |
Element Phosphorus (P) | Composition Range (%) Trace amounts |
The composition of brass varies significantly based on the desired properties and intended applications.
What Does Brass Look Like?
When polished, brass has a golden or red-gold color and forms a lustrous and reflective surface. Surfaces range from gloss reflective to matte or rough, but the oxide-free color remains the same. As the surface oxidizes it takes on a dull red-brown hue that deepens over time/atmospheric exposure and may vary with copper content. When exposed to acidic conditions, a green copper oxide forms that is fragile and powdery. Figure 2 shows a close-up image of a brass sheet:
Brass sheet.
Image Credit: Shutterstock.com/Magdalena Cvetkovic
What Are the Different Types of Brass?
The following list outlines some of the different types of brass:
- Yellow Brass: Refers to brass alloys with a higher zinc content, giving them a bright yellow color.
- Red Brass: Designated brasses with a higher proportion of copper, which have a more red hue.
- Cartridge Brass: A grade used for making ammunition casings.
- Naval Brass: A more corrosion-resistant brass used in marine applications.
- Free-cutting Brass: Brass alloys that are optimized for ease of machining, often by the addition of a small proportion of lead (Pb).
- Architectural Brass: Refers to brass used in architectural and decorative applications.
- Alloy Numbers (e.g., C26000): Brass alloys are often designated by numerical codes based on ASTM or other standards.
How Does Brass Differ From Bronze?
Brass and bronze are both copper alloys, but they differ in their primary alloying elements and properties. Brass is primarily composed of copper and zinc, with other metals in varying proportions to achieve specific properties. Bronze is composed of copper and tin, making a quite different family of materials.
Brass and bronze typically have a yellow/gold to red-brown color, depending on the proportion of copper. Brass is known for its excellent malleability, corrosion resistance, and electrical conductivity. It is often chosen for decorative and functional applications, including plumbing fixtures, musical instruments, and electrical connectors.
Bronze is recognized for its strength, hardness, corrosion resistance, and durability. It is often used for applications in which higher mechanical properties are essential, such as: bearings, sculptures, and historical artifacts.
What Are the Advantages of Brass?
Brass offers several advantages that make it a preferred material in many applications. Those advantages include:
- Exhibits excellent resistance to corrosion in mild and salt-free environments, making it ideal for plumbing fittings and marine hardware.
- Is highly malleable, allowing for easy shaping, machining, and fabrication.
- Its distinctive golden to red-brown color adds aesthetic appeal to decorative items, architectural elements, and musical instruments. It can be polished but this will tarnish. Brass items are often lacquered with a clear coat to maintain luster.
- Has excellent electrical conductivity, making it suitable for electrical connectors and terminals.
- Is environmentally “friendly” in that it can be repeatedly recycled, reducing waste and conserving resources.
- Has good ductility, making it adaptable to a spectrum of forming processes.
- Has a long history of use in art, coins, and cultural artifacts, adding to its appeal and value.
What Are the Disadvantages of Brass?
Brass is a versatile alloy with numerous advantages, but it also has some disadvantages that must be taken into account. Those disadvantages include:
- Can be more expensive than other materials, driven by the high commodity cost of Copper.
- While generally corrosion-resistant, brass is highly susceptible to corrosion in specific environments, impacting its longevity. It suffers the worst attack in contact with chlorides, acetates, ammonia, and certain acids.
- Some brass alloys containing lead (free-machining brass) can be toxic, posing health risks if ingested or handled improperly.
- It is denser than some materials, making it heavier and less suitable for weight-sensitive applications.
- May not perform well in elevated temperature applications due to its lower melting point (even compared to pure copper).
- In certain conditions and particularly in wet marine applications, brass alloys can undergo dezincification, which can compromise their structural integrity.
- May not offer the same level of wear resistance as various other materials, limiting its use in high-friction situations.
Is Brass Softer Than Silicon Bronze?
In general, yes, brass is softer than silicon bronze. Silicon bronze alloys are known for their relatively high hardness compared to many brass alloys. Brass alloys are more valued for their malleability and ease of machining, which are characteristics of softer materials.
How To Choose Between Silicon Bronze and Brass?
Choosing between silicon bronze and brass depends on the specifics of your application. Take the considerations from the following list into account when making your choice:
- Strength vs. Malleability: If your application requires strength, durability, and resistance to wear, silicon bronze may be the better choice due to its higher hardness. For applications in which malleability and ease of fabrication are more critical, brass may be preferred.
- Corrosion Resistance: Both silicon bronze and brass offer good corrosion resistance, but the choice may depend on the specific environmental conditions your application will face. Brass has more and higher sensitivities to particular environments than silicon bronze.
- Aesthetic Considerations: Consider the color and appearance of the material, as both alloys have distinct visual characteristics.
- Cost: Brass is often lower cost in material and processing than silicon bronze, which can be harder to work with.
The selection of silicon bronze or brass for a component/application should align with the product’s specific mechanical, environmental, and budgetary pressures.
What Are the Properties of Silicon Bronze and Brass?
Table 4 summarizes some of the key properties of silicon bronze:
Property | Silicon Bronze |
---|---|
Property Composition | Silicon Bronze Copper (Cu), Silicon (Si), Trace Elements (e.g., zinc) |
Property Color | Silicon Bronze Red-brown |
Property Density (g/cm³) | Silicon Bronze 8.82 to 8.92 |
Property Melting Point (°C) | Silicon Bronze Approximately 950–1,030 |
Property Tensile Strength (MPa) | Silicon Bronze 240–550 |
Property Hardness (Rockwell B) | Silicon Bronze 50–90 HRB |
Property Electrical Conductivity (% IACS) | Silicon Bronze 6–10% IACS |
Property Thermal Conductivity (W/m·K) | Silicon Bronze 33–59 |
Property Corrosion Resistance | Silicon Bronze Excellent resistance to corrosion, particularly in marine environments |
Property Machinability | Silicon Bronze Good |
Property Weldability | Silicon Bronze Generally good |
Property Ductility | Silicon Bronze High |
Property Magnetic Properties | Silicon Bronze Non-magnetic |
The precise properties of silicon bronze will vary with grade, heat treatment, and manufacturing processes.
Table 5 outlines the key properties of brass:
Property | Brass |
---|---|
Property Composition | Brass Copper (Cu), Zinc (Zn), Trace Elements (e.g., lead, tin, aluminum) |
Property Color | Brass Yellow to reddish-brown (depending on zinc content) |
Property Density (g/cm³) | Brass 8.4–8.7 |
Property Melting Point (°C) | Brass Approximately 900–940 |
Property Tensile Strength (MPa) | Brass 250–800 |
Property Hardness (Rockwell B) | Brass 30–100 HRB |
Property Electrical Conductivity (% IACS) | Brass 18–44% IACS |
Property Thermal Conductivity (W/m·K) | Brass 59–120 |
Property Corrosion Resistance | Brass Good resistance to corrosion, especially in freshwater environments |
Property Machinability | Brass Excellent |
Property Weldability | Brass Generally good |
Property Ductility | Brass High |
Property Magnetic Properties | Brass Non-magnetic |
The exact properties of brass also vary with grade, heat treatment, and manufacturing processes.
How Malleable Are Silicon Bronze and Brass?
Both silicon bronze and brass are considered malleable materials, but the degree of malleability will vary markedly depending on the specific alloy components and heat treatment.
Silicon bronze alloys are described as having moderate malleability. They can be relatively easily formed, shaped, and machined, making them suitable for various applications that require fabrication and manipulation. The silicon in the alloy contributes to its malleability while still providing desirable strength and corrosion resistance.
Brass alloys are generally highly malleable materials. They exhibit excellent malleability and can be readily formed, bent, and fabricated into intricate shapes and designs. Ease of machining and formability is an essential benefit in many grades.
What Is the Tensile Strength of Silicon Bronze and Brass?
The tensile strength of silicon bronze and brass can vary depending on the specifics of alloy composition, forming processes, and heat treatment. Silicon bronze has a tensile strength of 240 to 550 MPa, while brass has a tensile strength of 250 to 800 MPa.
To learn more, see our guide on Material Tensile Strength.
Do Silicon Bronze and Brass Rust?
Yes. Silicon bronze and brass do corrode. Both alloys develop red-brown oxide layers that thicken and darken slowly in air or wet conditions. This process is slower for silicon bronze. Both materials respond to acid conditions by suffering more rapid oxidation. Brass suffers a process referred to as dezincification when exposed to salt water, making it unsuitable for wet marine use. The zinc is preferentially corroded, turning the material pink and eventually severely weakening it. Silicon bronze only contains trace zinc and is unaffected by this.
Are Silicon Bronze and Brass Brittle?
No, neither silicon bronze nor brass are considered brittle materials. Both alloys are known for their malleability and ductility, which means they can deform and bend without fracturing easily. However, the brittleness of these materials can be higher for some specific alloys, heat treatment, and manufacturing processes.
How Can Xometry Assist You With Your Silicon Bronze or Brass Needs?
Xometry is an invaluable resource for fulfilling your silicon bronze or brass material needs. As a manufacturing and supply-chain platform. Xometry provides access to a network of validated suppliers and can help source high-quality materials that meet your specifications. They also offer a range of manufacturing services, including CNC machining and sheet metal fabrication. These services can be applied to components made from silicon bronze or brass alloys.
Whether you need prototypes or large-scale production runs, Xometry's manufacturing capabilities will flexibly accommodate your requirements. Xometry ensures quality control and compliance with material specifications. Xometry's online platform simplifies the procurement process, making it easy to request quotes, place orders, and track deliveries.
How To Identify Silicon Bronze and Brass?
Identifying/differentiating silicon bronze and brass can be challenging because they often share similar visual characteristics, such as color and luster. However, some methods may help:
- Silicon bronze and brass both have a red-brown to yellow color depending on surface oxidation. Brass, however, tends to have a brighter, more golden hue, while silicon bronze may appear slightly redder or duller because of the higher copper content.
- If the material is marked or stamped with a grade or alloy designation, this can reliably identify the material.
- When grinding the material, the sparks produced by silicon bronze tend to be fewer, shorter, and less intense compared to brass. A practiced eye or comparison with known samples can assess this.
What Are the Applications of Silicon Bronze and Brass?
Silicon bronze and brass find applications in various industries and sectors due to their unique properties. Silicon bronze’s applications range from:
- Marine and architectural hardware.
- Electrical contacts.
- Art and sculptures.
- Fasteners.
- Musical instruments (strings, valves, cymbals).
Brass, on the other hand, is used for:
- Plumbing fittings.
- Musical instruments (tubes, flares, valves, keys).
- Decorative items.
- Munitions cartridge casings.
- Valves and fittings.
Is Silicon Bronze Safe for Jewelry?
Yes. Silicon bronze can be safe for jewelry, but some considerations should be accounted for. While silicon bronze is generally considered safe, some individuals may be sensitive or allergic to copper. Silicon bronze, like other copper alloys, will tarnish and darken over time. Extended contact with the skin may result in temporary discoloration, as the metal's patina can transfer to the skin.
Is Brass a High-Quality Metal?
Yes, silicon bronze is a moderate-cost material with some remarkable capabilities, making it unusual and high-quality. These allow it to be used for high-value applications and it is often selected over alternatives because it offers an attractive and traditional appearance.
How Much Do Silicon Bronze and Brass Cost?
Silicon bronze bar stock can generally be purchased at moderate volumes for $5–7 per kg. The ingot price is highly variable with quality and quantity but ranges around $15,000 per tonne. Brass is less costly, at around US$5–10 per kg for bar stock and US$7,000 to $10,000 per tonne in ingot form, depending on quality and quantity.
Is Brass As Good as Gold?
It depends. Definitions of good, in this context, are very application-dependent! Brass is low value but low cost and can be used for bulk tasks. It is stronger, less dense, and in many regards more durable than gold.
Summary
This article presented silicon bronze and brass, explained each of them, and discussed their key differences. To learn more about both silicon bronze and brass, contact a Xometry representative.
Xometry provides a wide range of manufacturing capabilities and other value-added services for all of your prototyping and production needs. Visit our website to learn more or to request a free, no-obligation quote.
Disclaimer
The content appearing on this webpage is for informational purposes only. Xometry makes no representation or warranty of any kind, be it expressed or implied, as to the accuracy, completeness, or validity of the information. Any performance parameters, geometric tolerances, specific design features, quality and types of materials, or processes should not be inferred to represent what will be delivered by third-party suppliers or manufacturers through Xometry’s network. Buyers seeking quotes for parts are responsible for defining the specific requirements for those parts. Please refer to our terms and conditions for more information.
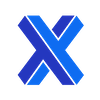