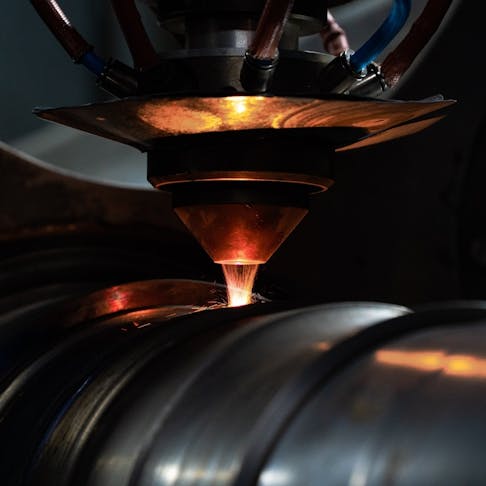
Laser Cladding: Definition, Process, Types, Applications, and Features
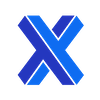
Laser cladding is an advanced manufacturing technique that involves the deposition of a protective or functional layer onto a substrate using a laser beam. Compared to conventional cladding techniques, it is a valuable precision-driven process. High-energy lasers provide precise control over heat input. This minimizes distortion and improves the metallurgical bonding between the substrate and the cladding material. Metals, alloys, ceramics, and composite materials can all be applied as cladding. Due to their adaptability, coatings can be customized to give their host part specific qualities like improved wear resistance, corrosion protection, or thermal conductivity.
Numerous industries, including aerospace, automotive, oil and gas, and tooling, use laser cladding. It is used to replace worn or damaged parts, add shielding to increase part longevity, and even create intricate geometries from scratch. Laser cladding has become a cutting-edge manufacturing technology due to its remarkable precision and flexibility. This article will discuss the procedure, categories, uses, and characteristics of laser cladding
What Is Laser Cladding?
Laser cladding is a manufacturing process that deposits a metallic material onto a surface using a laser beam as the heat source. The substance is melted, fused to the surface, and then typically becomes harder and more resistant to wear than the base material. Industries like aerospace, automotive, and tooling commonly use this method.
What Is the Other Term for Laser Cladding?
Another term for laser cladding is laser metal deposition (LMD). LMD refers to the same process of applying a coating, adding material to a component (deposition), and fusion of materials onto a surface using a laser beam.
What Is the Origin of Laser Cladding?
Laser cladding can be traced back to the late 1970s when lasers were introduced to the surface coating industry. However, conventional coating techniques were typically preferred because lasers were so expensive. The popularity of laser cladding has grown, however, with the development of more accessible laser sources and the investigation of new applications for lasers.
How Does the Laser Cladding Process Work?
Laser cladding works by depositing metal from a wire or powder onto a substrate using a laser beam. The laser melts it at the same rate as it is fed onto the substrate. As the molten substance solidifies, a metallurgical bond is created between it and the substrate. The coating thickness, composition, and surface characteristics can all be precisely controlled using this process.
What Is the Purpose of Laser Cladding?
Laser cladding is intended to repair damaged or worn surfaces and create a protective coating for the item. It gives users fine control over the process, enabling improved surface properties and durability.
Why Is Laser Cladding Important?
Laser cladding is significant because it can be employed to precisely repair, improve, and protect surfaces. It outshines other processes by leaving fewer heat-affected zones, generating less material waste, and being compatible with a variety of materials. Overall, it’s a flexible and effective process.
What Are the Uses of Laser Cladding?
Among the applications for laser cladding are:
- Surface restoration and repair of damaged components.
- Wear- and corrosion-resistant coating.
- Thermal barrier coating for high-temperature applications.
- Enhancement of surface properties like hardness and friction resistance.
- Creation of complex geometries and structures.
- Additive manufacturing and 3D printing of metal parts.
What Are the Different Types of Laser Cladding?
The various kinds of laser cladding methods include:
1. Powder-Fed Laser Cladding
Powder-fed laser cladding is an additive manufacturing style that involves melting and depositing powdered material onto a substrate using a laser. Given that the material is delivered in powder form, it differs from the wire-fed style of laser cladding. It can be applied to coating, repair, and prototyping tasks.
2. Wire-Fed Laser Cladding
Wire-fed laser cladding is a process in which a laser melts a metal wire and deposits its material onto a substrate, creating a protective or functional coating. It differs from other cladding techniques in the use of wire as feedstock rather than powder. It has a variety of uses, including restoring worn or damaged components, incorporating wear-resistant coatings, and constructing intricate geometries.
3. Direct Energy Deposition (DED) Laser Cladding
The process of direct energy deposition (DED) laser cladding involves depositing and melting metal powder onto a substrate using a laser. It is distinct from other additive manufacturing techniques because it is primarily used to fix, coat, or add custom features to existing parts rather than making entirely new ones.
What Type of Laser Is Used in Laser Cladding?
For the deposition process, laser cladding typically uses a high-power solid-state laser. The following is a list of laser types used in laser cladding:
1. Fiber Lasers
Fiber lasers generate laser beams using optical fibers and are known for their efficiency and reliability.
2. Diode Lasers
Diode lasers emit laser beams through semiconductor diodes and offer precise control in a compact package.
3. CO2 Lasers
Carbon dioxide lasers, CO2 lasers, produce laser beams through a gas mixture and are suitable for cladding larger areas.
4. Nd:YAG Lasers
Neodymium-doped yttrium aluminum garnet lasers generate laser beams using solid-state crystals. They are versatile for various cladding applications.
What Are the Different Applications of Laser Cladding?
Different industries use laser cladding in various ways. Here are a few examples of typical applications:
1. Aerospace Industry
The aerospace industry uses laser cladding to fix broken or worn-out parts, enhance surface qualities, and apply protective coatings to increase part durability and performance.
2. Automotive Industry
Laser cladding is used in the automotive industry to restore or repair worn-out engine parts like cylinder heads and camshafts. Both their lifespan and functionality are improved this way.
3. Medical Industry
Laser cladding finds value in the medical field for manufacturing and repairing medical implants and prosthetics. It allows for the precise deposition of biocompatible materials and enhances the longevity and functionality of these devices.
4. Oil and Gas Industry
The oil and gas sector uses laser cladding to repair and safeguard drilling equipment, valves, and other crucial pieces of machinery that are subject to challenging operating conditions. It aids in extending their service life and limiting downtime.
5. Energy Industry
In the energy industry, laser cladding is used for the refurbishment and repair of turbine blades, boiler parts, and other high-temperature, high-stress components. Their resistance to corrosion, wear, and thermal fatigue is improved.
6. Mold and Die Industry
The mold and die industry uses laser cladding to modify and repair broken or worn-out molds and dies. Since lasers can deposit materials precisely, they reduce the need for extensive rework and increase productivity.
Check out our Laser Cladding Services to get started on a new quote.
What Are the Key Parameters that Affect the Quality of a Laser Cladding?
The important factors that influence laser cladding quality are: substrate type, process environment, scanning speed, powder feed rate, powder composition, and laser power. The cladding geometry, bonding, porosity, and surface finish are all directly impacted by these parameters. They must be optimally controlled and adjusted to achieve desired clad quality and properties.
How Does Laser Power Affect the Laser Cladding?
Higher laser power improves the melting and bonding of cladding material, leading to better adhesion. It permits thicker layers and deeper penetration. It must be properly tuned, though; too much power can result in thermal damage whereas too little results in weak bonding. The appropriate power level is essential for the best cladding quality.
How Does Laser Speed Affect the Quality of Laser Cladding?
Faster laser speeds produce layers that are thinner and less diluted. Better control is possible at slower speeds. Low speeds expose the item to thermal damage while high speeds result in incomplete melting. The ideal cladding quality depends on selecting the proper speed.
What Materials Are Used in Laser Cladding?
It is possible to use many different materials with the adaptable process of laser cladding. Among the popular options are:
- Metal alloys such as: stainless steel, nickel-based alloys, titanium alloys, cobalt-chromium alloys, and aluminum alloys.
- Ceramics such as: zirconia, alumina, and tungsten carbide.
- Metal matrix composites are composed of metal and ceramic particles dispersed in a metal matrix.
- Tool steels are used for enhancing wear resistance and tool life.
Can Metals Be Used in Laser Cladding?
Yes, laser cladding can be done with metals. For their superior mechanical properties and capacity to form metallurgical bonds during the cladding process, metal alloys like stainless steel, nickel-based alloys, titanium alloys, cobalt-chromium alloys, and aluminum alloys are popular options. For more information, see our guide on what are metalloids.
Is It Possible To Use Alloy in Laser Cladding?
Yes, many alloys can be used in laser cladding. A layer of material is applied to a substrate using the laser cladding technique, and alloys can be created especially to improve the coating's properties. For more information, see our guide on the properties of alloys.
What Are the Advantages of Laser Cladding?
The following are the benefits of laser cladding:
- Precision and accuracy in depositing materials.
- Control over the composition and microstructure of the coating.
- Enhanced surface properties such as wear resistance, corrosion resistance, and thermal performance.
- Reduced material waste and cost savings.
What Are the Disadvantages of Laser Cladding?
The following are some drawbacks to laser cladding:
- High initial equipment cost.
- Limited deposition rates compared to other processes.
- Thermal stresses and distortions in the substrate.
- Limited range of suitable materials.
- Complex setup and parameter optimization are required.
How Much Does a Laser Cladding Machine Cost?
The price of a laser cladding machine depends heavily on its size, features, and productivity. A large-scale machine may cost between $250,000 and $350,000, whereas a small-scale machine may cost around $100,000. There are, however, less expensive models that cost between $900 and $11,000.
How Long Does Laser Cladding Machine Last?
A laser cladding machine's lifespan will depend on how the equipment is used and maintained. Most laser machines can last up to 15 years under proper usage. This will vary, however, depending on several factors such as the design and manufacture of the laser itself, the operating power that is used versus the rated power of the device, and the operating temperature of the laser.
Is Laser Cladding a Type of Additive Manufacturing?
Yes, laser cladding is a type of additive manufacturing. Similar to other additive manufacturing processes like 3D printing, it involves adding material to build up a part layer by layer.
Is Laser Cladding the Same as Laser Welding?
No, laser welding and laser cladding are not the same. A layer of material is deposited onto a substrate during laser cladding, whereas a laser beam is used during laser welding to fuse two or more workpieces together.
Can Laser Cladding Add Multiple Layers of Different Materials to a Substrate?
Yes, a substrate can receive multiple layers of different materials through laser cladding. It is possible to deposit multiple layers with different compositions and properties onto the substrate by adjusting the feed material and laser parameters.
Can Laser Cladding Be Used To Add a New Layer of Material Onto a Substrate?
Yes, laser cladding is made specifically to cover a substrate with new layers of material. The main purpose is to improve the substrate's characteristics.
What Is the Difference Between Laser Cladding and Laser Cutting?
While laser cutting involves removing material to create a cut, laser cladding involves adding material to a substrate. Laser cutters slice through the material while laser cladding machines build up layers of new material.
Summary
This article presented laser cladding, explained it, and discussed the processes and different types. To learn more about laser cladding, contact a Xometry representative.
Xometry provides a wide range of manufacturing capabilities, including sheet cutting and other value-added services for all of your prototyping and production needs. Visit our website to learn more or to request a free, no-obligation quote.
Disclaimer
The content appearing on this webpage is for informational purposes only. Xometry makes no representation or warranty of any kind, be it expressed or implied, as to the accuracy, completeness, or validity of the information. Any performance parameters, geometric tolerances, specific design features, quality and types of materials, or processes should not be inferred to represent what will be delivered by third-party suppliers or manufacturers through Xometry’s network. Buyers seeking quotes for parts are responsible for defining the specific requirements for those parts. Please refer to our terms and conditions for more information.
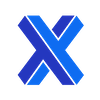